12. Soft robotics¶
- Document the concept, sketches, references also to artistic and scientific publications
- Make a soft robotic sample, develop the pattern for the Inflatable and draw a sketch of the air flow
- Build a pneumatic wrist brace (basic level) or thermovynil sample
- Build a Soft Gripper (intermediate level) or
- Build and document a Pneumatic, digitally controlled system , electronics schematic, electronic control and code (advanced level)
- Experiment with different materials, such as silicones, 3d printing, parchment paper, thermoadesive vynil, bioplastic , document your achievements and unexpected outcomes
- Upload a small video of your inflatable working
- EXTRA POINT Integrate it into a project
Research¶
FlowIO¶
Last month the researcher Ali Shtarbanov gave a talk on Soft Robotics at our node.
Festo¶
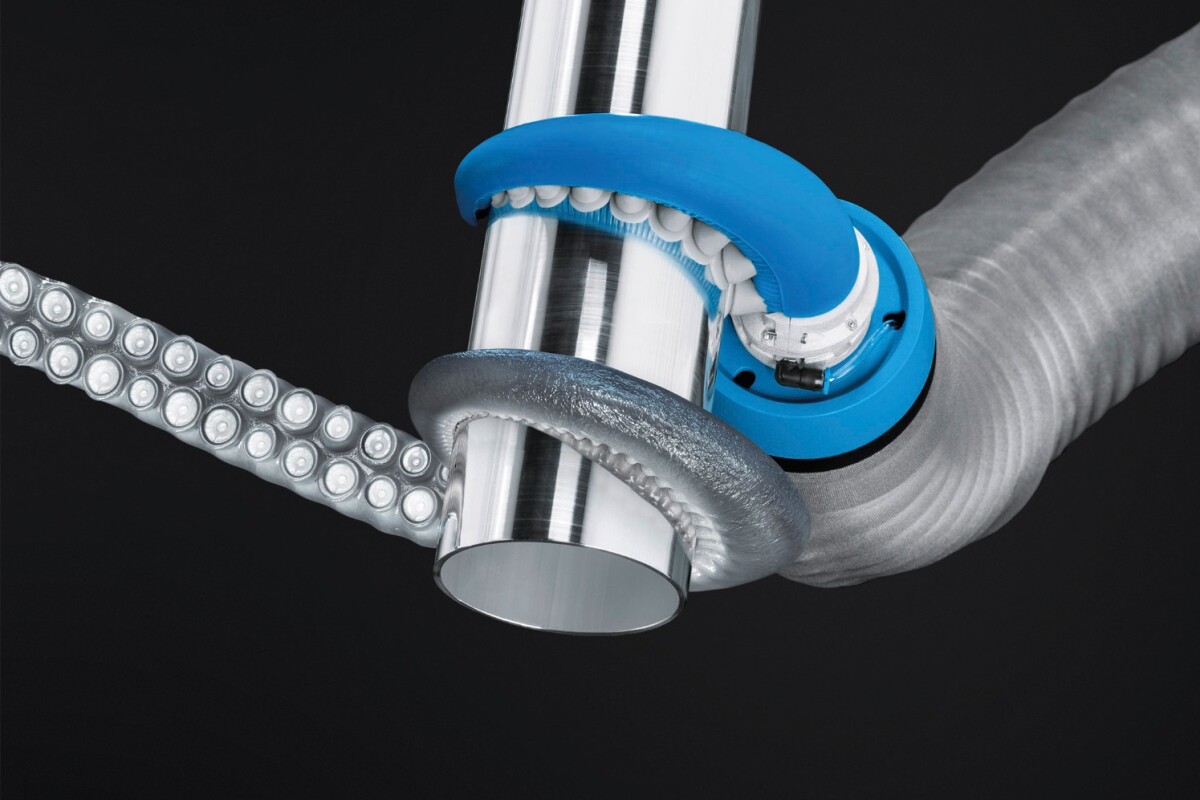
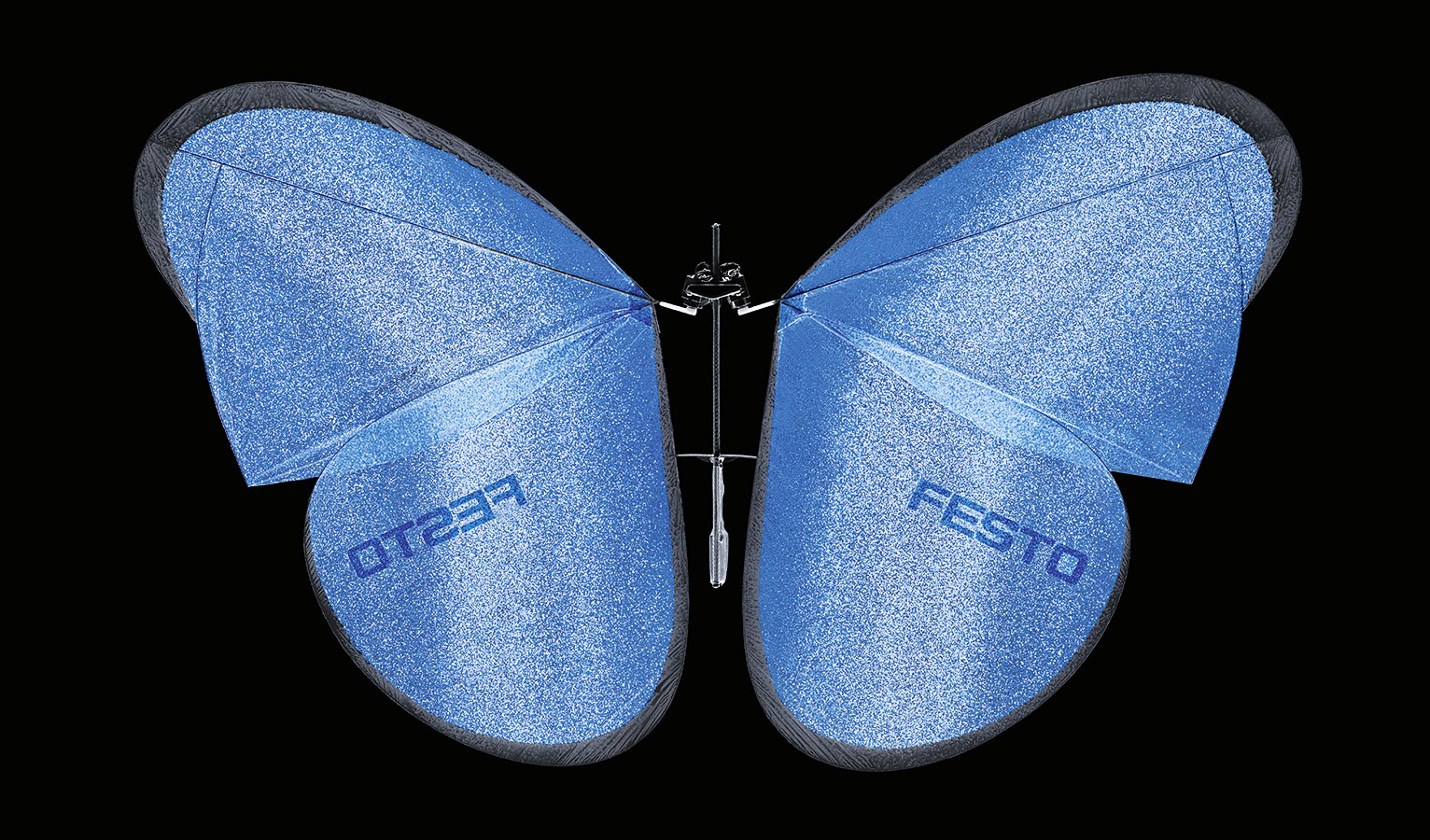
Festo – BionicFinWave
I found inspiring the projects of the brand Festo. They created soft grippers that look like elephant trunk or octopus tentacles. They also make soft robots in the shape of an aquatic creature, birds, flying fox or butterflies.
I particularly like 3D sphere mold made by previous Fabricademists. See for example the final project "Bodymimicry" from Montserrat Ciges.
Another artistic project that catched my attention is the work of Janaina Tschäpe, whose photos show characters wearing bio-inspired wearables made with balloons. See for example the series After the rain and The see and the mountain.
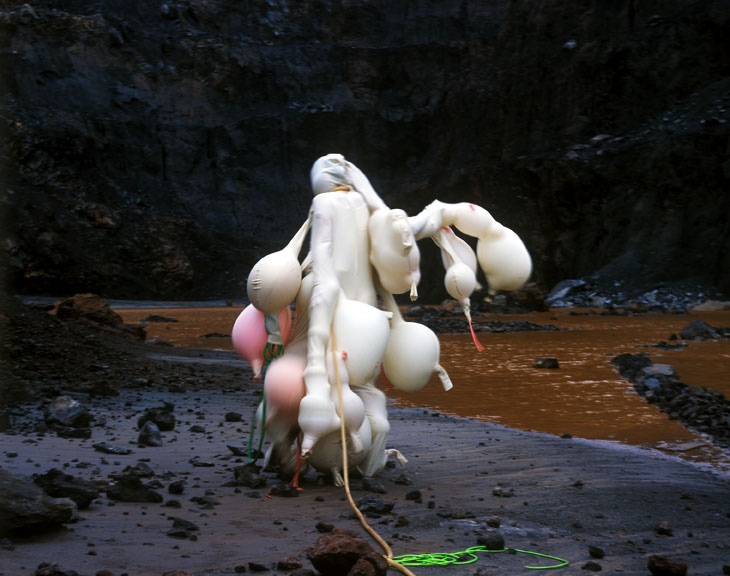
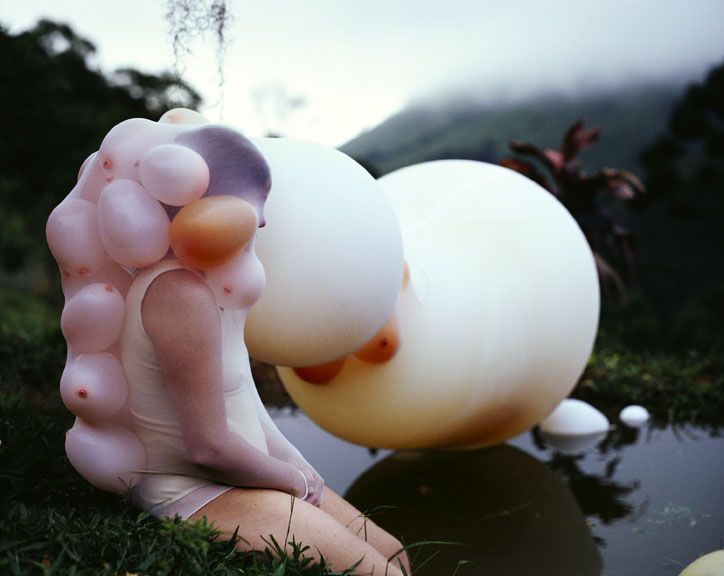
Bending actuators¶

I 3D printed several mold for soft actuators. Both are from Soft Robotics Toolkit. The first one is the so called Pneunets bending actuator, that I have not modified.
Parametric mold¶
The second mold is a parametric one inspired from Pneunets. I designed with the software Openscad. I changed the twist angle of the mold, as well as the number of air channels. The detailed design instructions are available here.
Simulation¶
I managed to simulate the deformation of the air chamber thanks to the software Abaqus, doing Finite Element Analysis (FEA)
Design from scratch¶
I designed a mold with XGen. The graph mode is similar to Grasshopper. The mold is still a work in progress.
Biodegradable actuators¶
I wanted to use an other material than silicone to make soft actuators. As a consequence, I poured liquid gelatin in my previous 3D printed molds. The Glycerin:Gelatin:Water ratio is 1:2:4 .
Jellyfish gripper¶

I followed this tutorial from Jono Sanders to build a 8-armed gripper robot. The 3D model is available here. First I 3D printed the mold in the Ultimaker S5 :
Afterwards, I poured silicone in the mold.
I had a problem because i ran out of silicone. There were other types of silicone available. I don't think I can mix different silicons together. However, I can add a new layer of silicone as soon as the first layer dried. According to this website it is possible to add a layer of tin cured silicon on platinium cured silicone.
Vacuum pump¶
https://fabacademy.org/2018/labs/barcelona/students/oscar-gonzalezfernandez/2018/04/18/Week-11-Output-Devices.html