3. Circular fashion
FABRICADEMY WEEK3 EXPECTED LEARNING OUTCOMES
FABRICADEMY WEEK3 ASSIGNMENT
-Design and prototype with paper and scissors modular configurations and locking connections.
-Document the paper prototypes
-Run tests of laser cutting of your designs in fabric and document the parameters for the chosen fabric.
-Design and Document the process.
-Laser cut the modules. Create a modular or seamless garment, showing that the connection is well designed and holds the pull/stretch of a garment. Document the assembly process and tests.
-Upload the open source file in pdf, in correct scale with 1-5 pictures at (https://oscircularfashion.com) (preferably in white background)
-EXTRA POINT Submit some of the modules to the analog or digital material library of the lab. (20cm *20cm aprox)
Files to download |
Modular Garment Kit per file .ZIP |
1 |
Modular Garment Kit in 1 file .PDF |
2 |
Modular Garment Kit 3D module as .STL |
3 |
Published on: |
oscircular-fashion |
This Week’s assignment is the main part of my Final Project
current development of a garment kit (front) |
current development of a garment kit (back) |
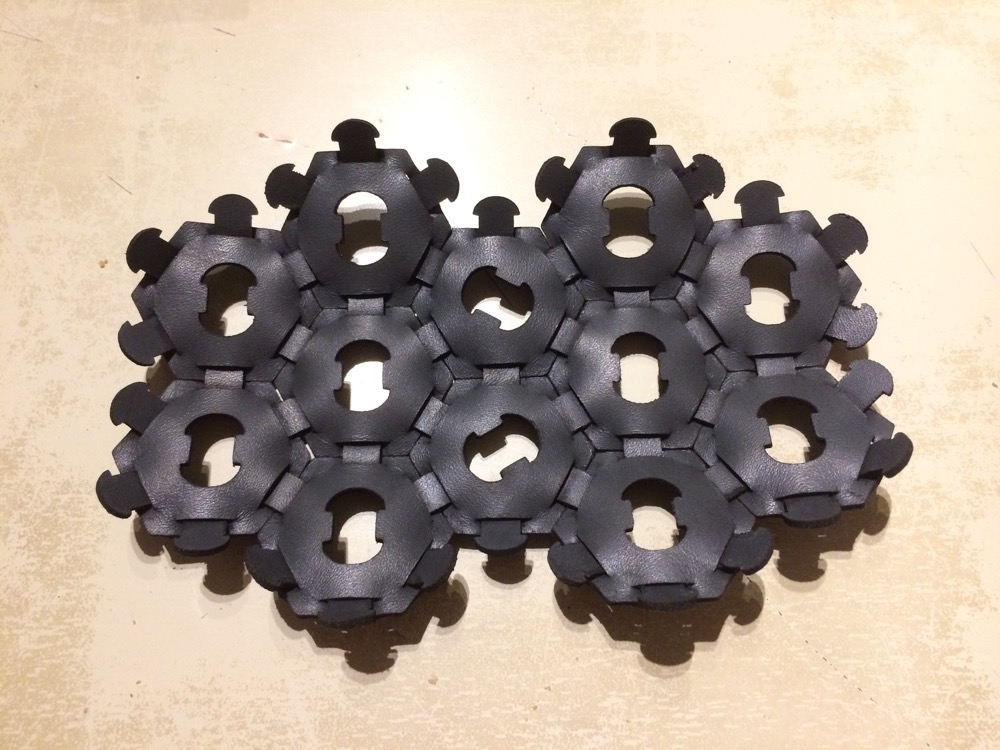 |
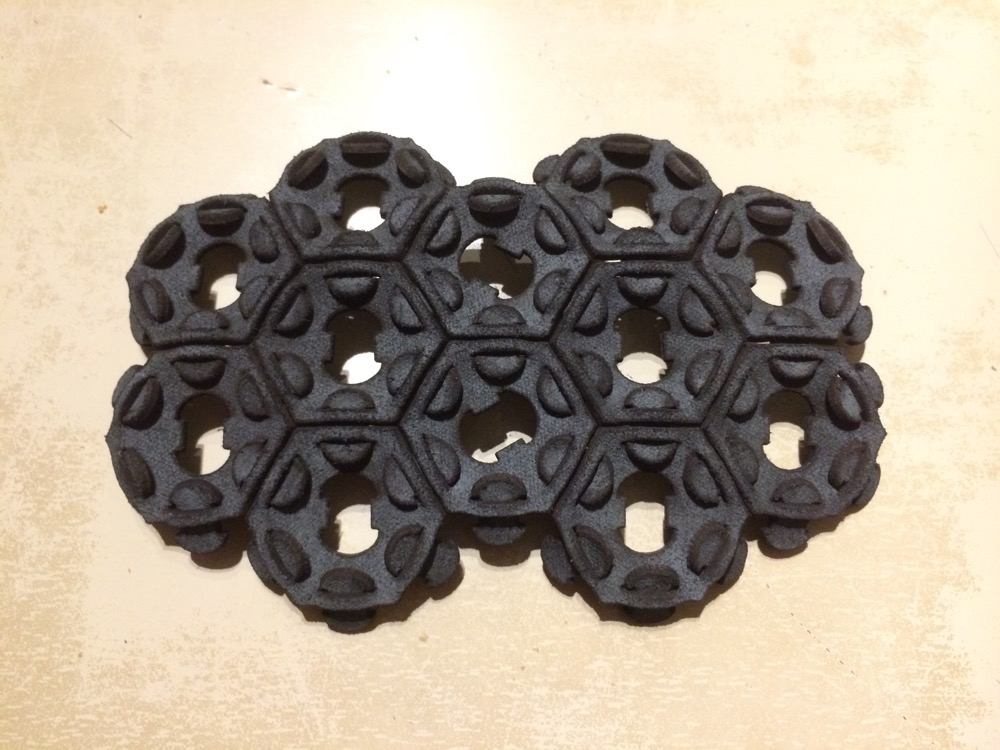 |
current development of a garment kit |
current development of a garment kit |
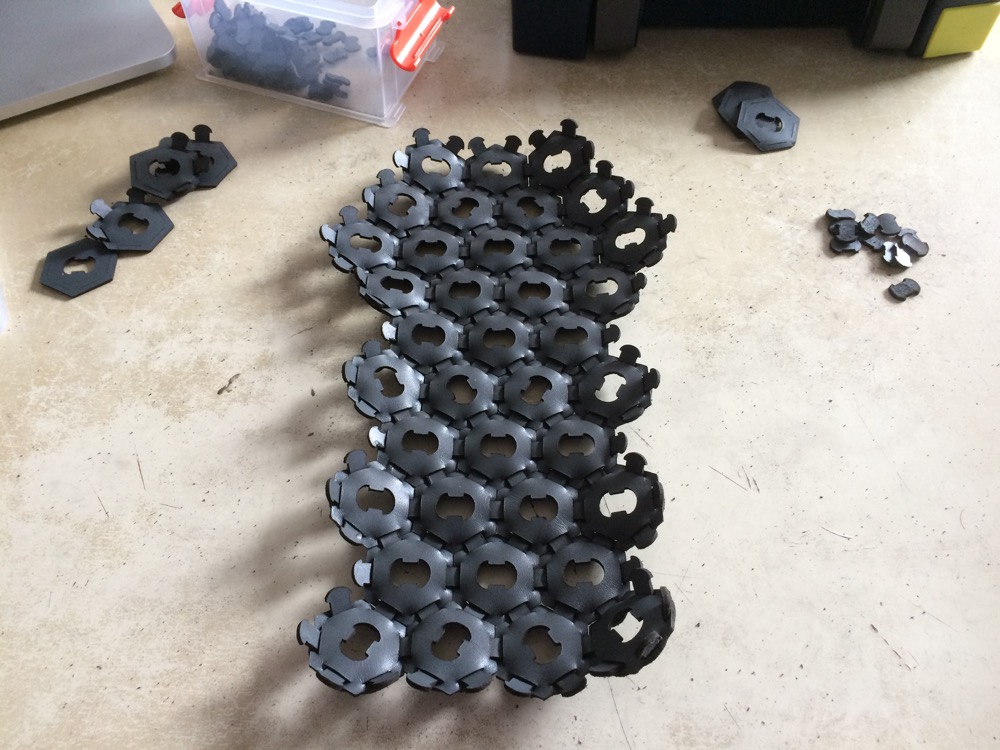 |
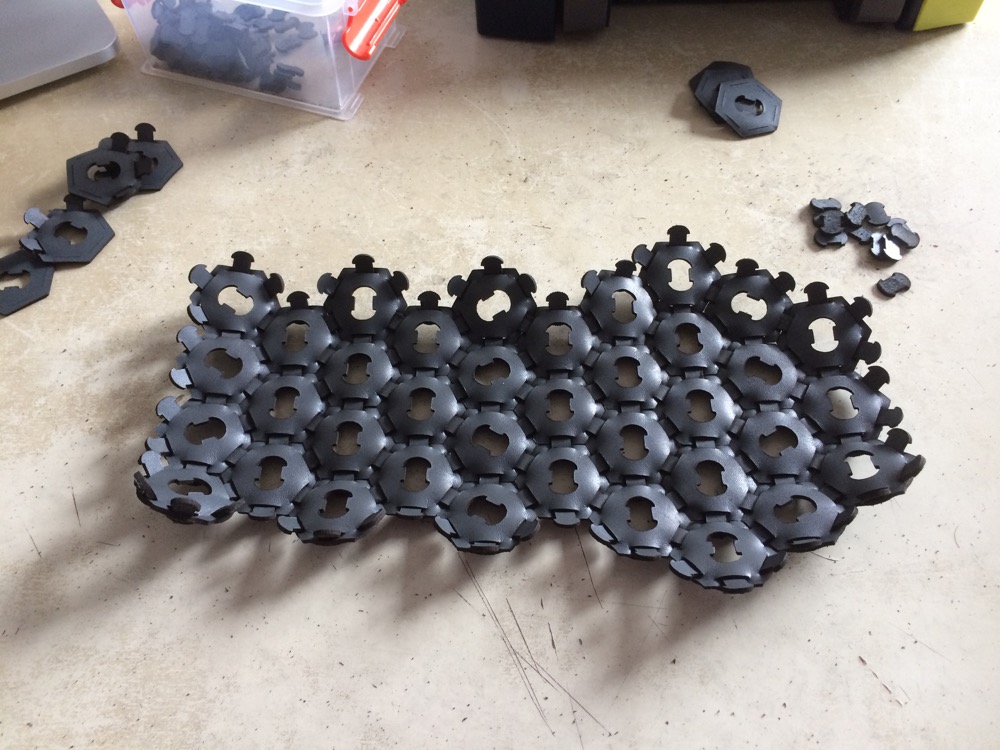 |
current development of a garment kit |
current development of a garment kit |
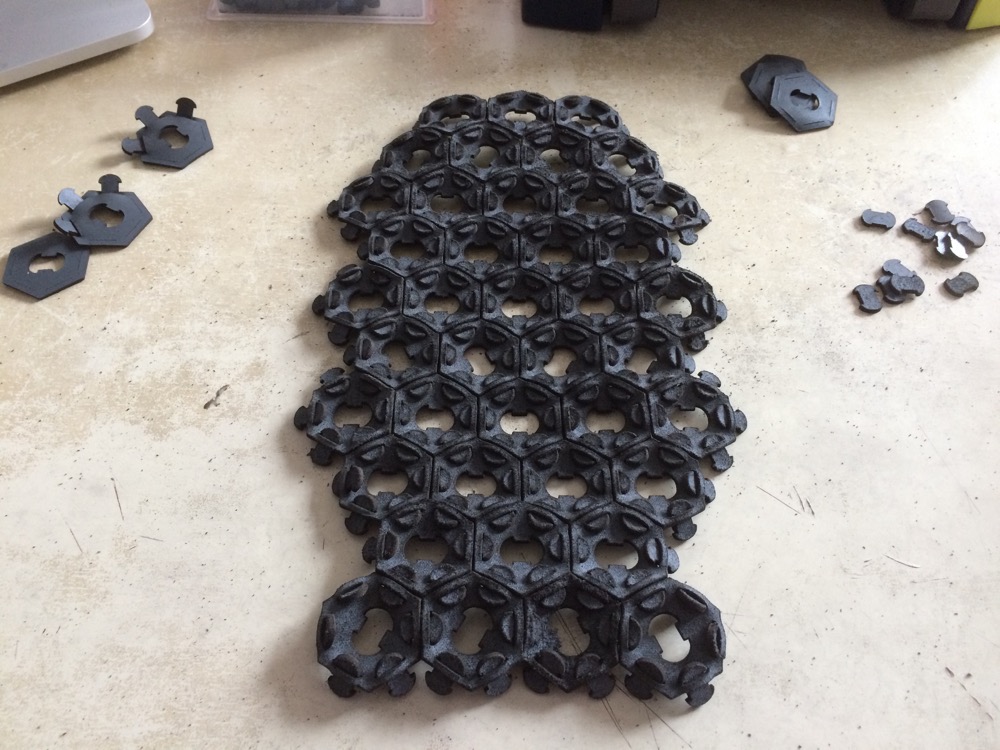 |
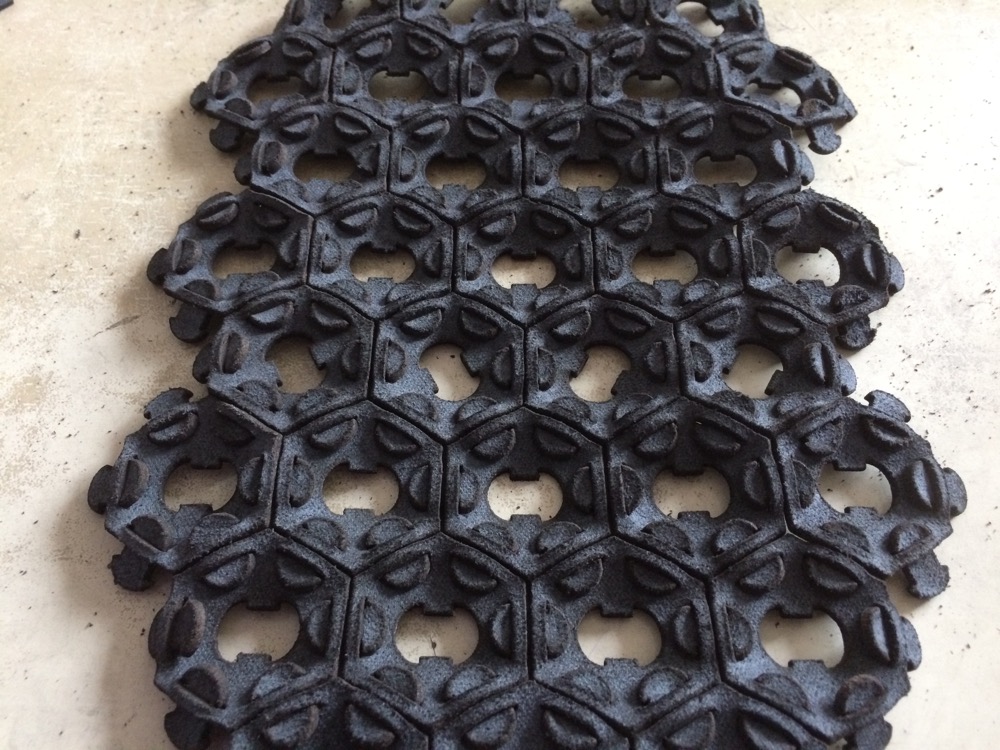 |
current development of a garment kit |
current development of a garment kit |
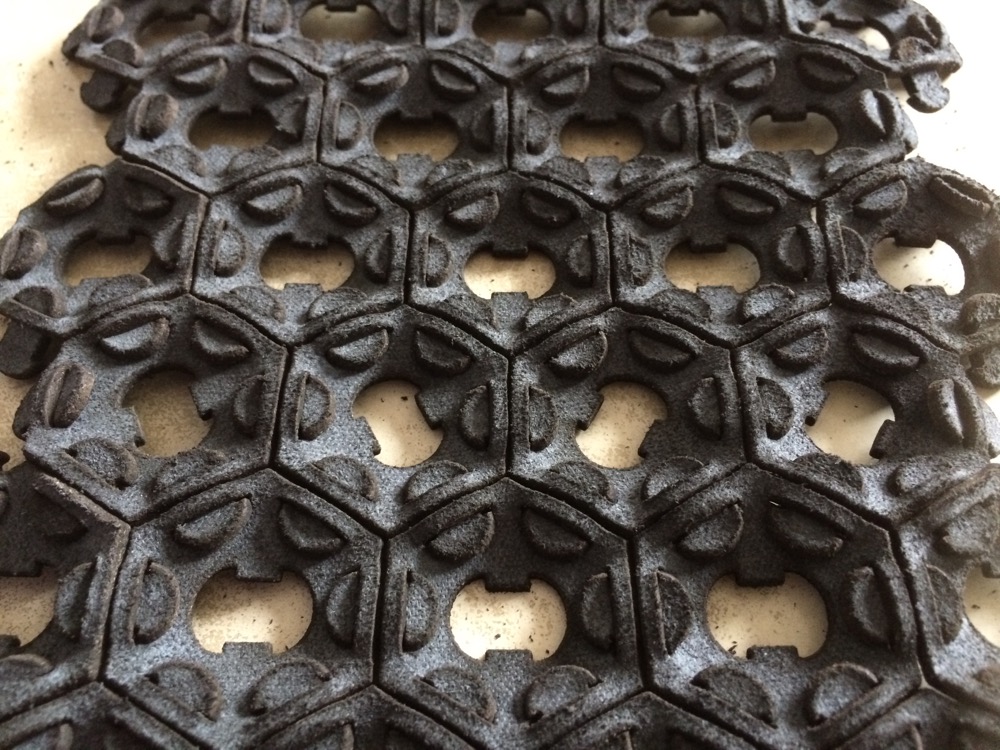 |
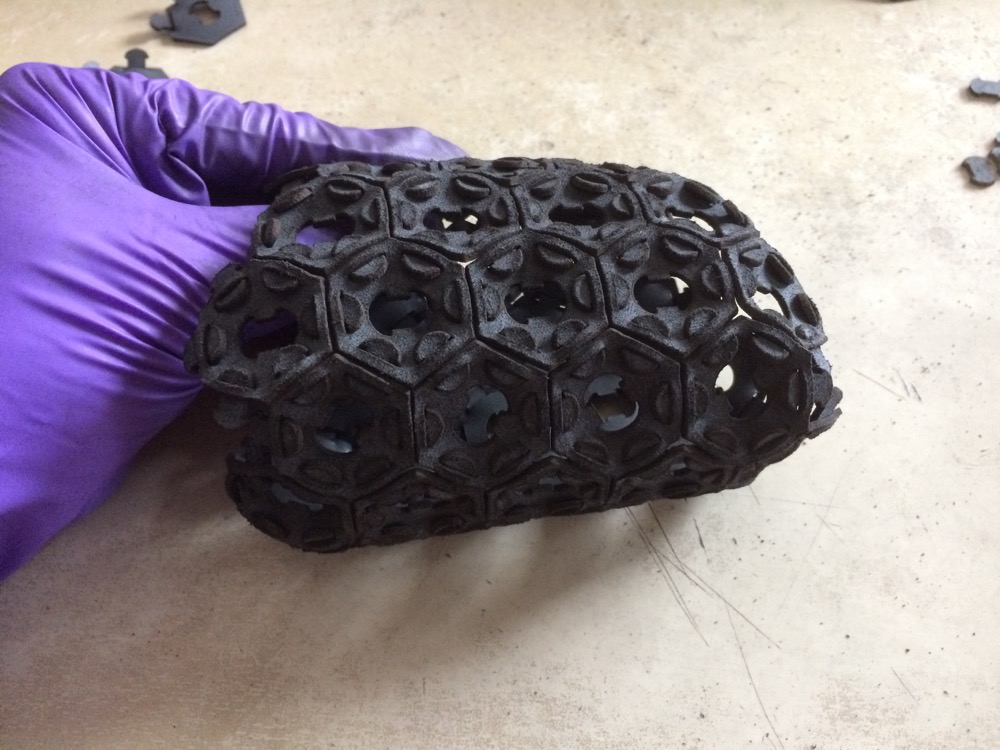 |
current development of a garment kit |
current development of a garment kit |
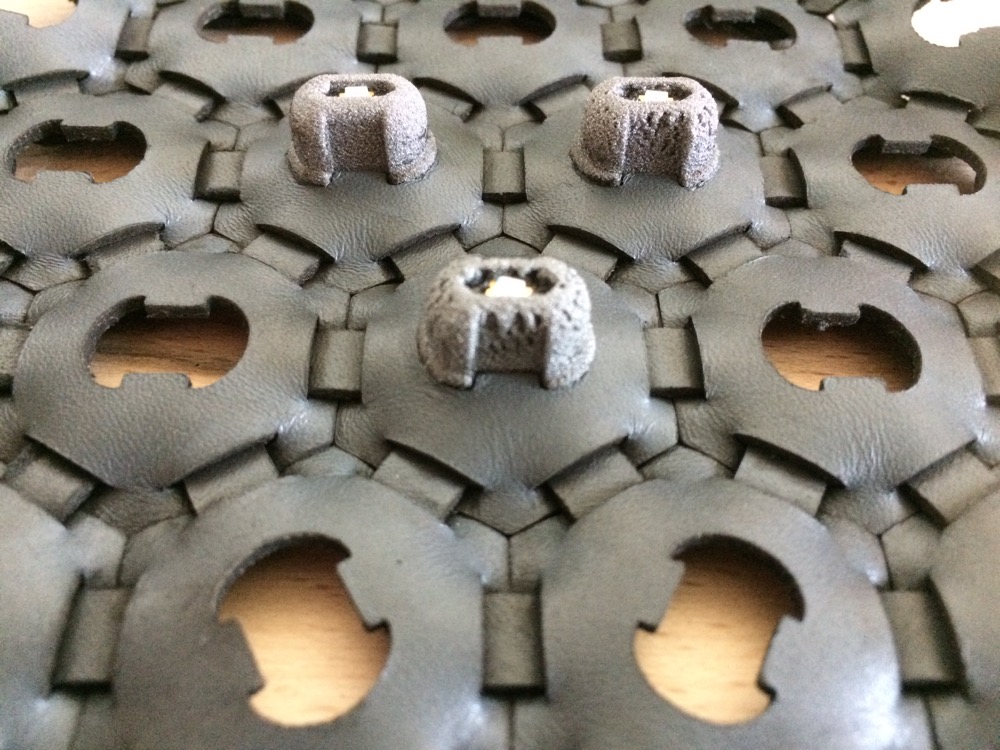 |
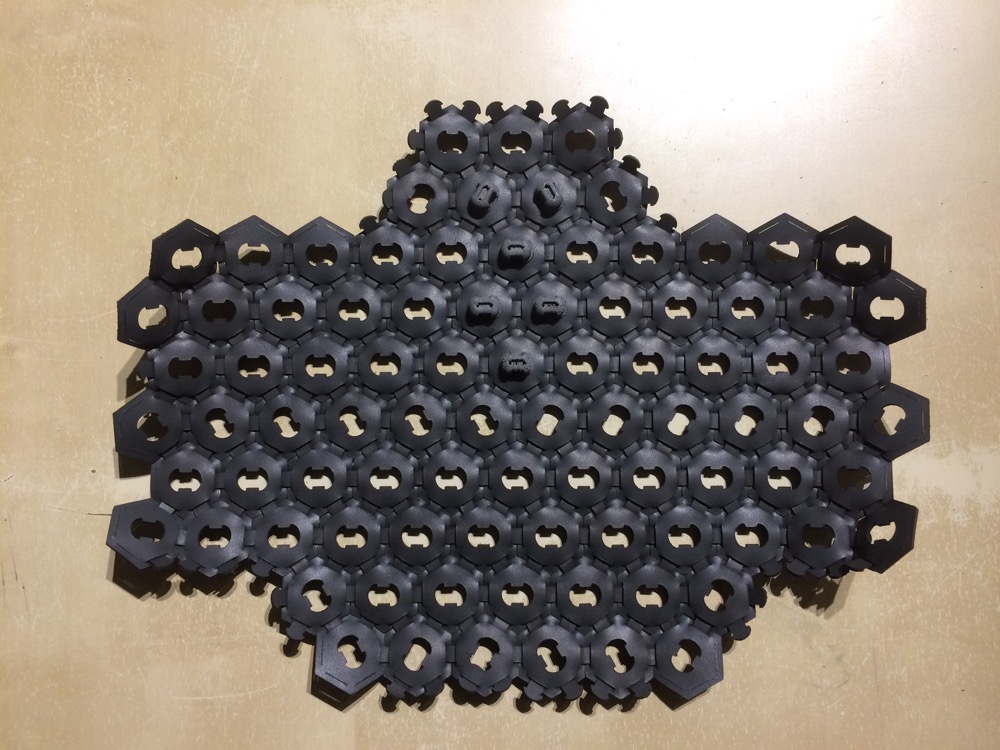 |
current development of a garment kit |
current development of a garment kit |
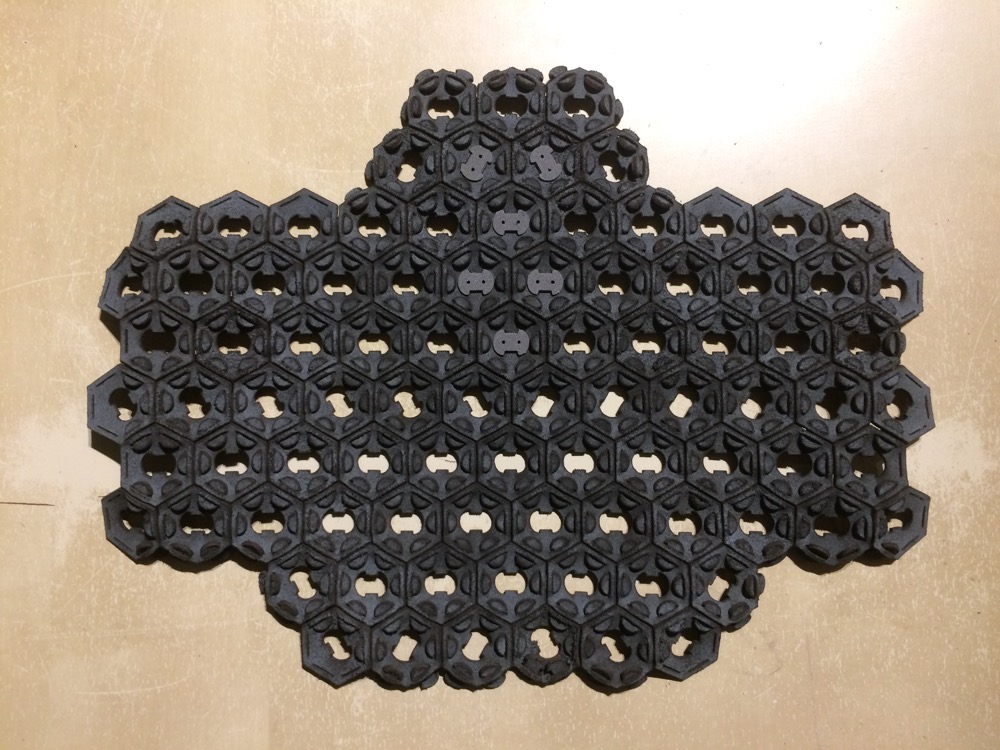 |
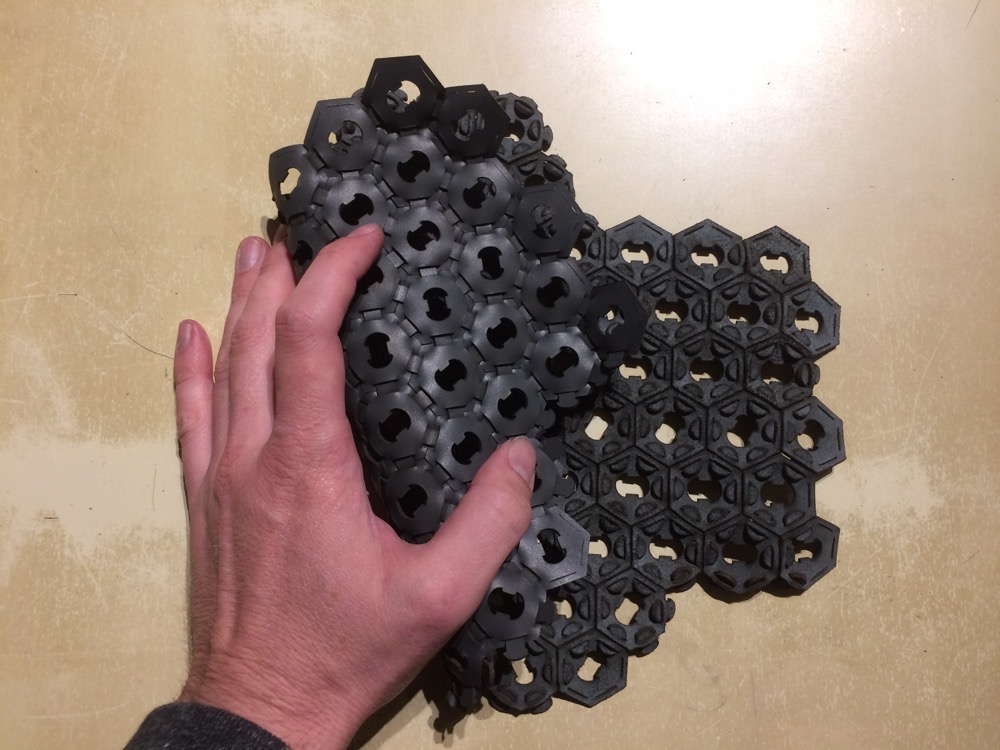 |
1 | Getting prepared to make reconfigurable/modular-cells assemblers: Previous experiment on a reconfigurable garment kit |
I started to take the Fabricademy bootcamp in september 2017. Lack of time lead me to interrumpt my participation pretty early…but I had the time to laser-cut leather-reconfigurable/modular parts. I wanted 2 main patterns that would fit together and would cover as much surface as possible while keeping flexibility. At some point, I could make them evolve parametrically, up-scale or down-scale them to adapt them to different assembly projects. I really enjoyed it. It looked like this:
a |
b |
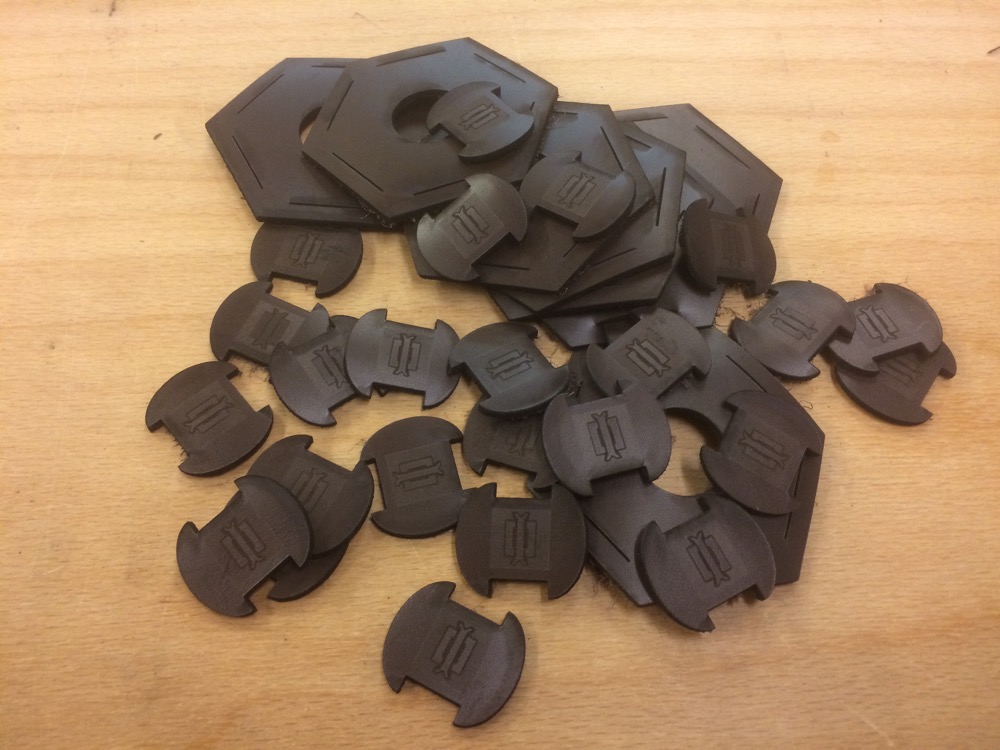 |
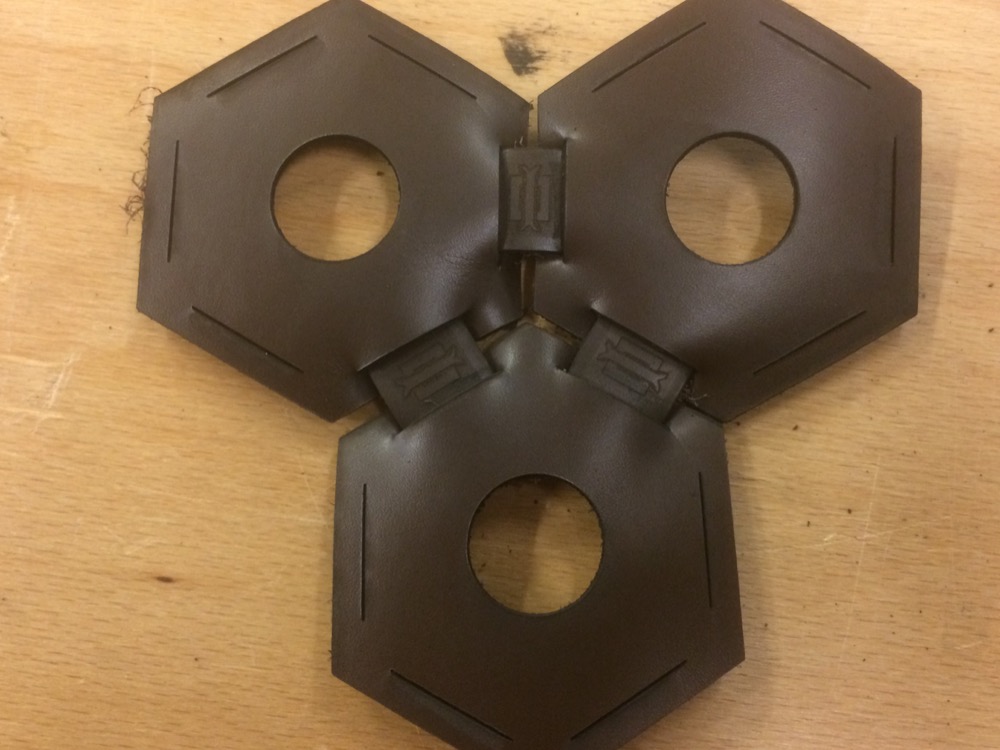 |
c |
d |
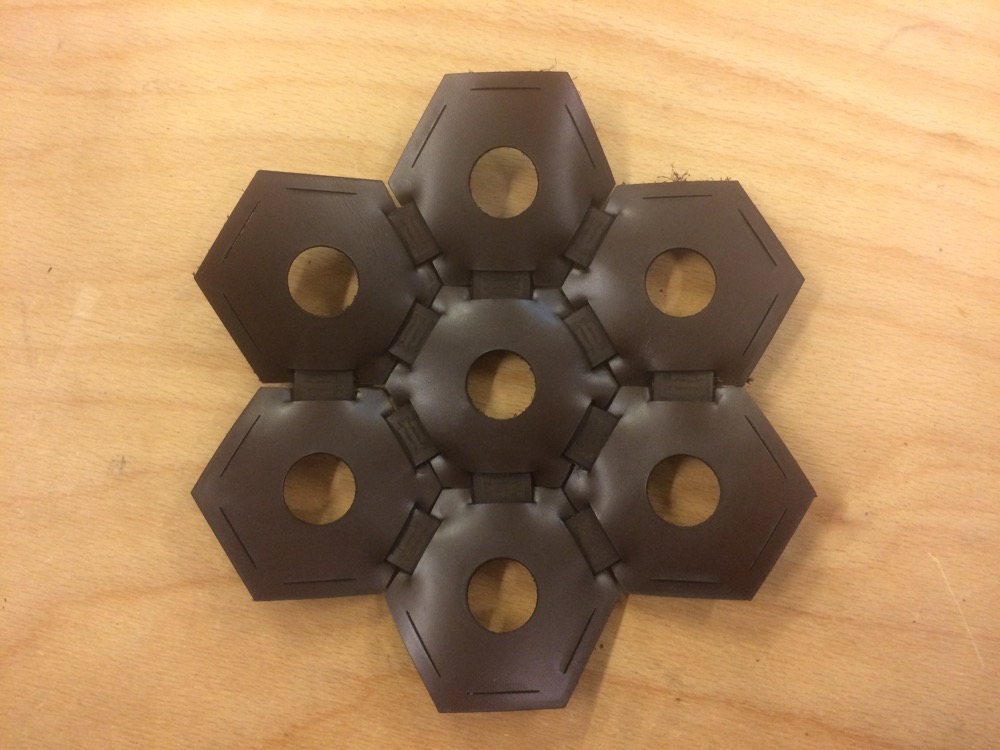 |
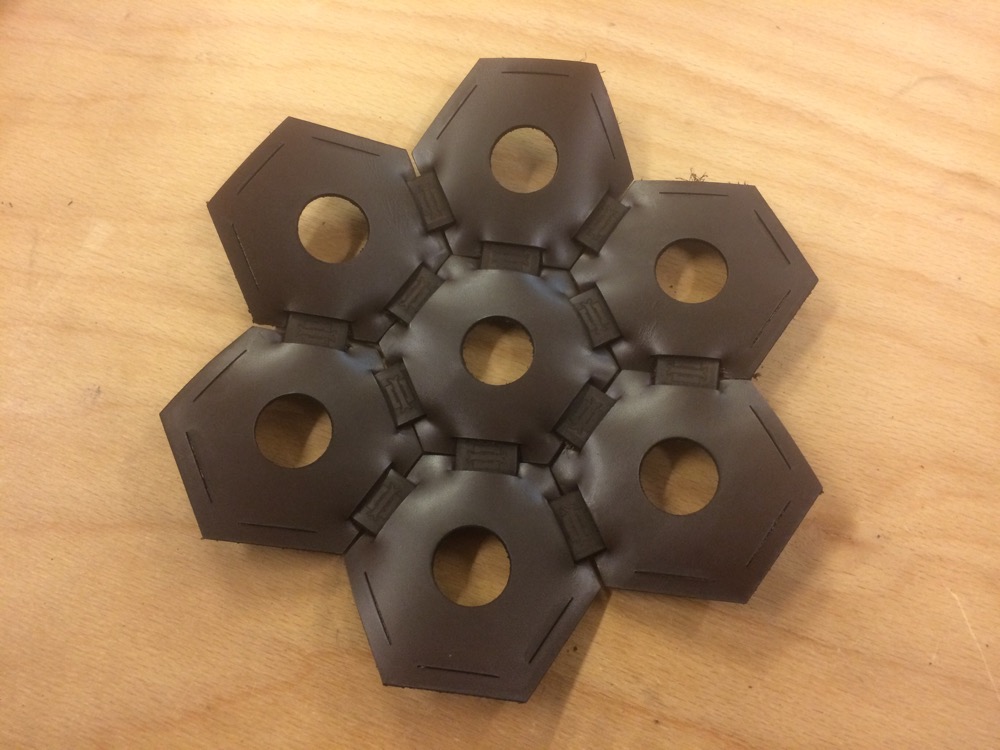 |
e |
f |
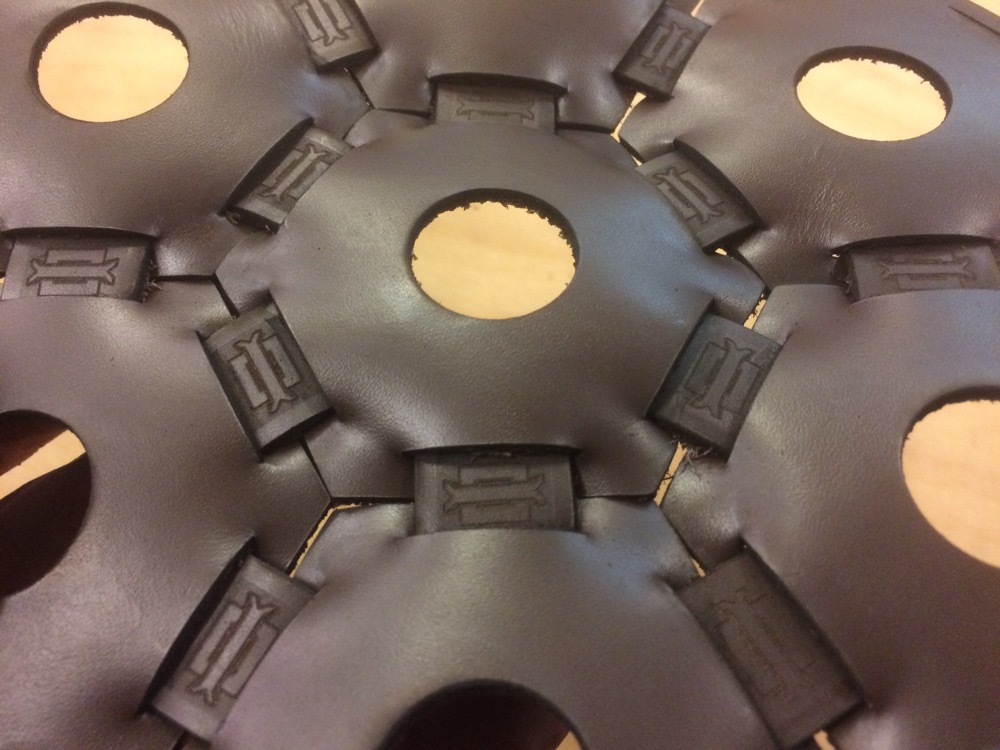 |
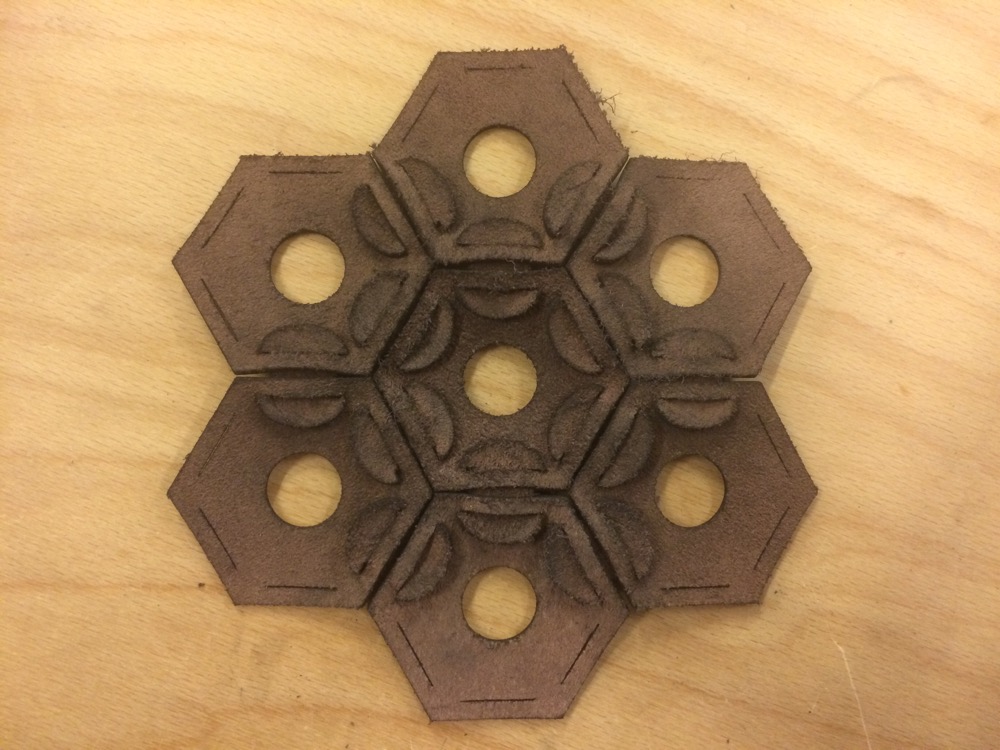 |
2 | Haute Couture leather wastes for all! |
Zola and me went to la Réserve des Arts to buy some leather. These leathers are wastes coming from Haute Couture that La Réserve des Arts sells for a very friendly price. Going there means spending 2h checking what’s for sell. For example, the big purple leather skin you can see on the table on the first picture costs 25€…
Zola surrounded by leathers |
Other Leathers |
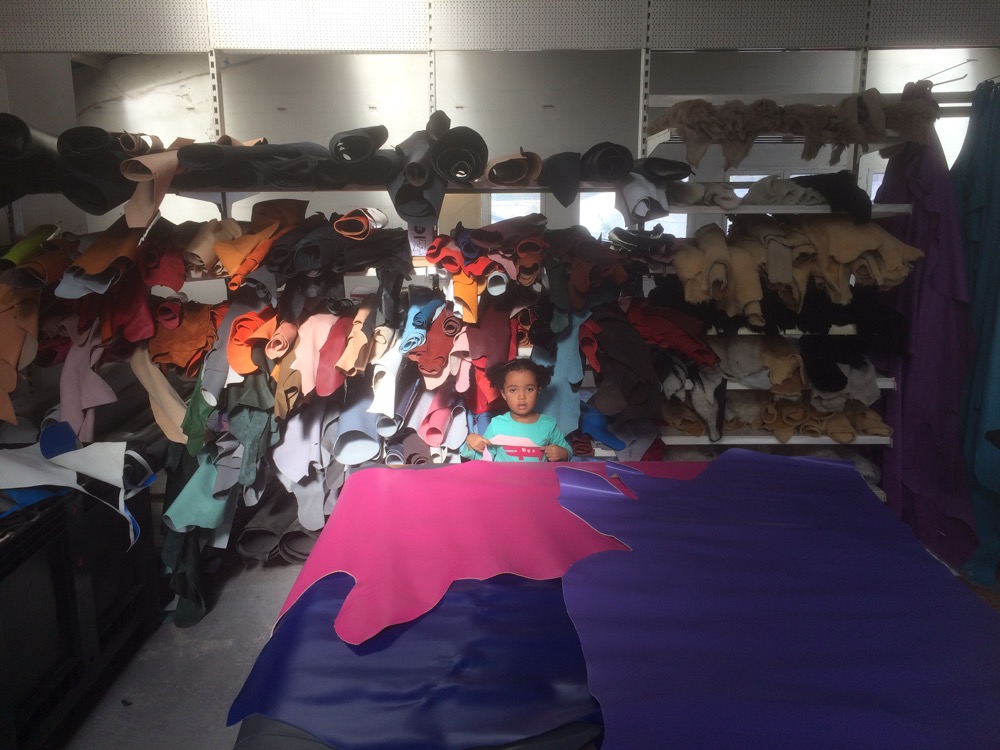 |
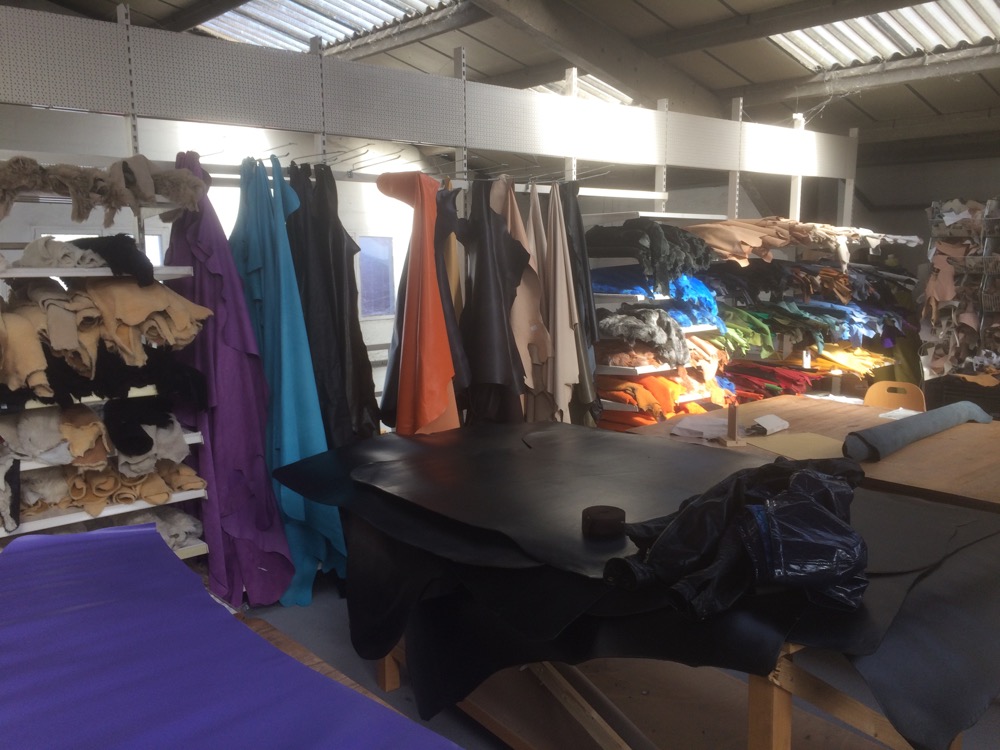 |
More leathers |
Leathers Everywhere |
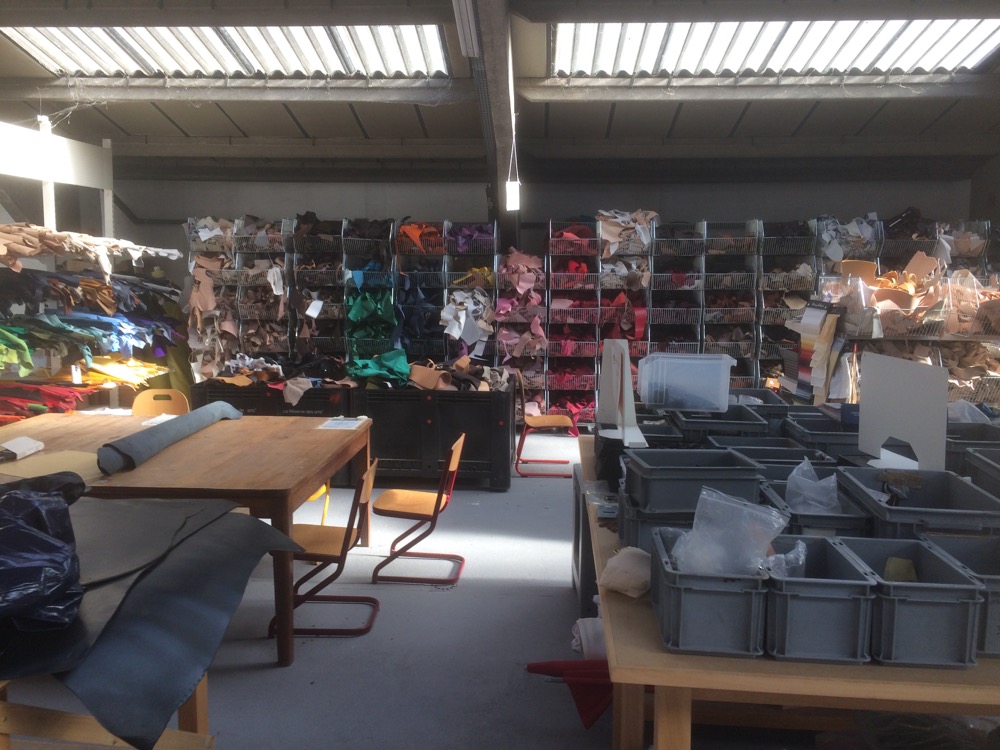 |
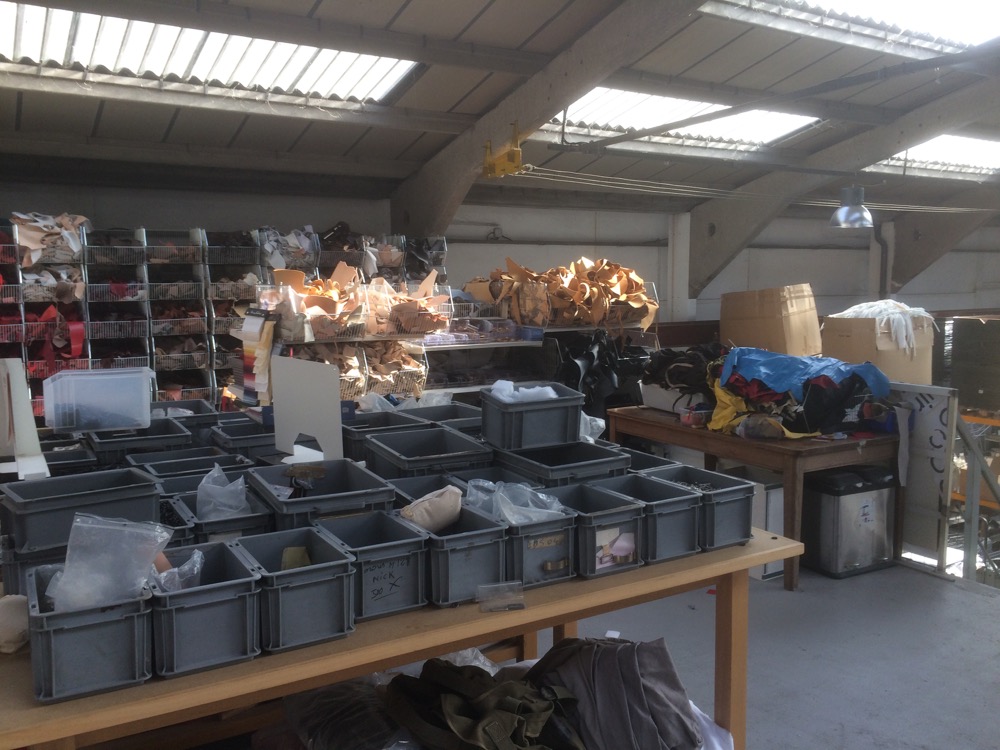 |
3 | About recycling materials |
It might not be obvious for everyone that using leathers - for garments and clothes or anything else - implies a societal responsability. Leather comes from dead domestic animals (in the best cases…) and it should be considered a rare product and of a high value, because the big amount of water and food cows need to grow to bring steaks on our tables has a very negative impact on our natural ecosystems and on global warming.
Some people would ban leather from our shelves, and this is a point of view I can share somehow.
In parallel, using vegetal fibers to make non comestible things is often - or always - better if the fiber we use is not comestible at all by leaving things like humans or animals. Knowing that millions of peoples are starving should lead people to make ethical choices on how fibers should be used. Do you prefer to transform corn into burritos or into corn-fiber for wadding ? Starvation vs Industrial Production of Fibers. Food should remain a priority when it comes to determine how a stock of fibers should be used. But, many synthetic fibers or textiles come from Oil and other chemical transformations which at some points have an even more negative impact on ecosystems and on our health.
We are trapped…
4 | (TUTORIAL) | Drawing a reconfigurable/modular pattern with Illustrator |
Here is how I drew and laser-cut the first iteration of the design above:
Design on Illustrator:
1 |
2 |
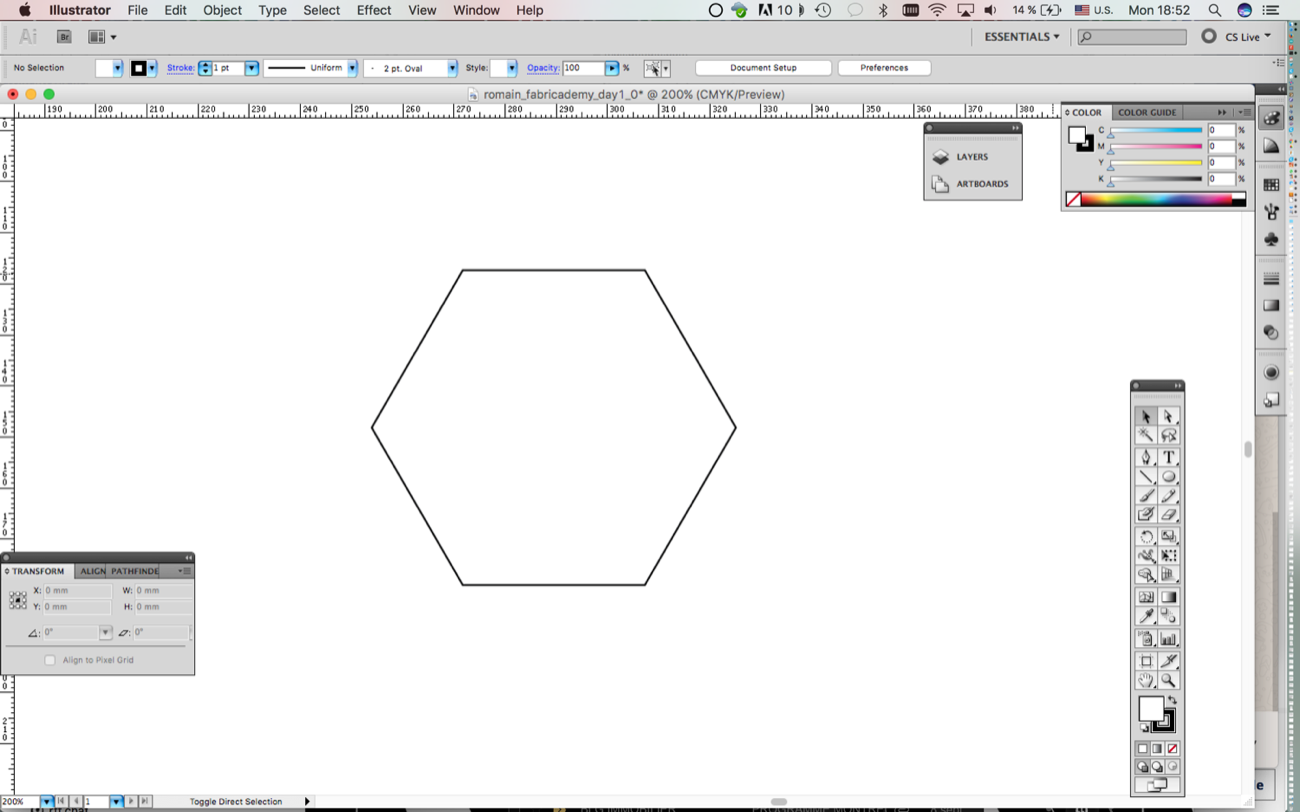 |
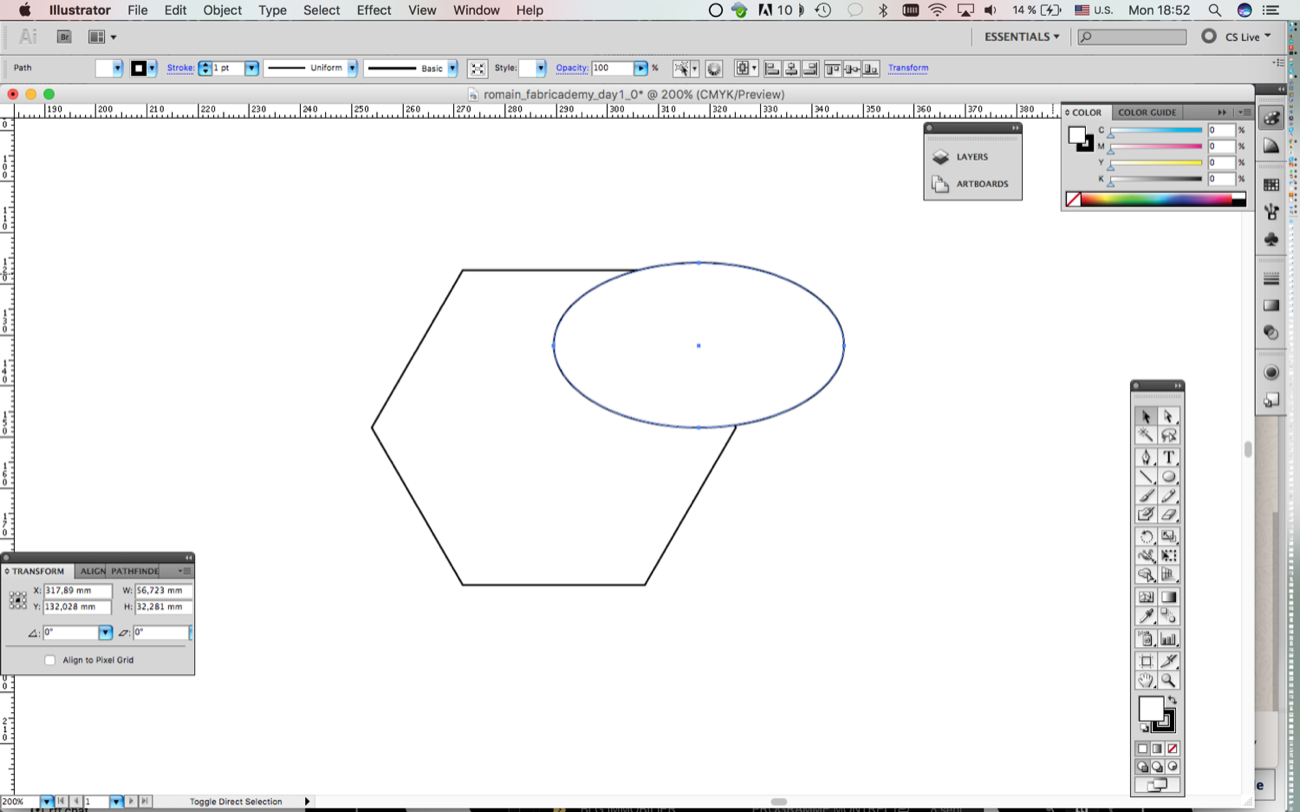 |
3 |
4 |
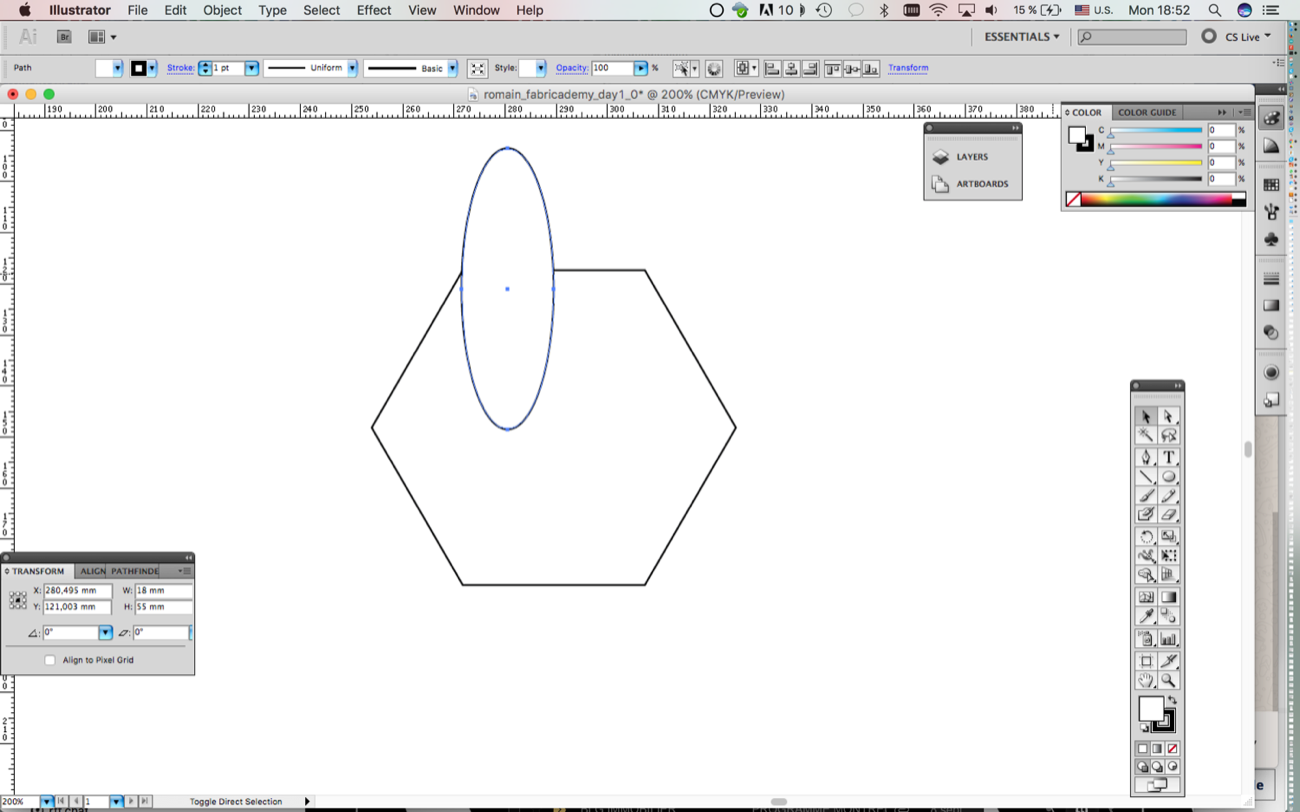 |
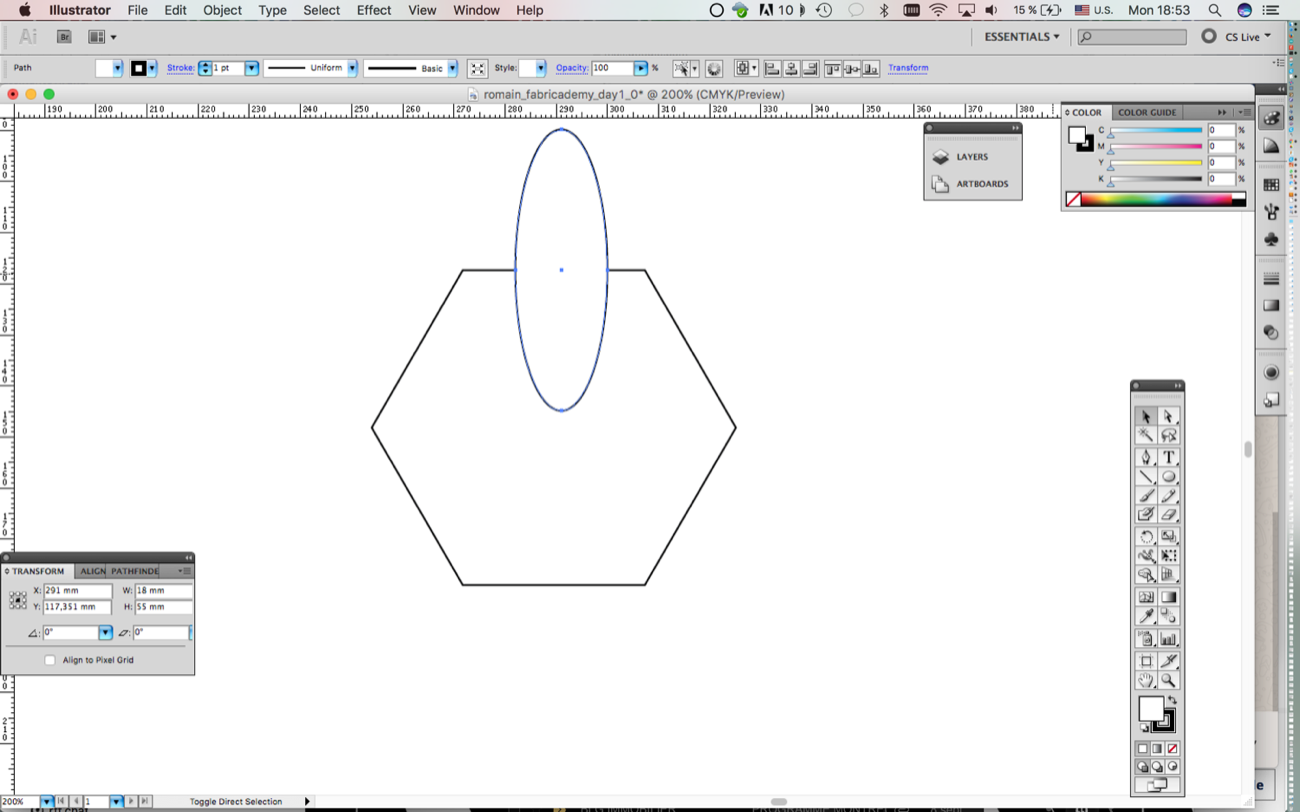 |
5 |
6 |
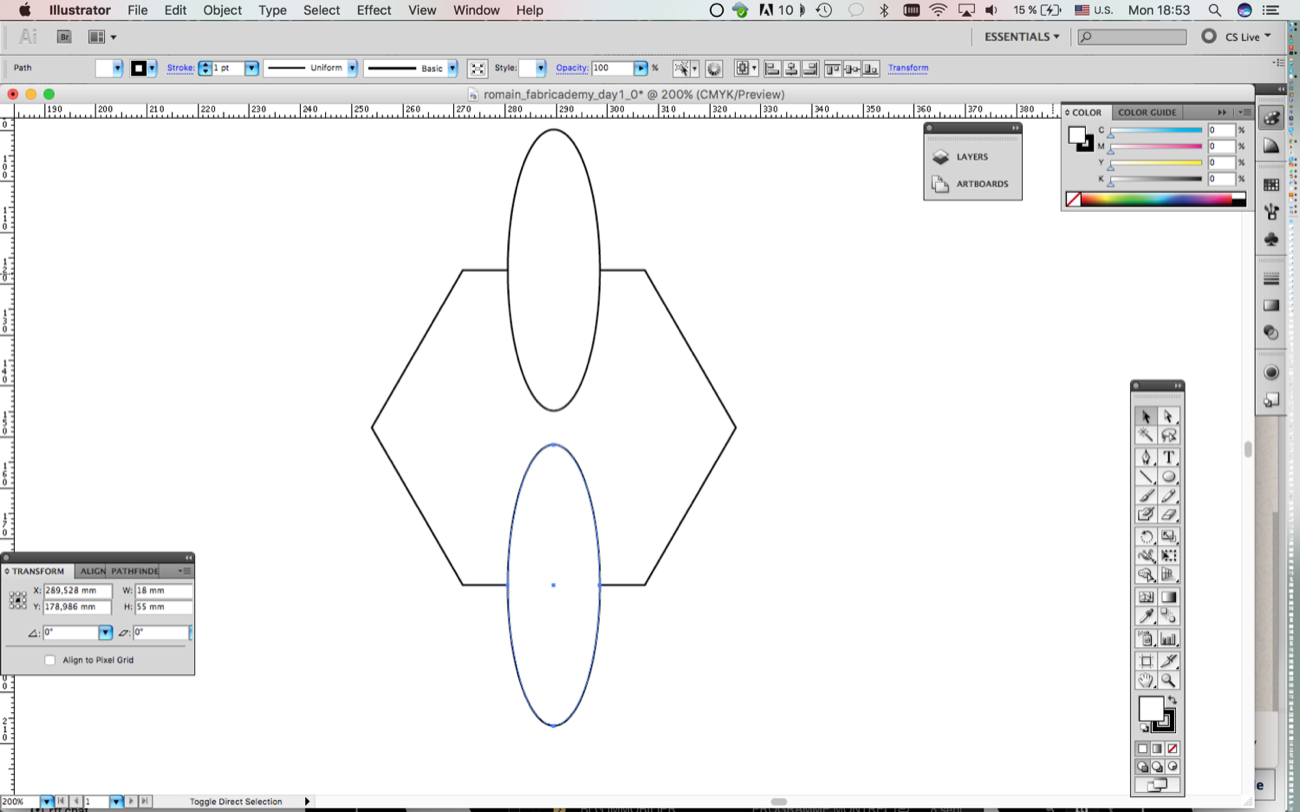 |
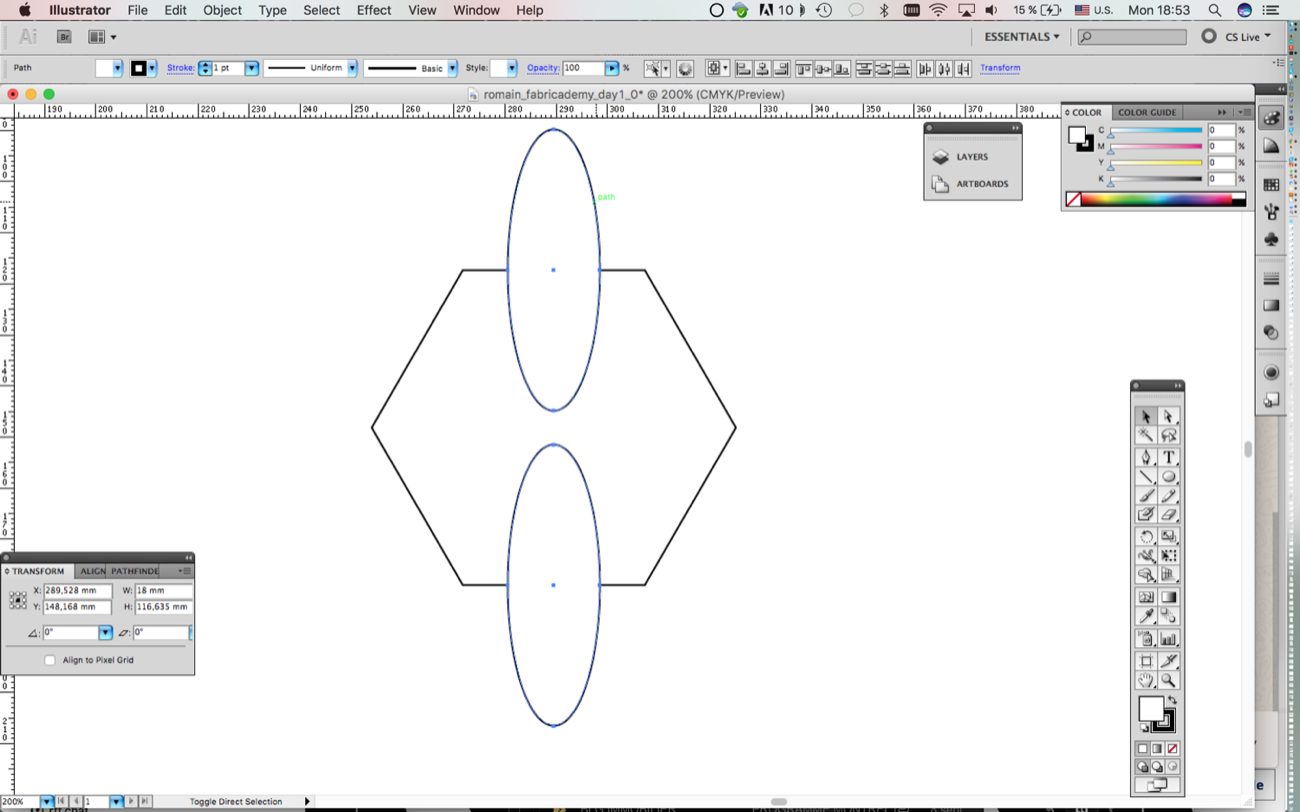 |
7 |
8 |
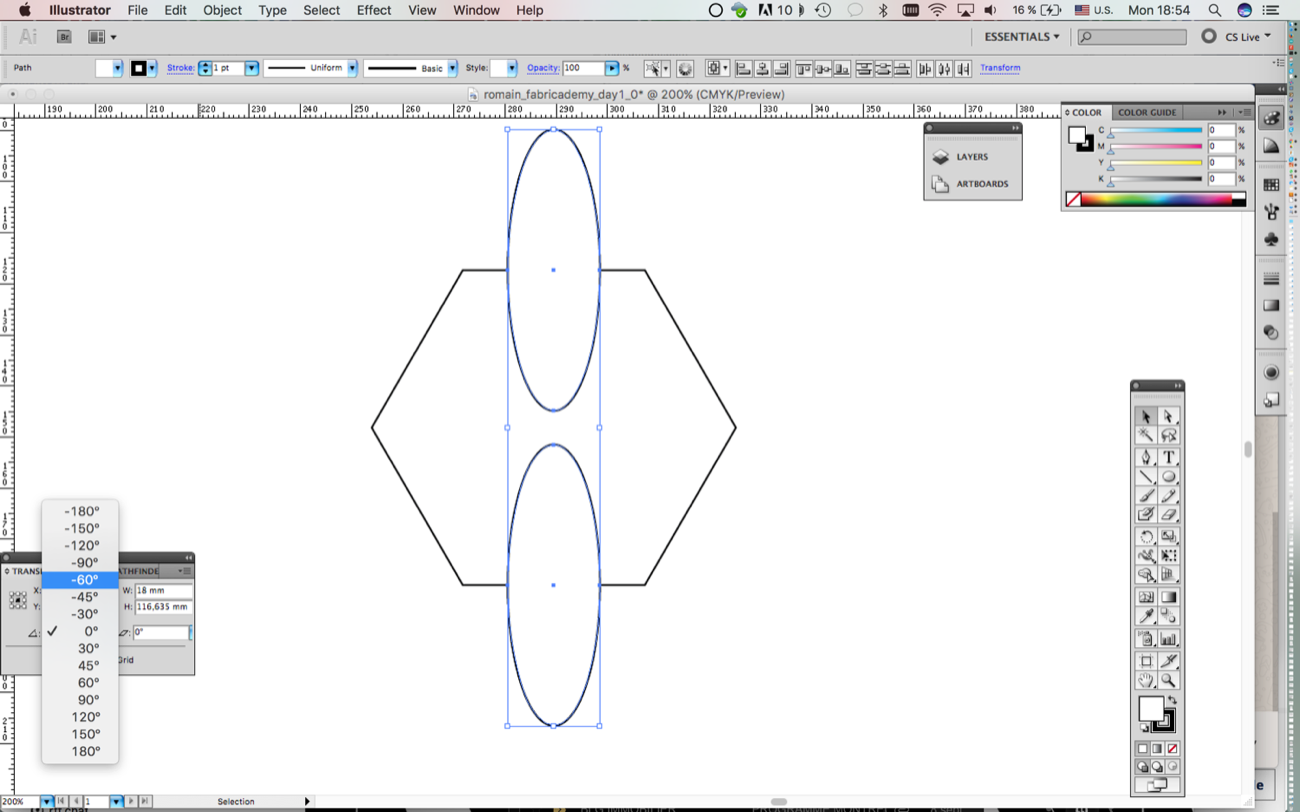 |
 |
9 |
10 |
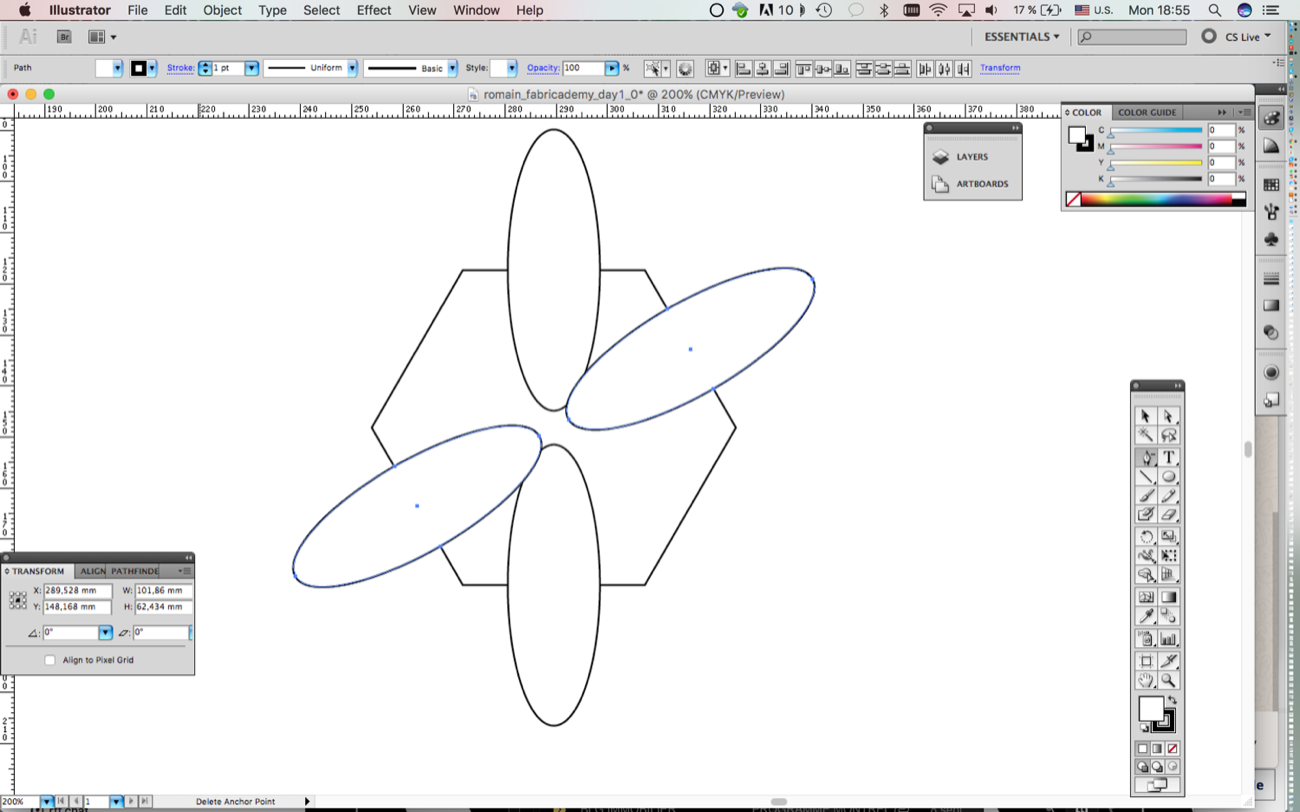 |
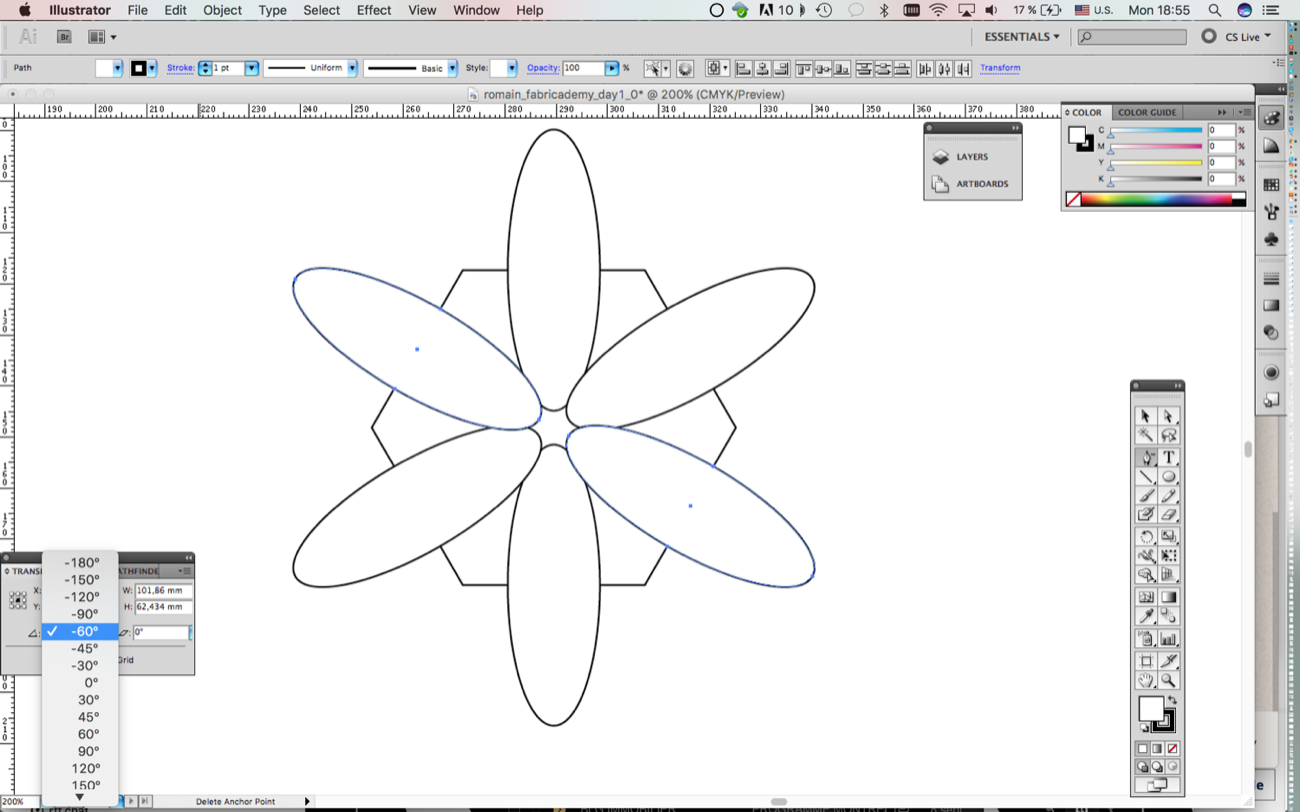 |
11 |
12 |
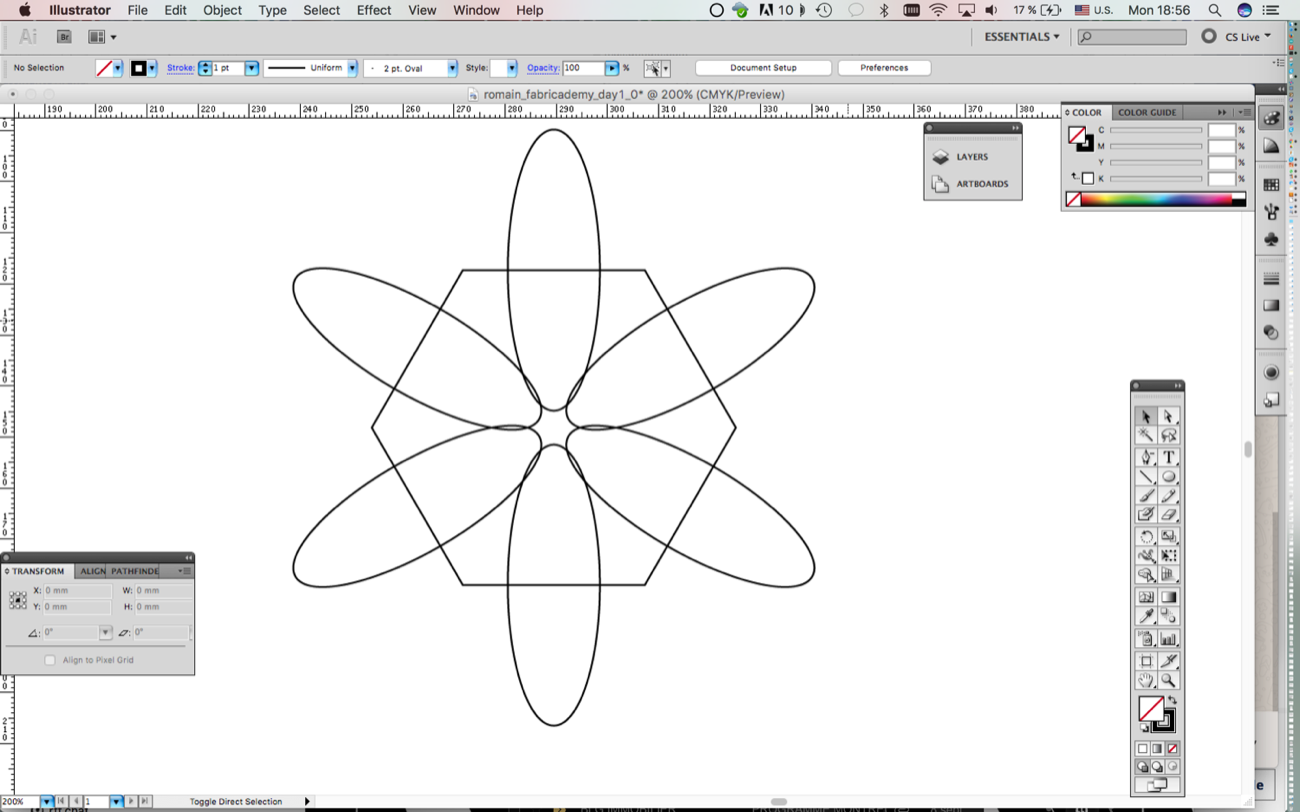 |
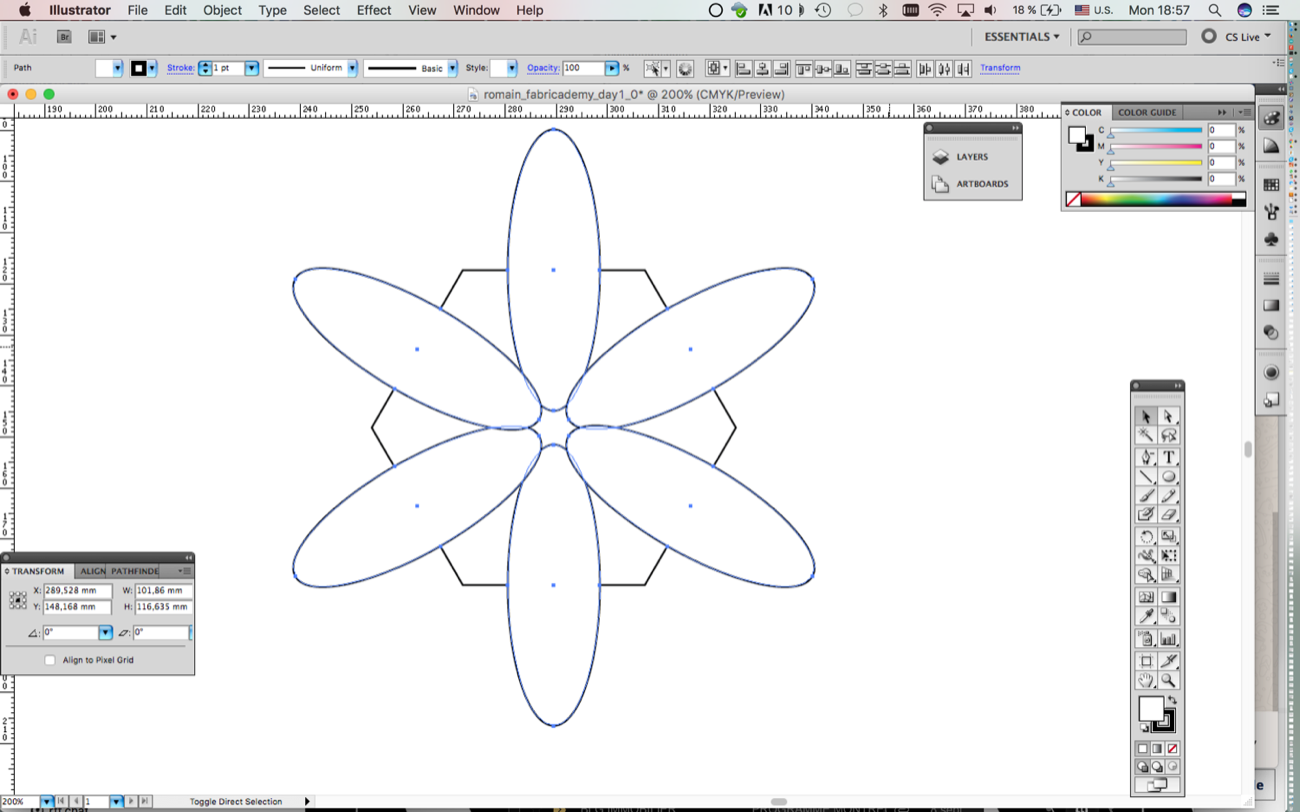 |
13 |
14 |
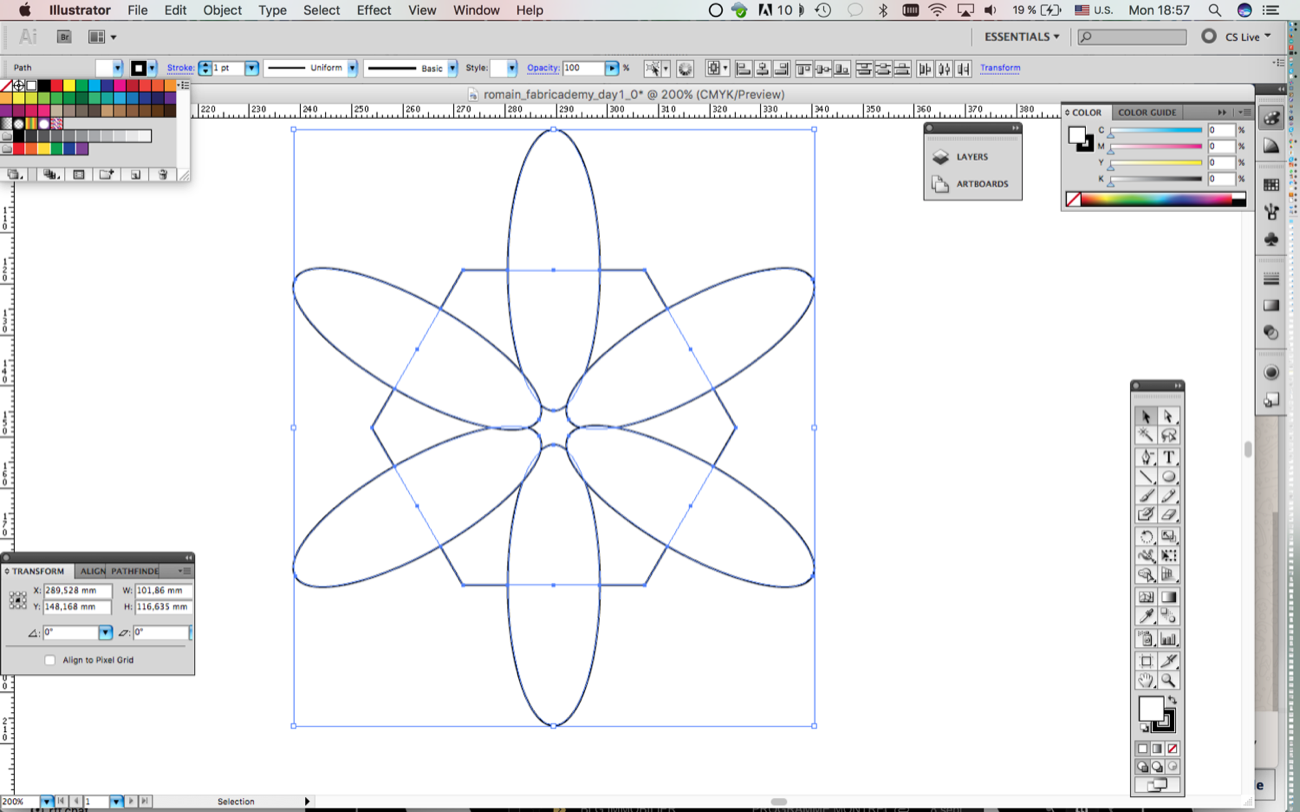 |
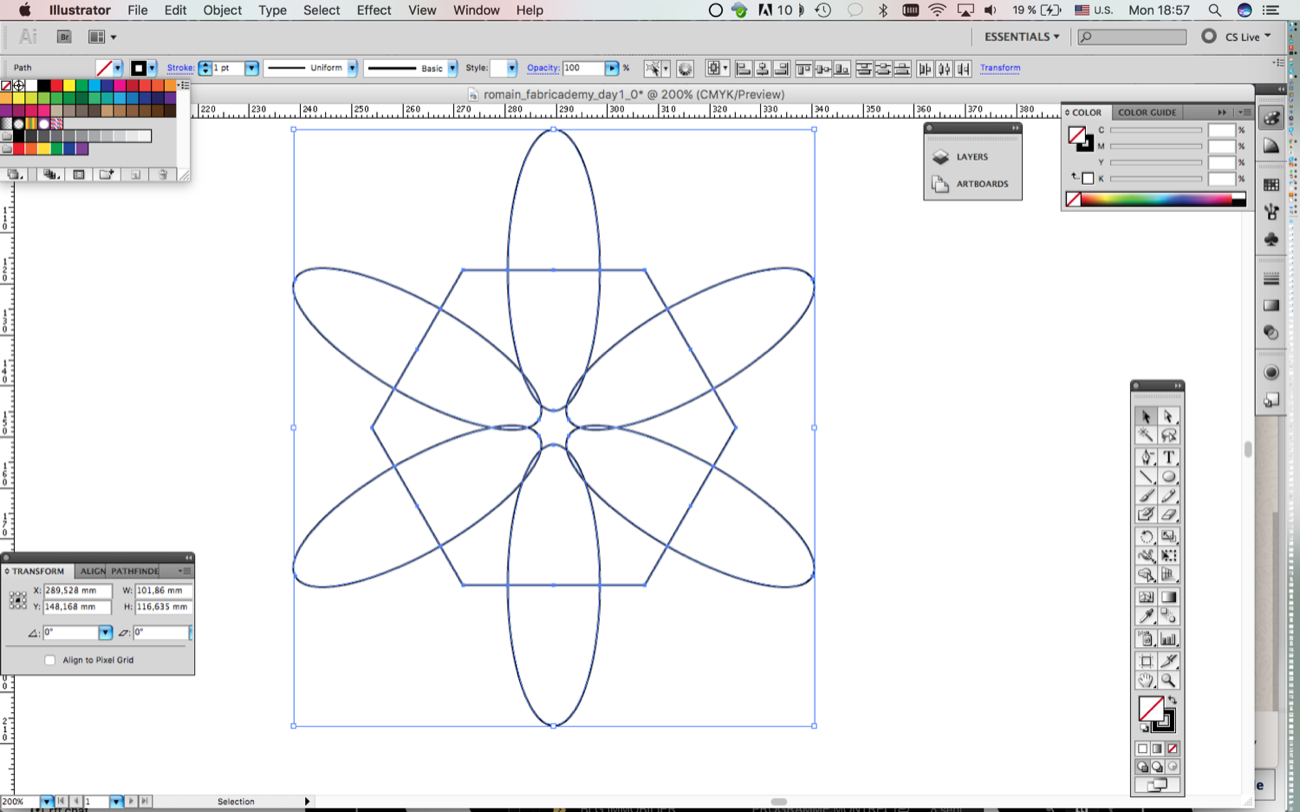 |
15 |
16 |
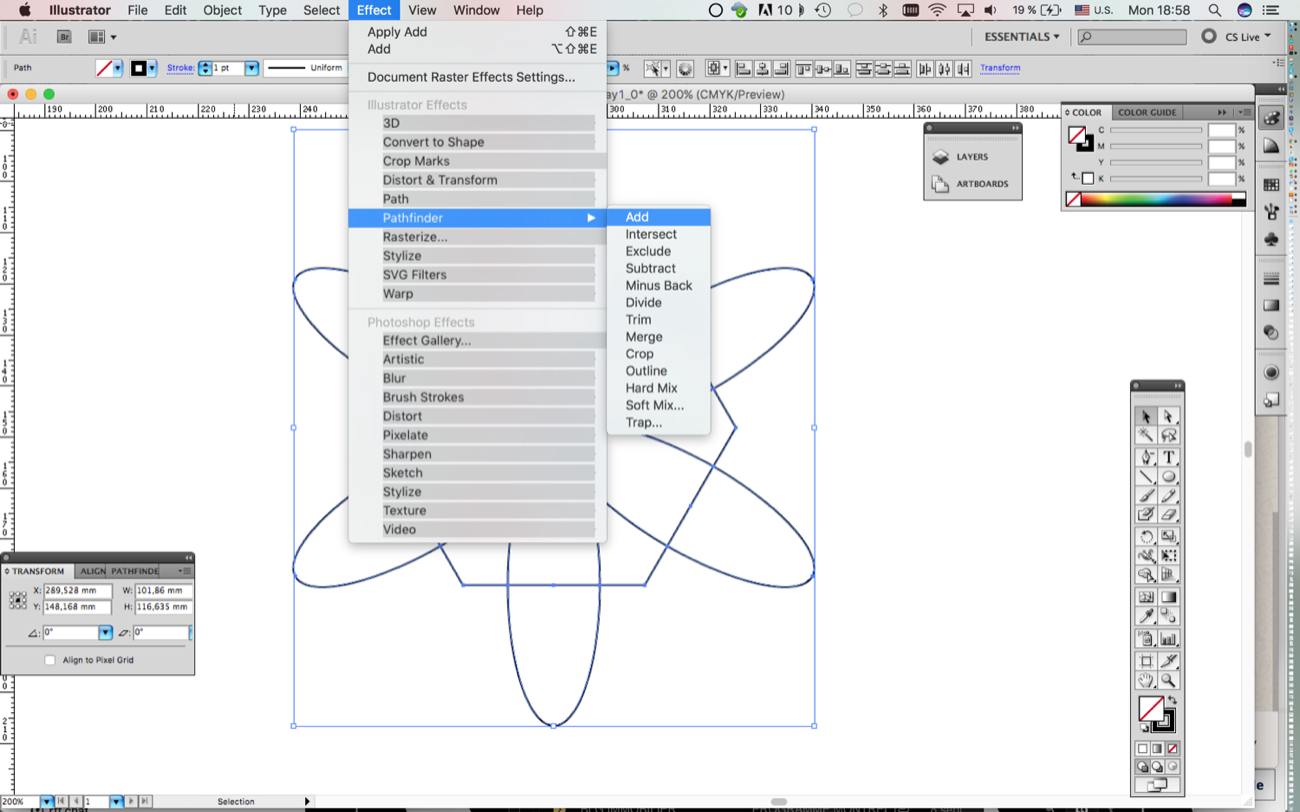 |
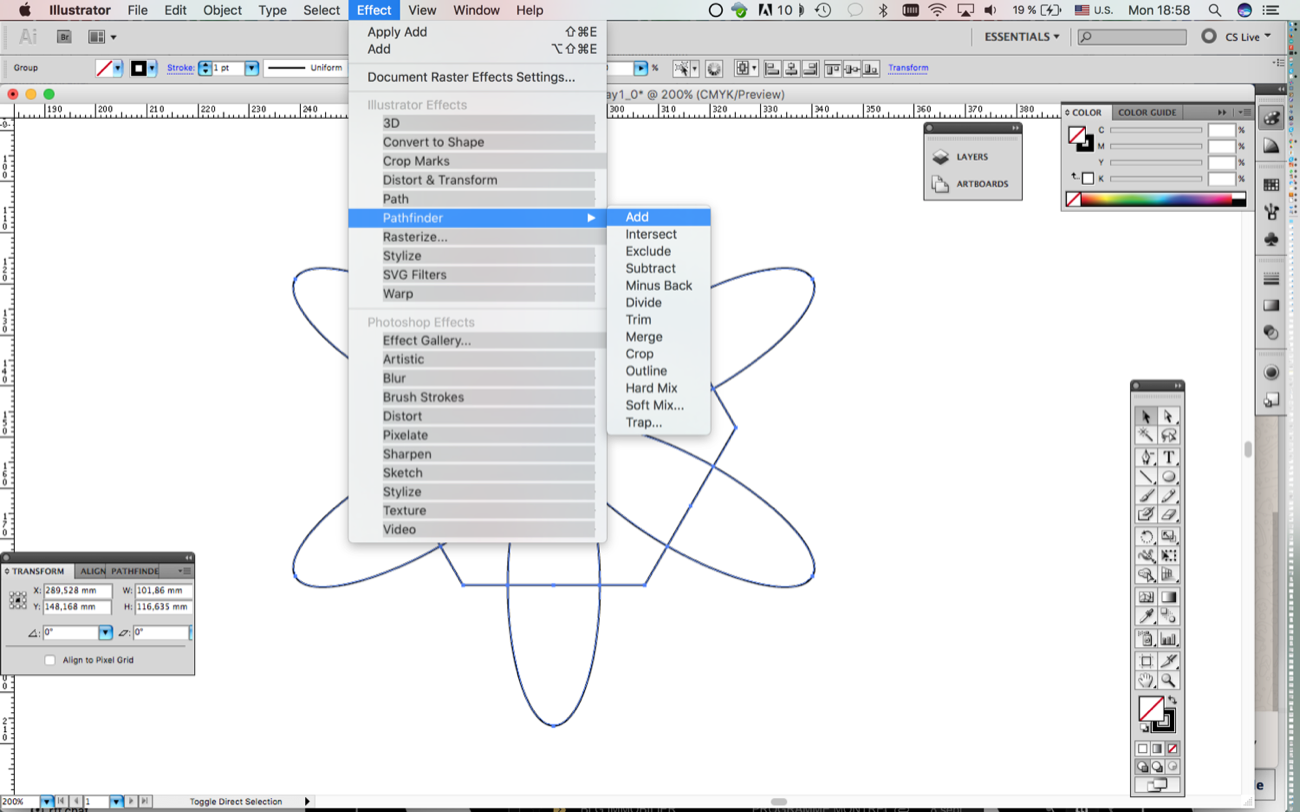 |
17 |
18 |
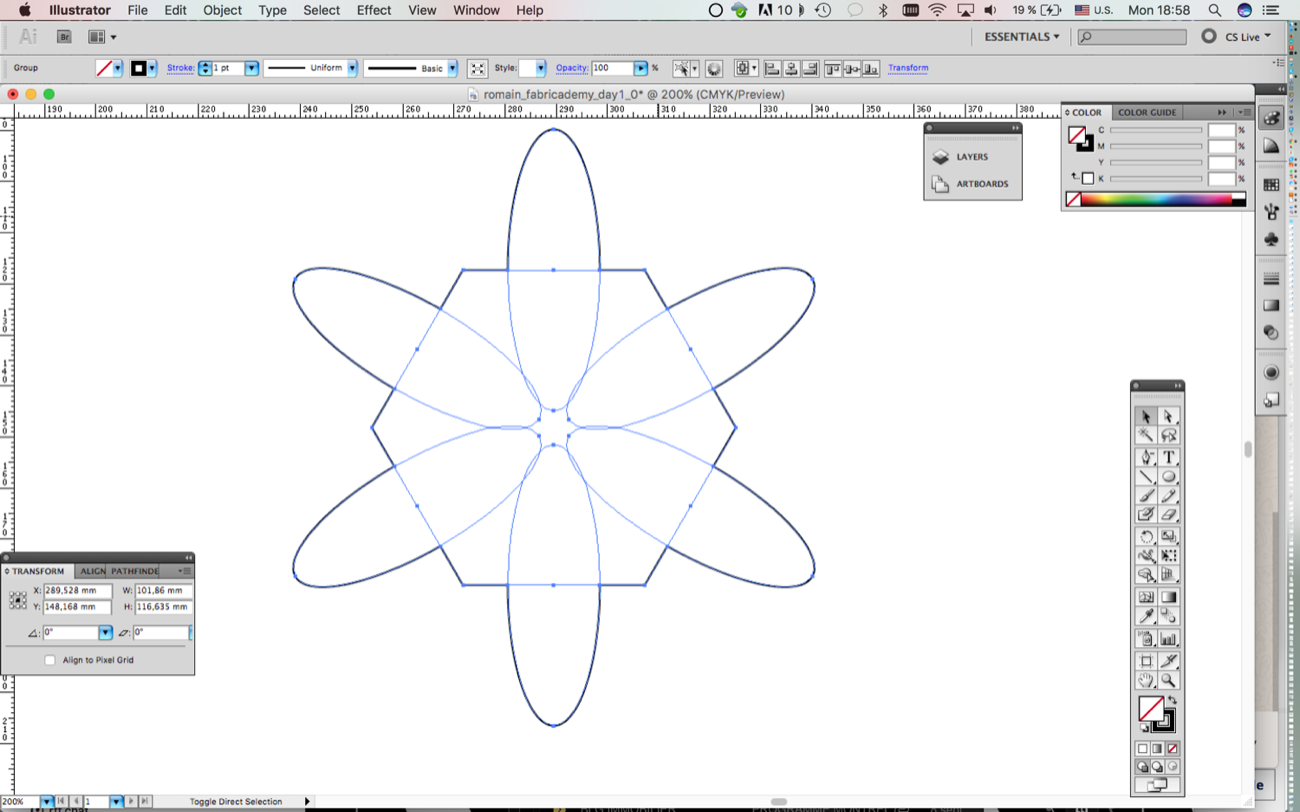 |
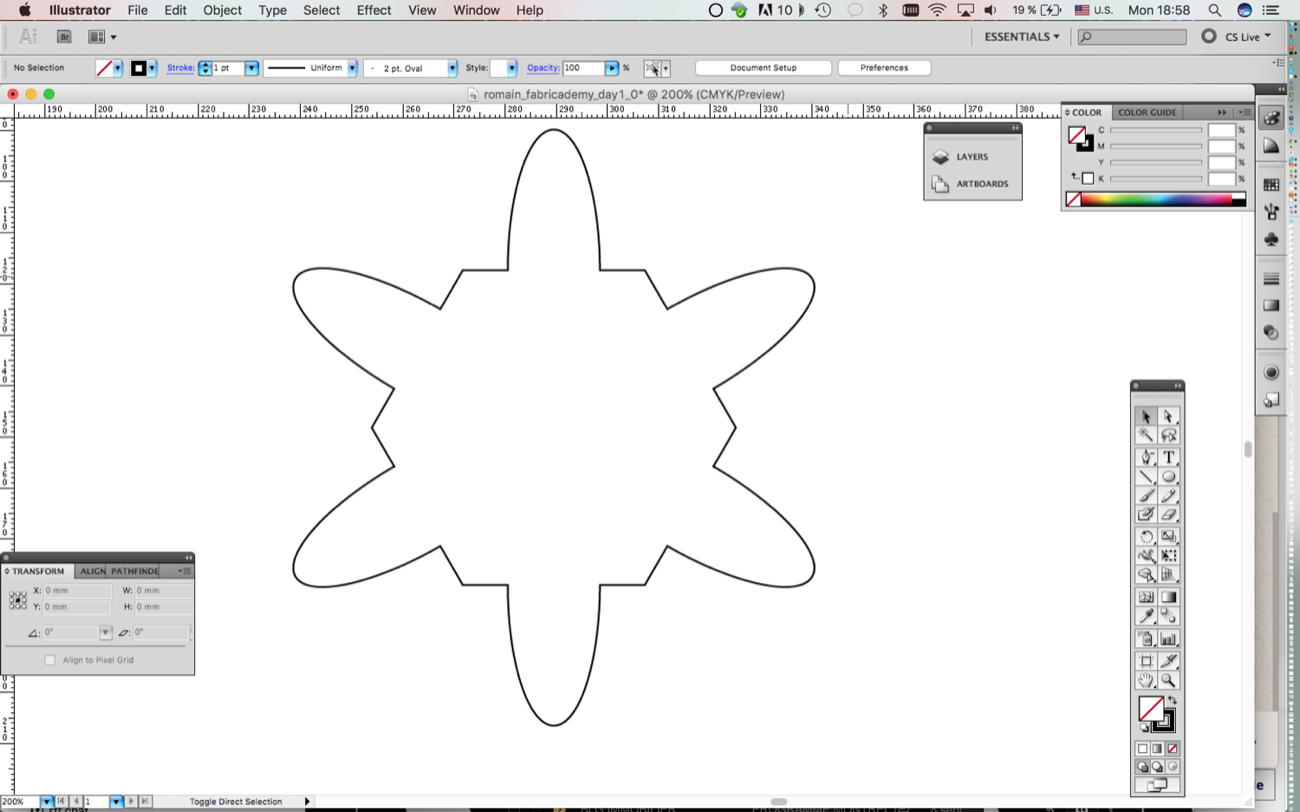 |
19 |
20 |
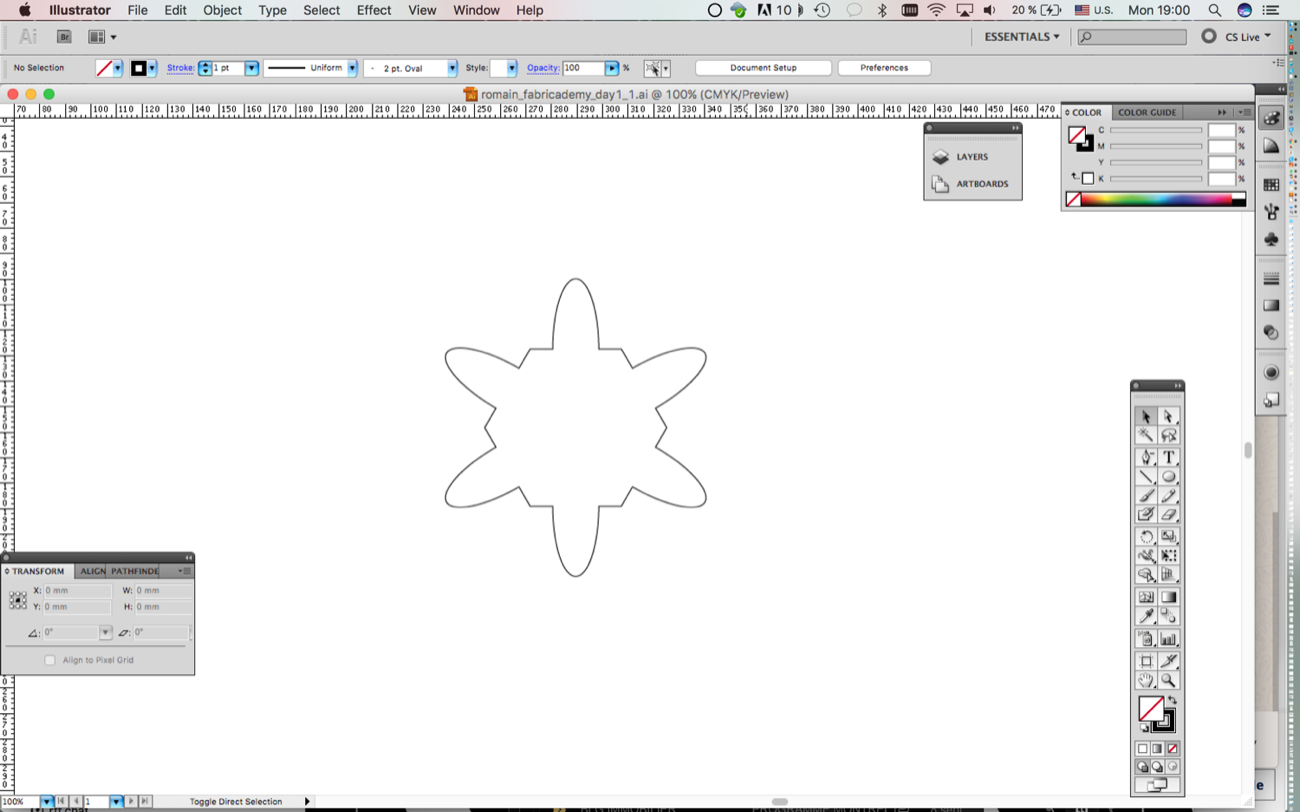 |
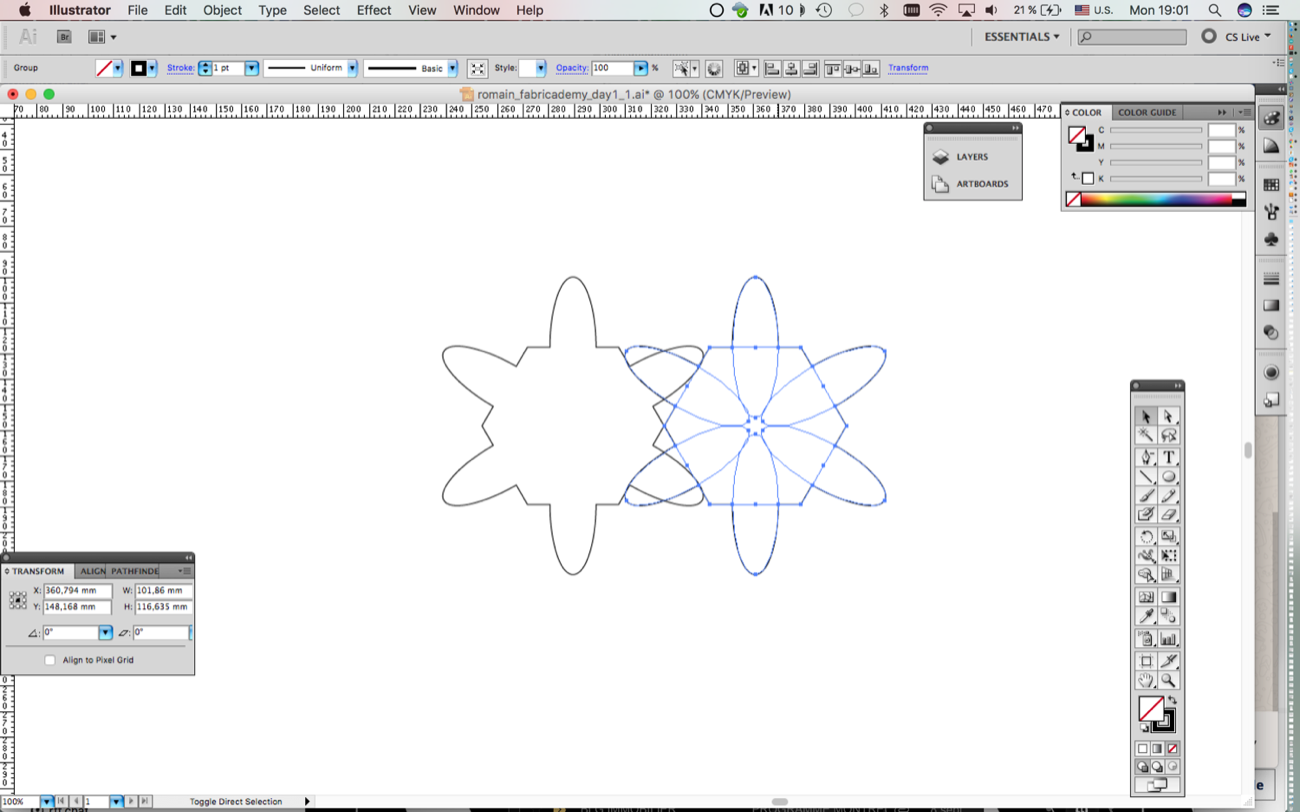 |
21 |
22 |
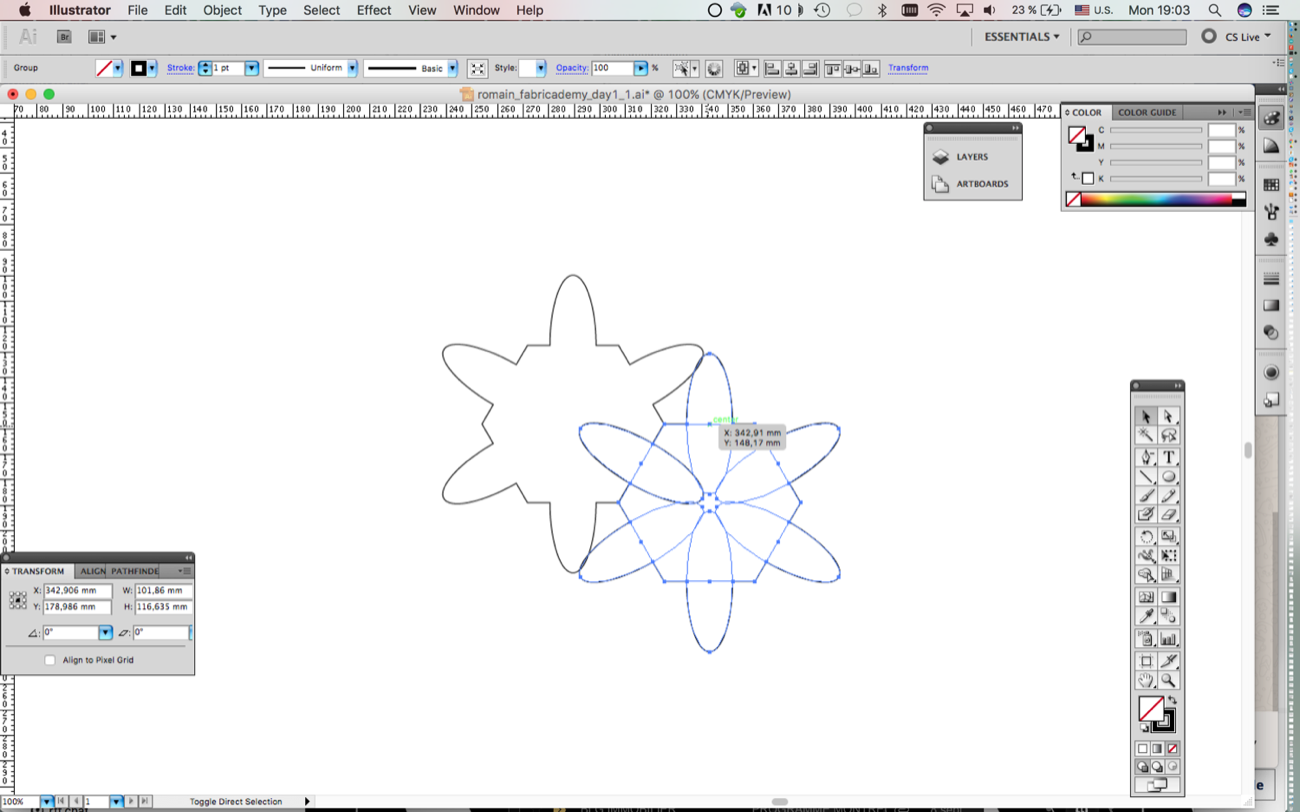 |
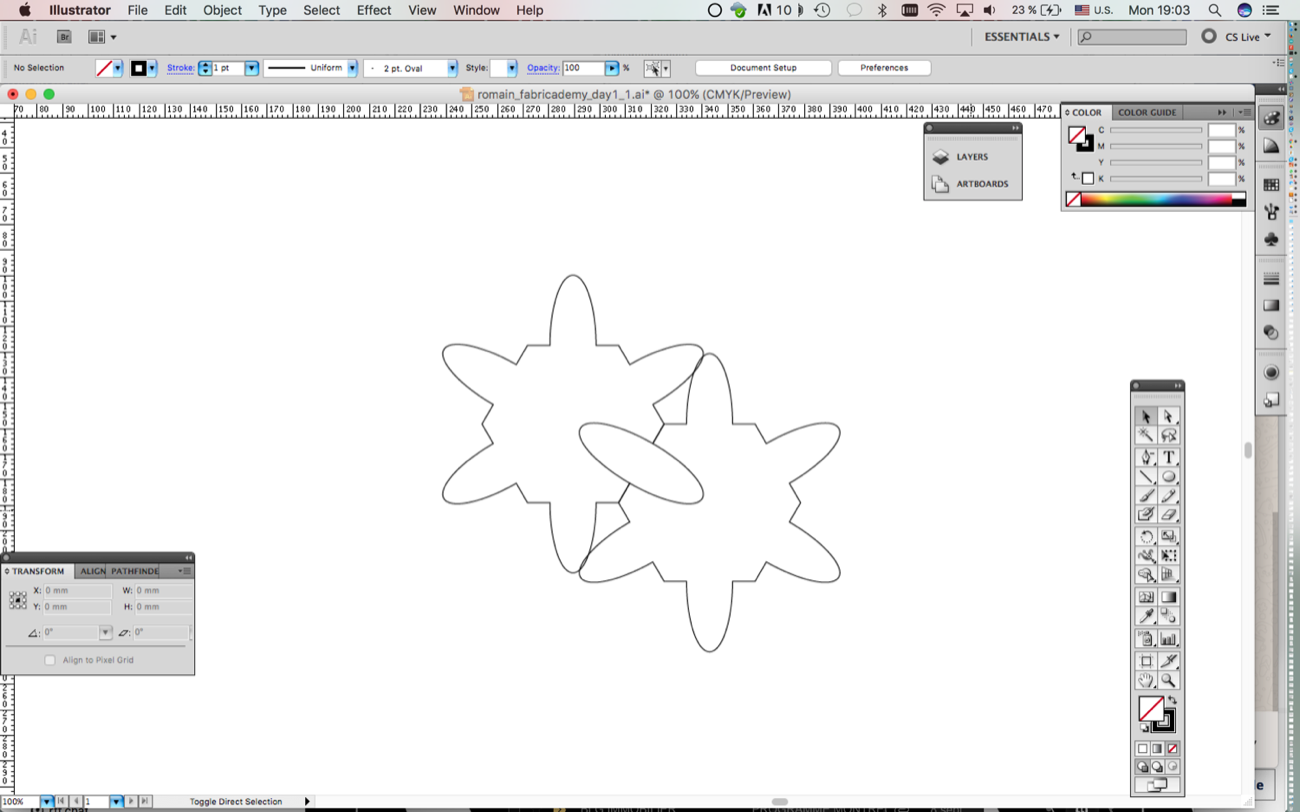 |
23 |
24 |
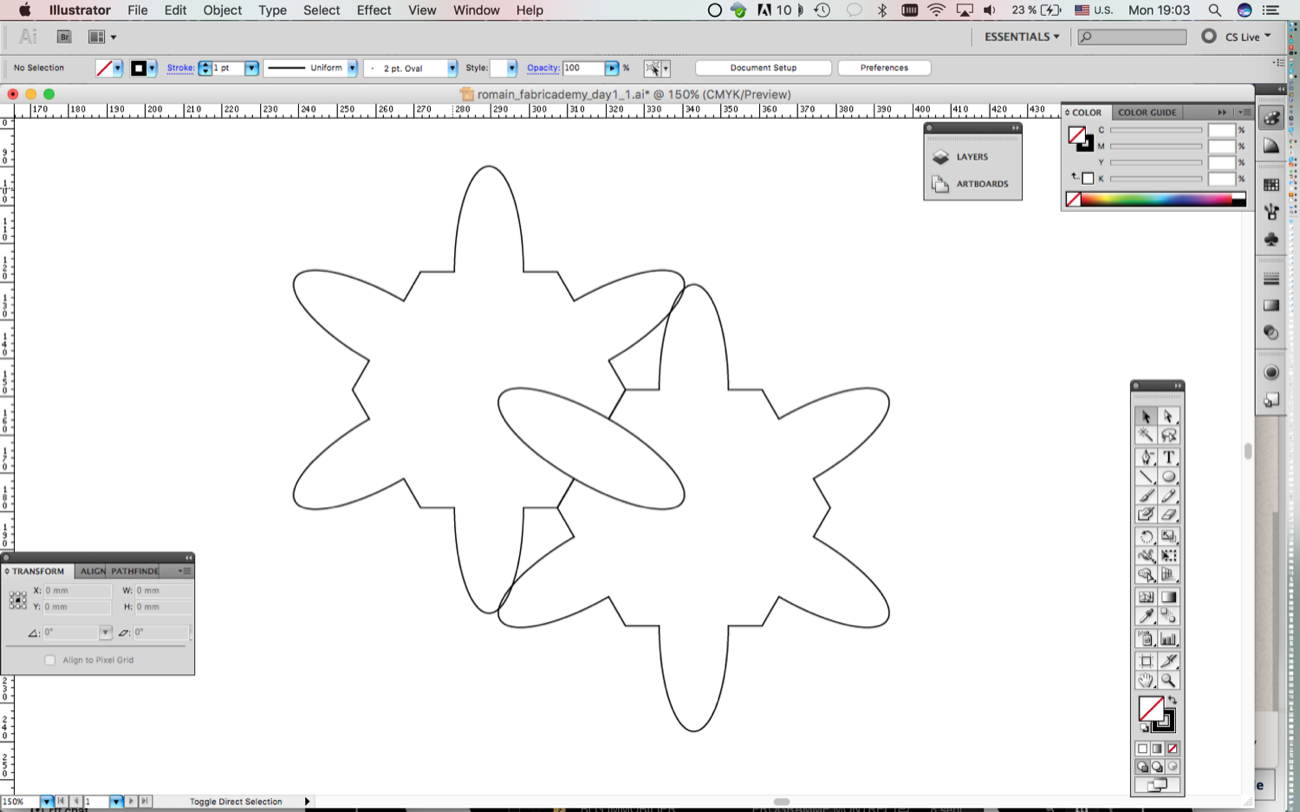 |
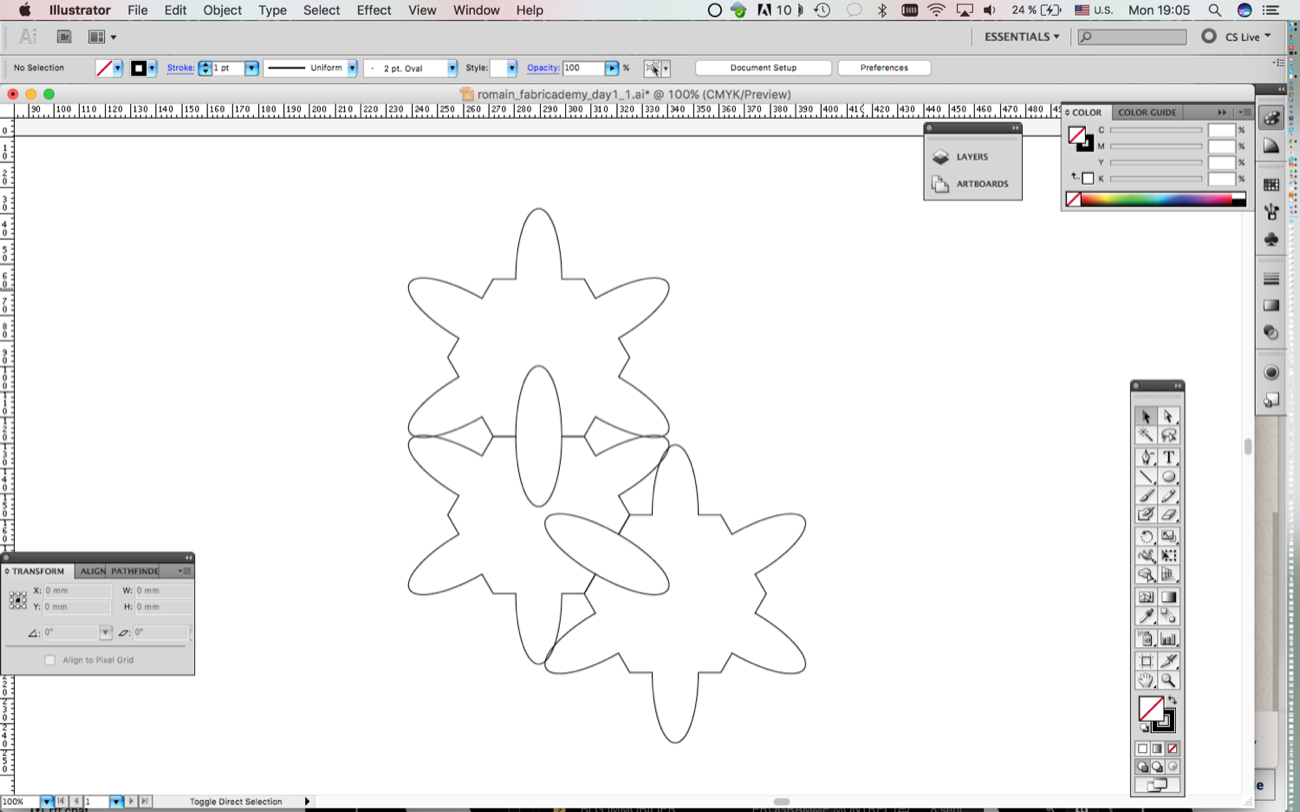 |
25 |
26 |
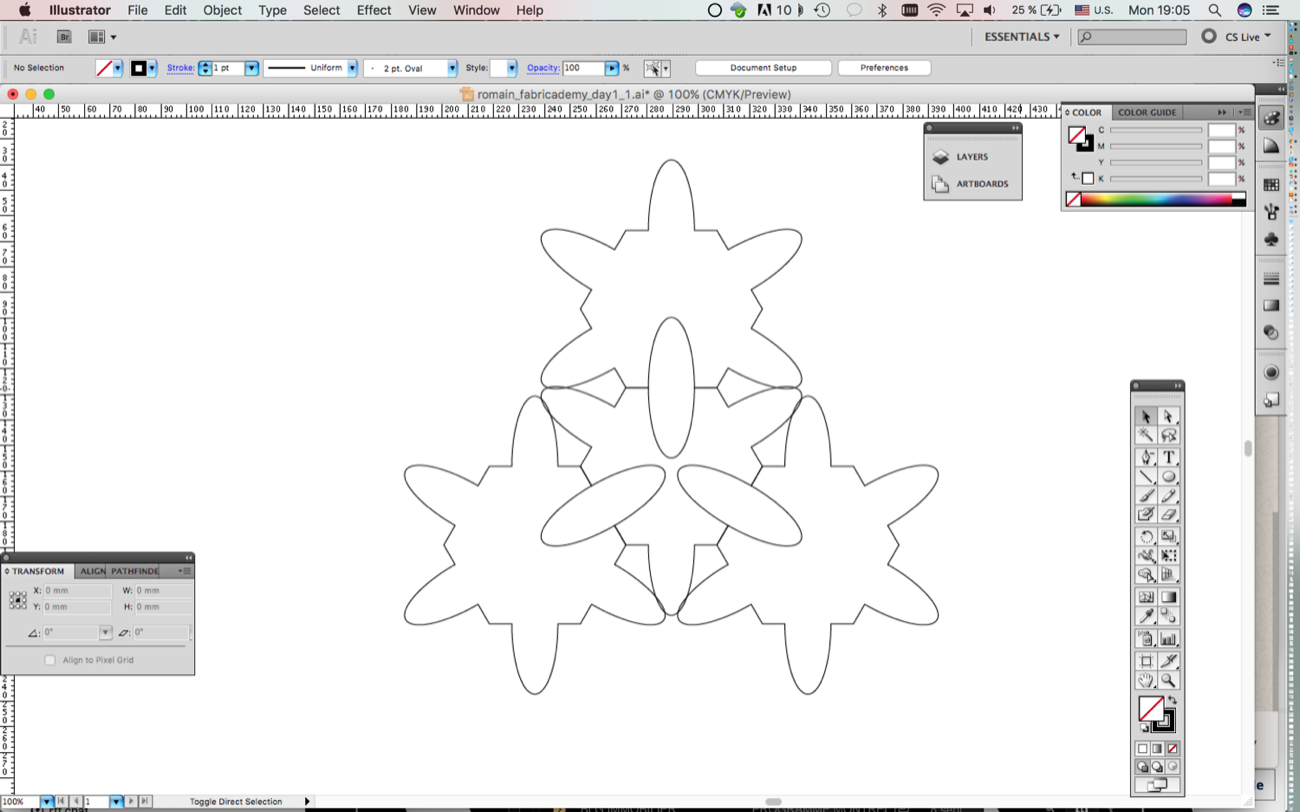 |
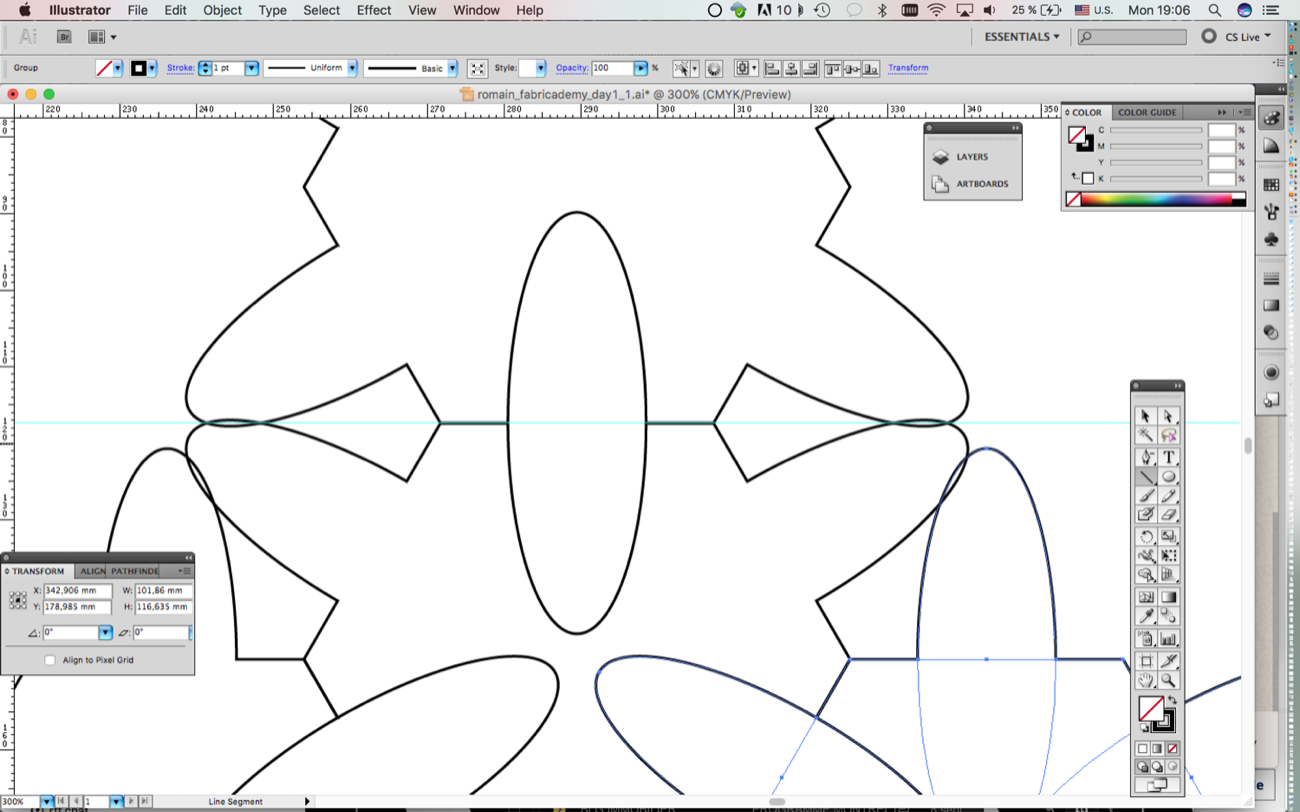 |
27 |
28 |
 |
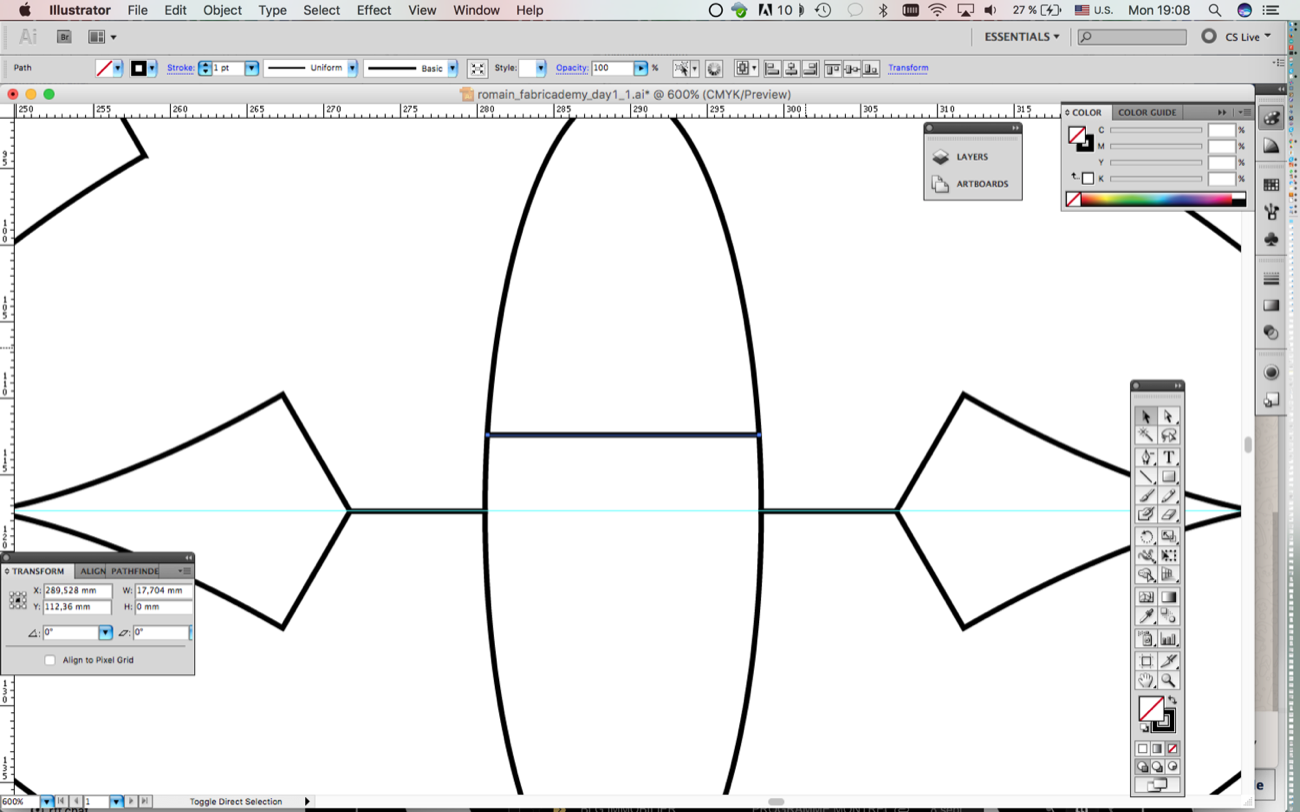 |
29 |
30 |
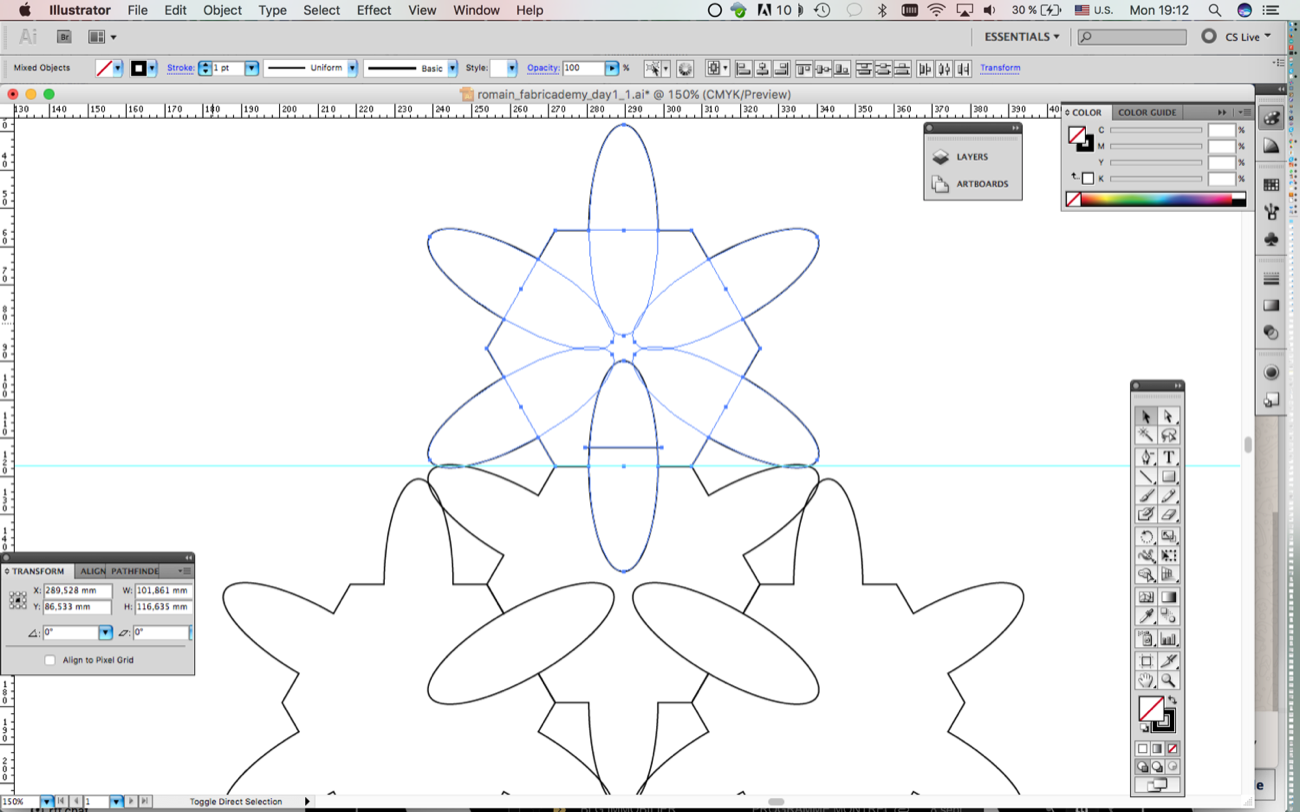 |
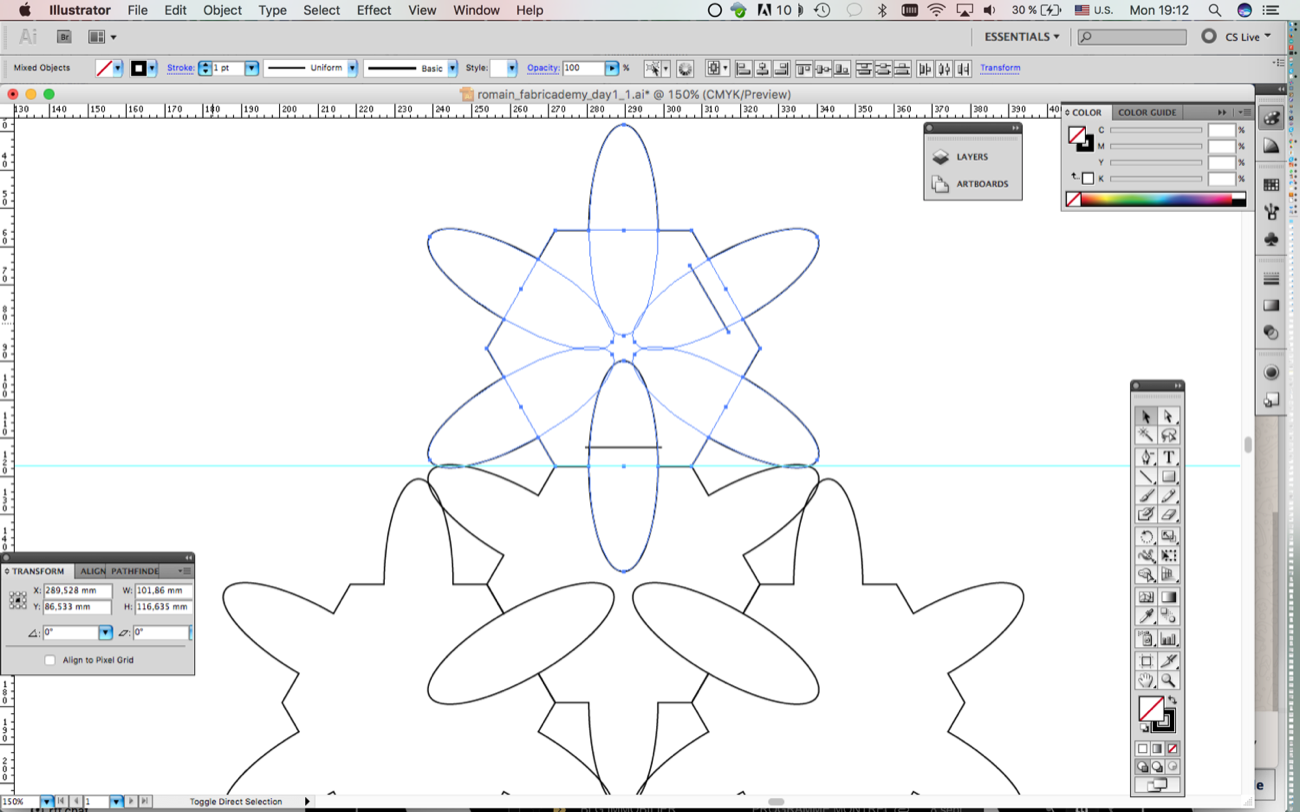 |
31 |
32 |
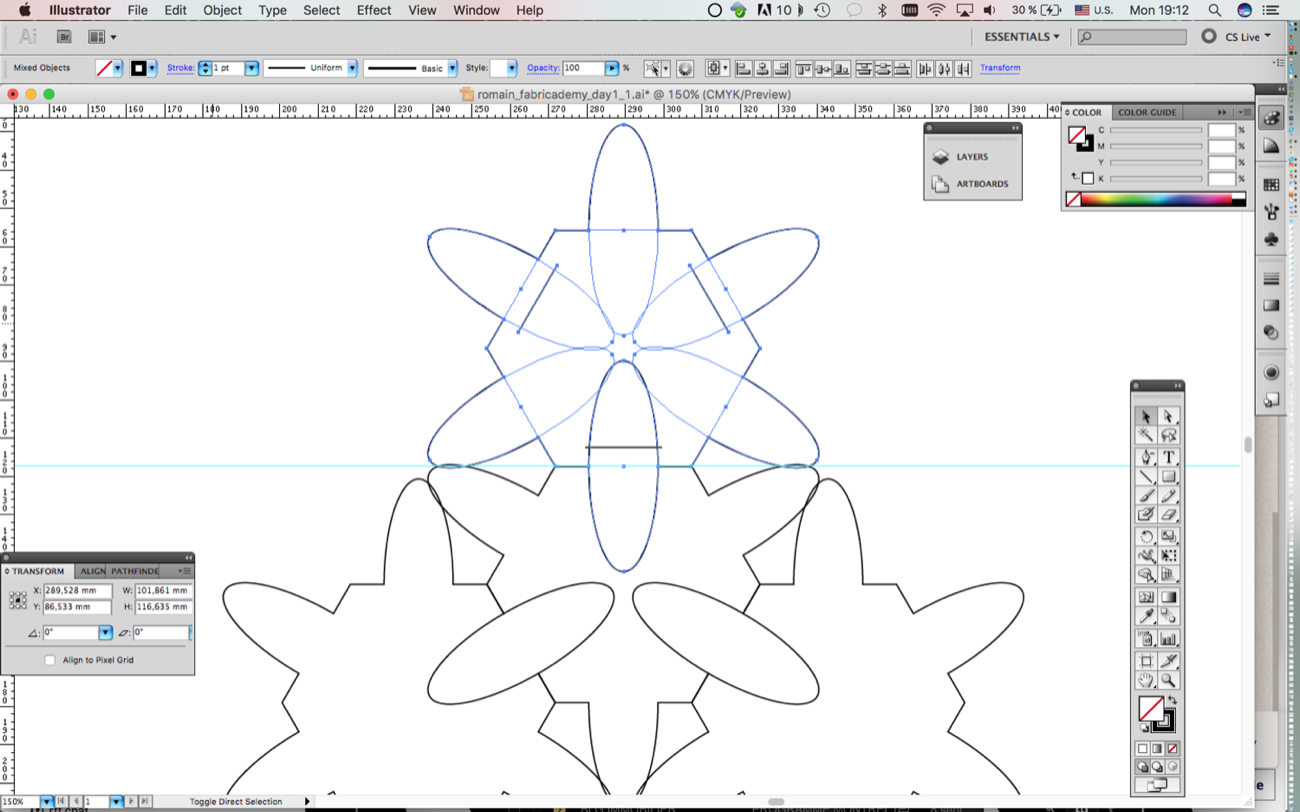 |
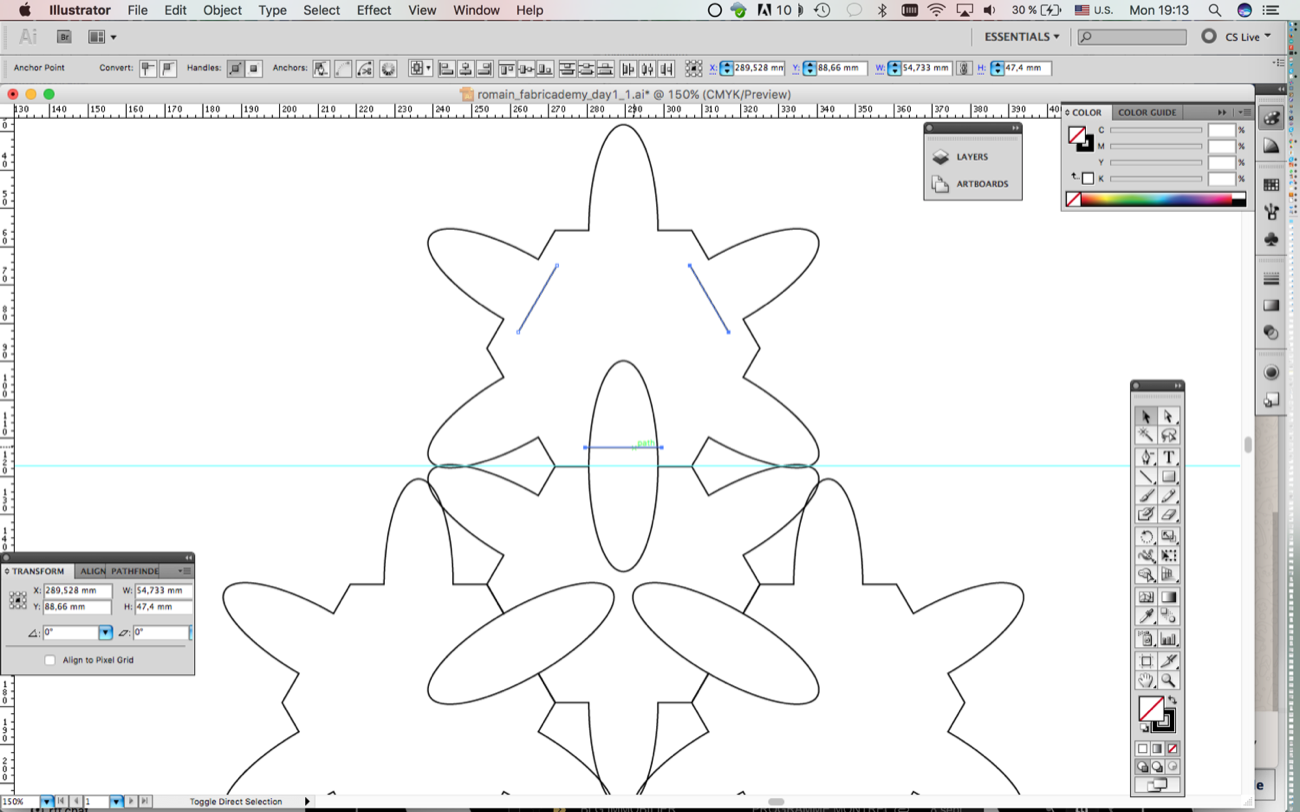 |
33 |
34 |
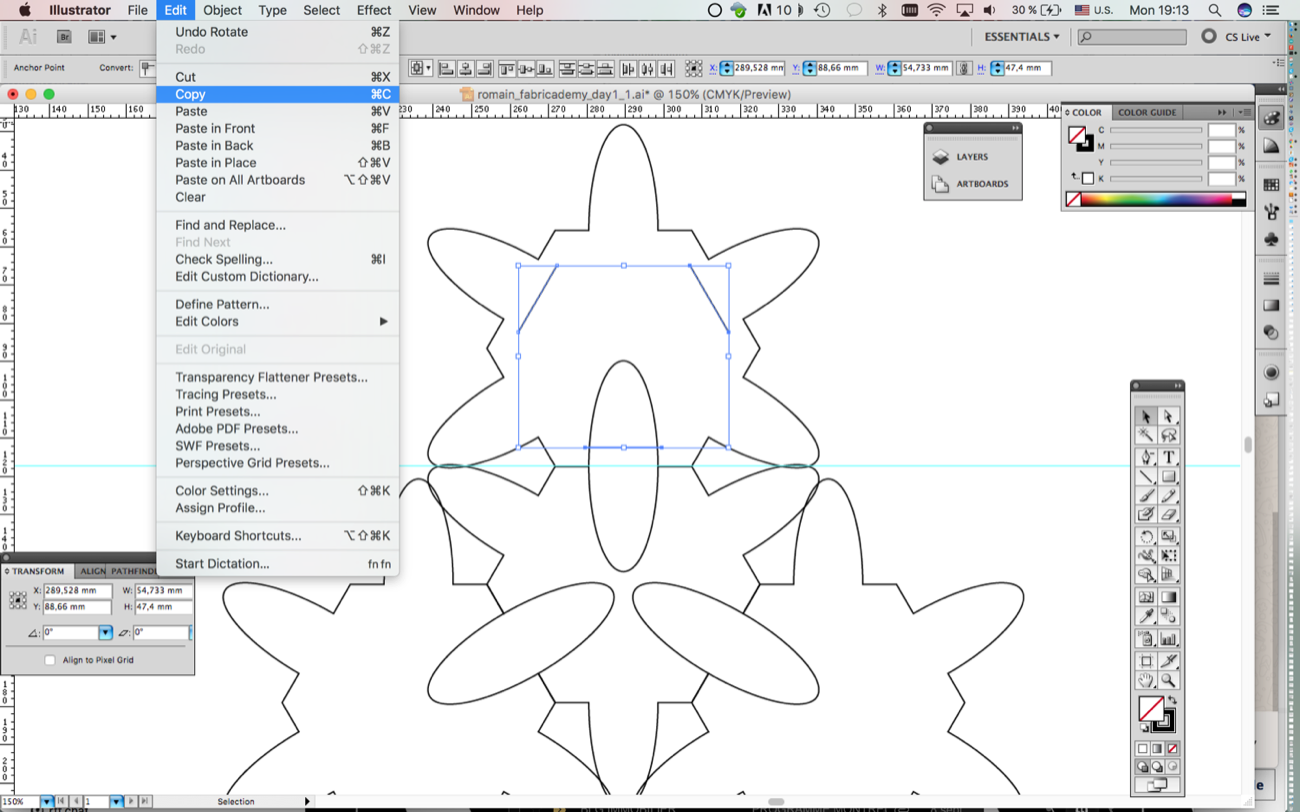 |
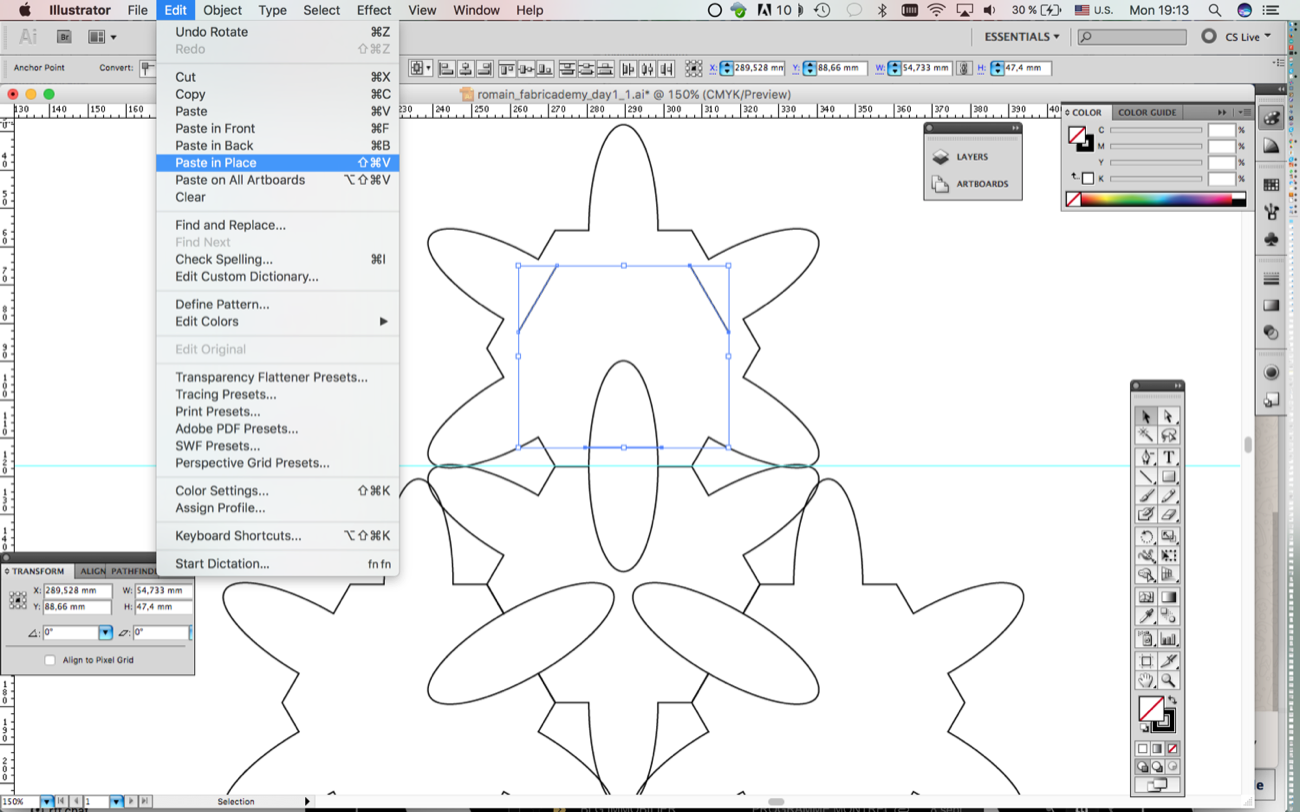 |
35 |
36 |
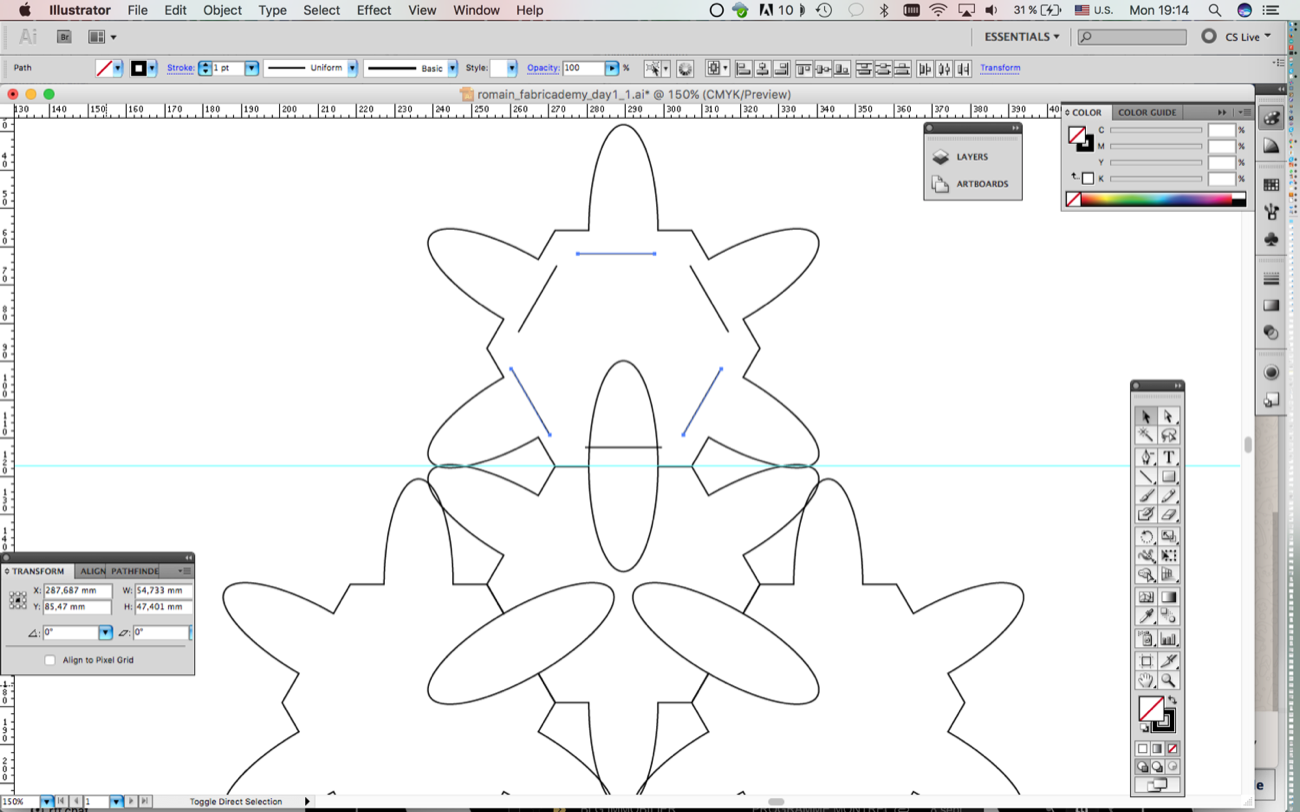 |
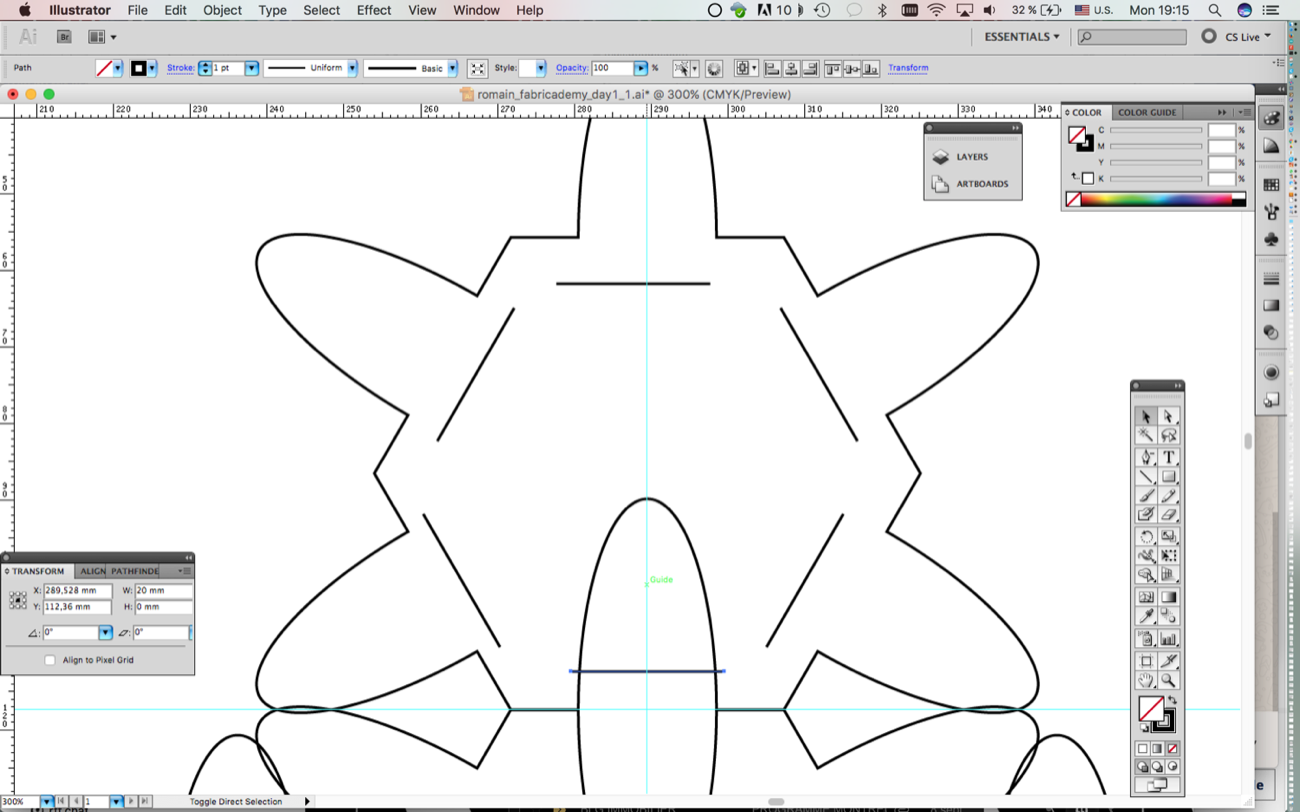 |
37 |
38 |
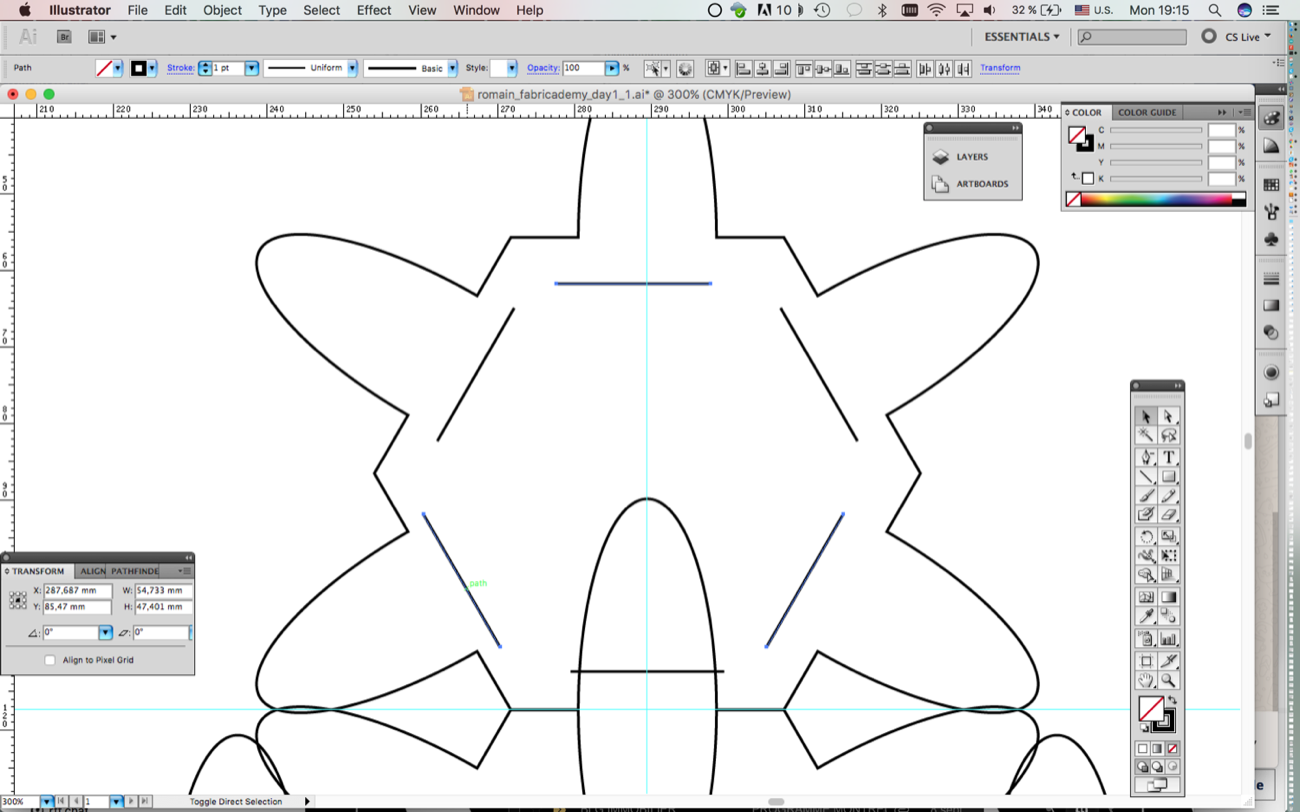 |
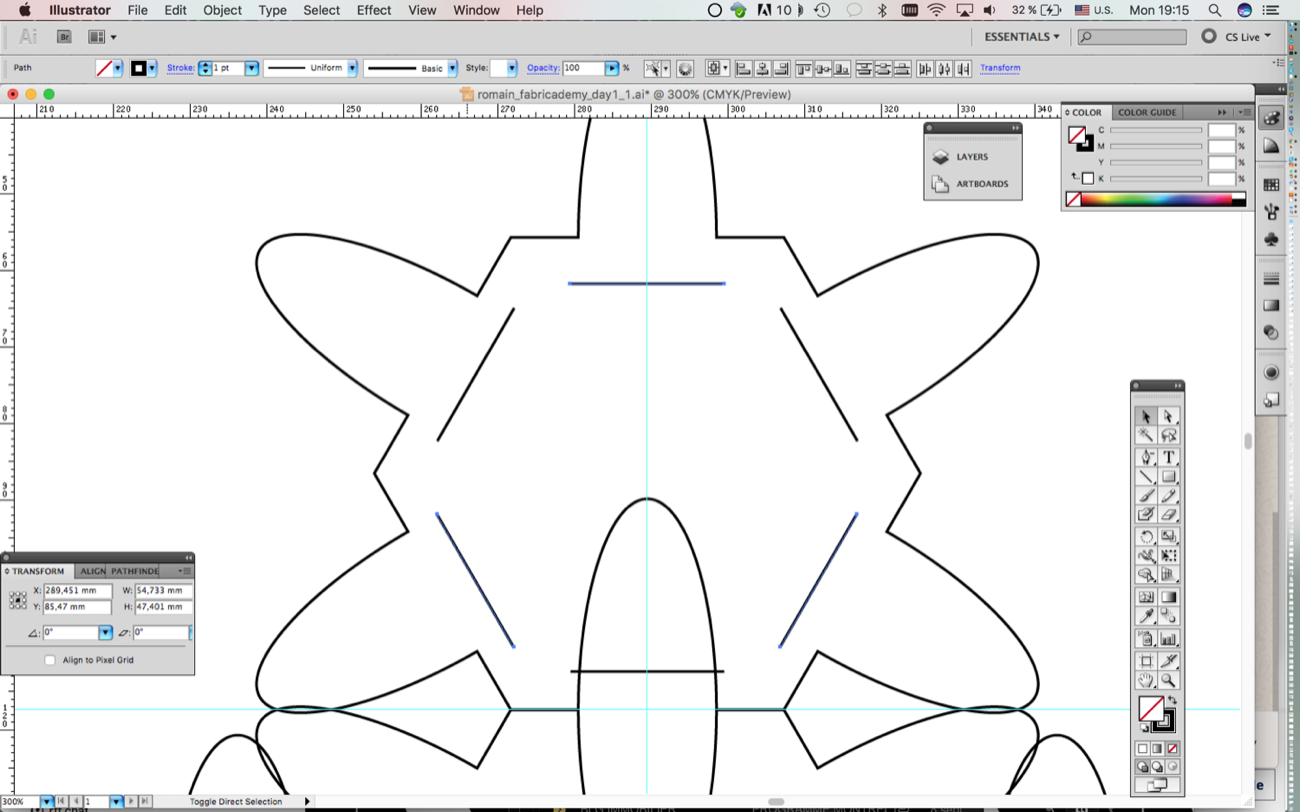 |
39 |
40 |
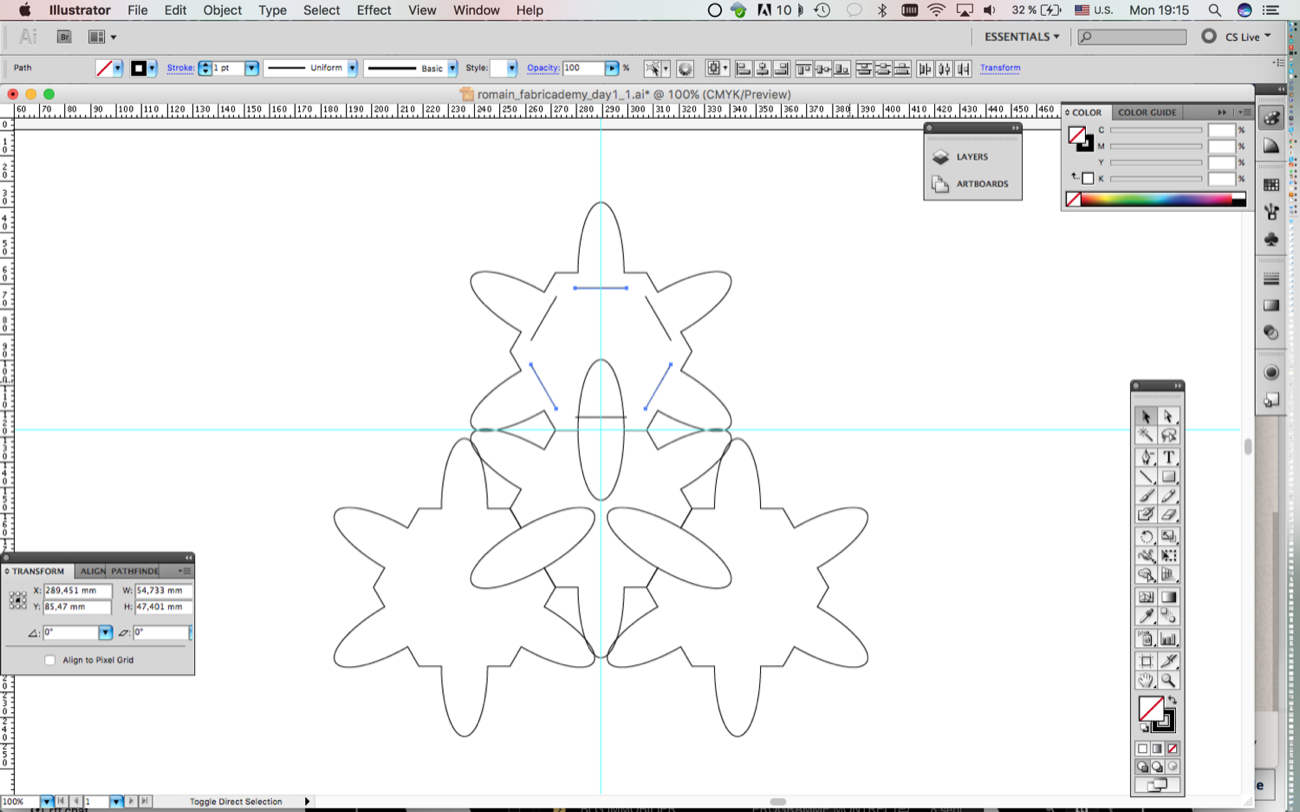 |
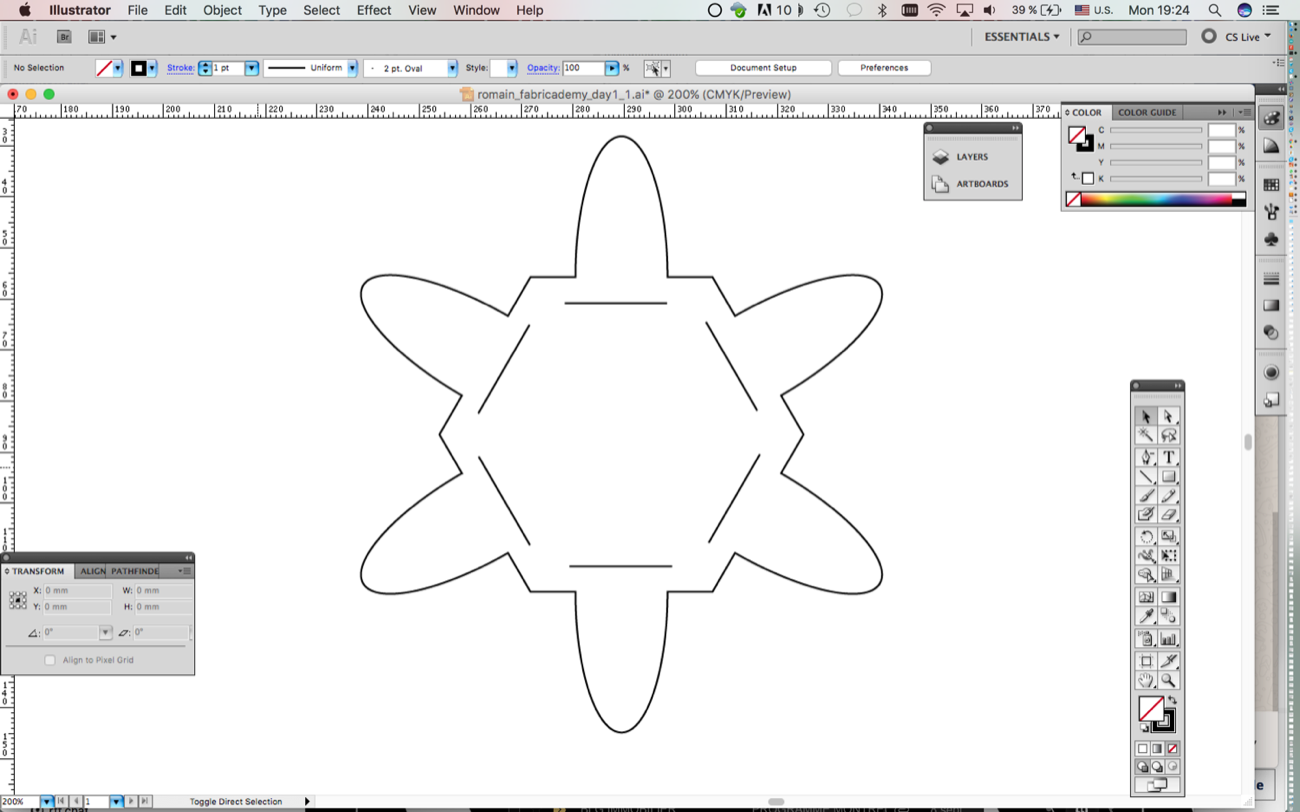 |
a |
b |
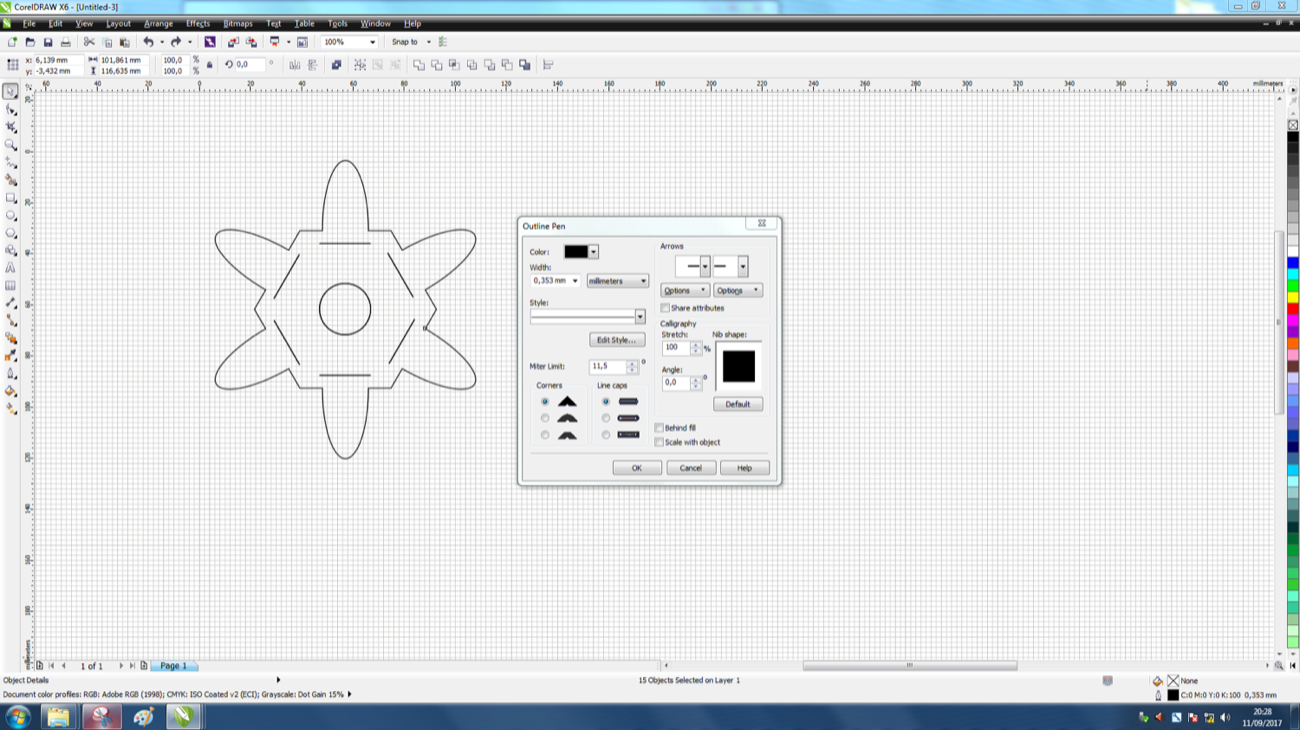 |
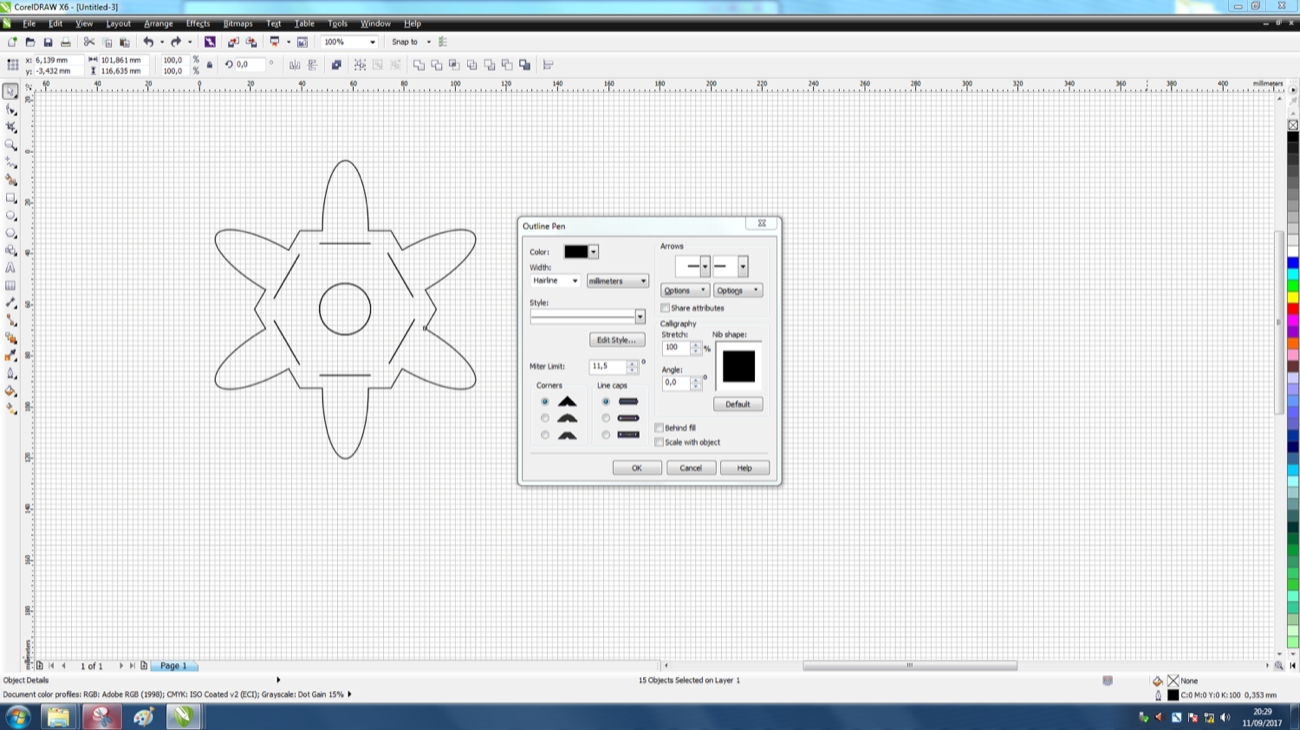 |
5 | Laser-cutting new leather-parts on Epilog Mini 40W through CorelDraw |
c |
d |
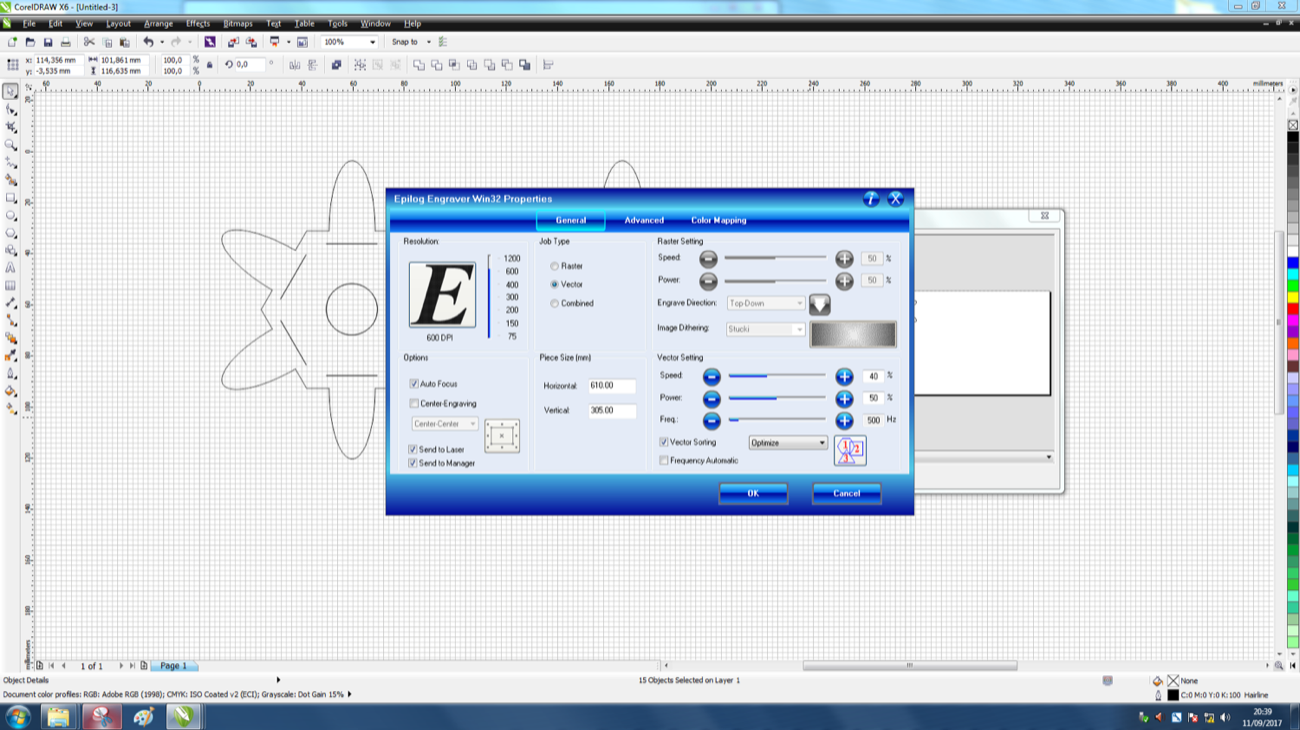 |
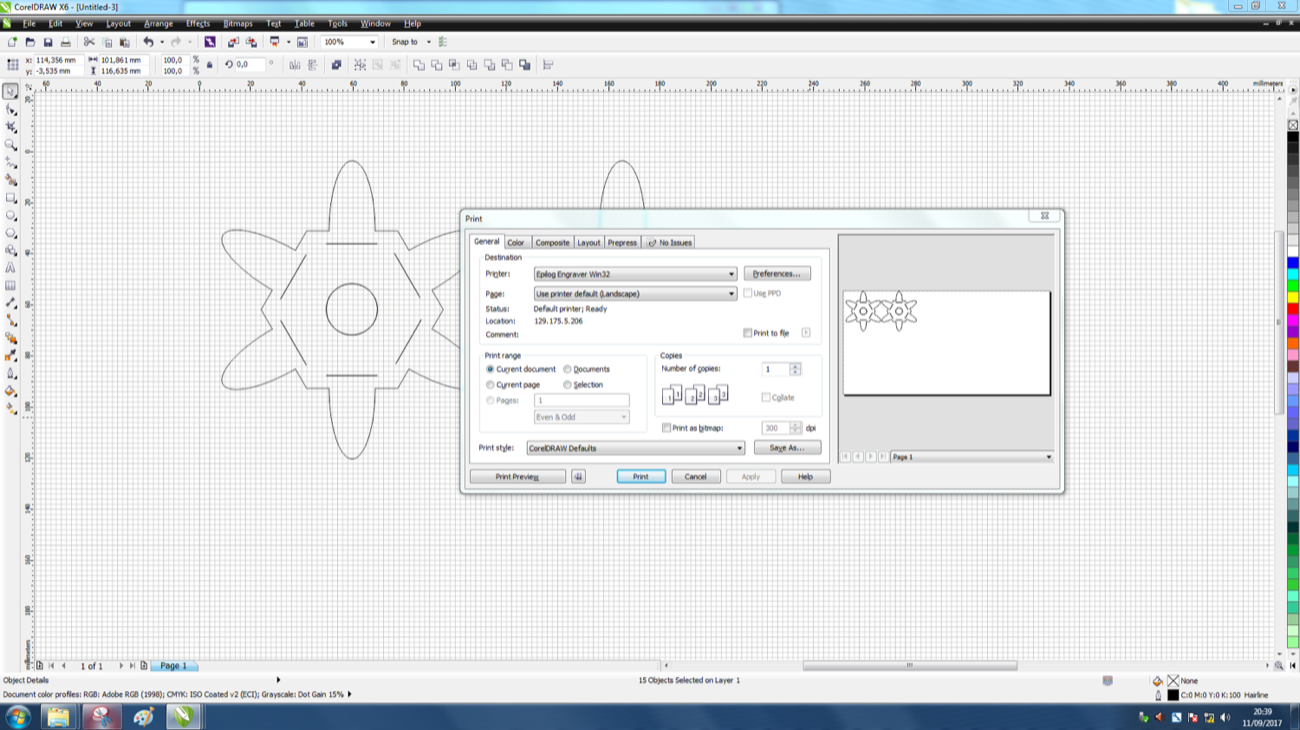 |
First test and results:
Upper Side of the Leather |
Down Side of the Leather |
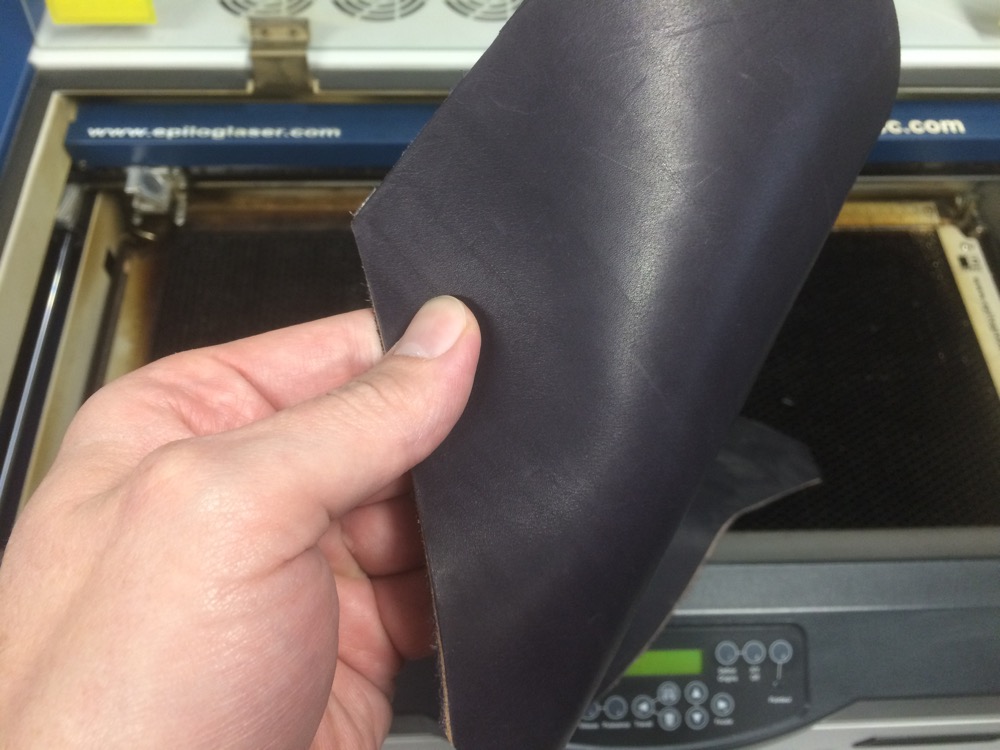 |
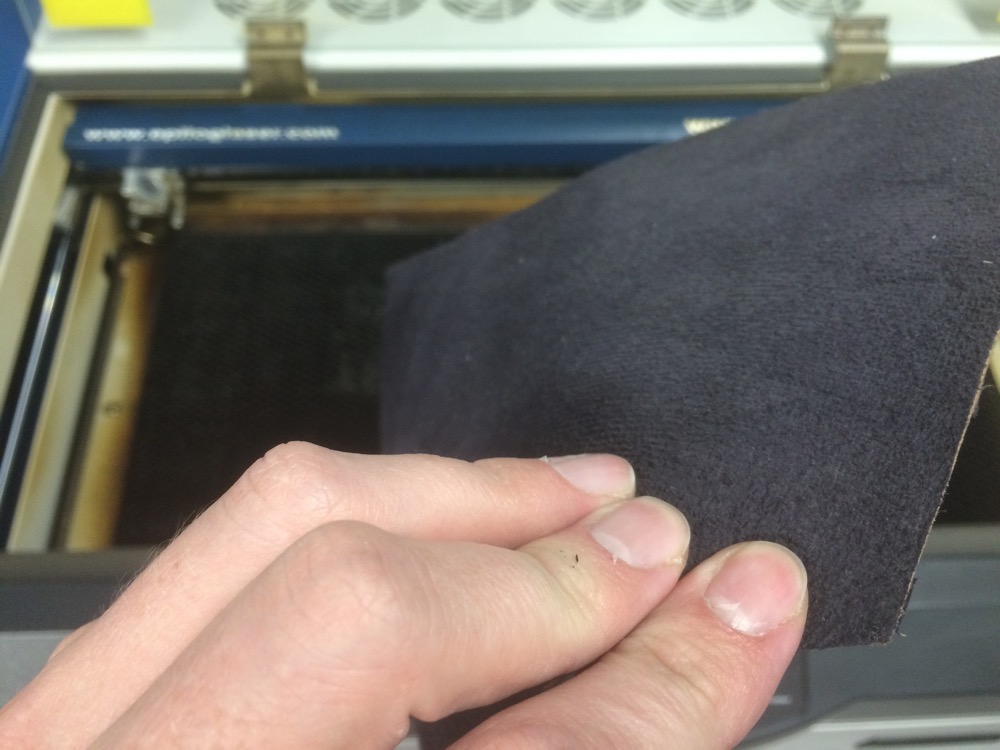 |
Thickness of the Leather (3mm) |
Leather inside the Laser-cutter |
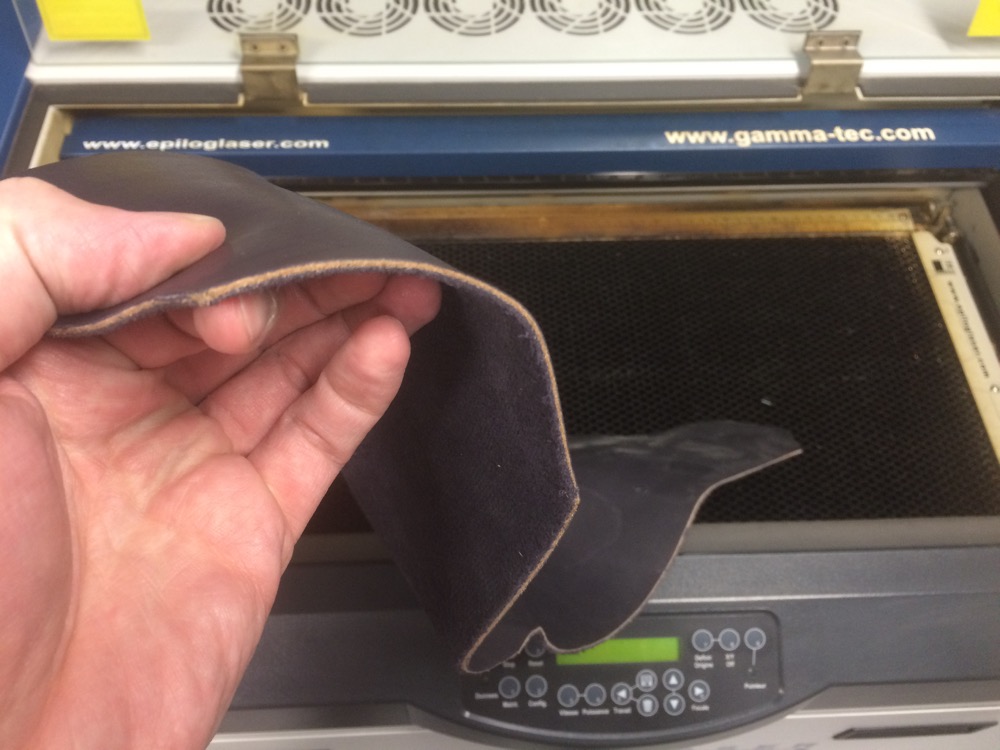 |
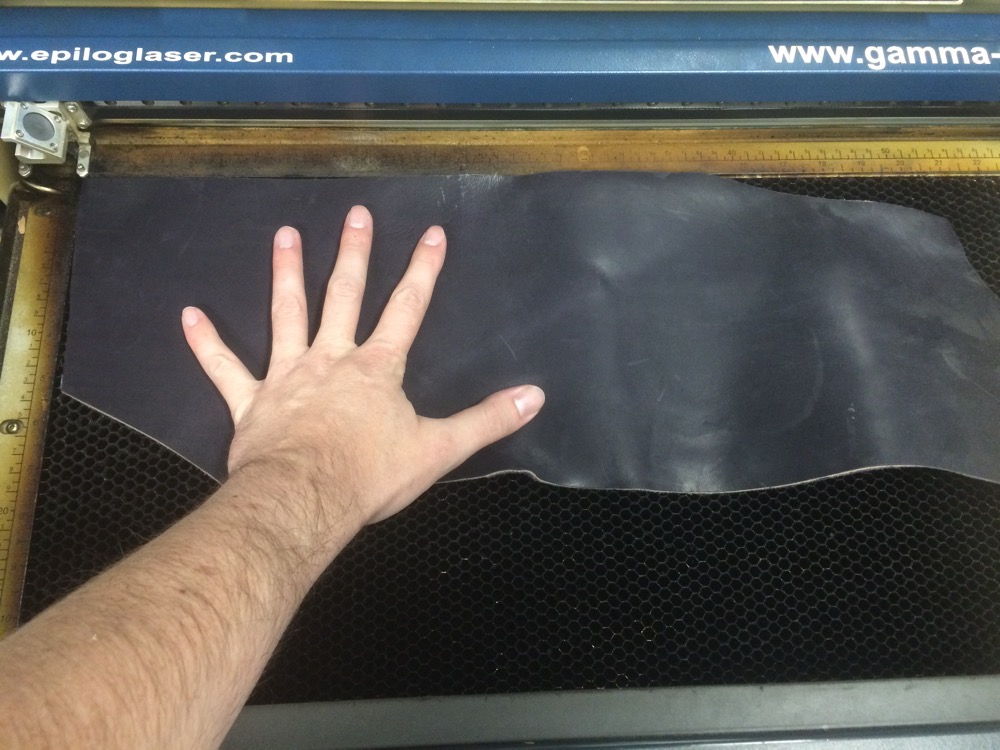 |
First cut |
2 parts |
 |
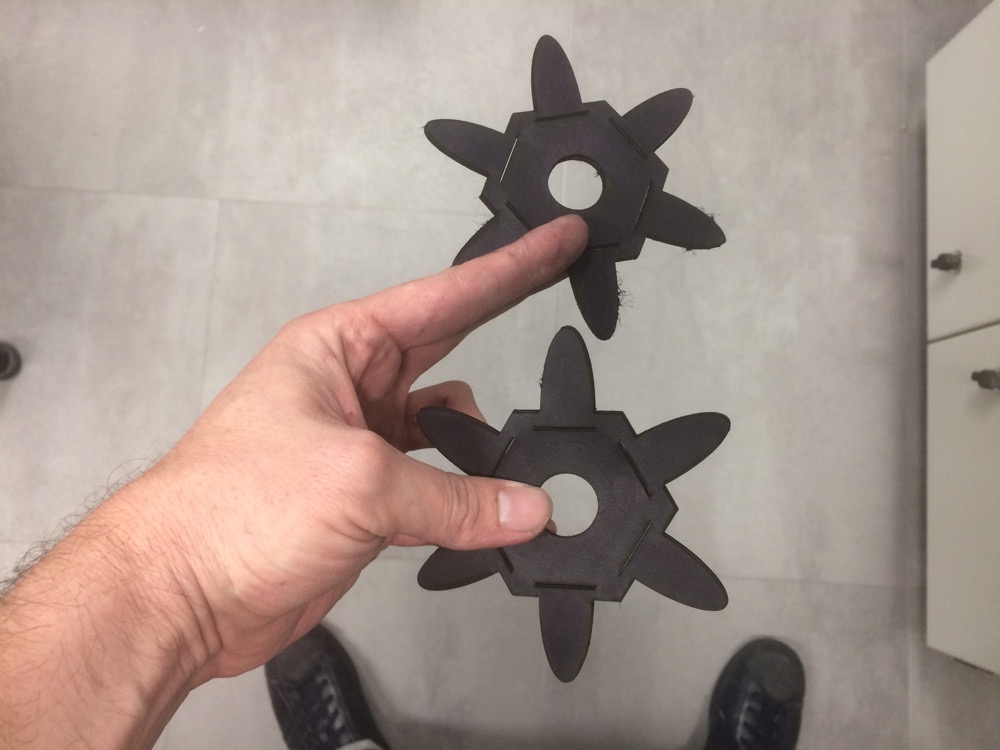 |
Parts Assembly front |
Parts Assembly back |
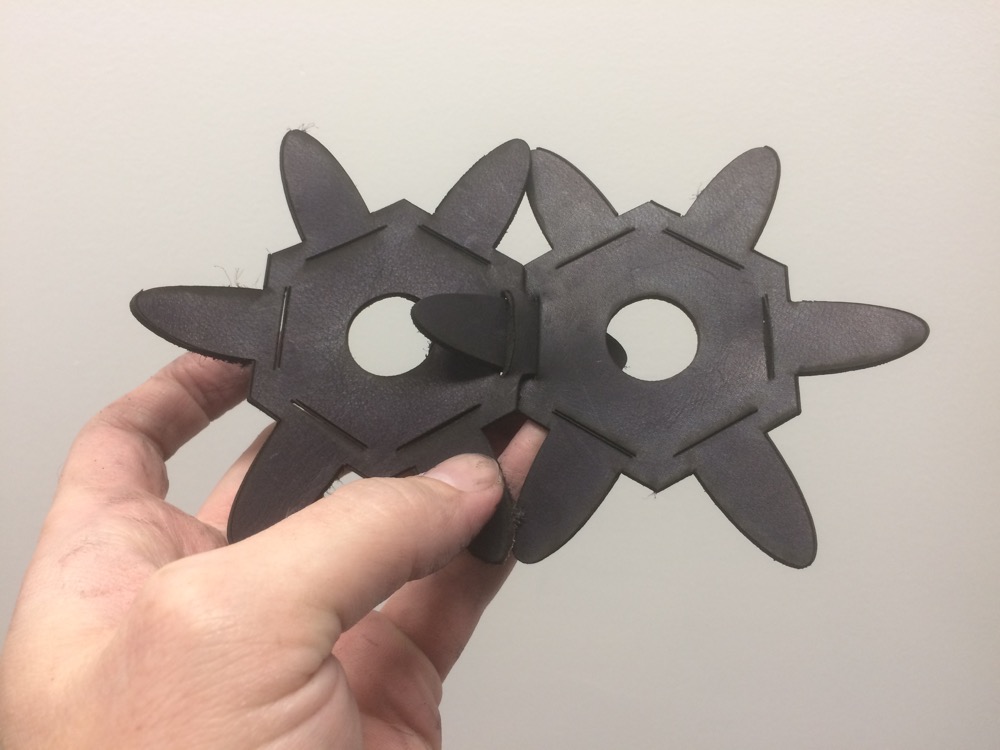 |
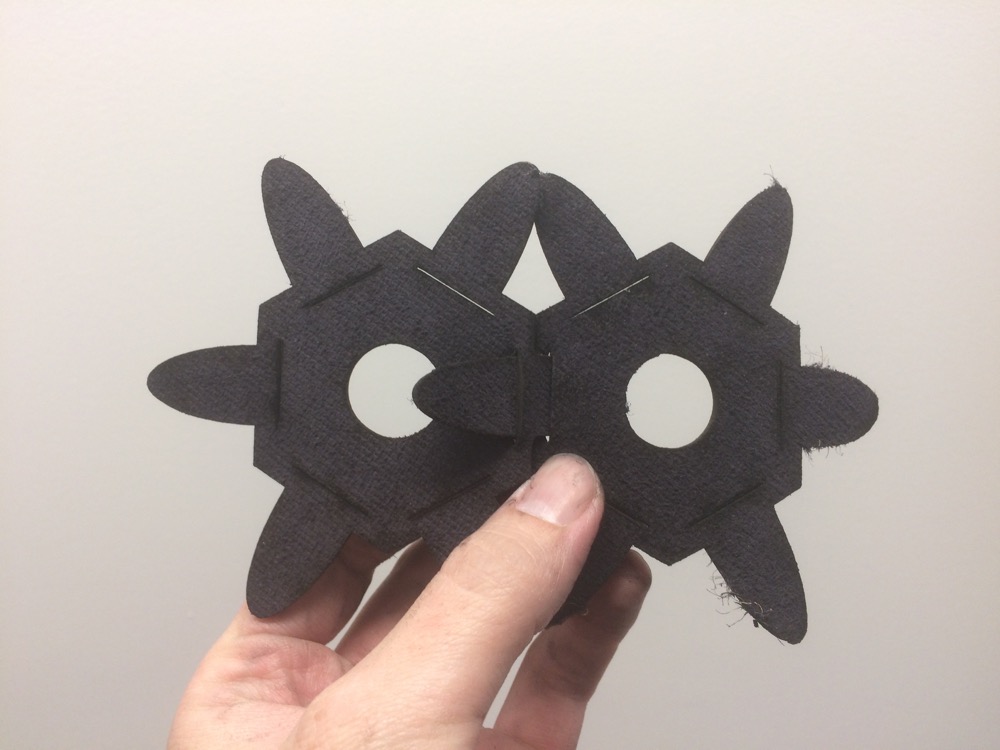 |
6 | Laser-cutting leather-parts on Epilog Fusion M2+ 75W through CorelDraW |
Laser-cutting leather parts with the Epilog Fusion is far better than with the mini because the working area is a lot wider (1000x700mm vs 600x300mm for the Mini) and because the laser on the Fusion has more wattage (75W vs 40W for the Mini). I now can cut parts in one a single pass using the settings below:
-Speed = 15%
-Power = 100%
-Frequency = 50%
-No “Power Compression”
Various Scales of Reconfigurable Pattern |
New Laser-cutter Settings |
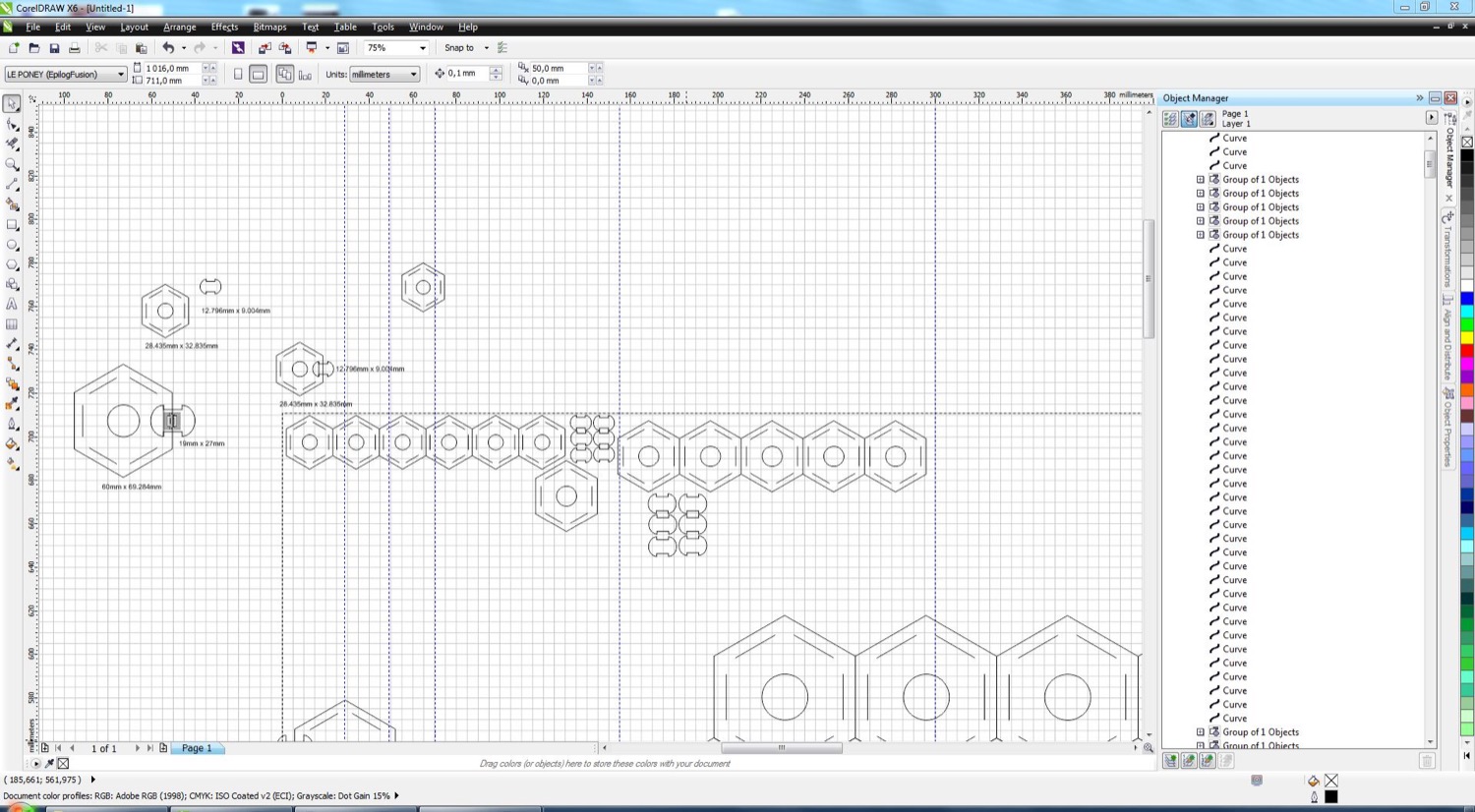 |
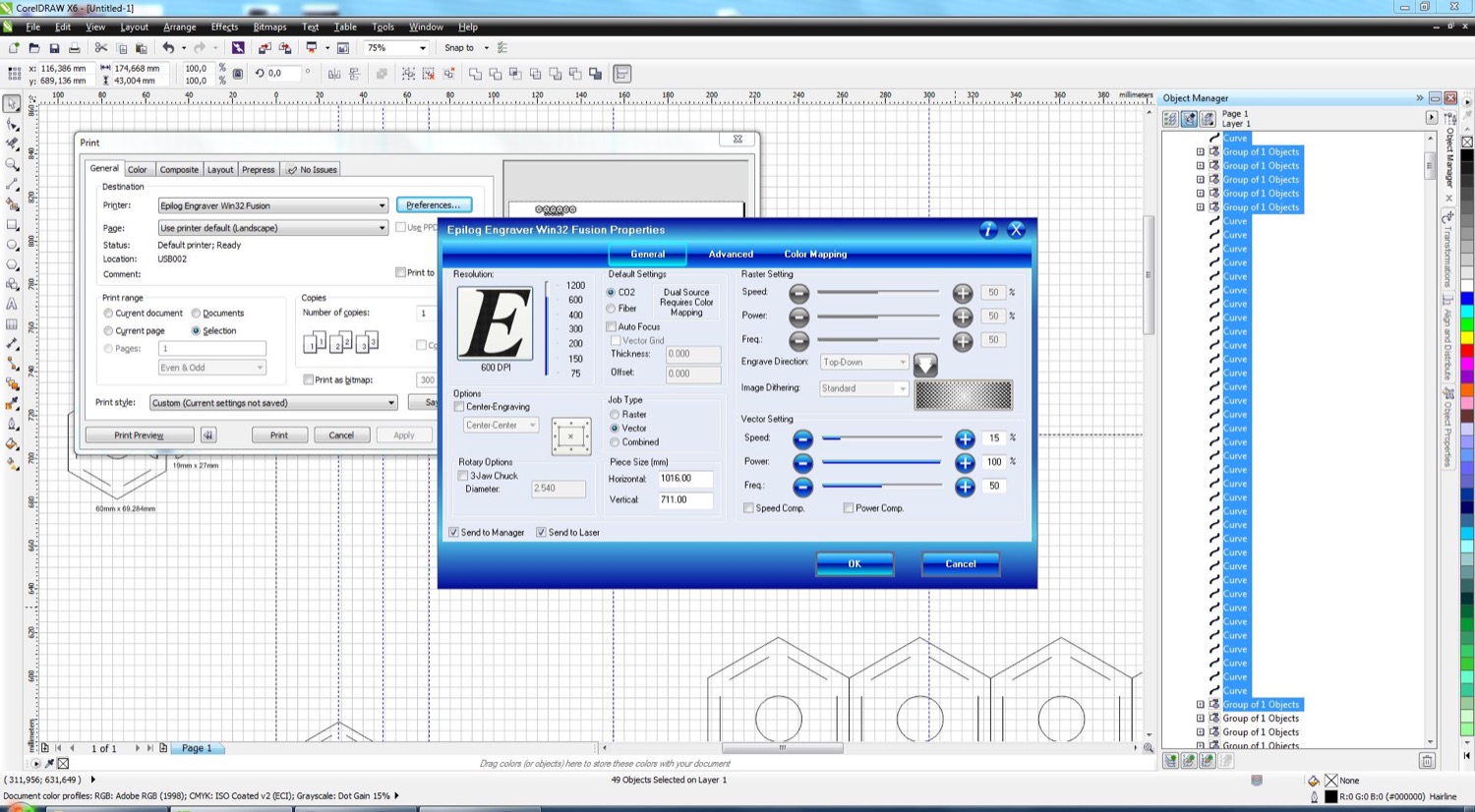 |
Second test and results:
30mmx30mm Patterns and joinery |
3 Different scales of the same pattern |
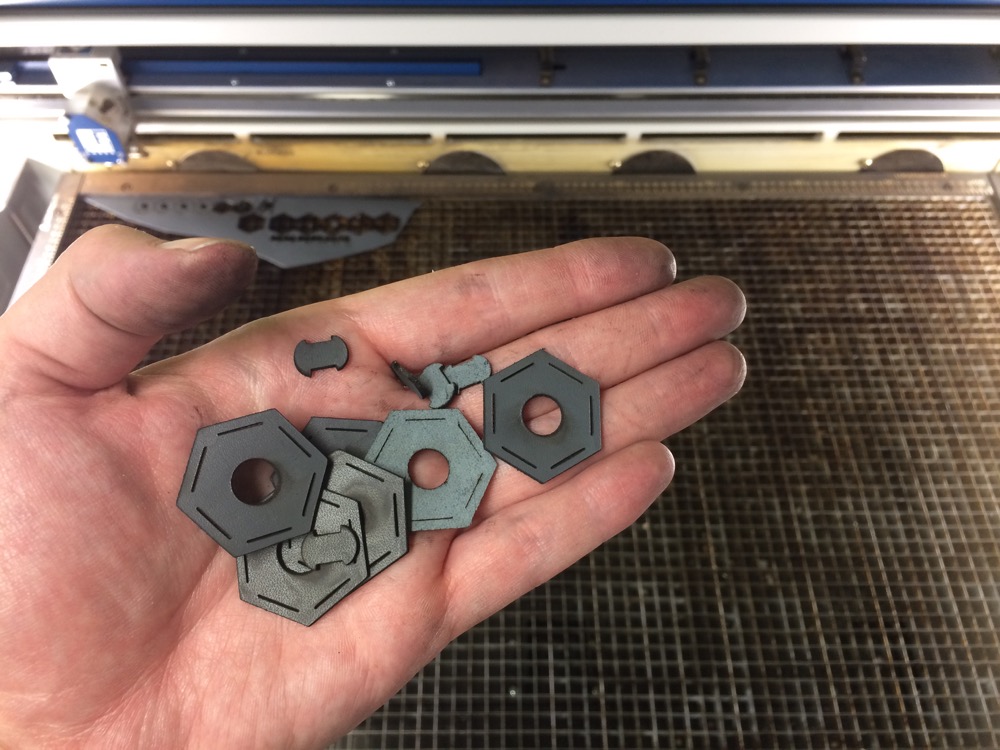 |
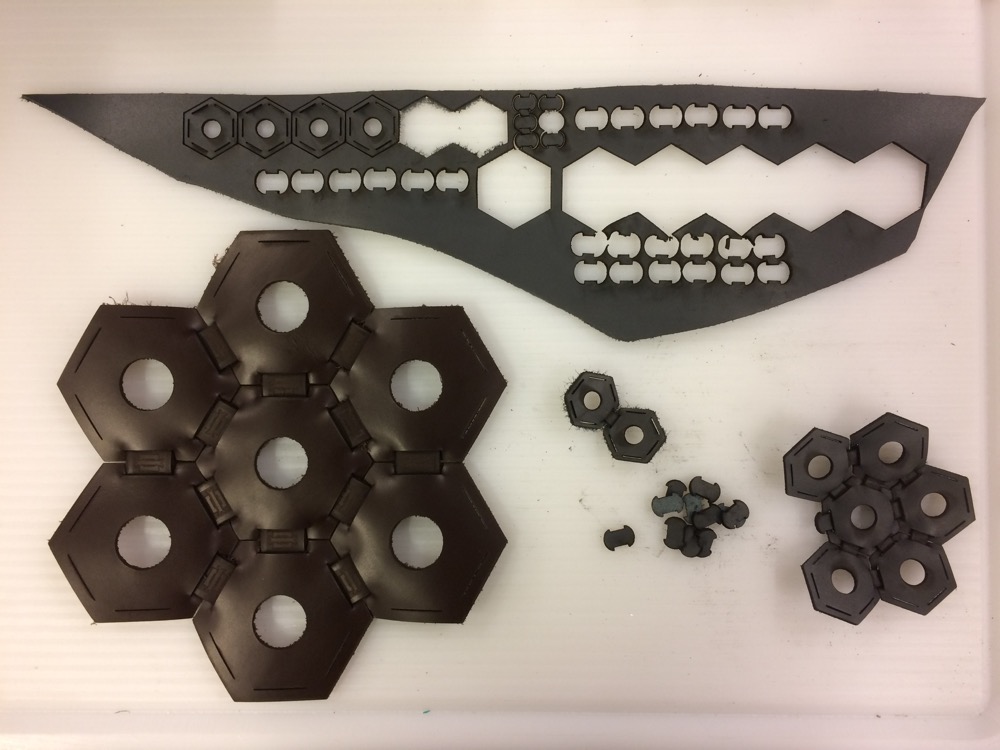 |
Folding a 2D pattern to obtain a 3D Pattern |
Folding a 2D pattern to obtain a 3D Pattern |
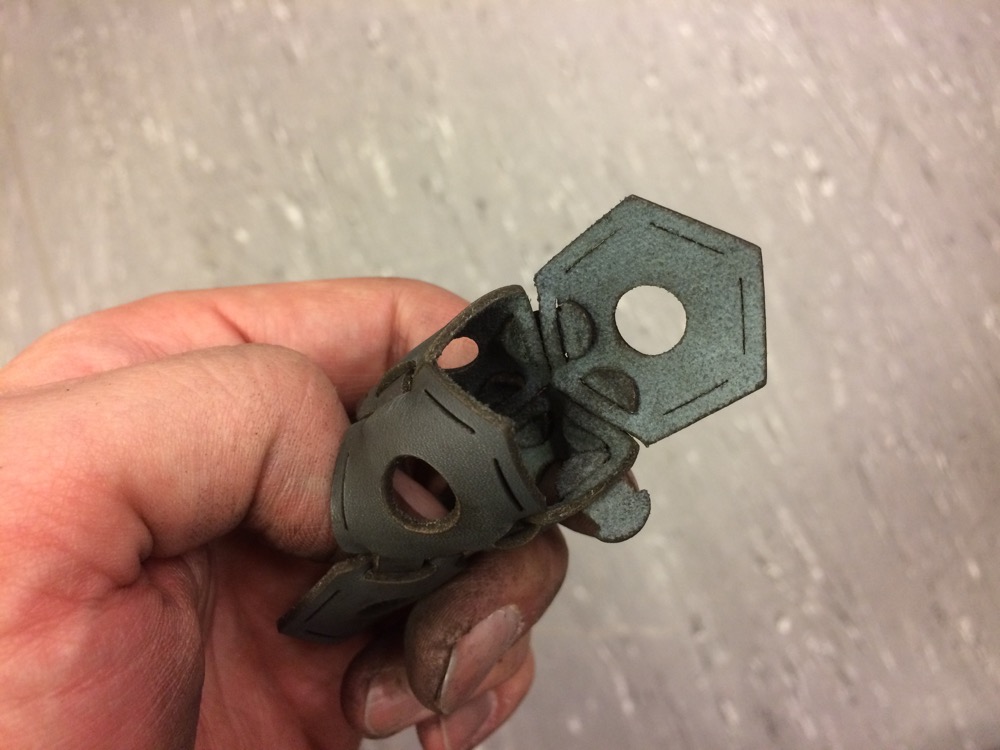 |
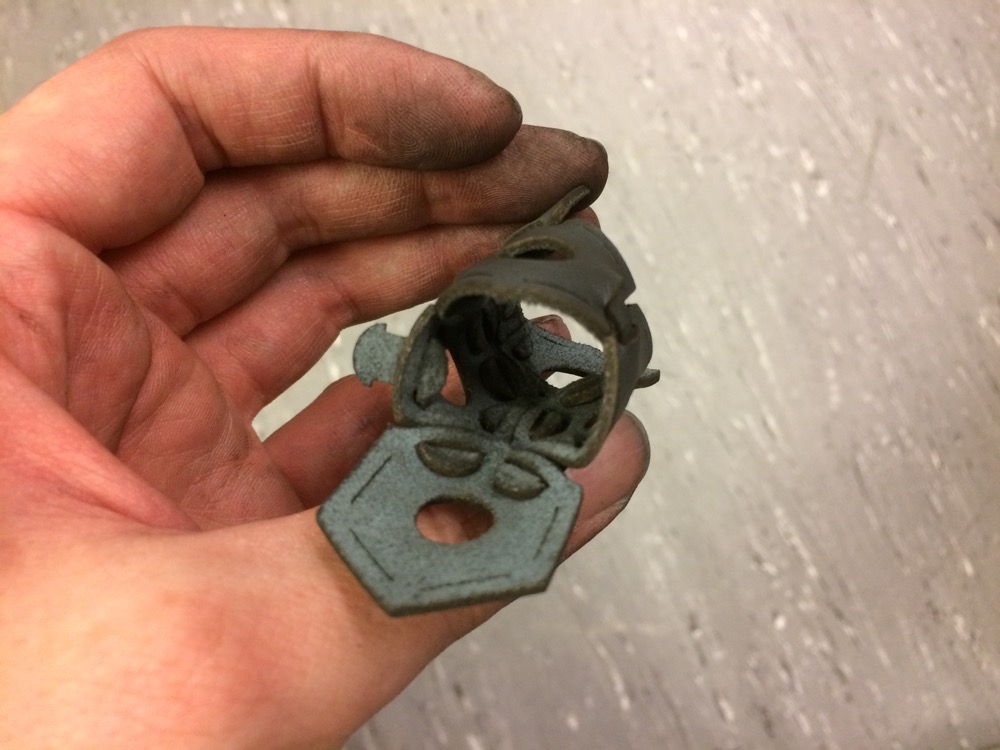 |
7 | Review of available wadding for Poufs at the closest store |
Ouatine (Polyester) |
P.E.T |
Corn Fiber |
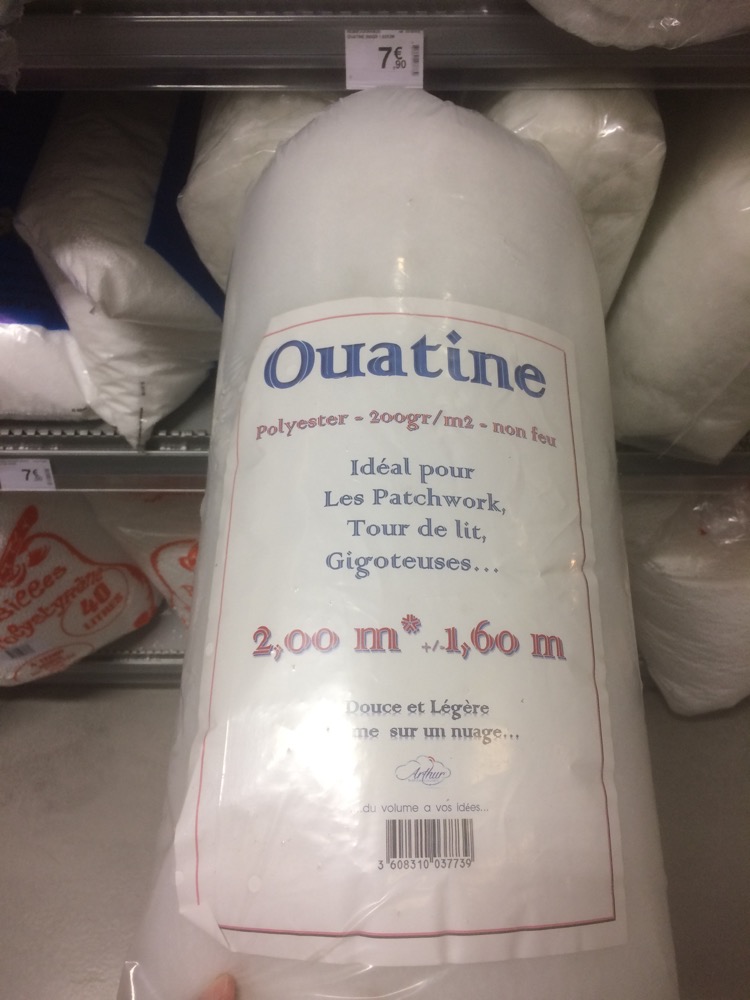 |
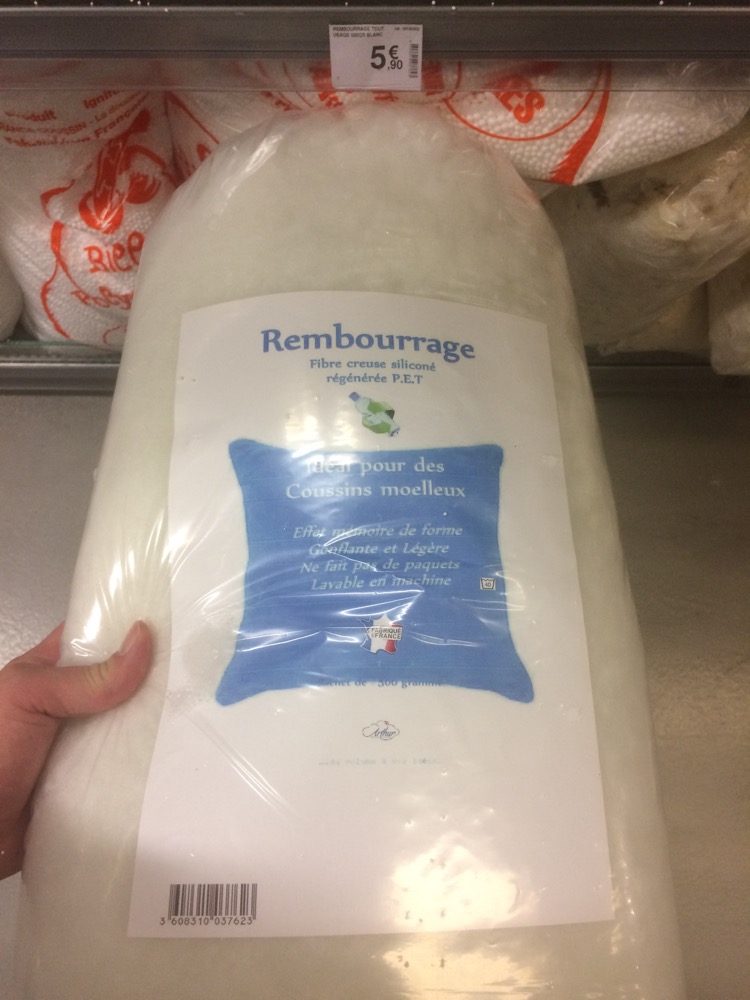 |
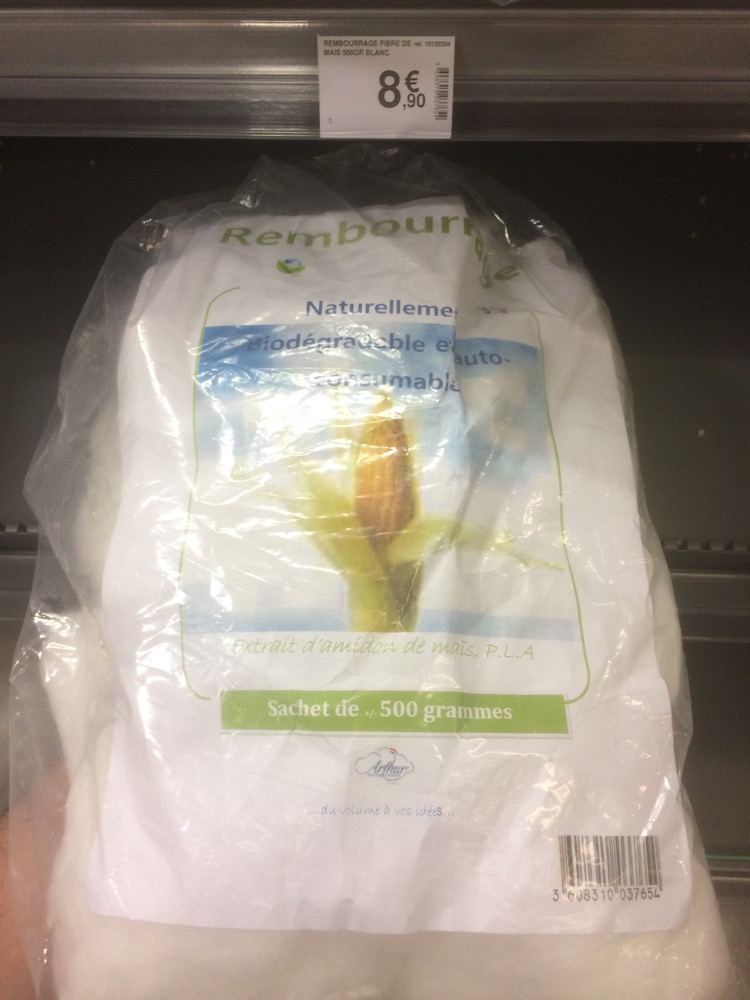 |
Duck Feathers (brrr) |
Polystyrene |
Ignite Polystyrene |
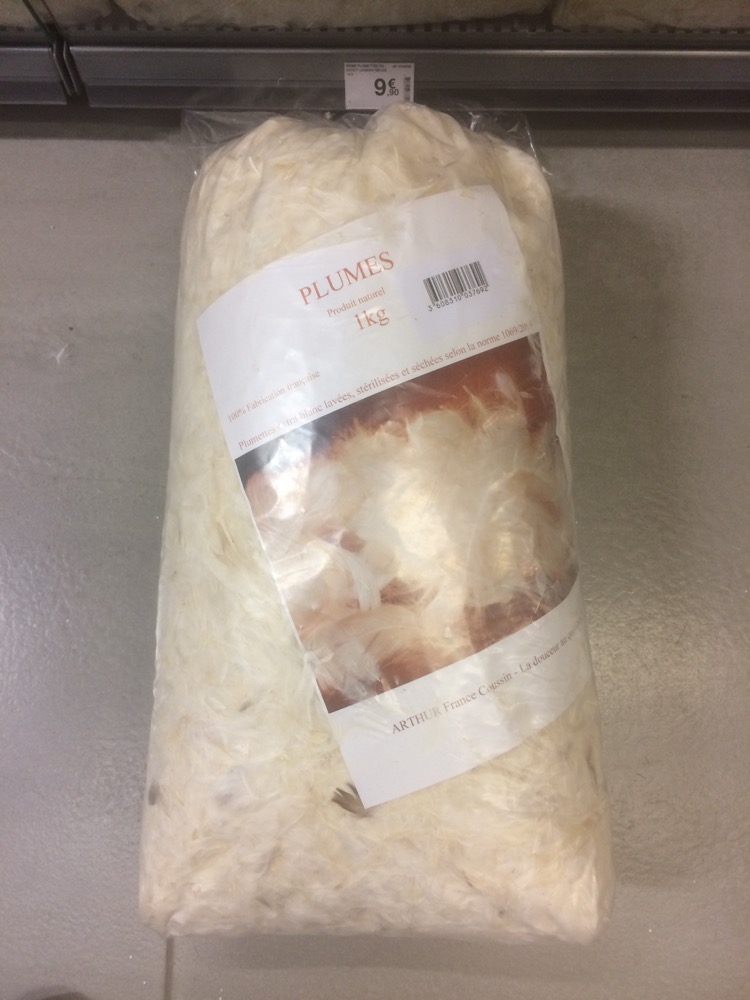 |
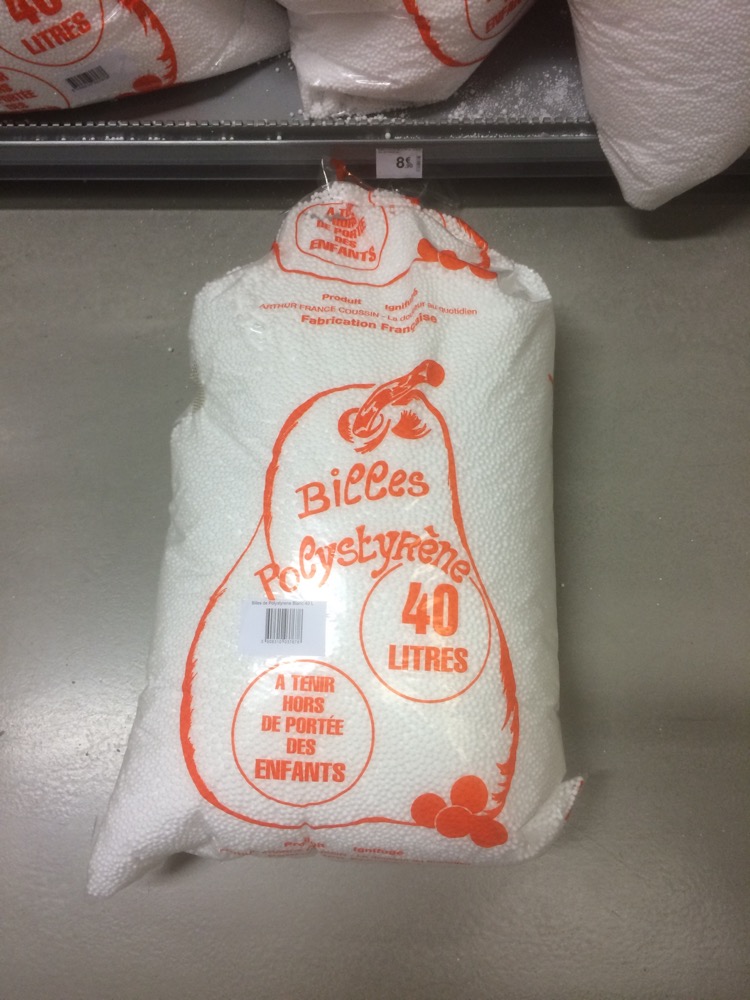 |
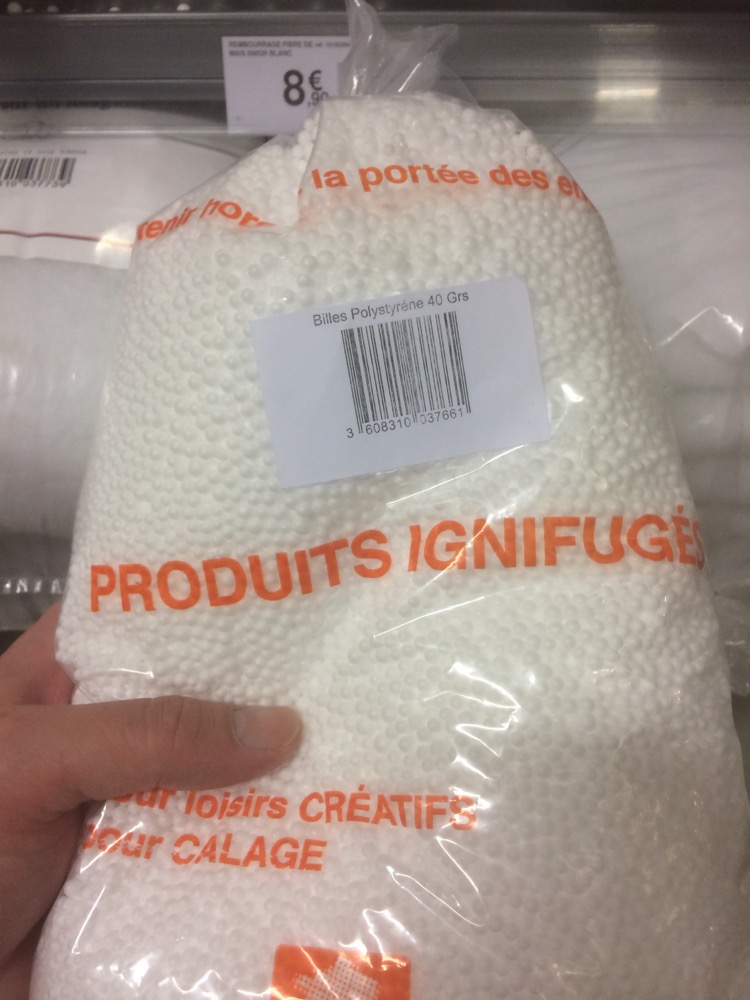 |
8 | Scaling-down the patterns and optimizing material: first step of a kit-development |
At first I felt like going big and make a pouf. Now I see my design differently, with modular variations in 3D. From the pics below I’ll laser-cut a batch of 2000 pieces to assemble. Going from 2D parts to make 3D objects.
Pattern Kit |
Pattern Kit |
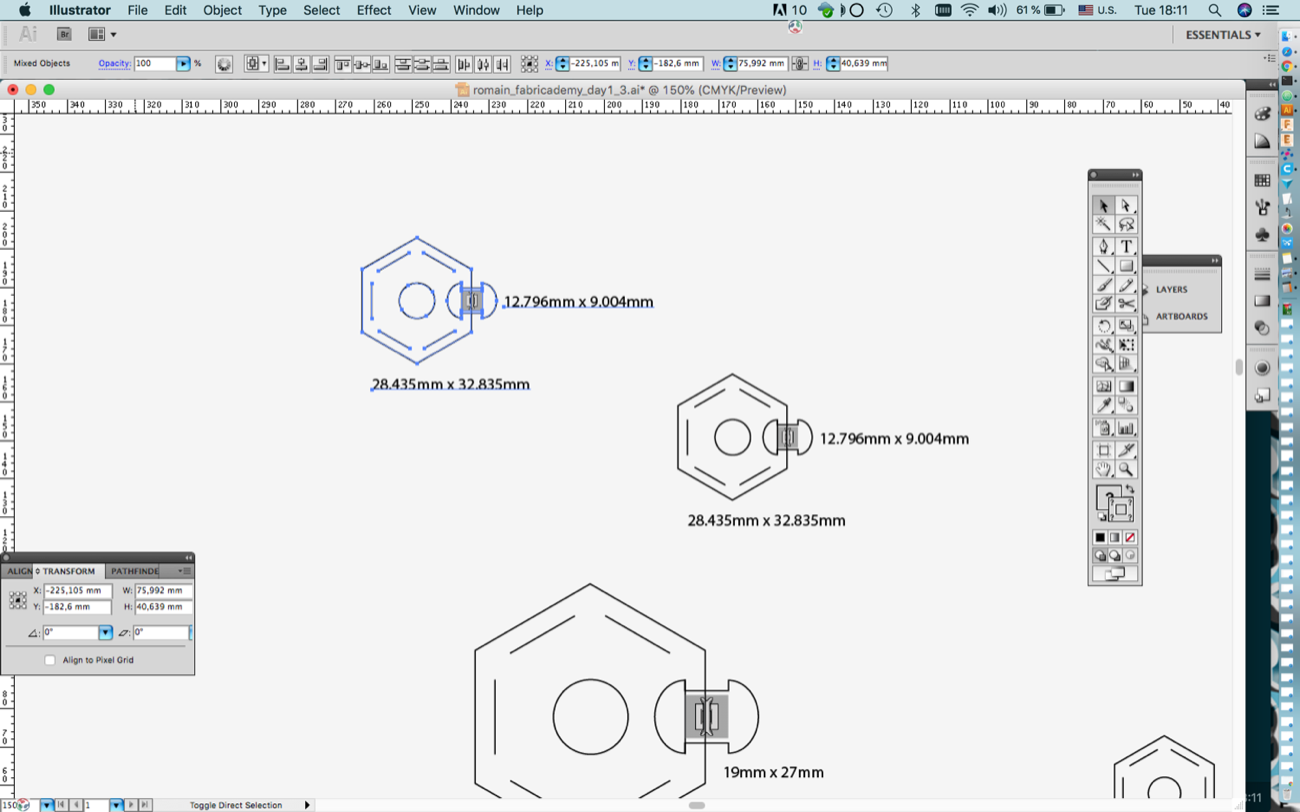 |
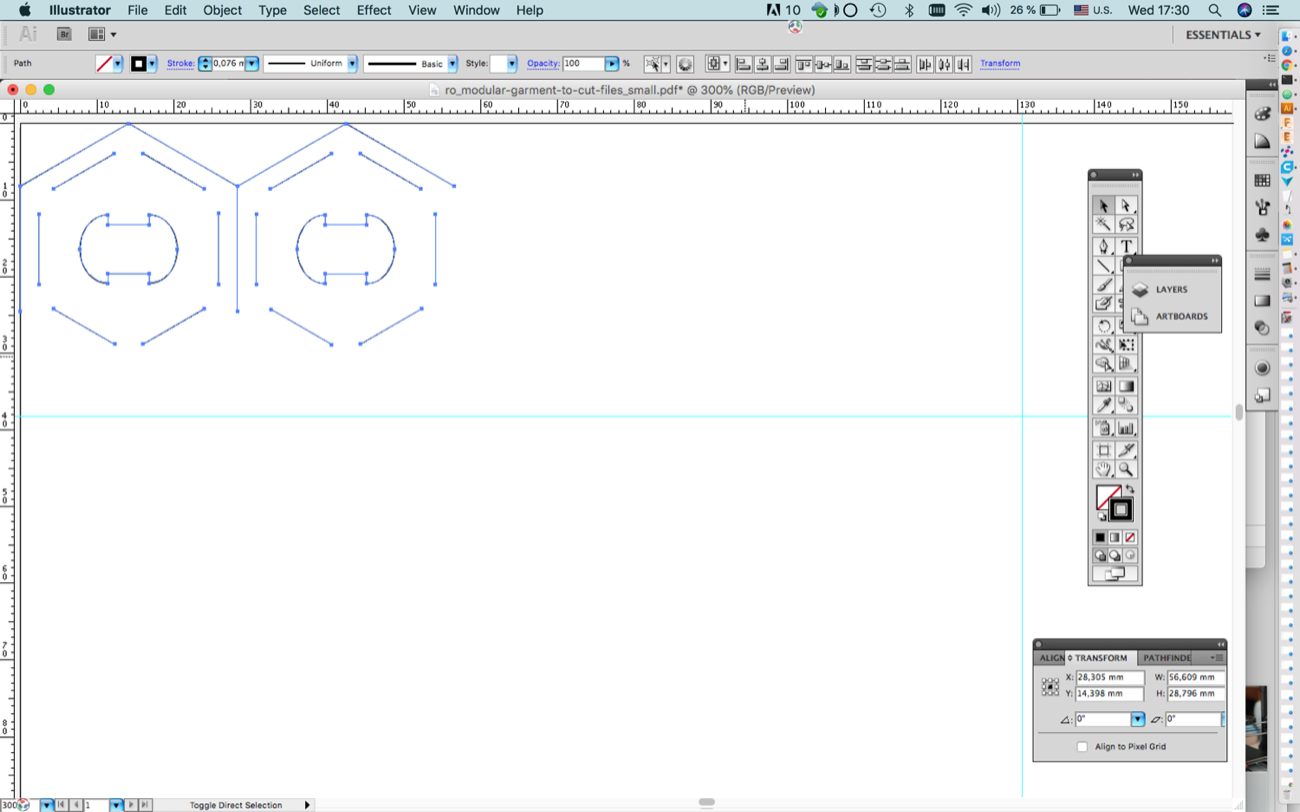 |
Pattern Kit |
Pattern Kit |
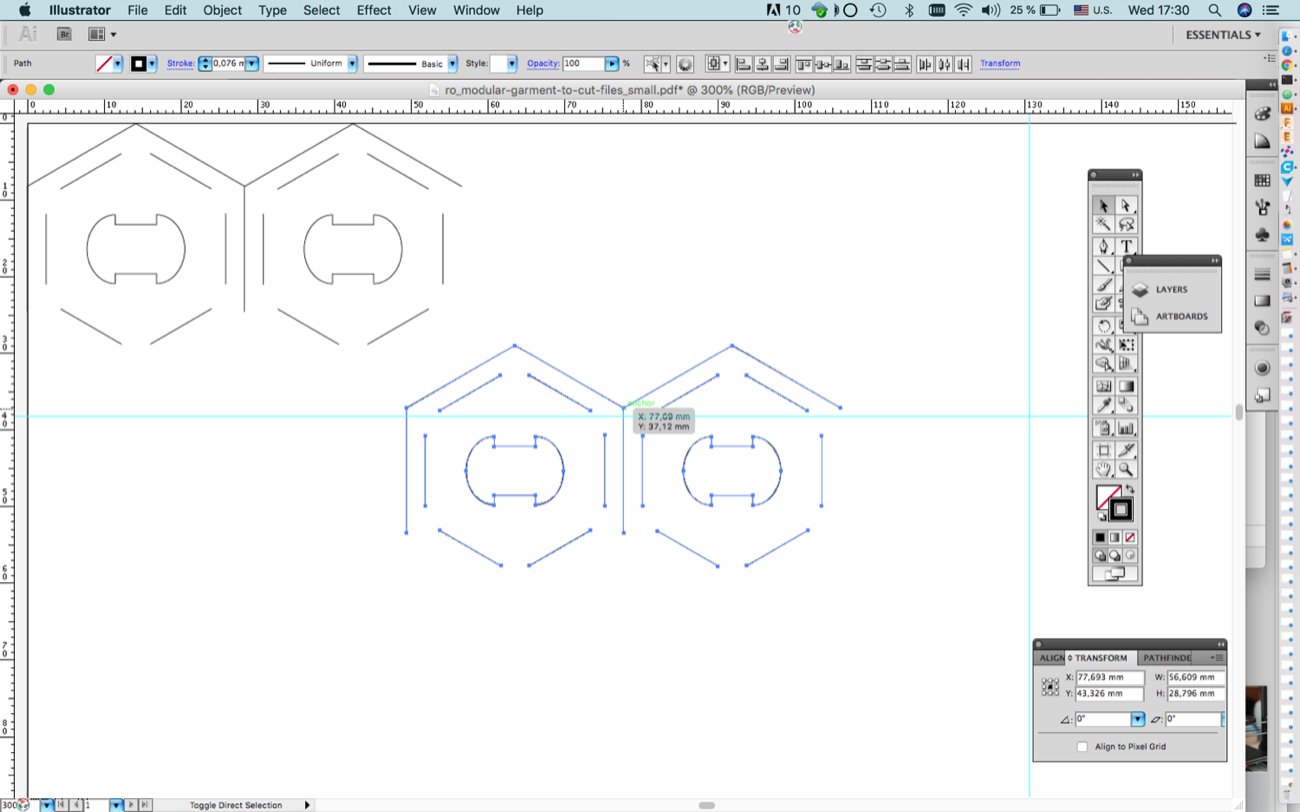 |
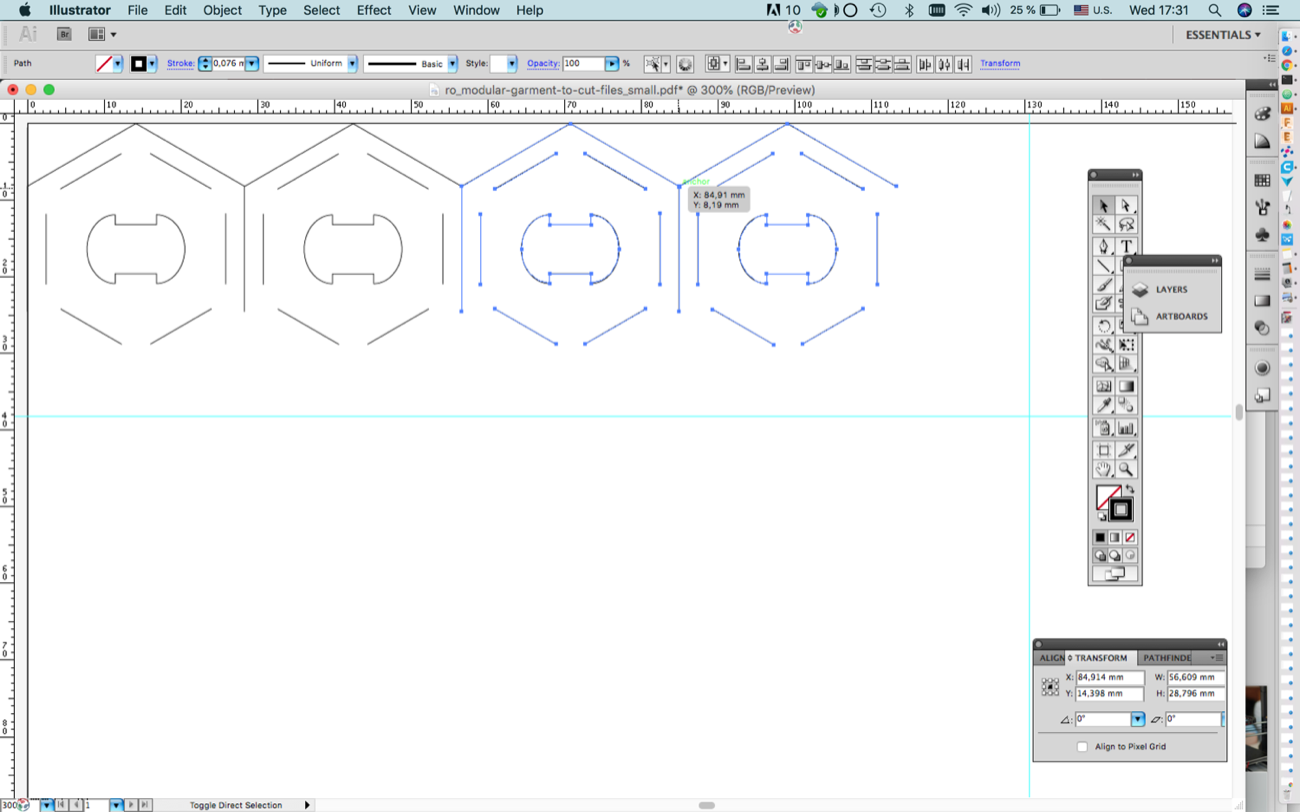 |
Pattern Kit |
Pattern Kit |
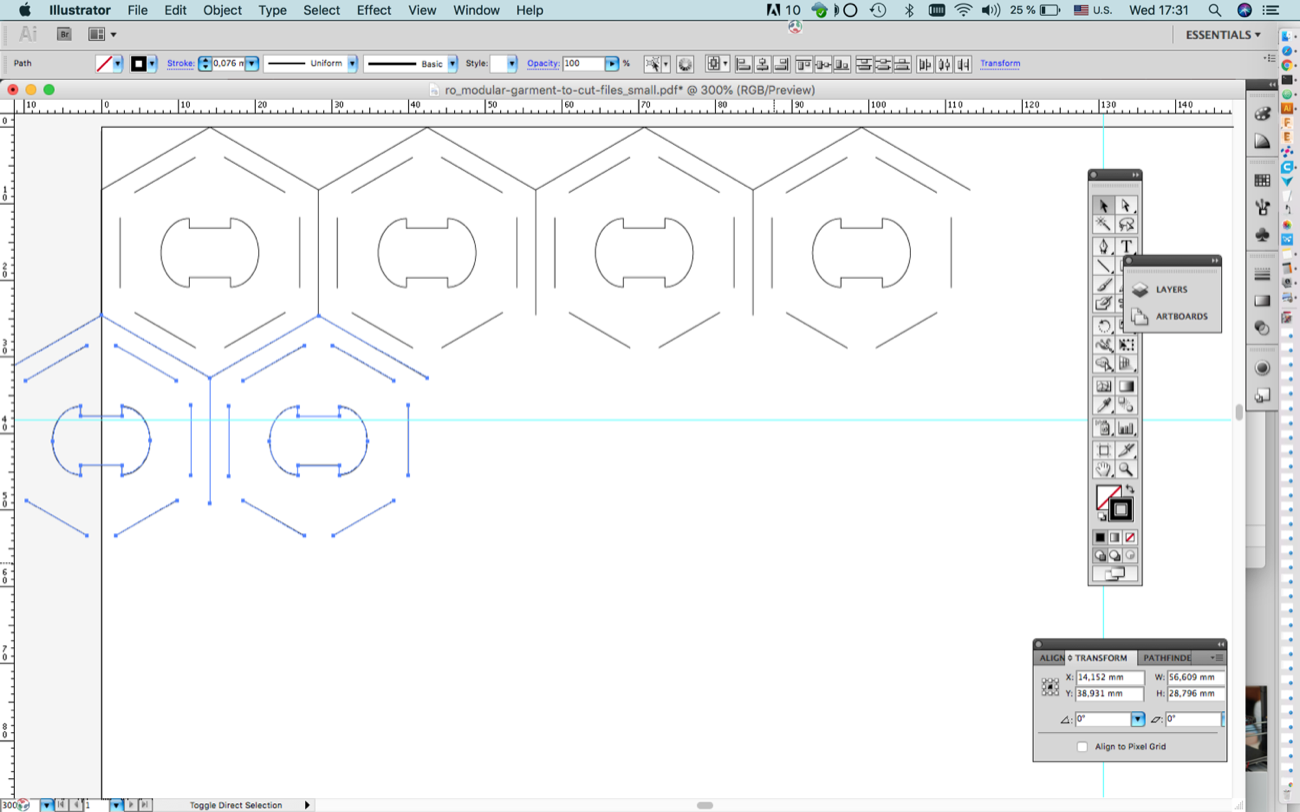 |
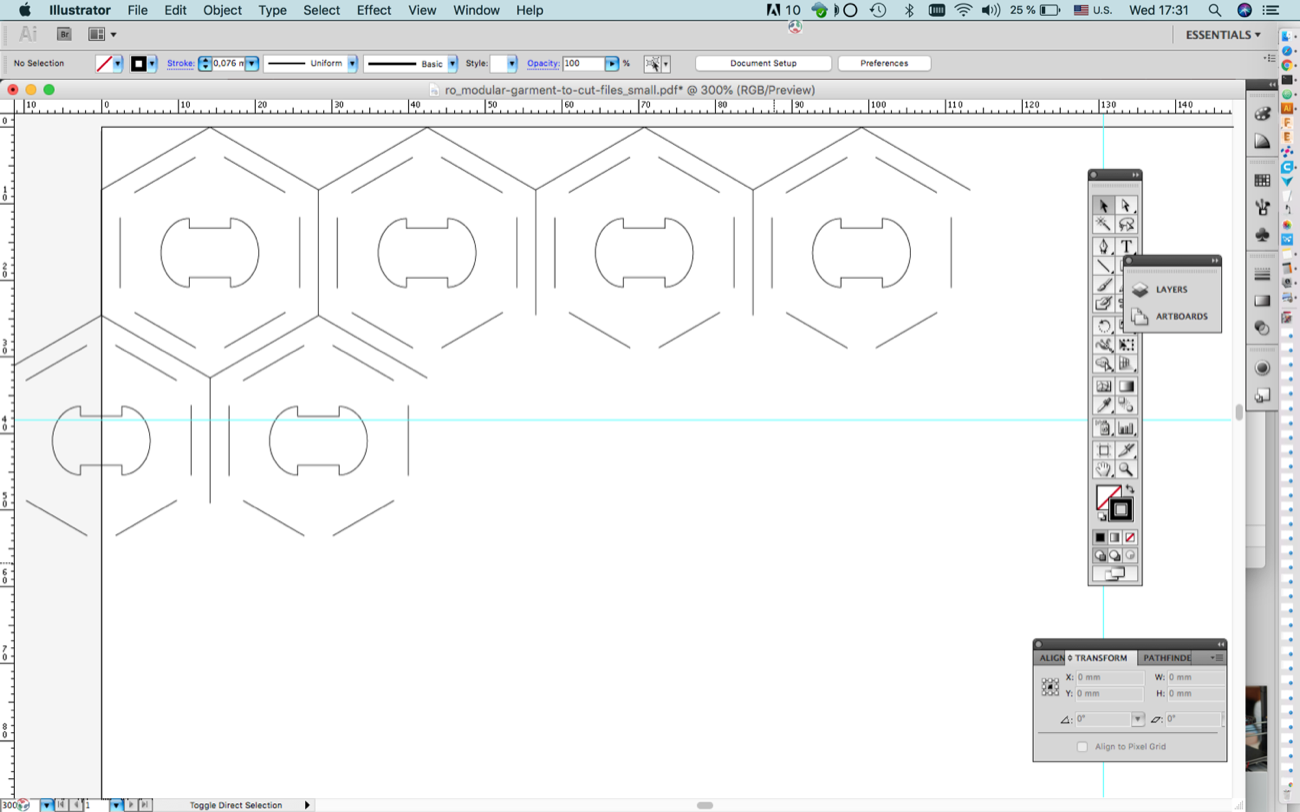 |
Pattern Kit |
Pattern Kit |
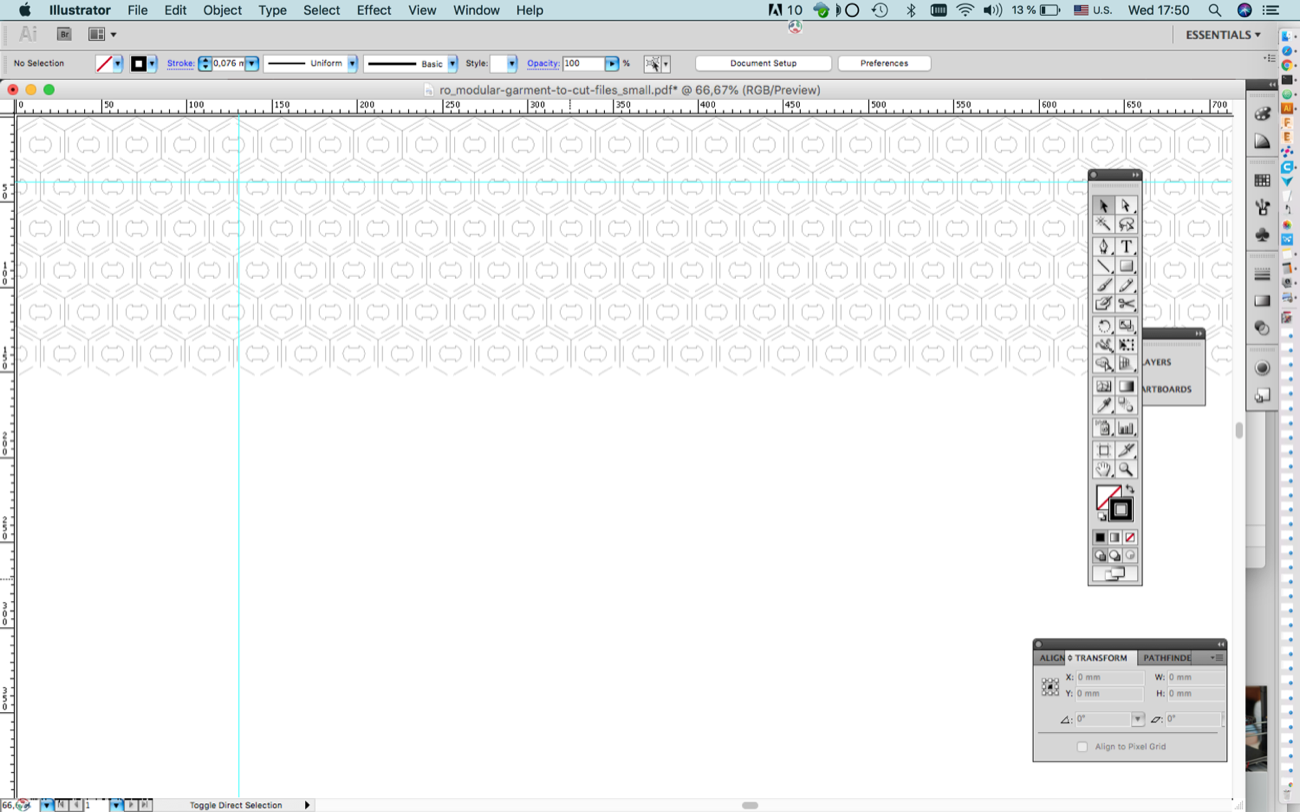 |
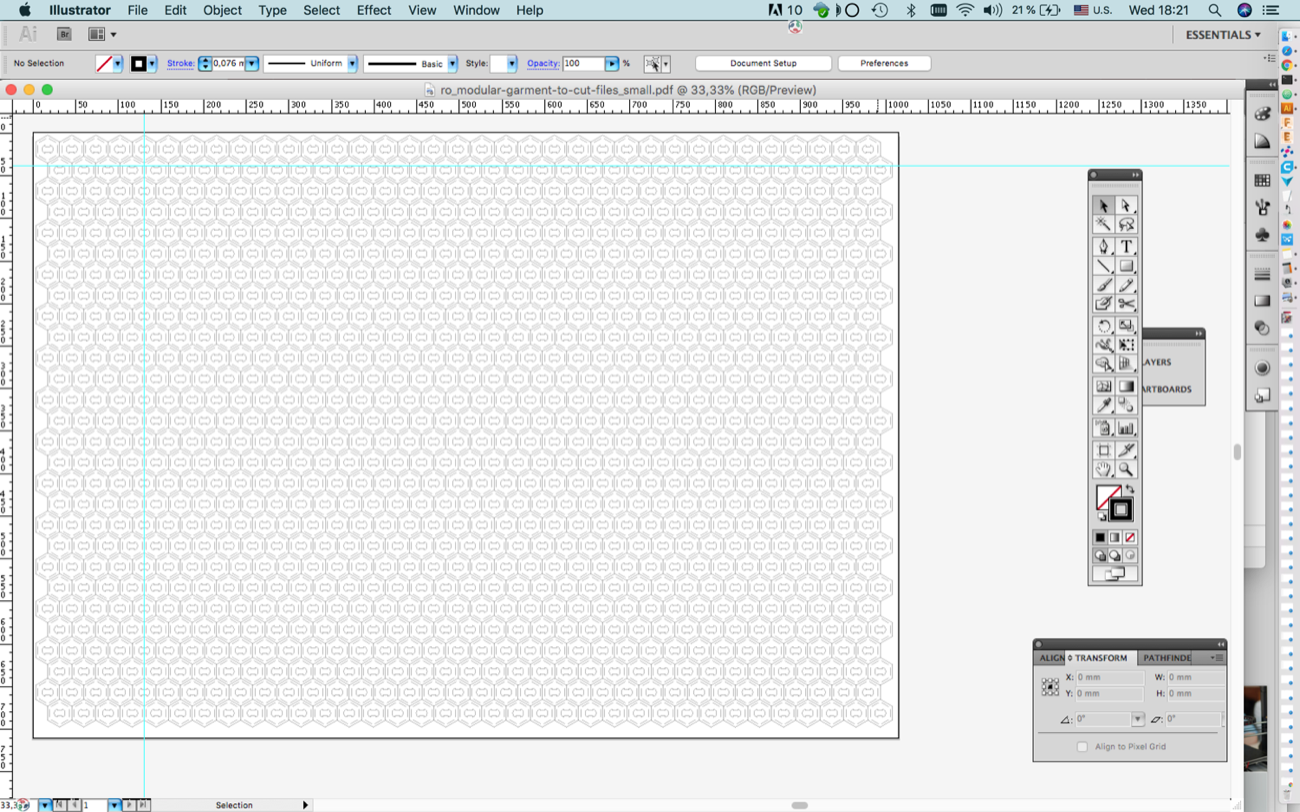 |
Pattern Kit |
Pattern Kit |
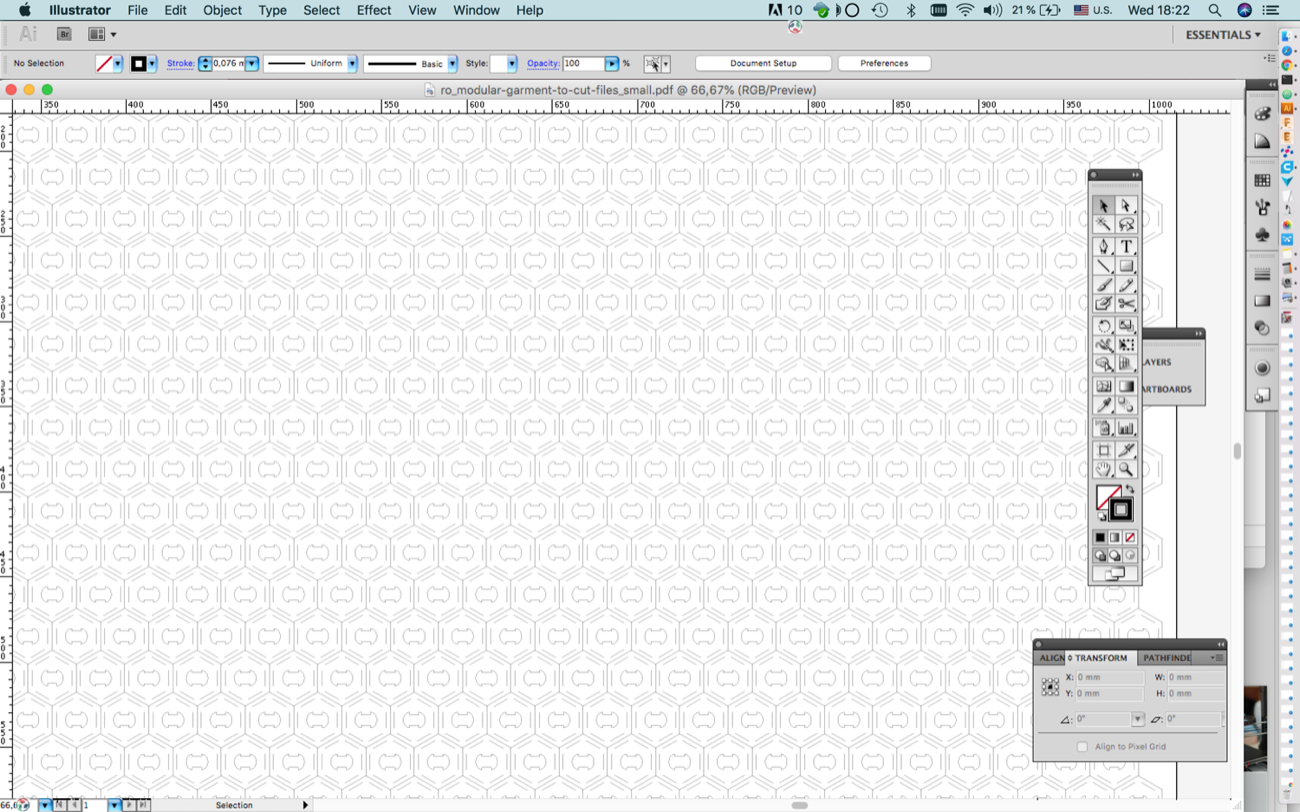 |
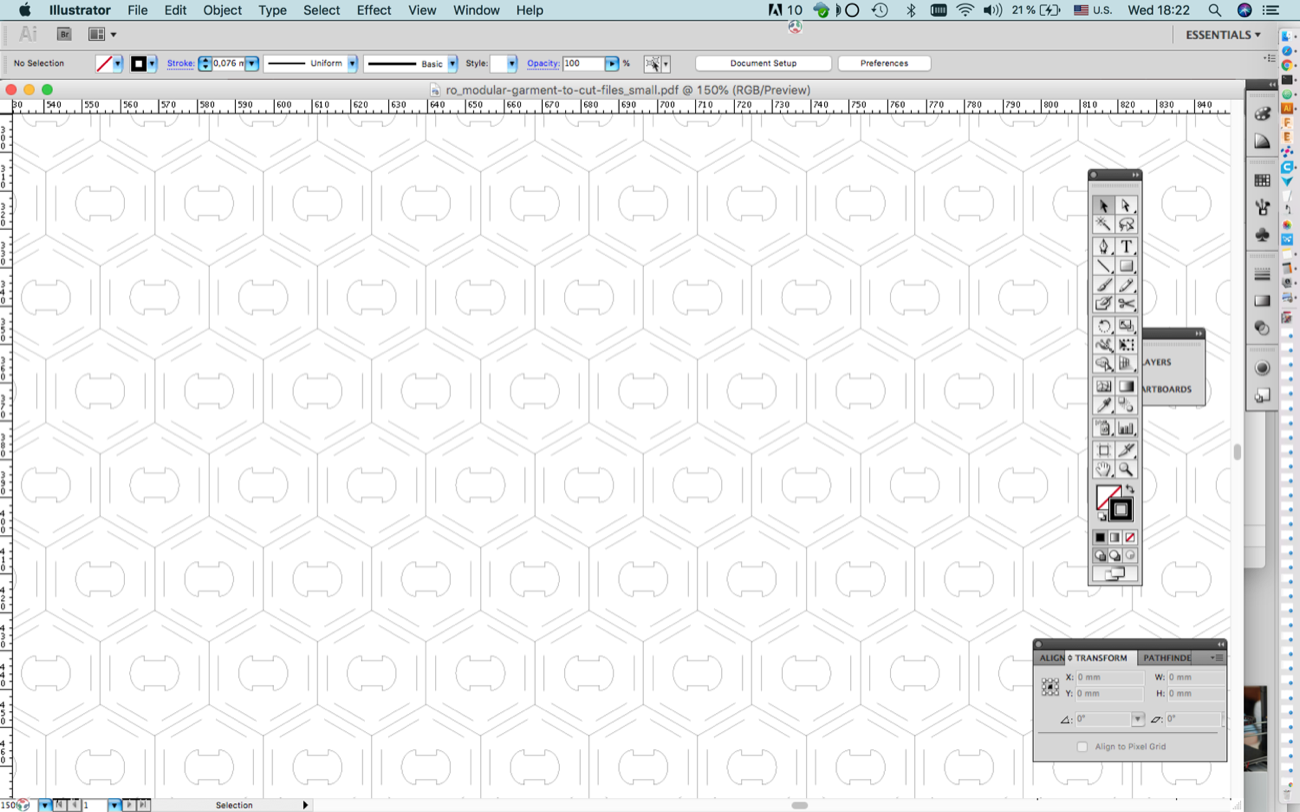 |
Pattern Kit |
Pattern Kit |
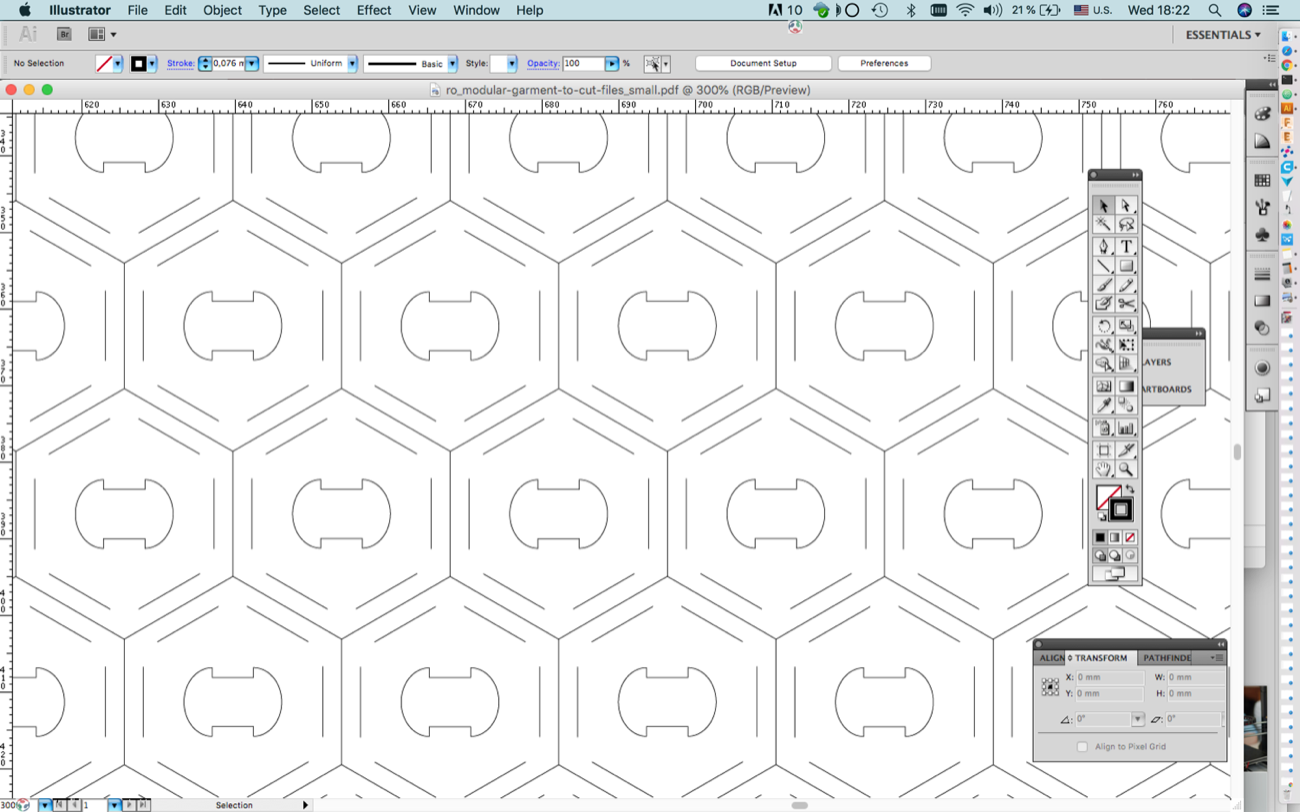 |
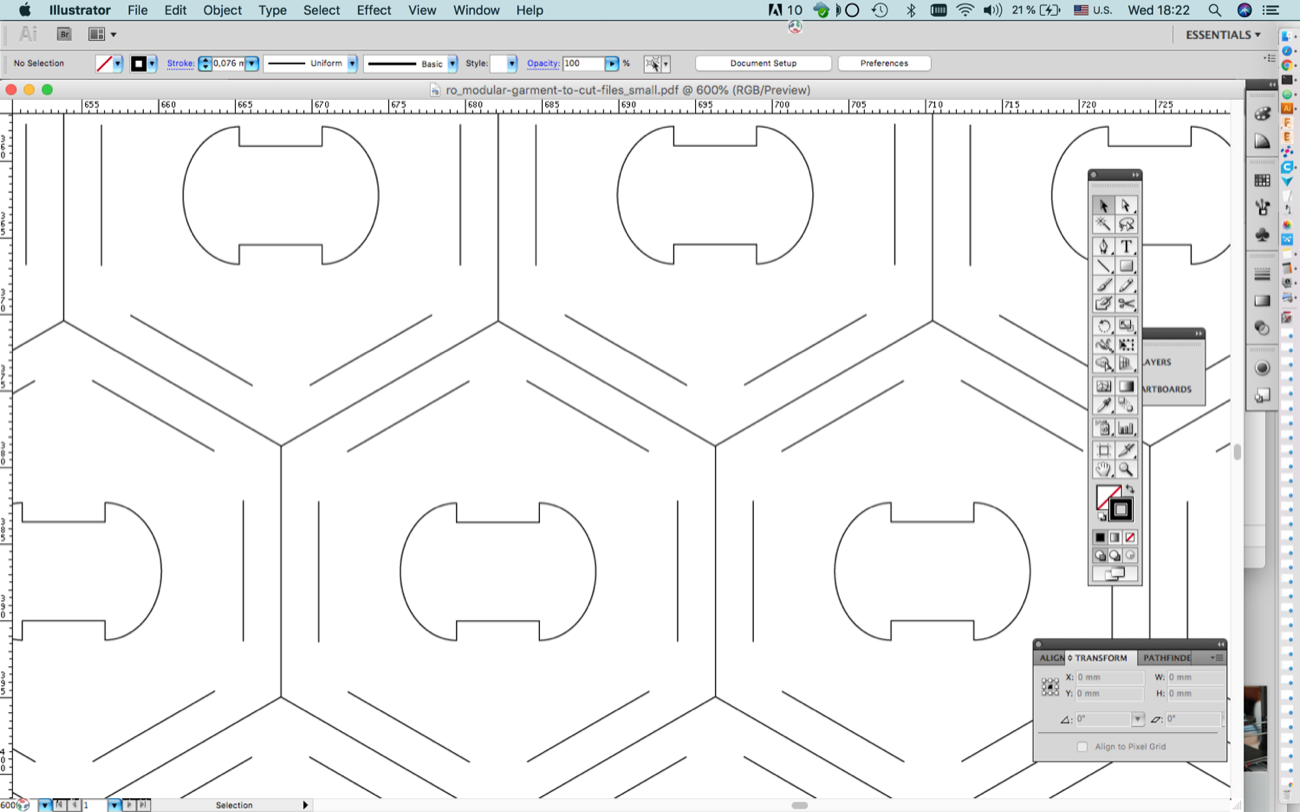 |
9 | Optimizing the Laser-cutting process for leather |
New laser-cutting tests |
New laser-cutting tests |
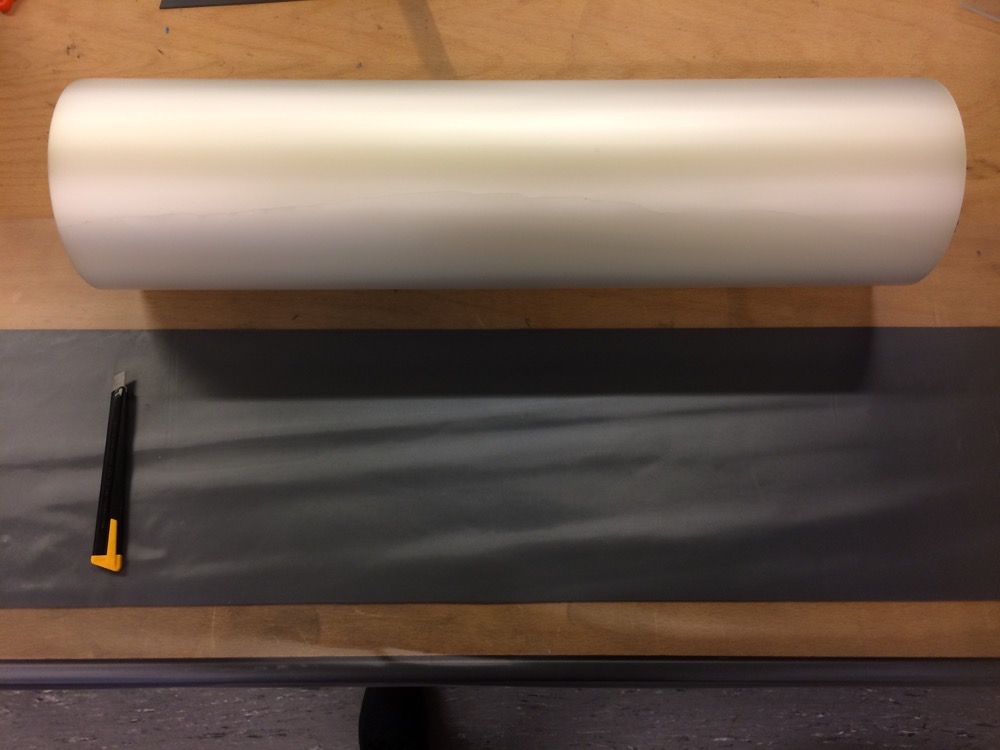 |
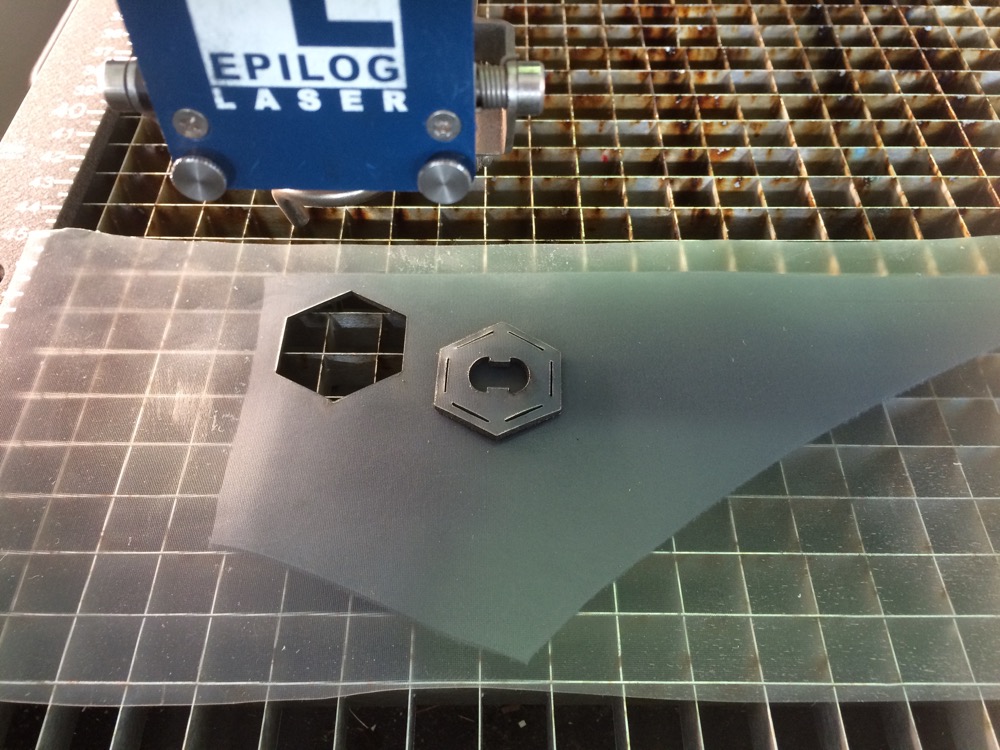 |
New laser-cutting tests |
New laser-cutting tests |
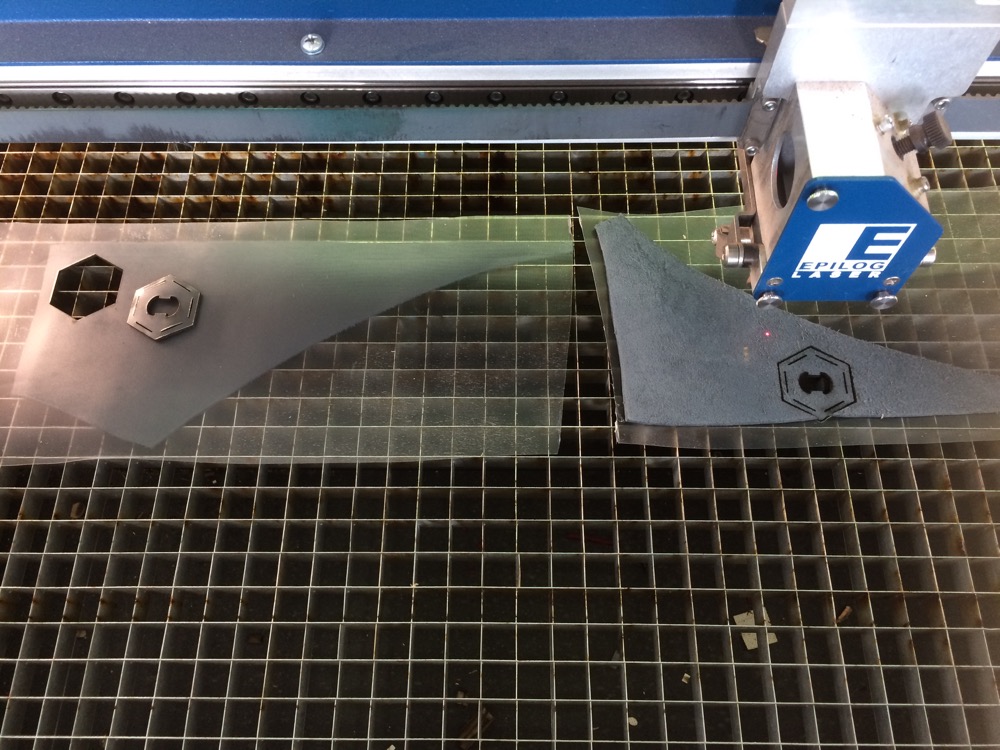 |
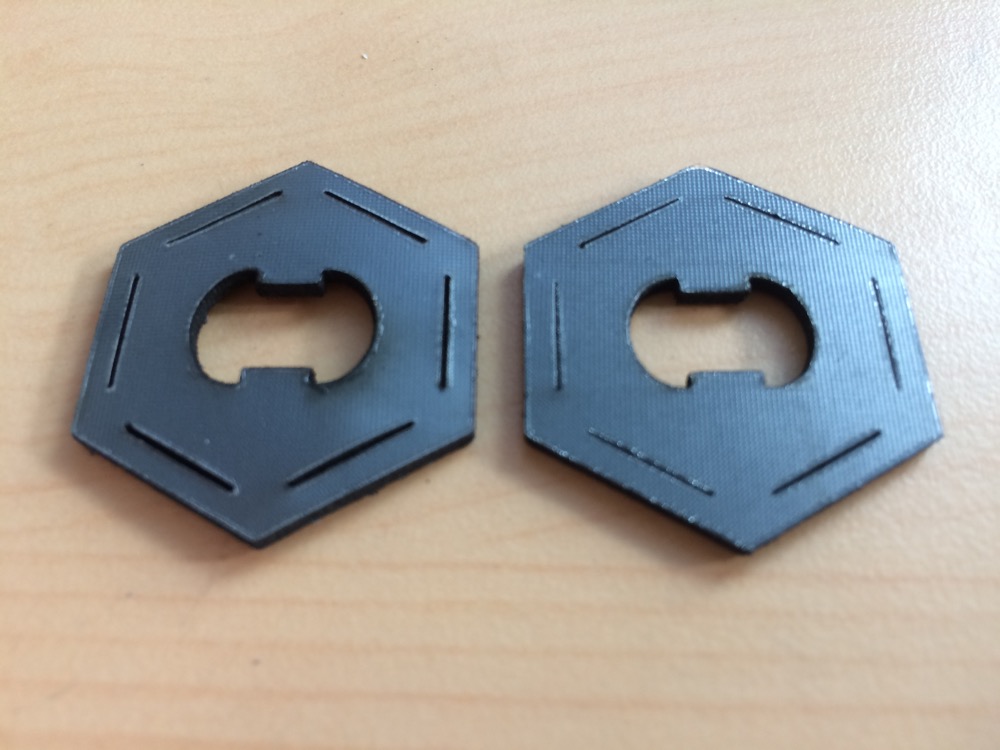 |
New laser-cutting tests |
New laser-cutting tests |
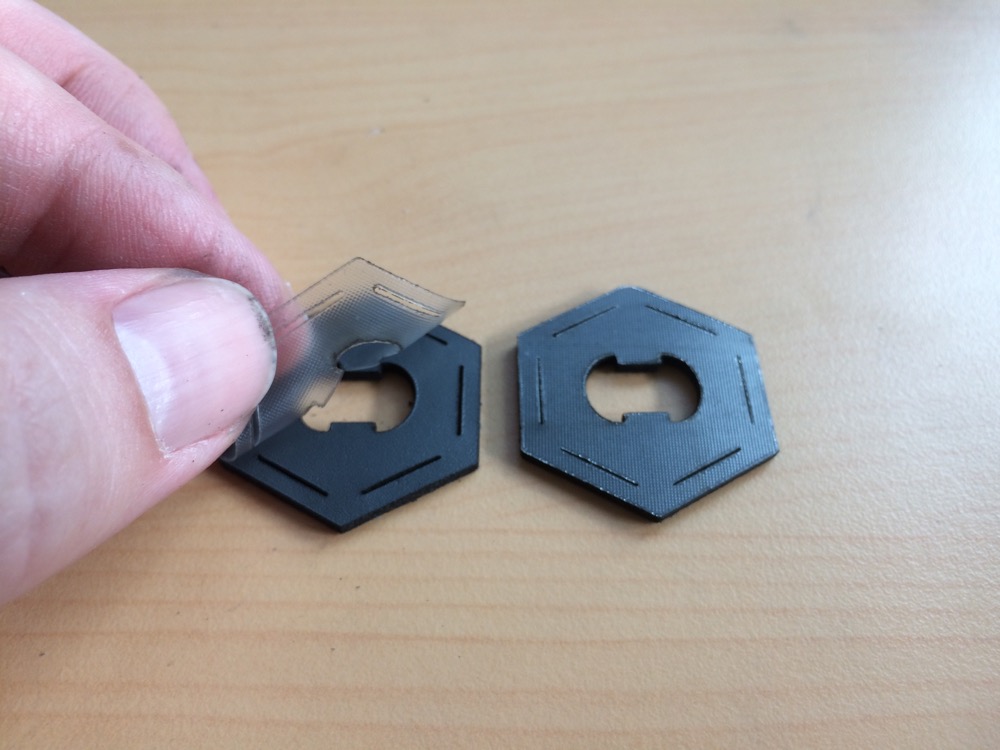 |
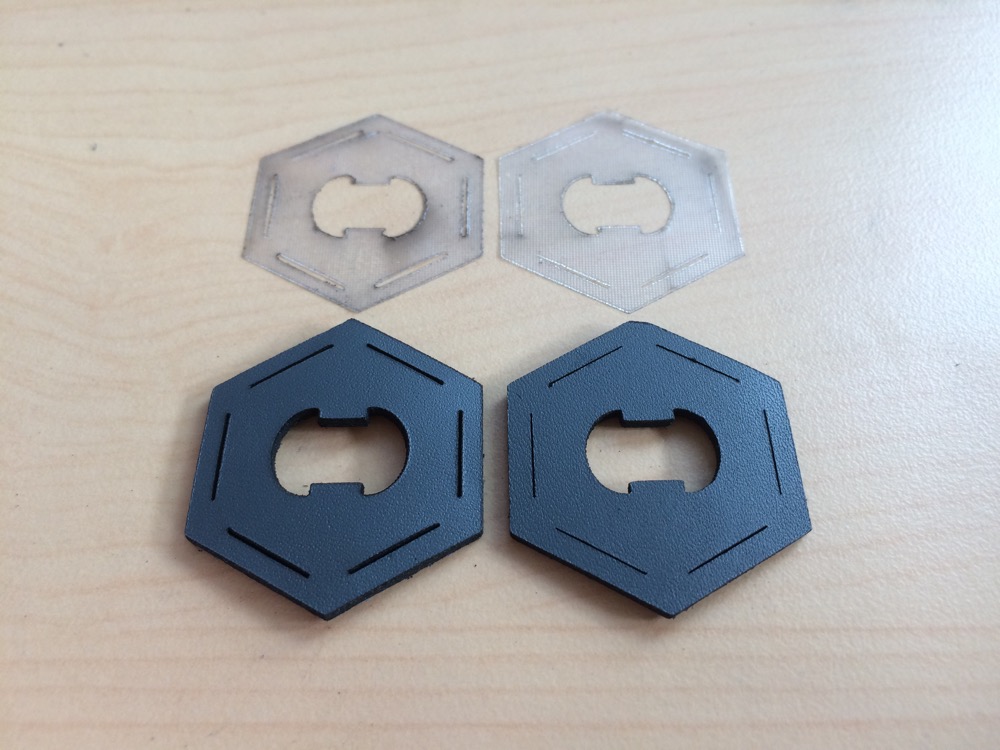 |
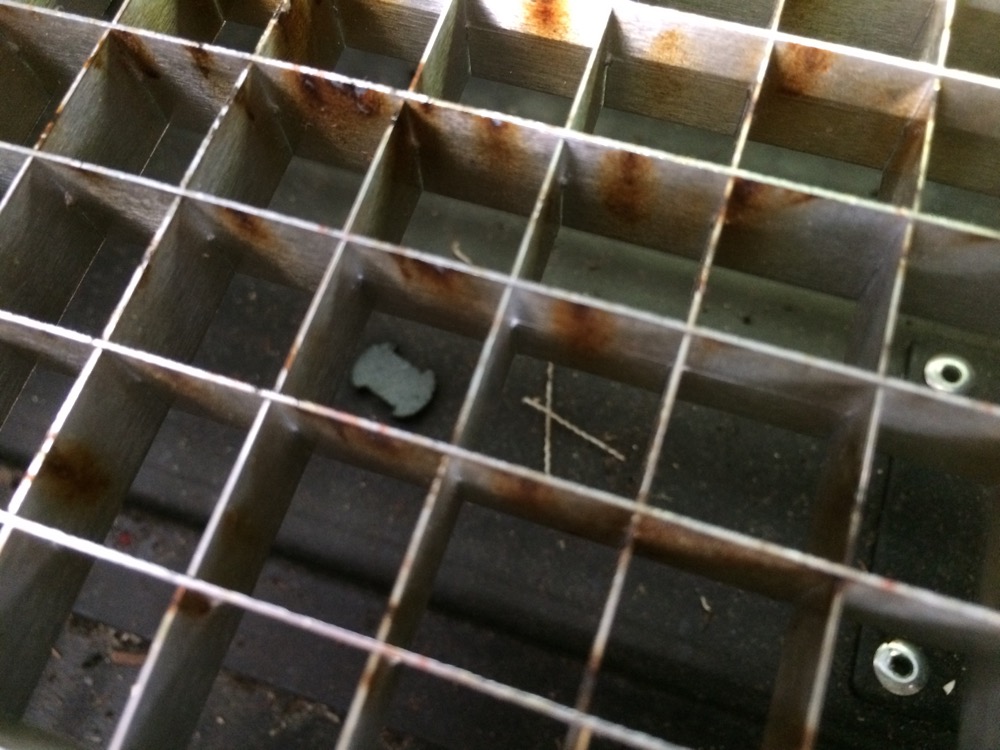
10 | First (small) batch of leather modules |
New laser-cutting tests |
New laser-cutting tests |
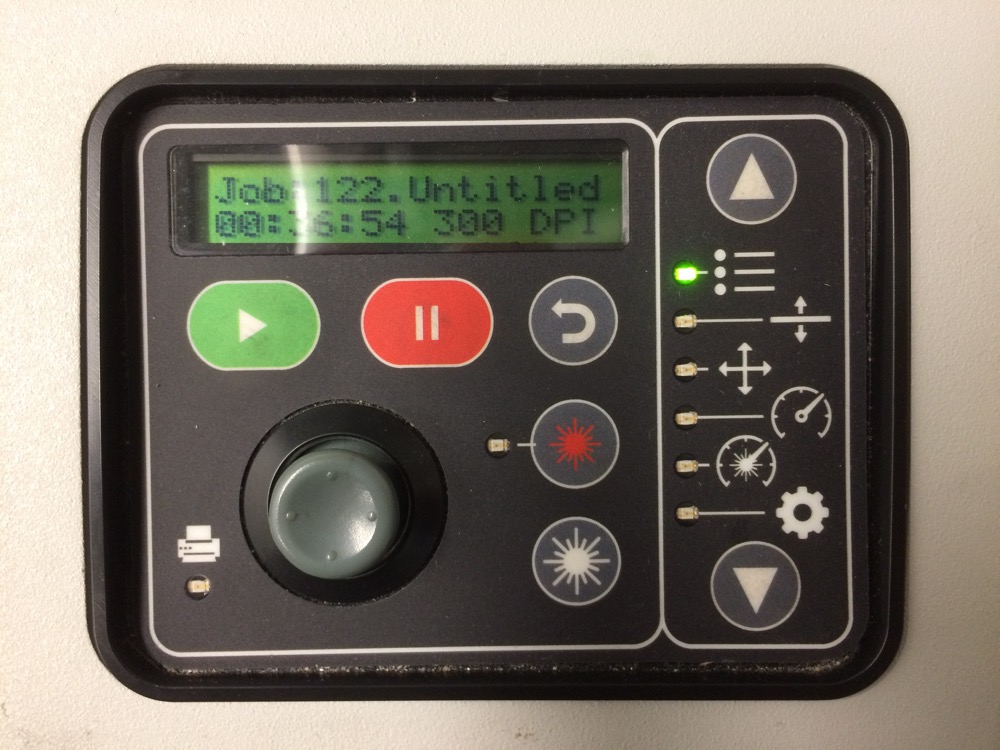 |
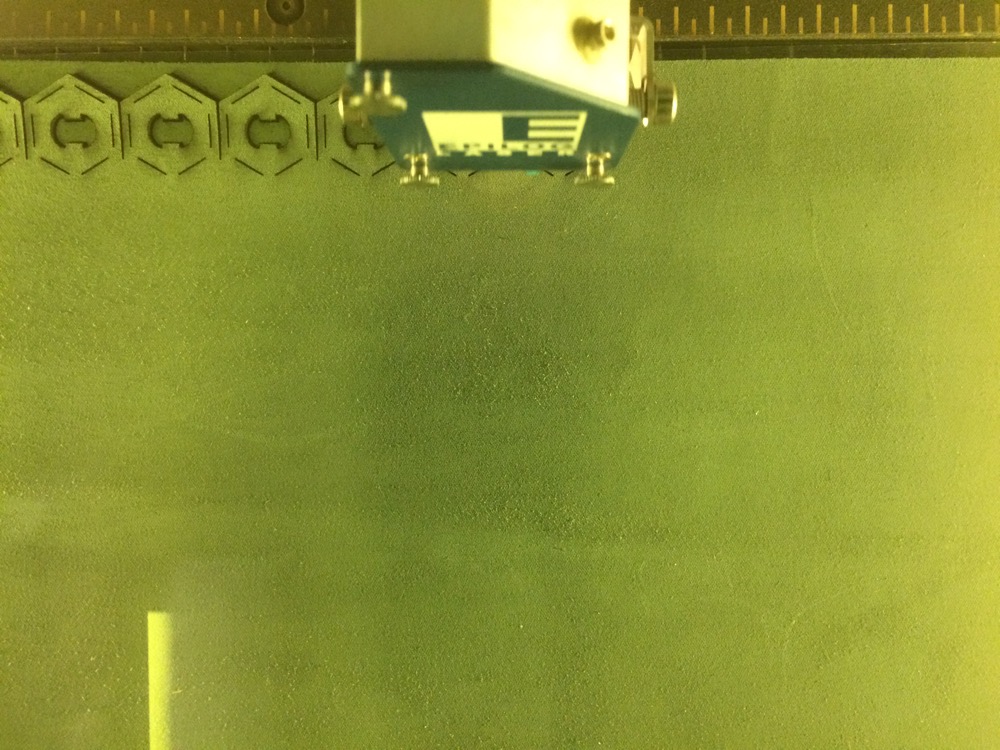 |
New laser-cutting tests |
New laser-cutting tests |
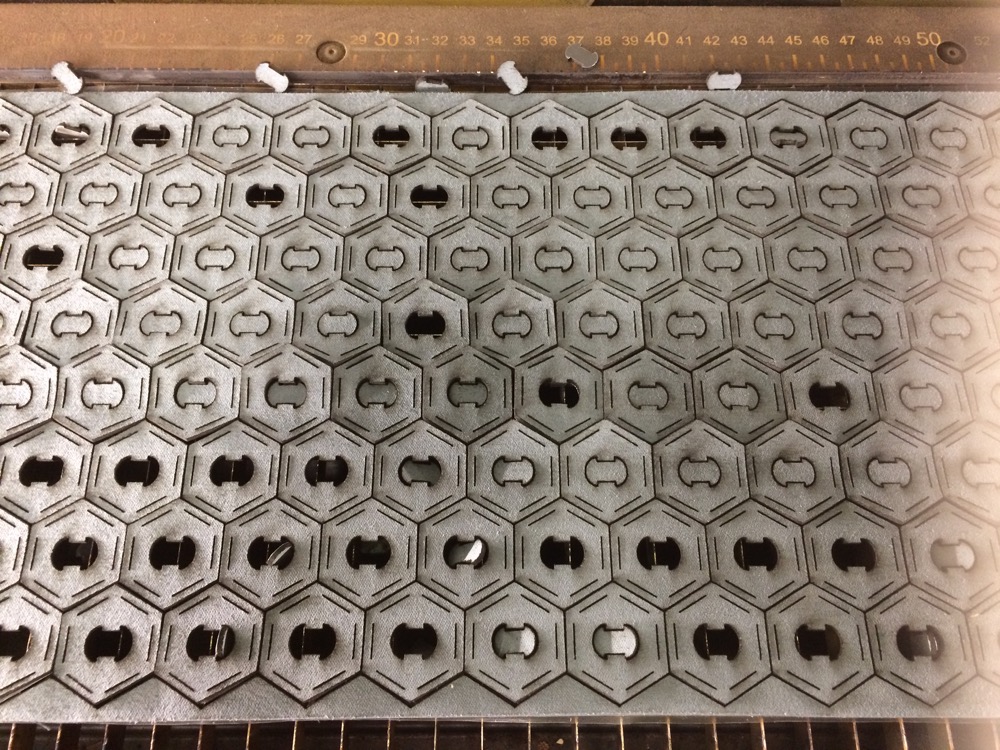 |
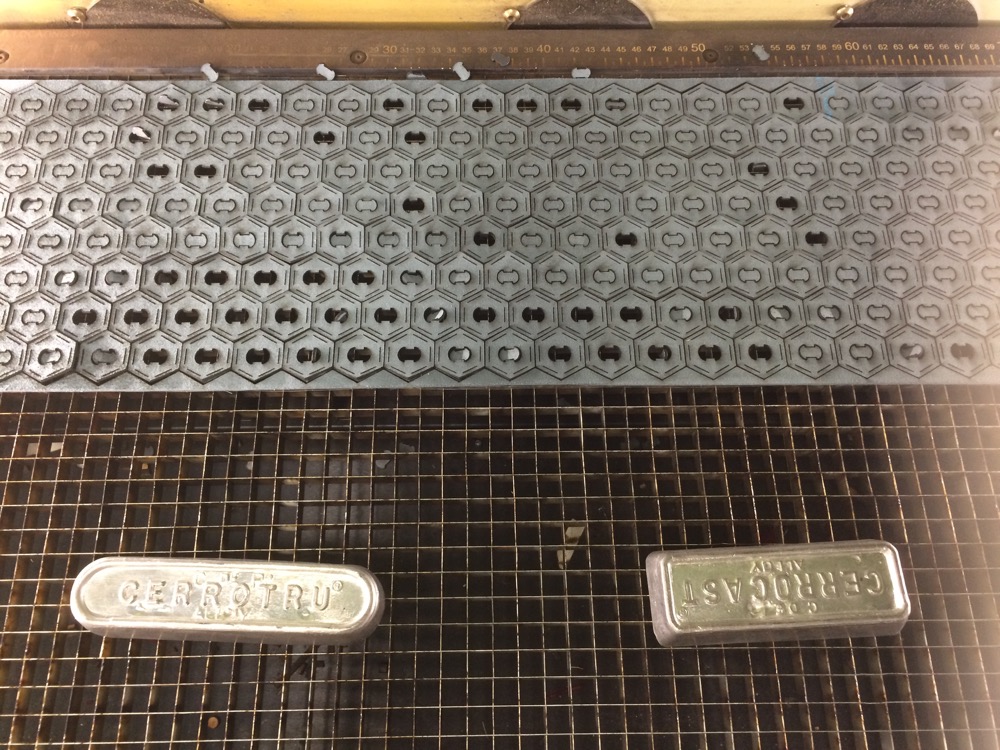 |
New laser-cutting tests |
New laser-cutting tests |
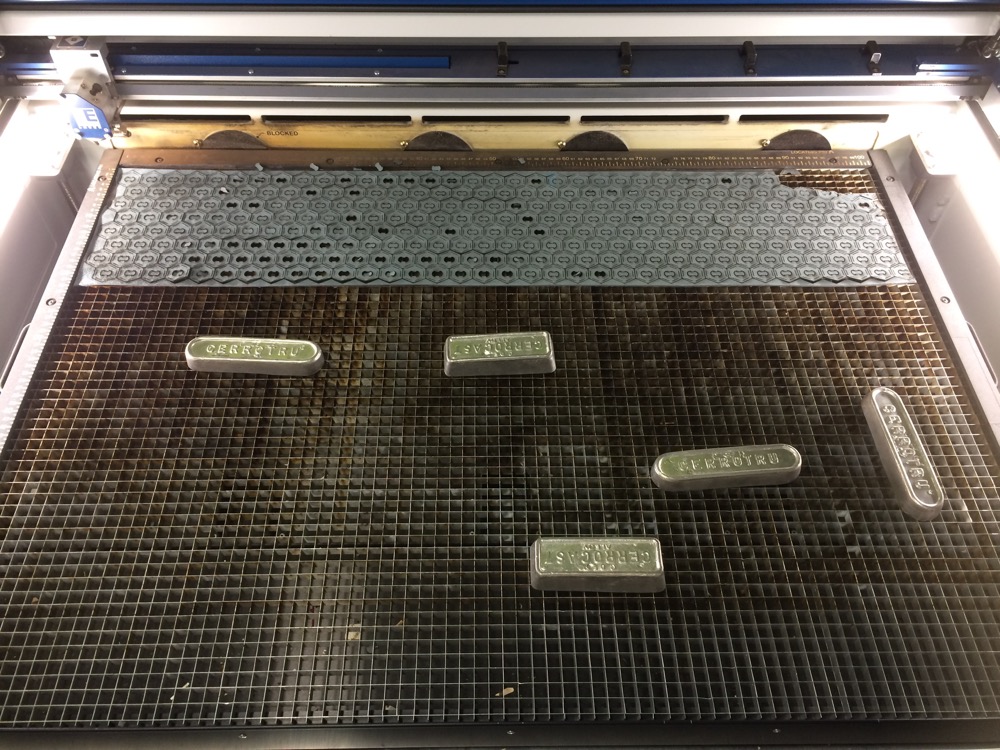 |
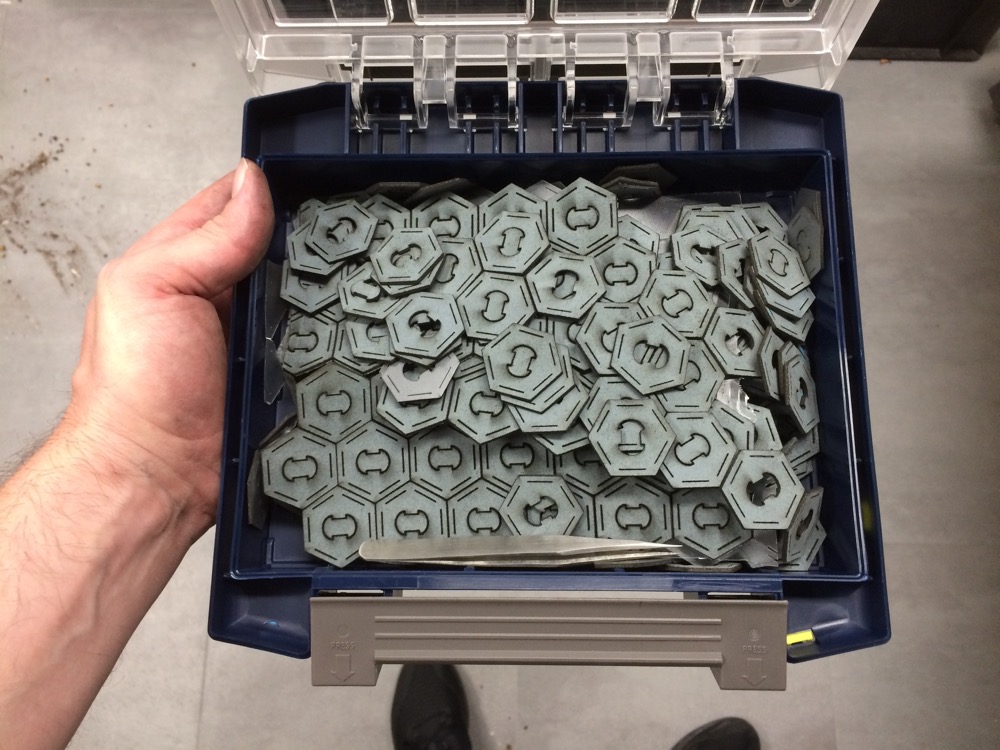 |
11 | Post production process of leather modules |
First batch |
First batch |
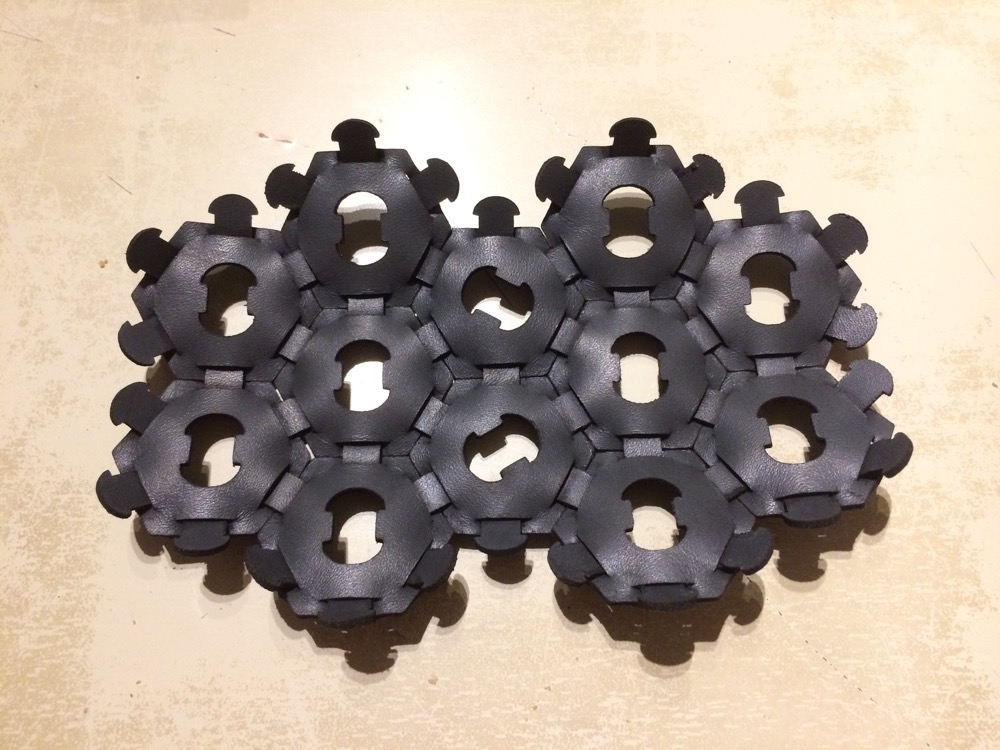 |
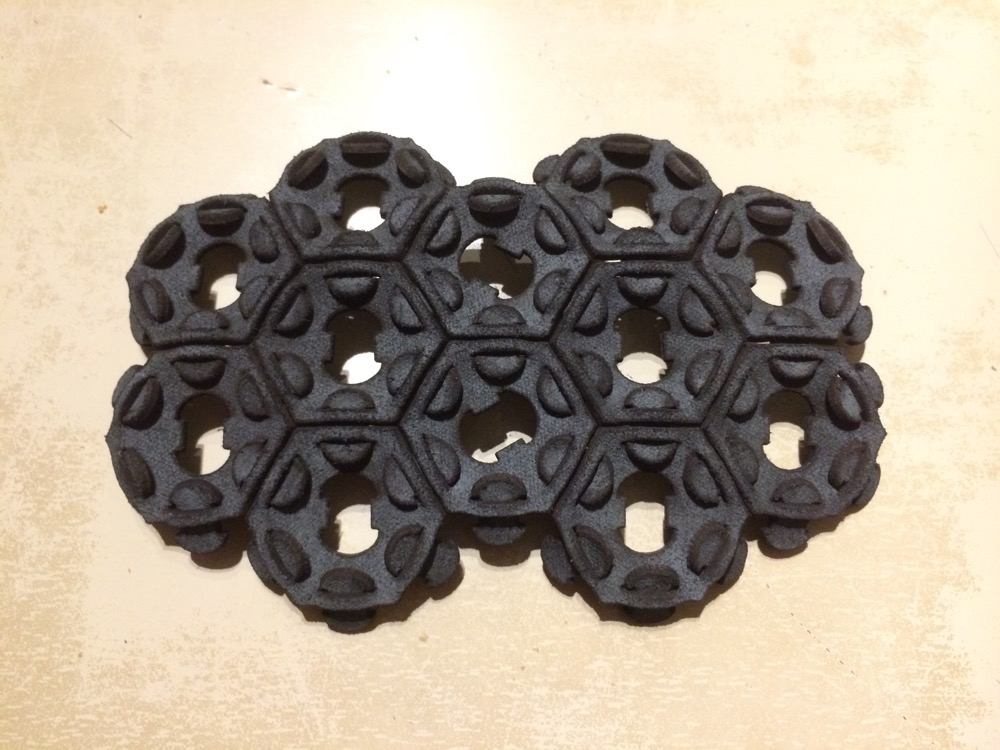 |
First batch |
First batch |
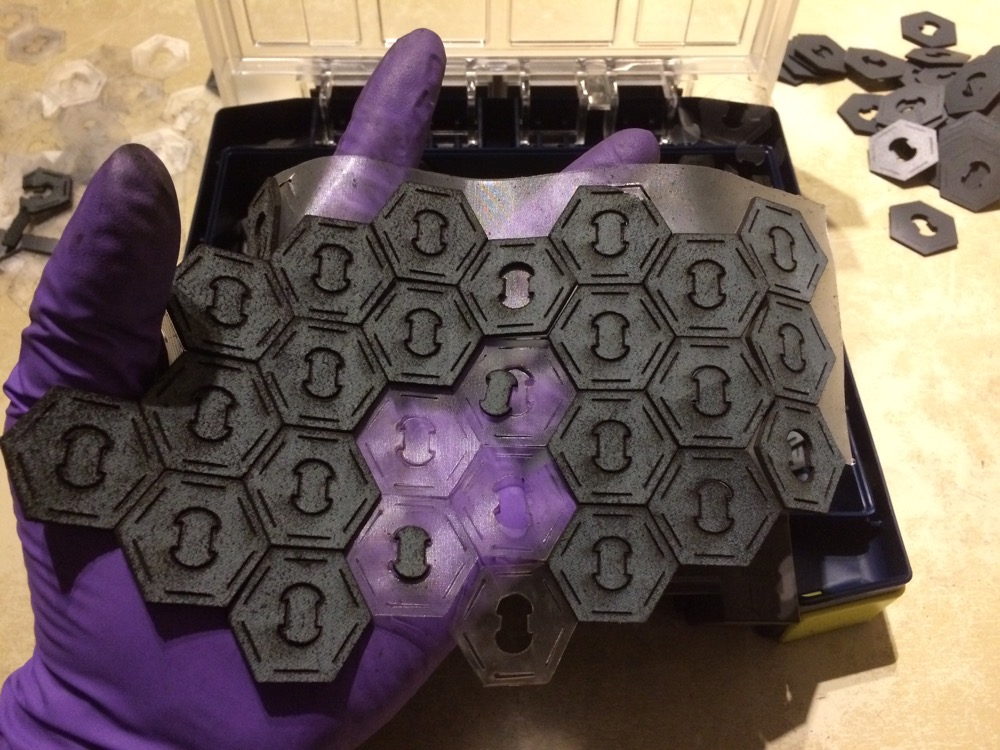 |
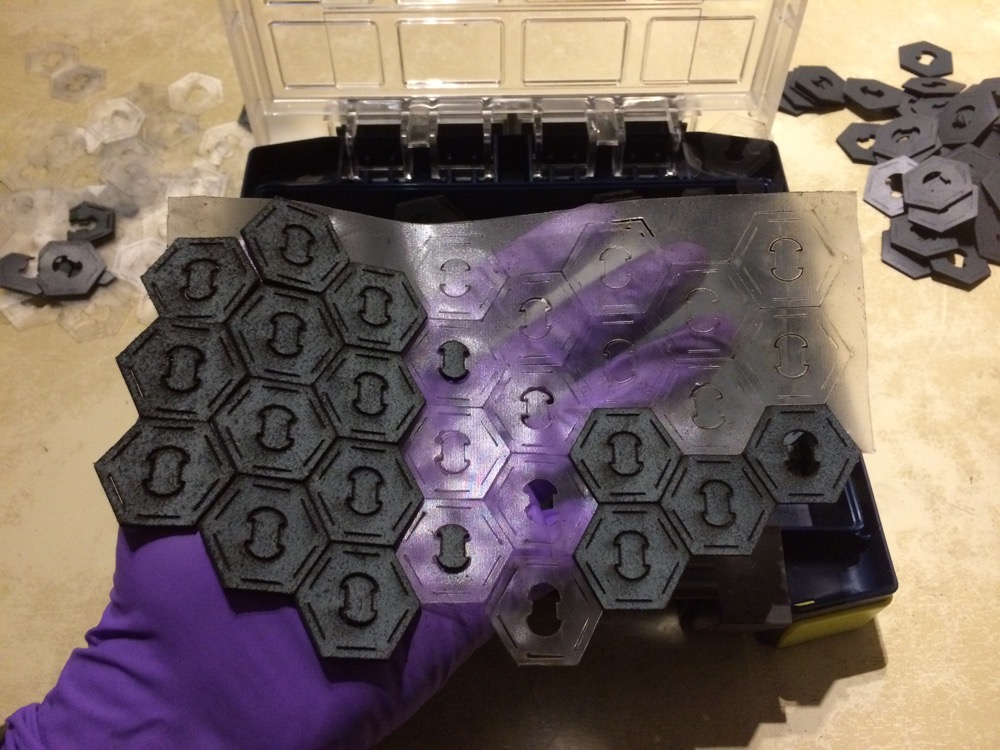 |
First batch |
First batch |
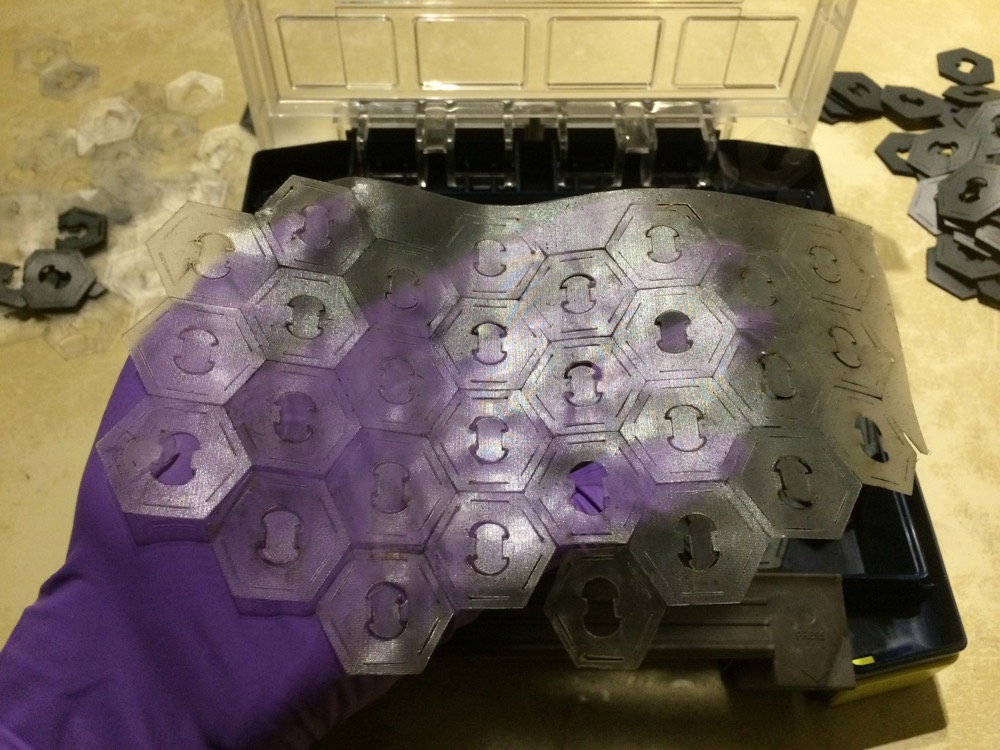 |
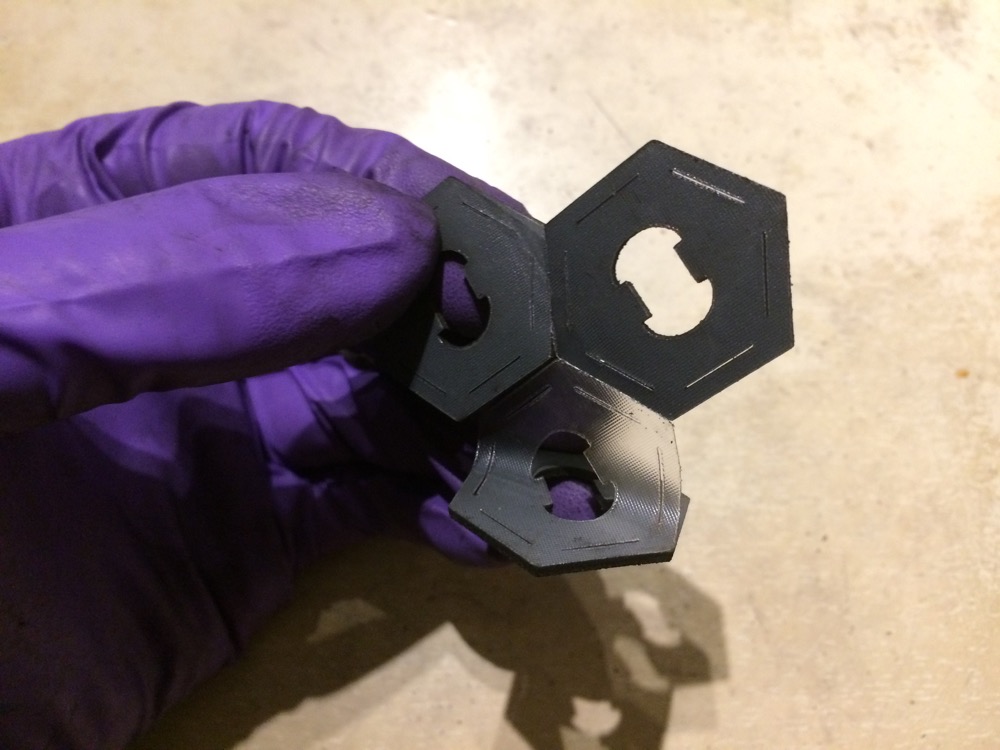 |
First batch |
First batch |
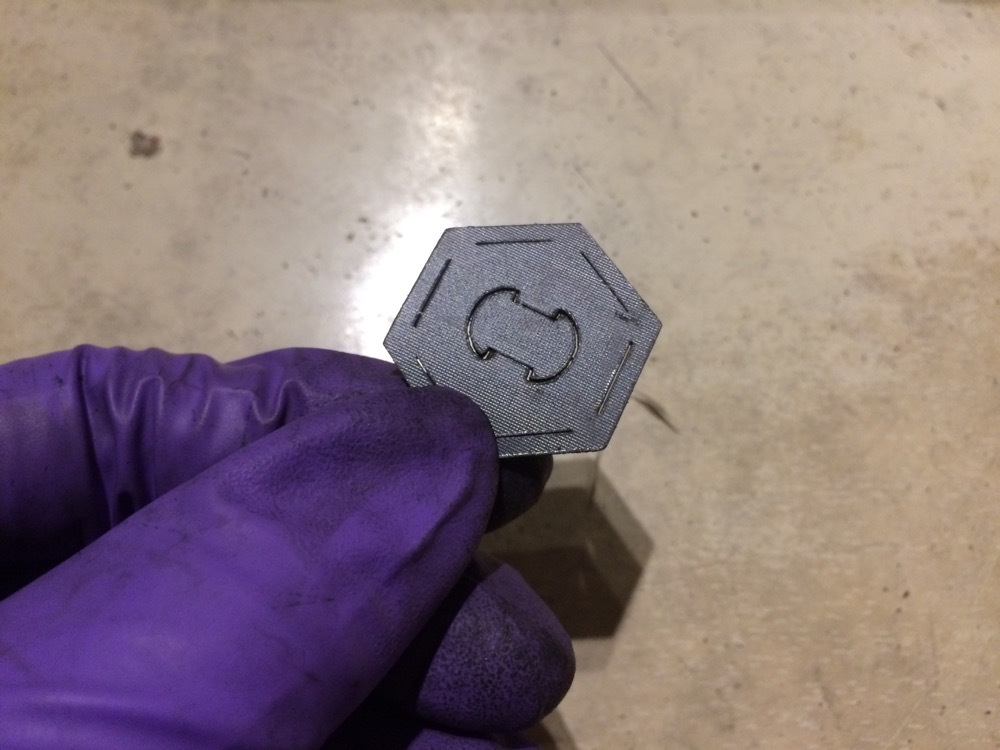 |
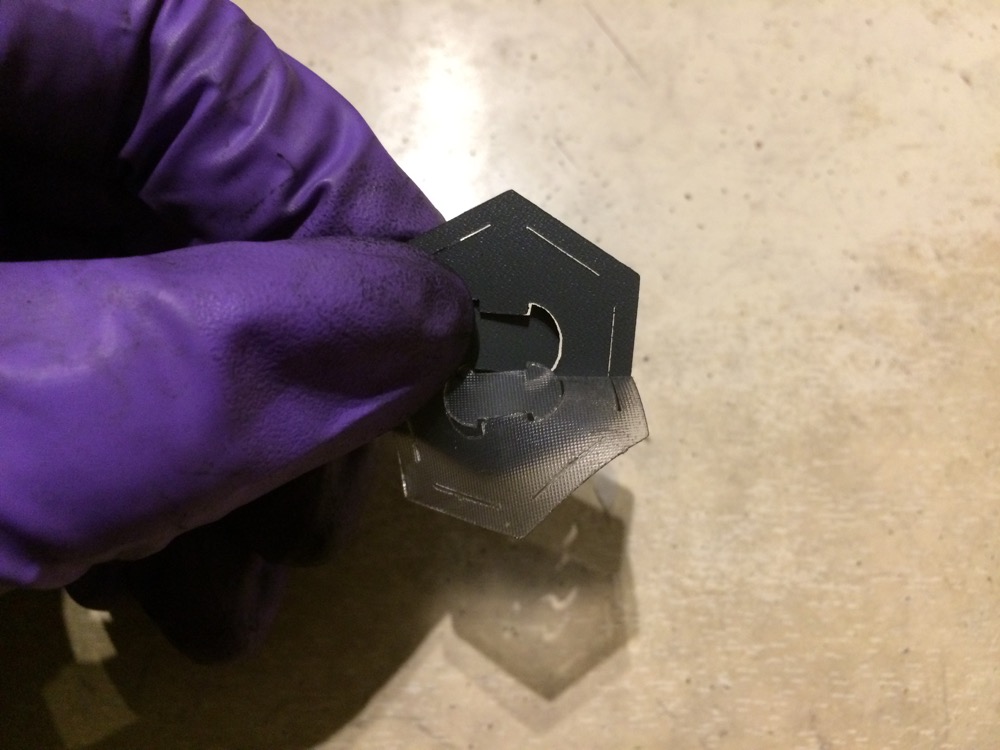 |
First batch |
First batch |
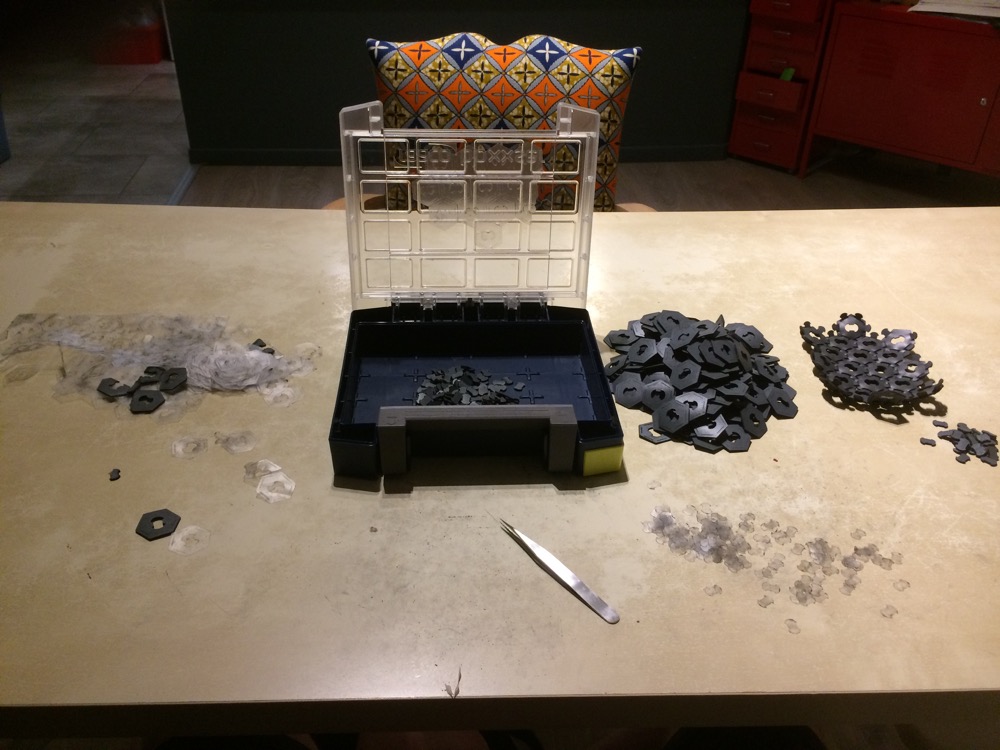 |
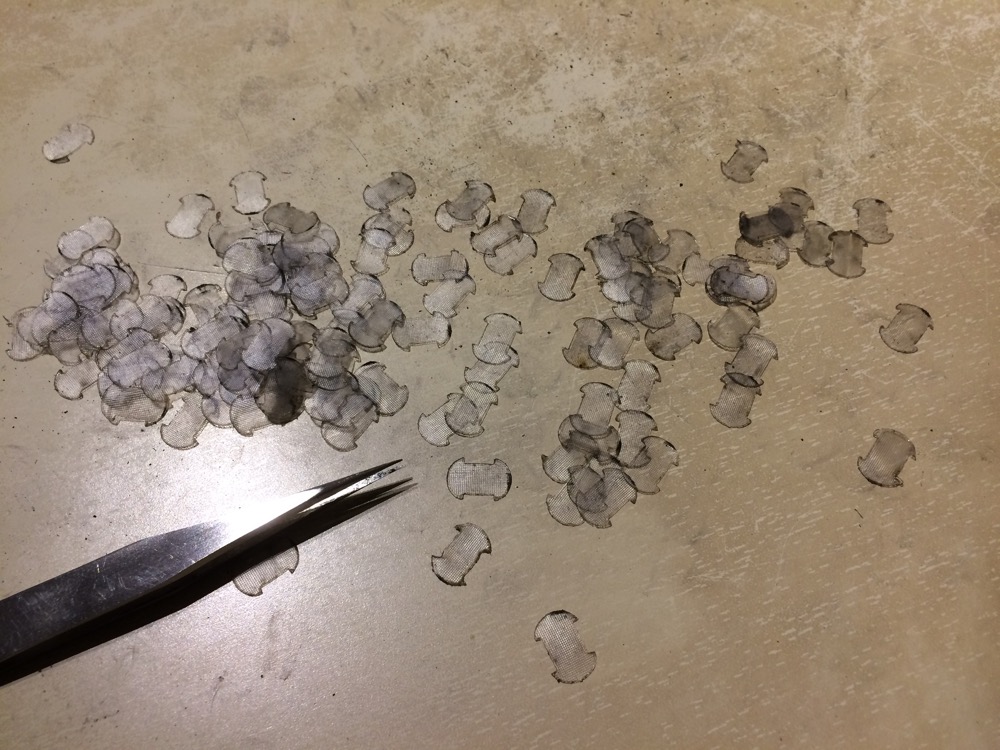 |
12 | New iteration on adding passive-reflective 3D modules to leather garment for body-detection in dark conditions |
I started to test a new light-reflective 3D printable filament. I want insert 3D modules of light-reflective plastic to the leather garment I am working on. It looks like this after a first print:
a |
a |
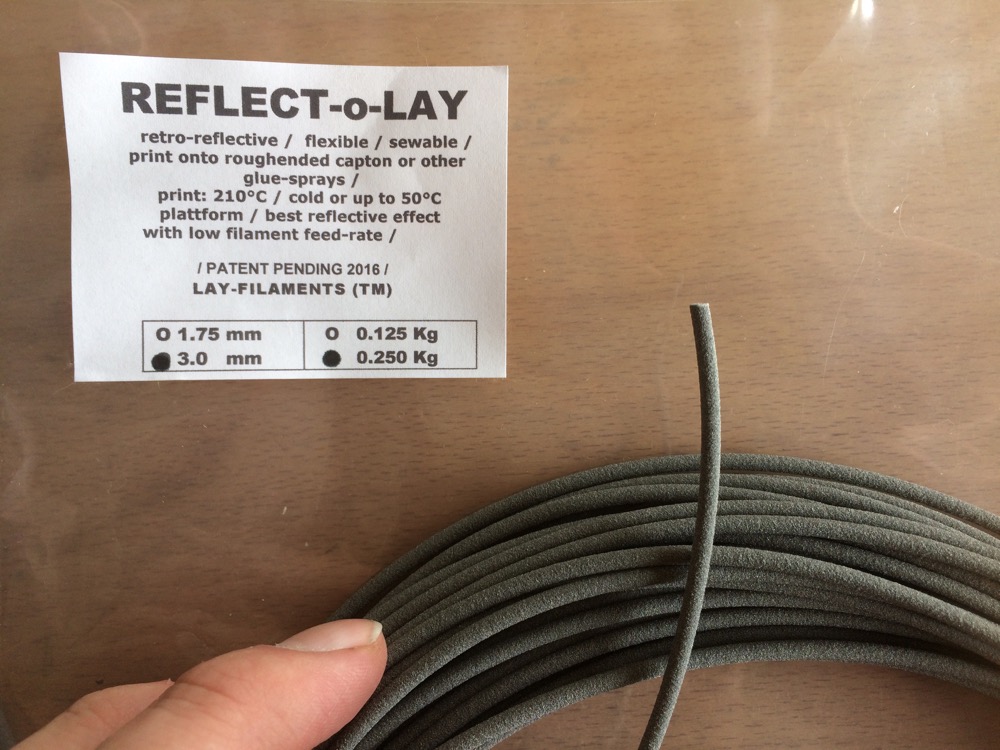 |
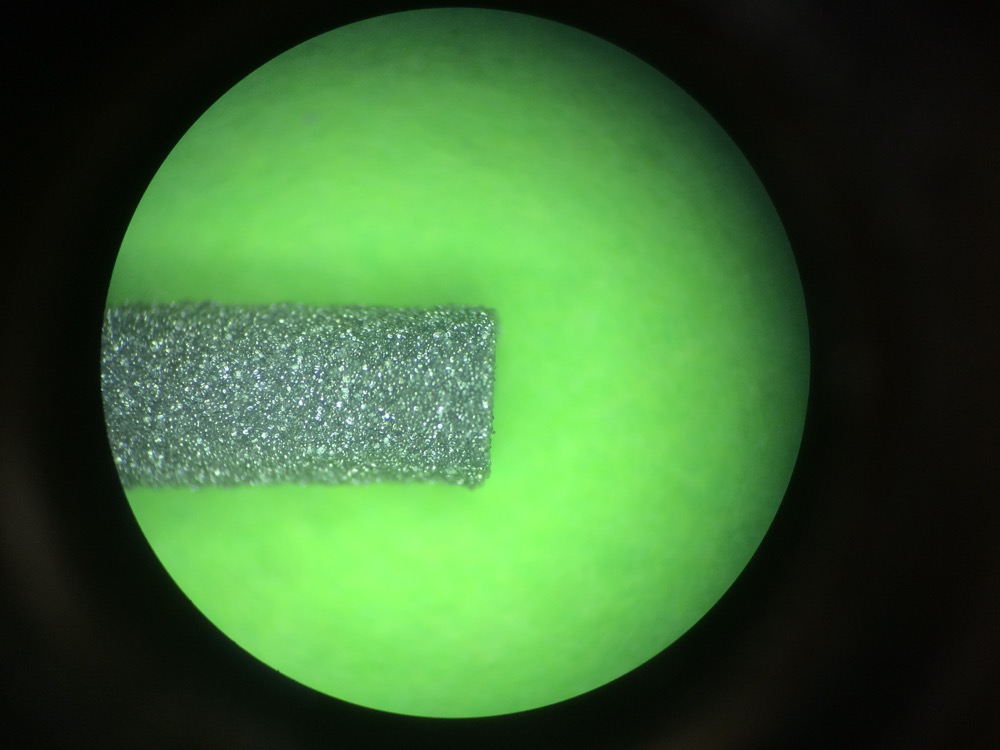 |
Here is a sketch of the 3D printed module I want to insert inside the cut left in the middle of my hexagonal modules. Those cuts outputs are the connectors I use to assemble the hexagons together. Sketched in an old piece of software named 123Ddesign:
a |
a |
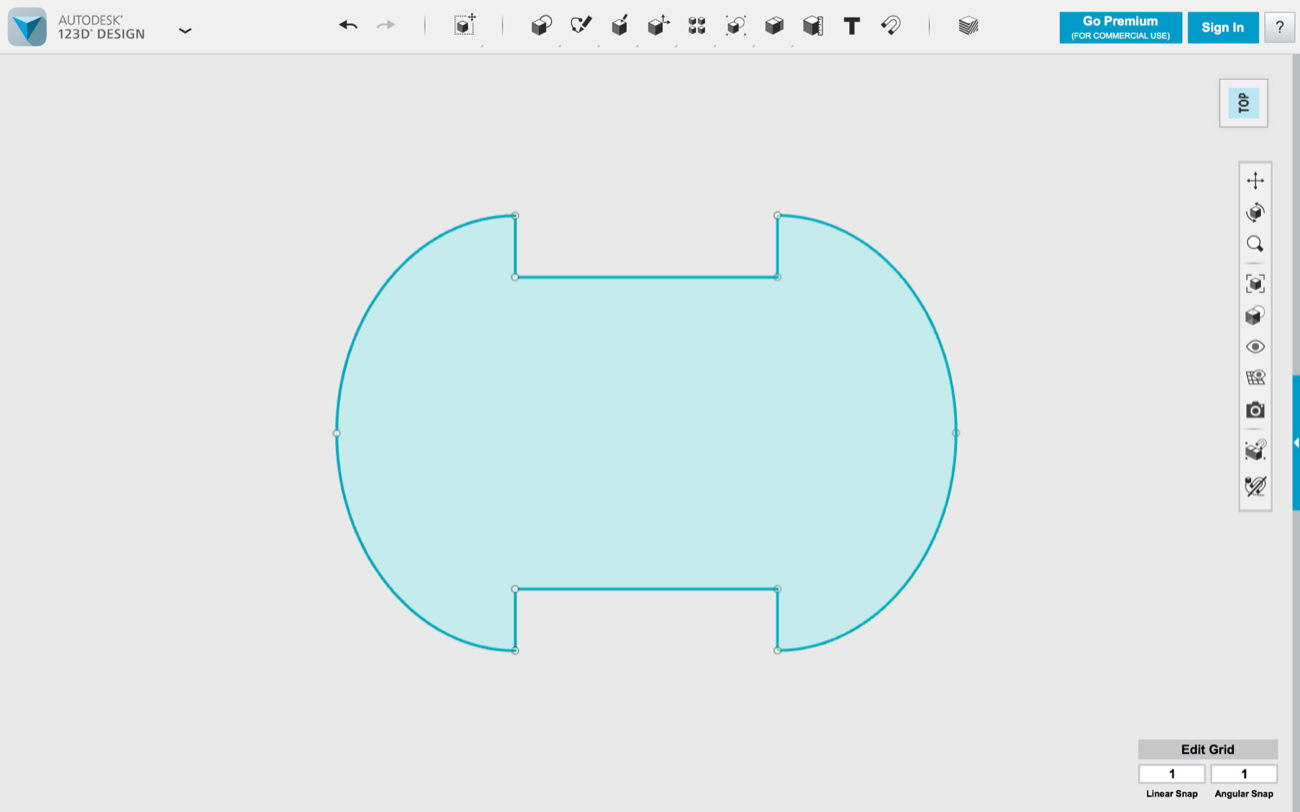 |
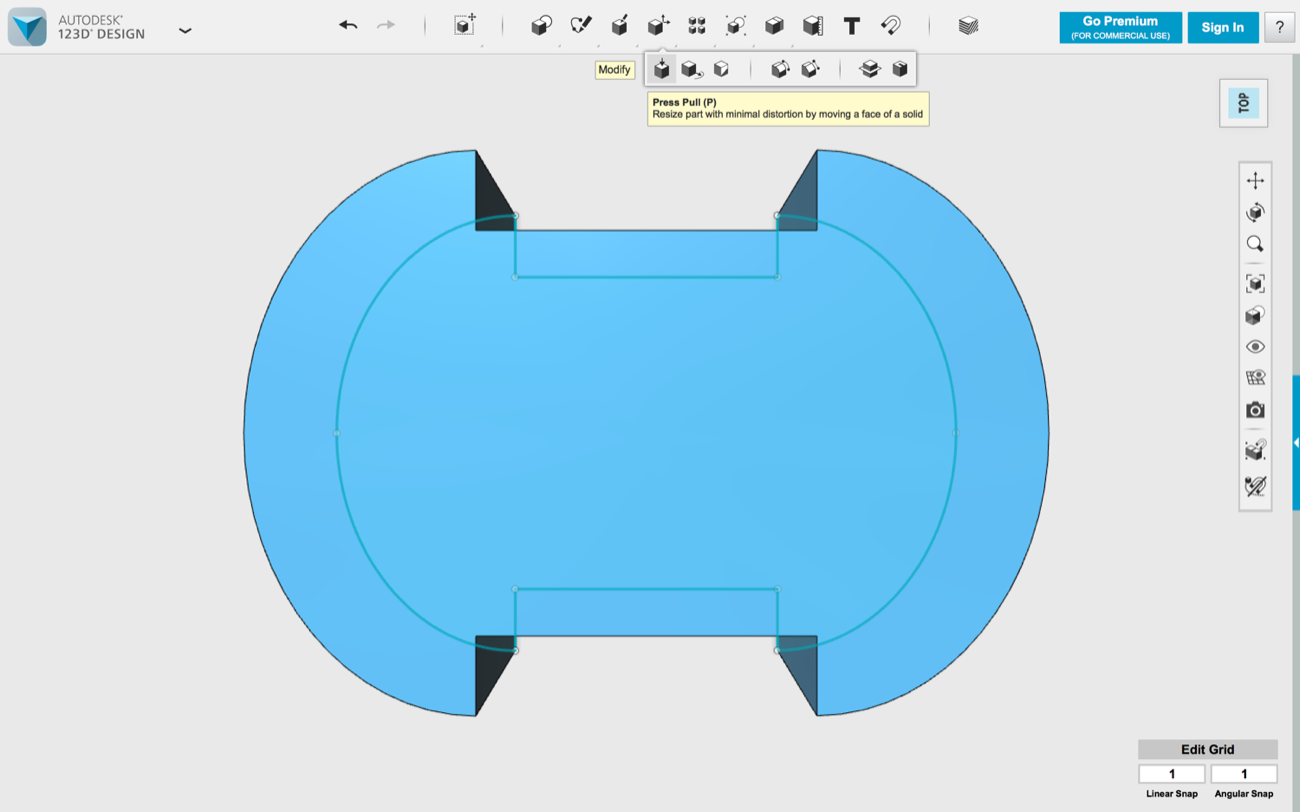 |
a |
a |
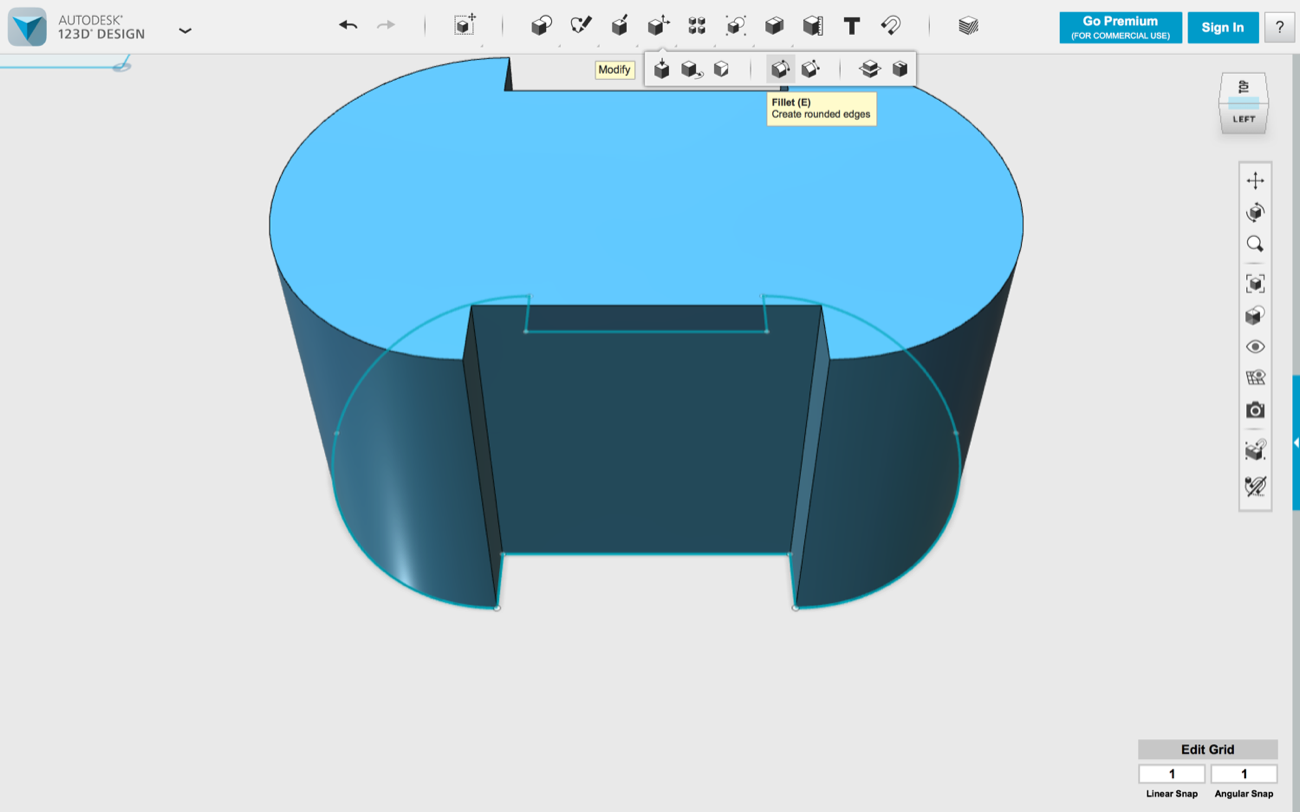 |
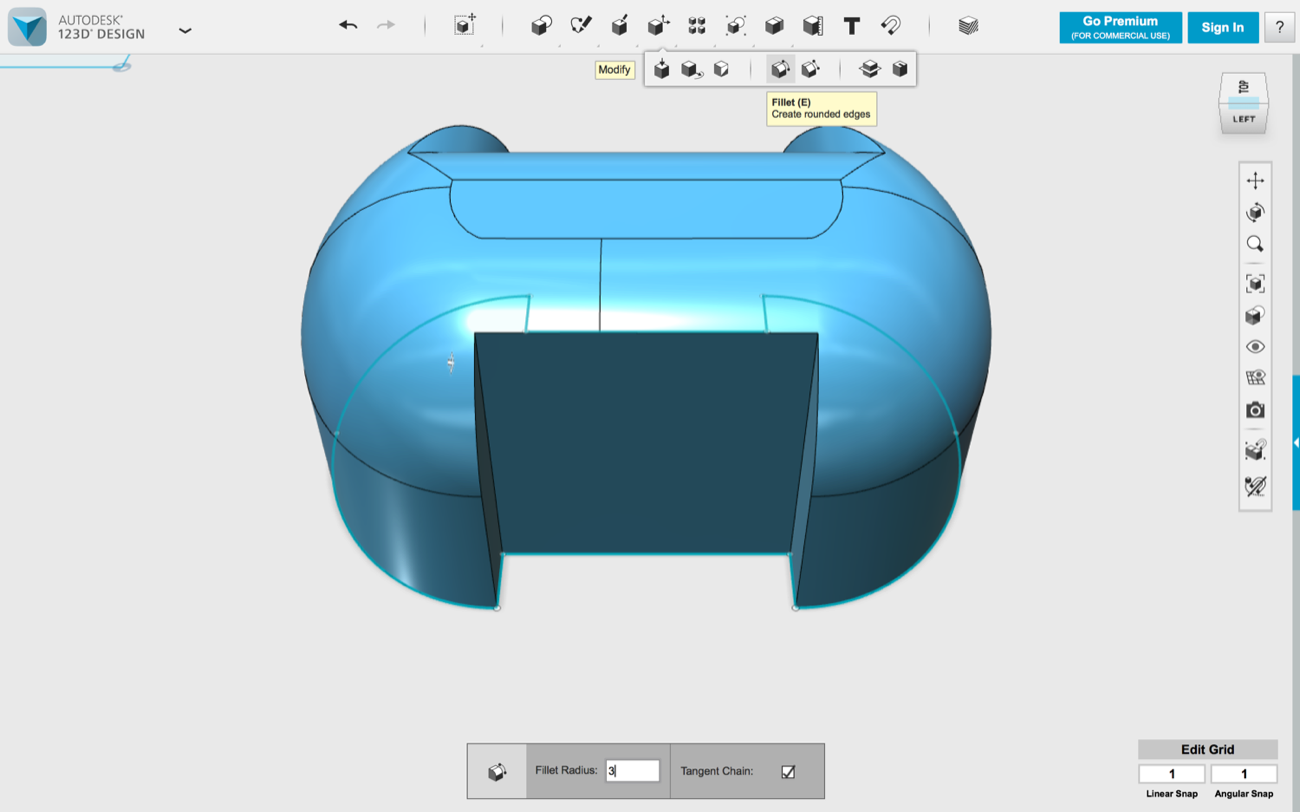 |
a |
a |
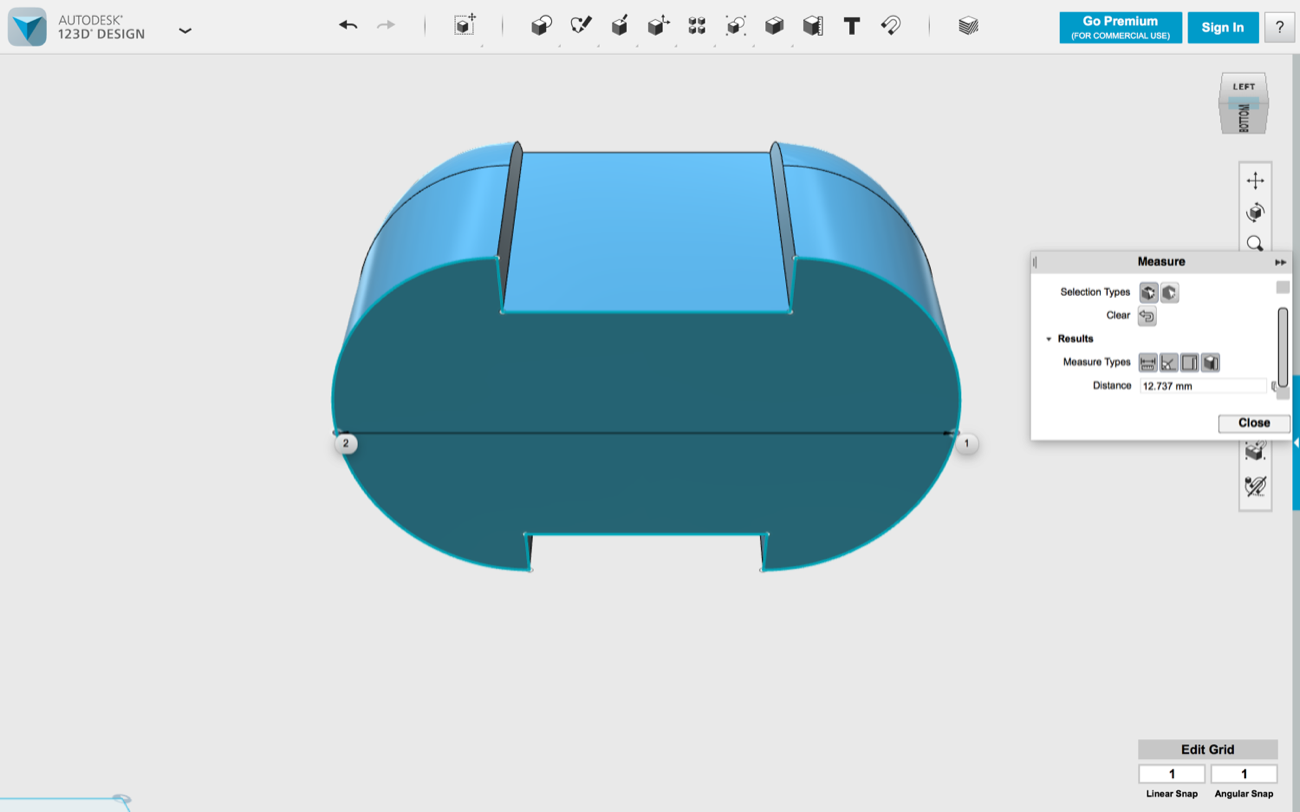 |
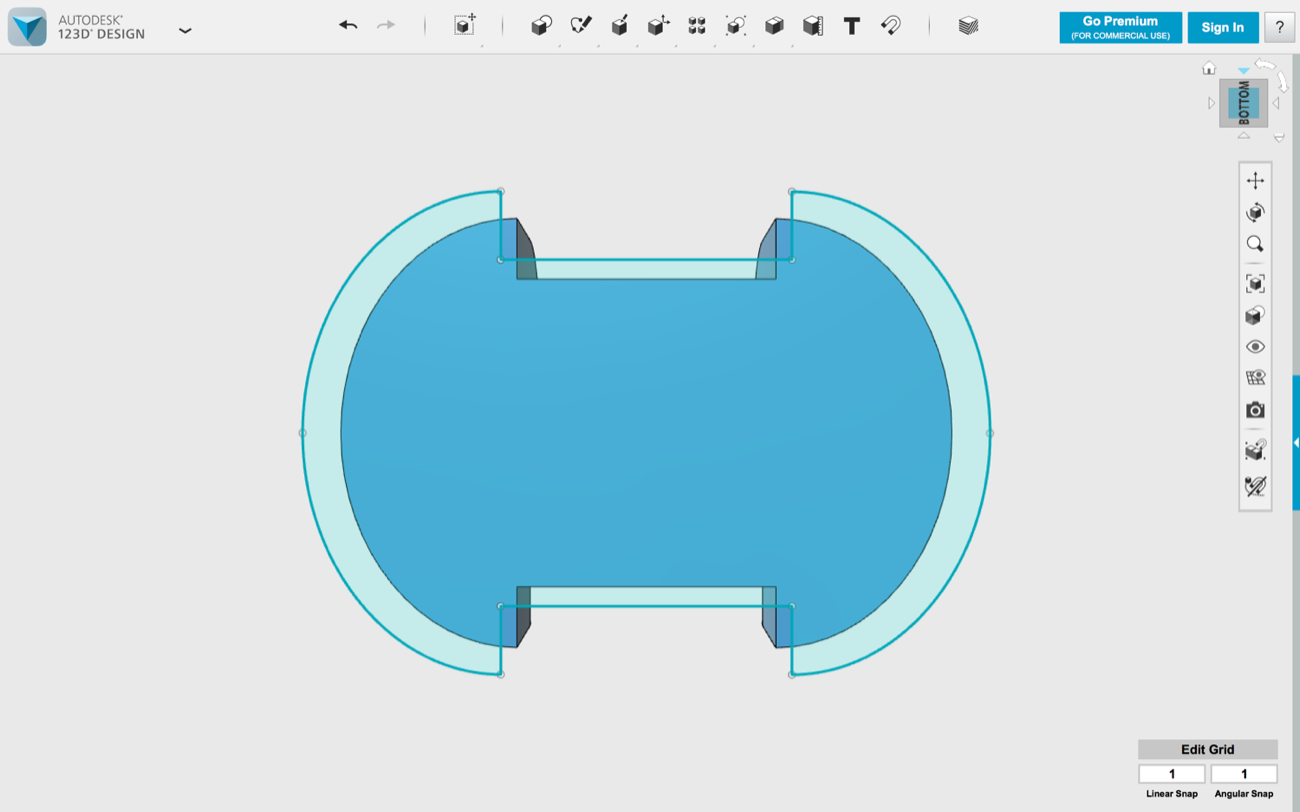 |
a |
a |
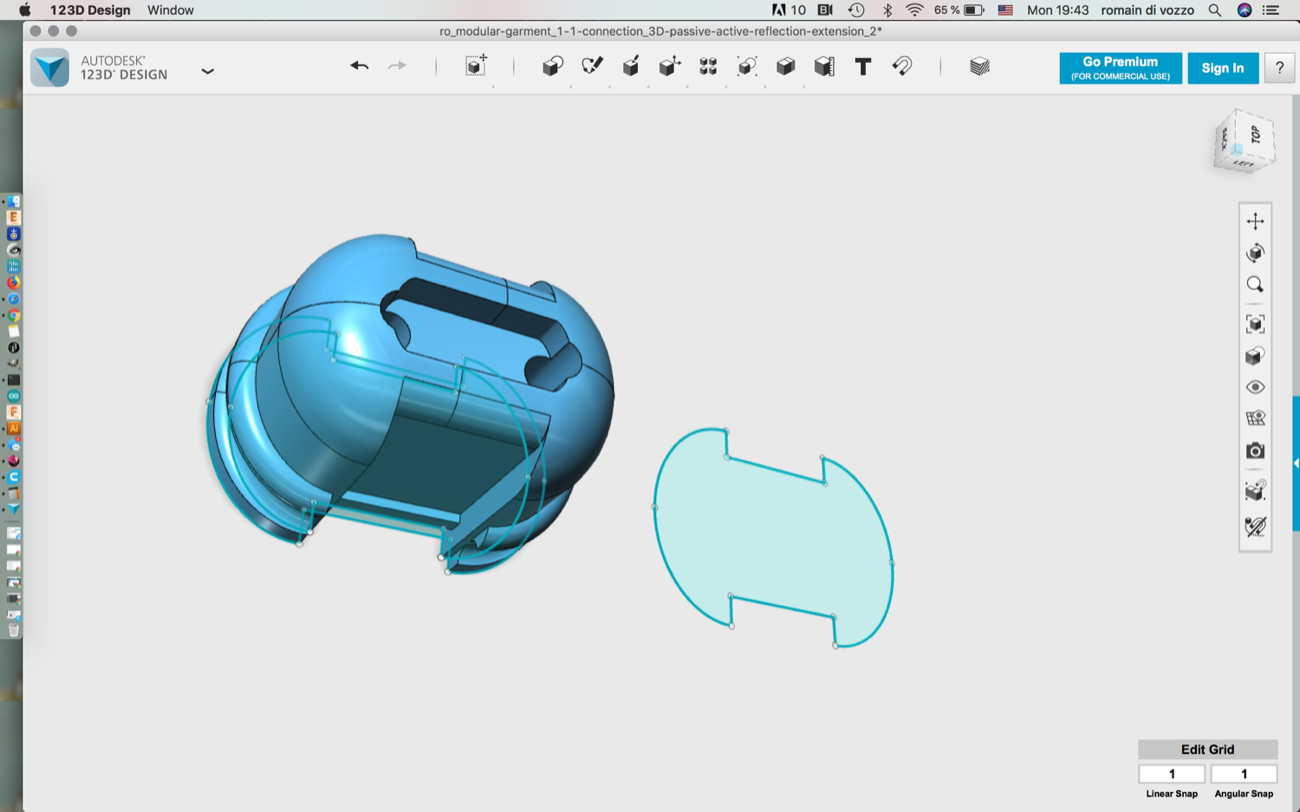 |
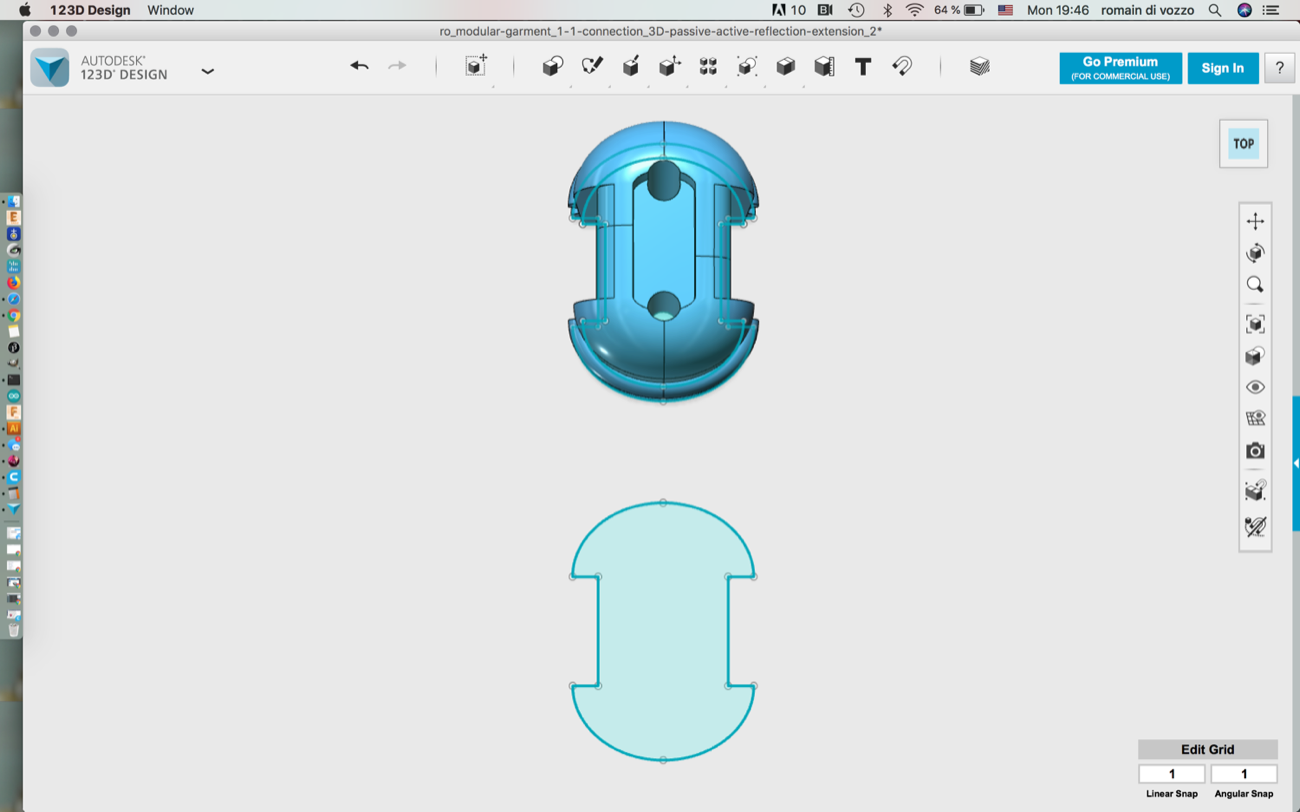 |
a |
a |
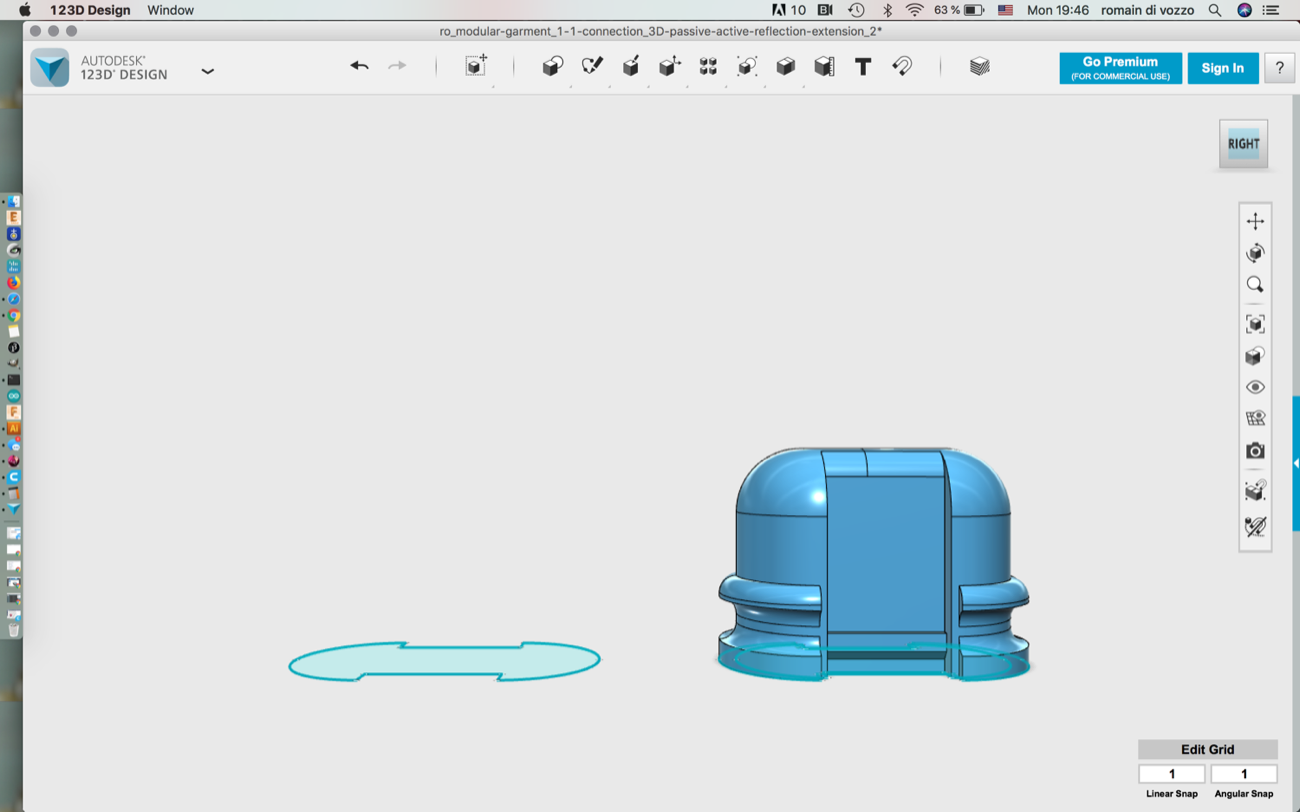 |
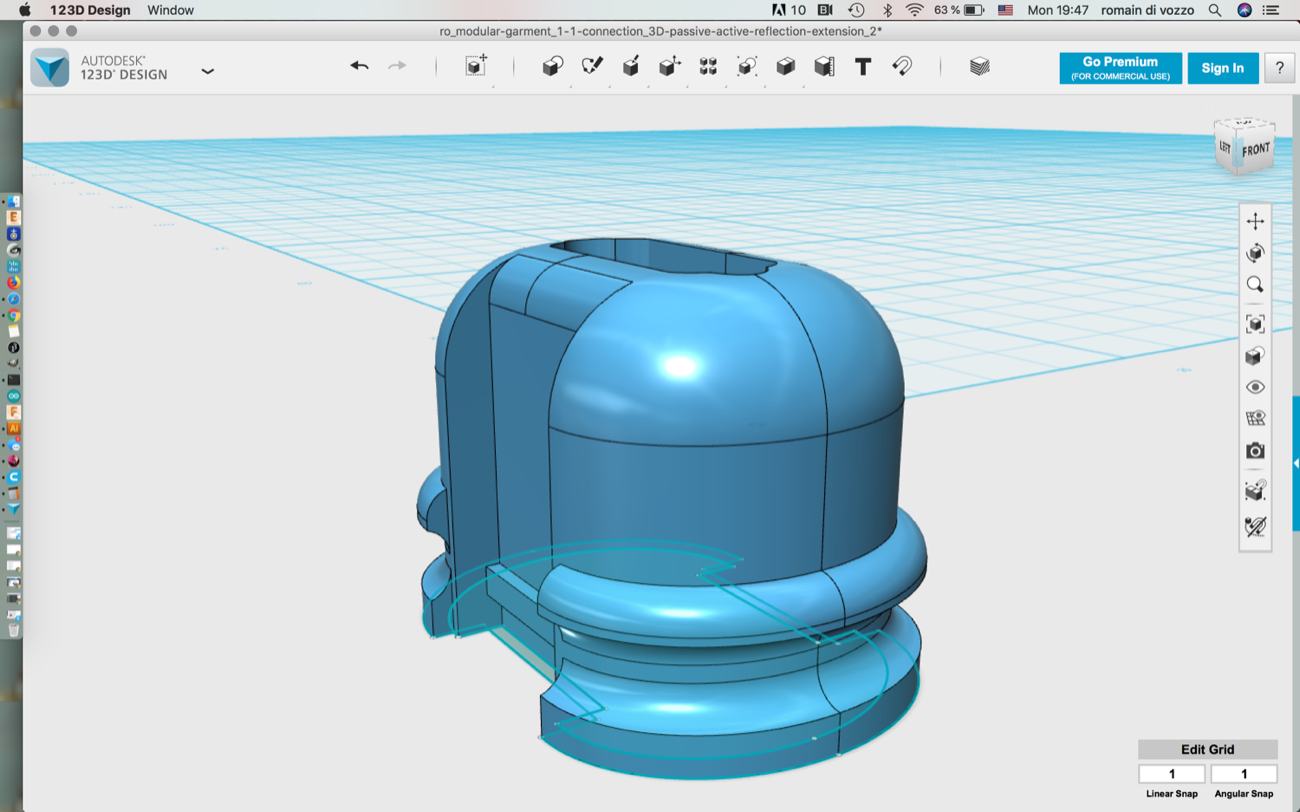 |
a |
a |
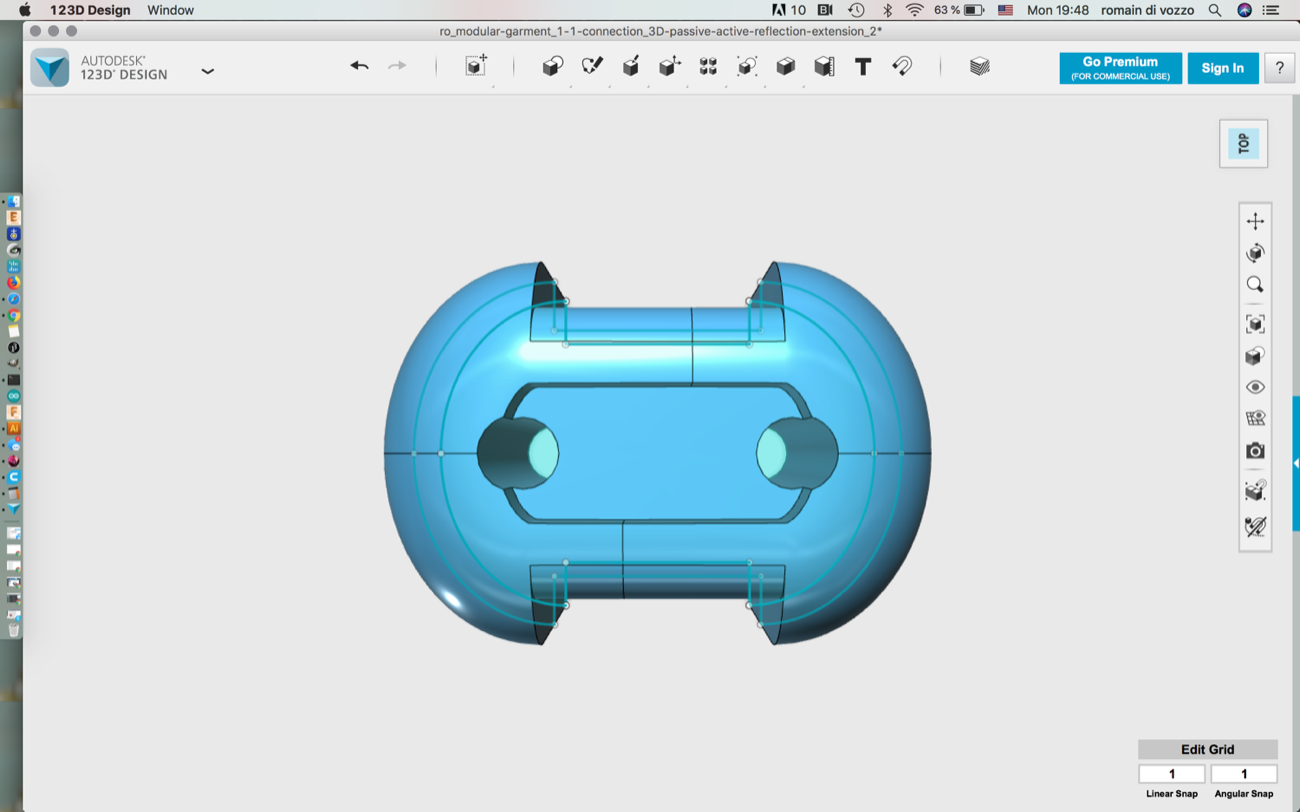 |
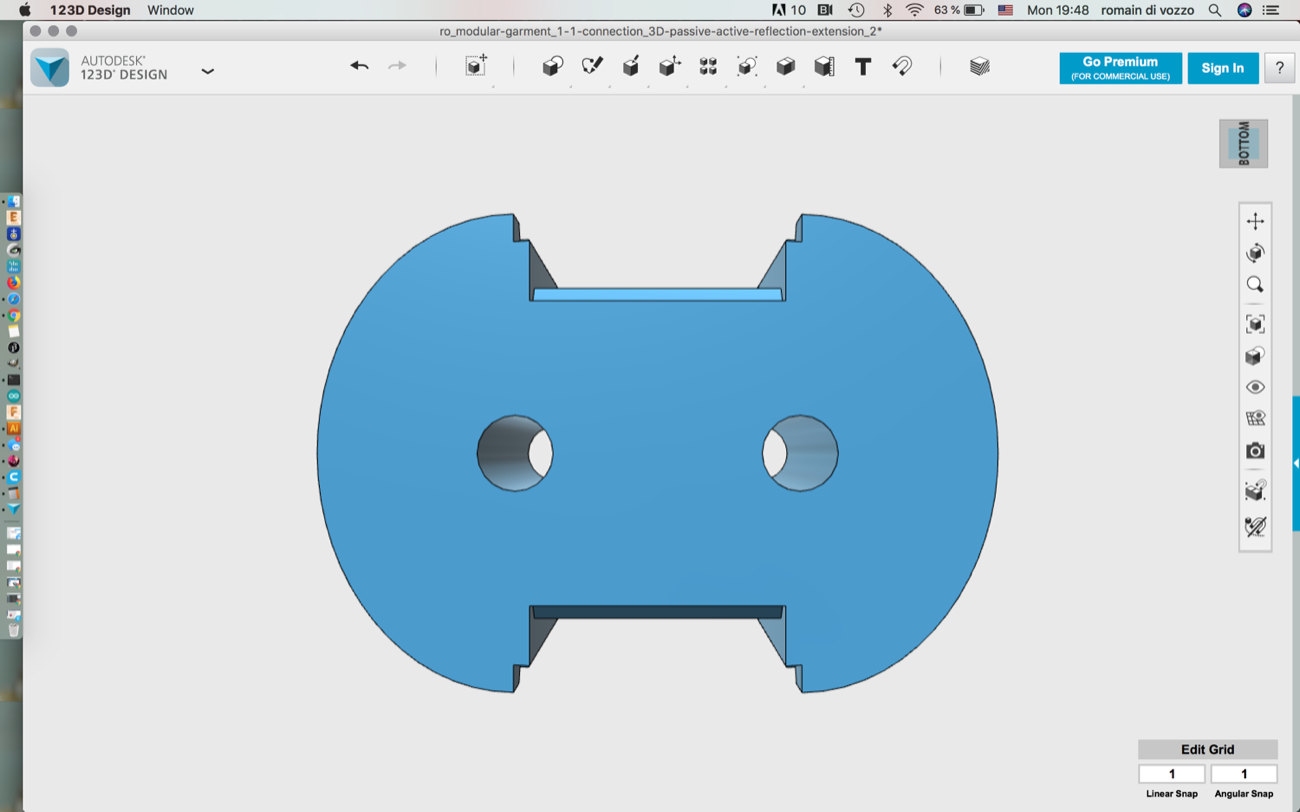 |
a |
a |
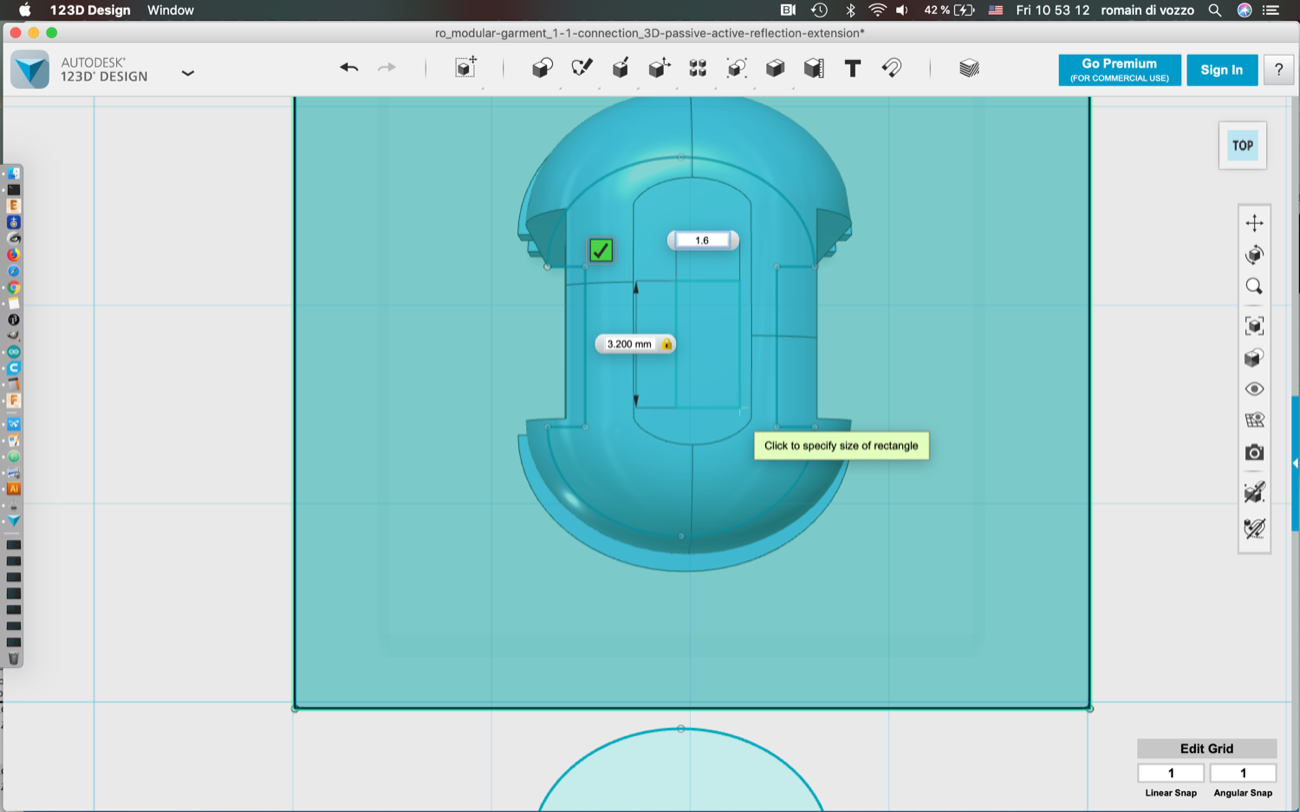 |
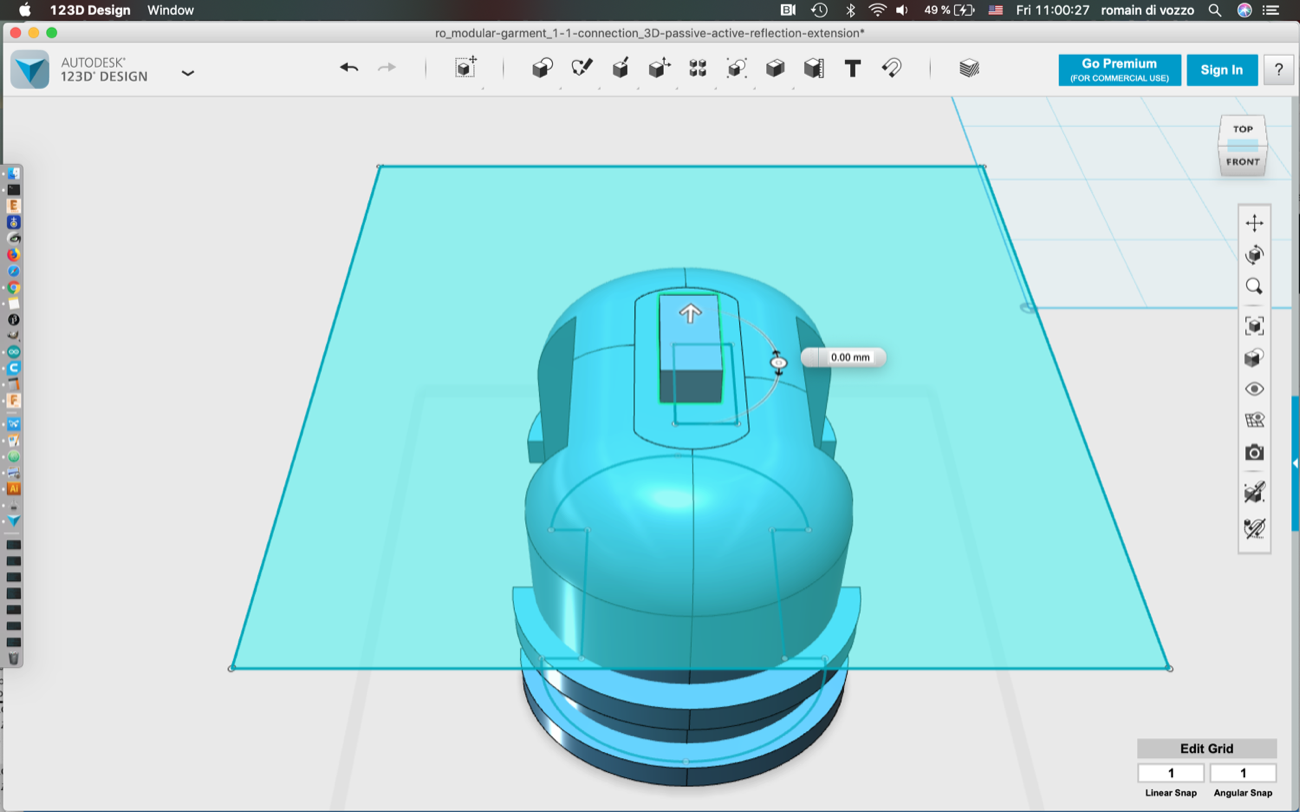 |
Then simulating integration of the 3D light-reflective module into the leather garment:
a |
a |
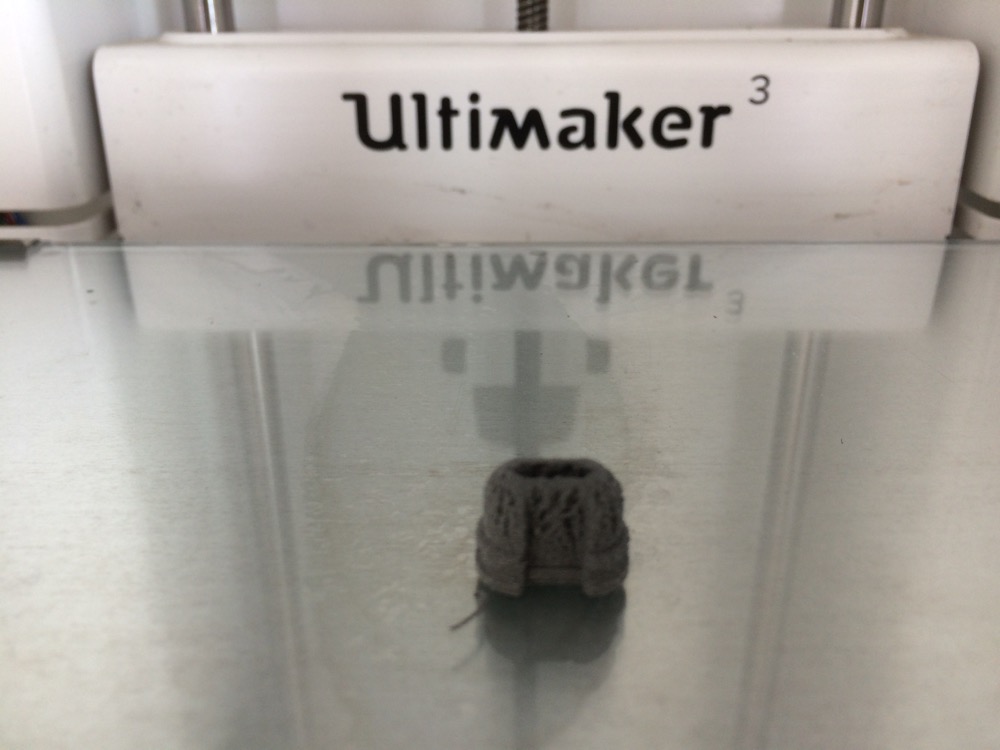 |
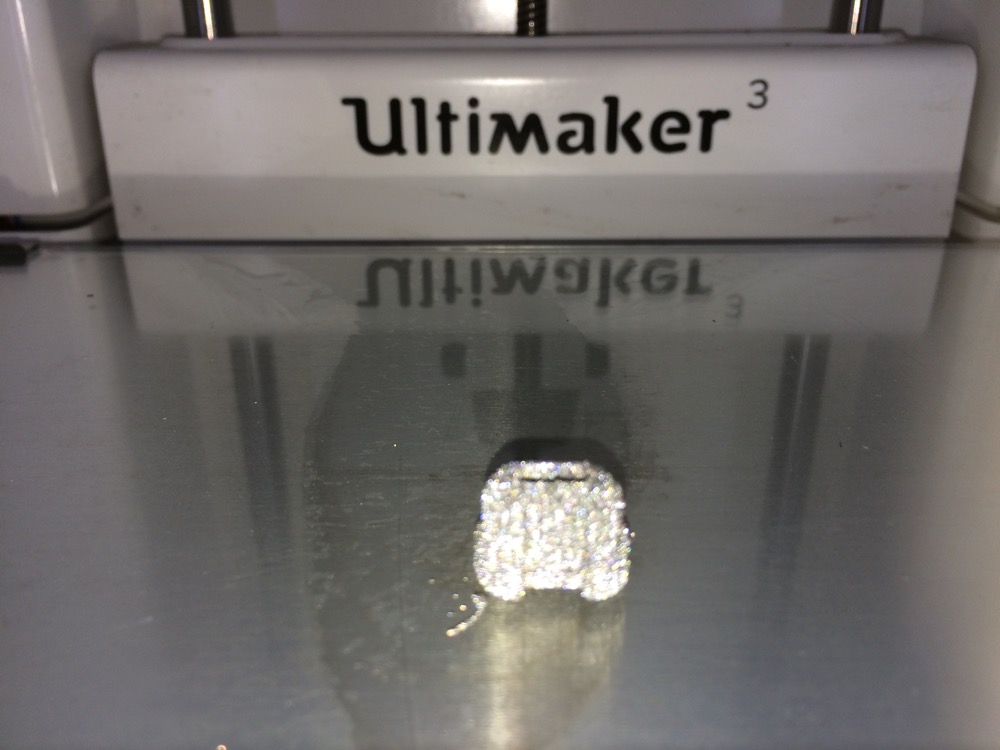 |
a |
a |
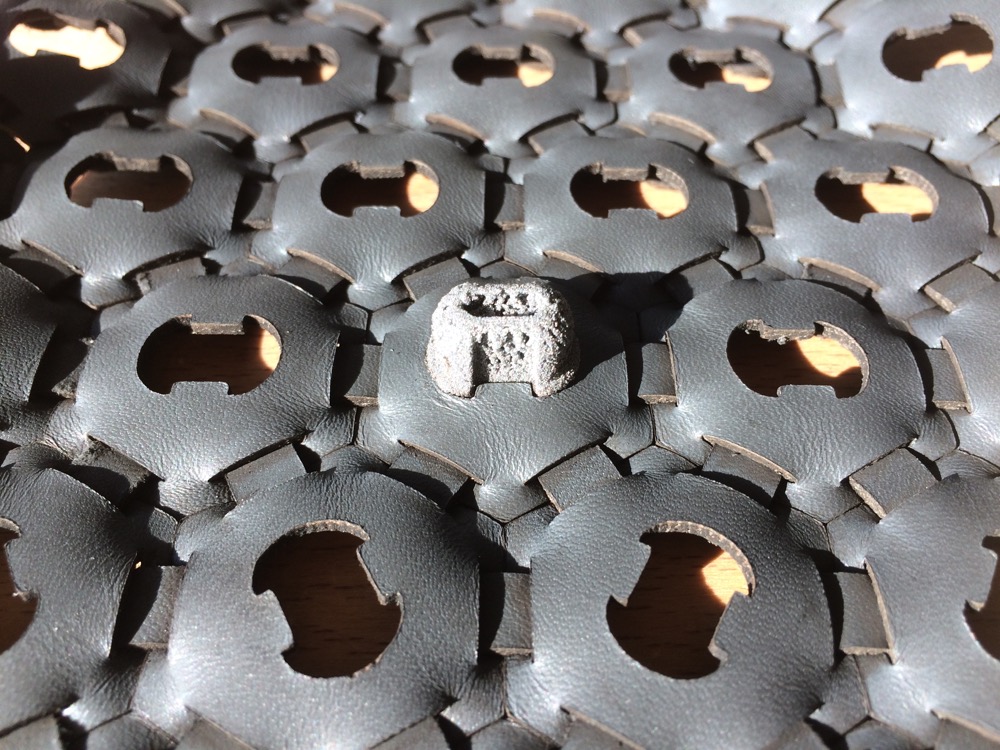 |
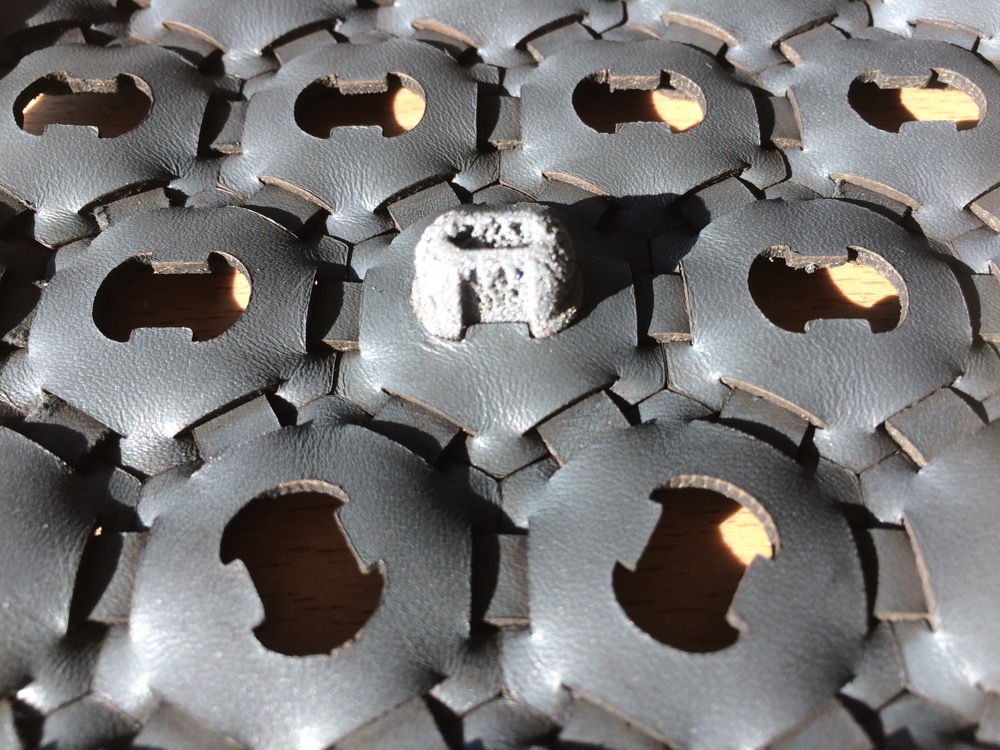 |
a |
a |
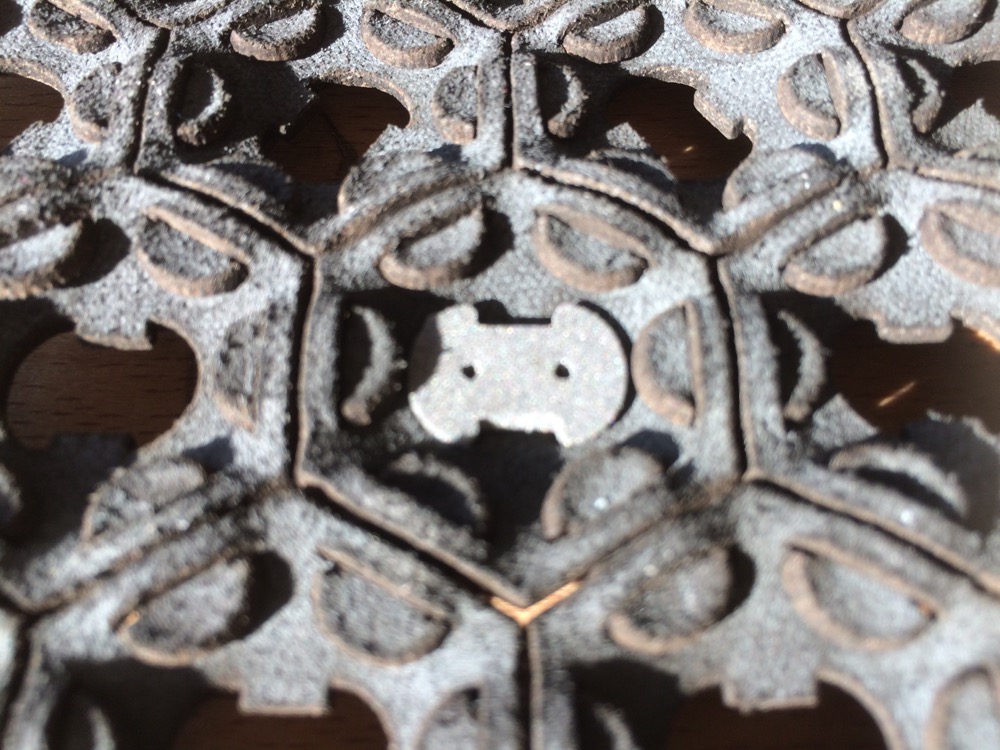 |
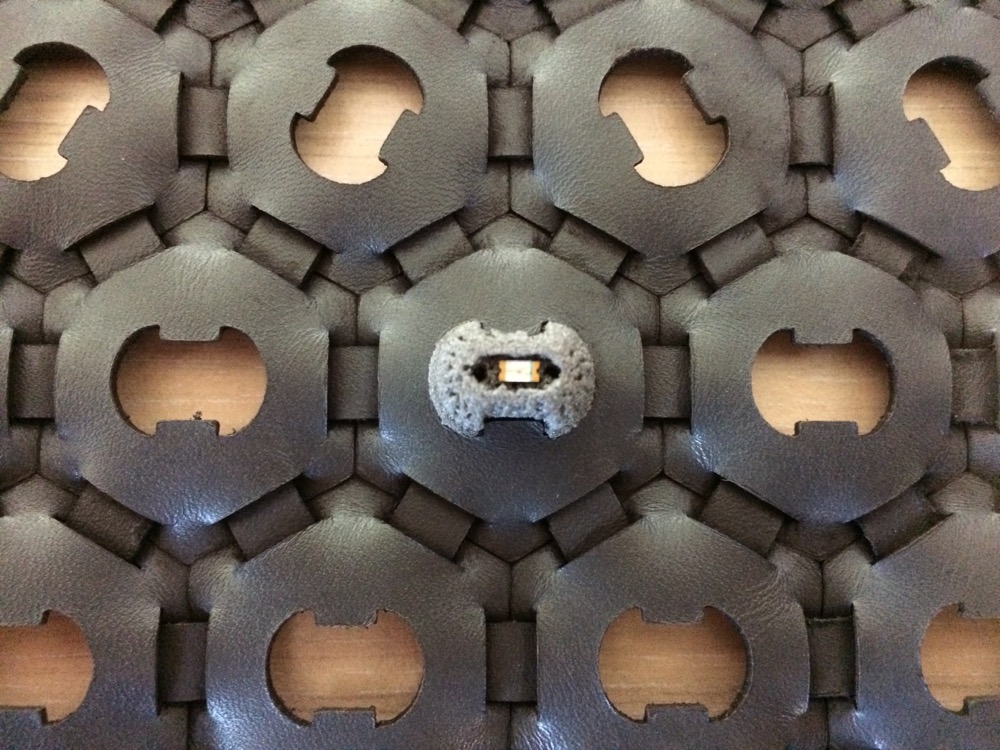 |