AB-010
Mounting Vibration Motors To Flexible Materials & Clothing
Wearable computing is showing some tentative signs of coming to age, and with it comes the opportunity for body-worn computers to alert users via tactile means instead of relying on audible or visual alerts.
Of course, for haptic feedback and vibration alerting to work, the user needs to be in contact with the source of vibration, and for most applications, it is sufficient to simply build a vibrating motor into the device. However, there are a number of possible applications that would require the vibration motor to be mounted in a flexible material, for example, clothing.
We’ve already covered mounting vibration motors to PCBs and bulkhead enclosures in our Application Bulletins AB-006 and AB-007 which are great for applications with rigid components. However, using vibrating motors within flexible materials/clothing is nowhere near as common, so we’ve compiled a number of ideas for mounting the vibrating motors into these materials.
Wearable Computing
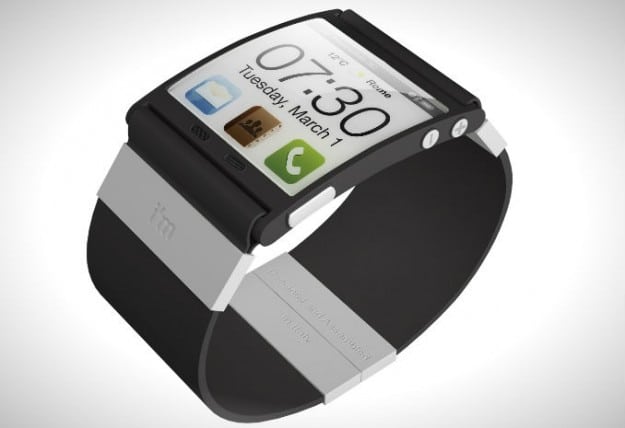
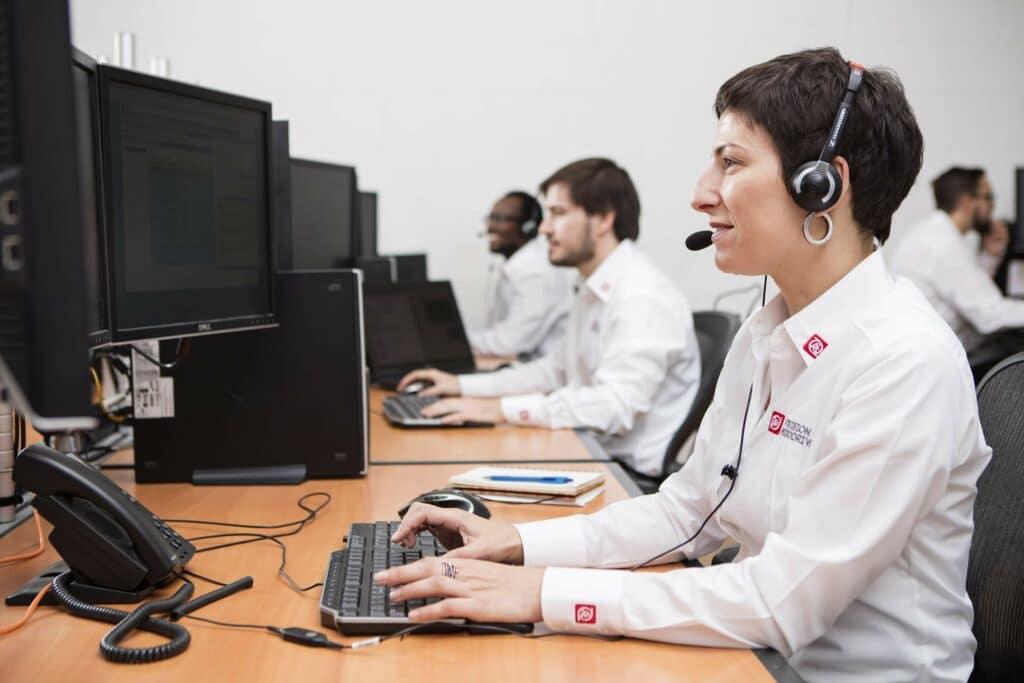
Get in touch
Speak to a member of our team.
Motor catalogue
Looking for our products?
Reliable, cost-effective miniature mechanisms and motors that meet your application demands.
As mobile connectivity increases semi-permanent access to the internet is now commonplace in many parts of the world. Many companies, particularly in the sporting market, are developing smart clothing that can detect information about those wearing these garments, such as heart-rate, reaction times, attentiveness, etc. These garments are likely to have some form of wearer alerting, for example, if an exercise intensity level has been reached or lost. Haptic feedback and vibration alerting with miniature vibration motors are a discreet and quiet way to achieve this.
Vibration Gloves
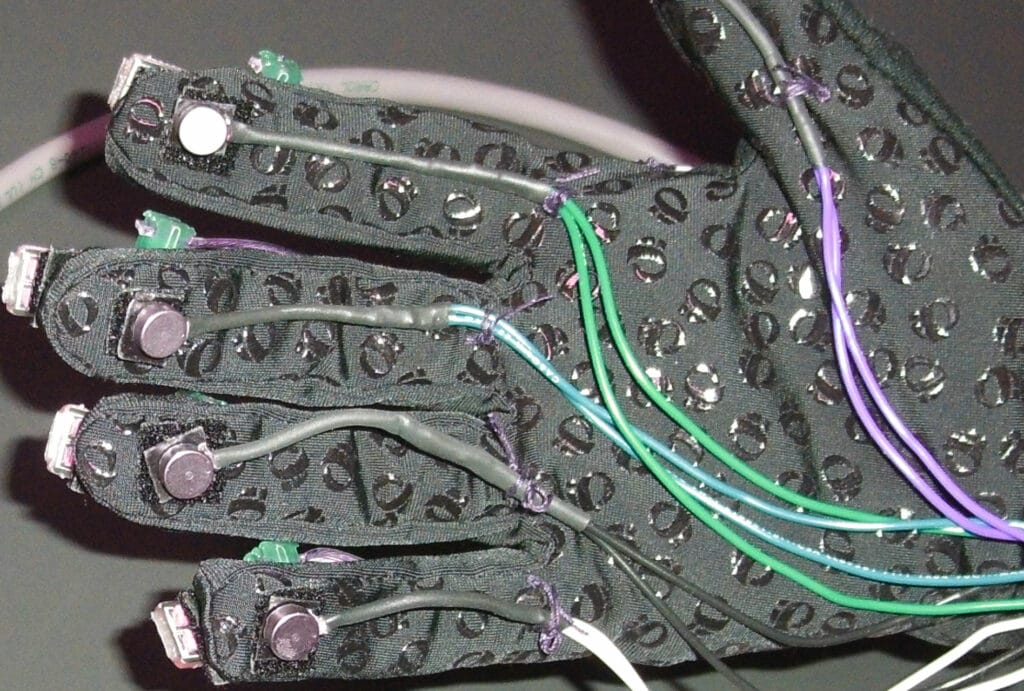
Aside from being used in the wearable computing field, vibration gloves can also be used to aid, for example, stroke patients regain their motor skills. These could also be used to provide haptic feedback to the user, whilst keeping both hands free to use as normal. Combining haptic feedback with 3D projections would give users the ability to interact more conventionally with virtual environments.
Of course, there’s also plenty of scope for ‘good vibrations’ here as well, as a message can be augmented a precisely applied source of vibration.
Vibration Vests
Security and safety guards, either personal or public events, often have to work in loud and distracting environments. Haptic feedback or vibration alerting vests can help provide information at a time when their other senses are overloaded and in a discrete way.
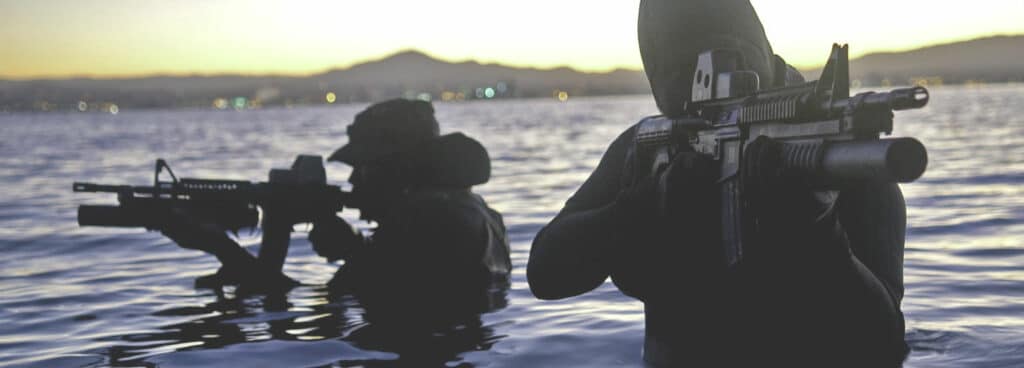
Covert armed forces are already using this technology as a way to communicate without alerting others to their presence. Localising the vibration to particular areas of the body offers more detailed information to be received.
Vehicle / Machinery Safety Alerting
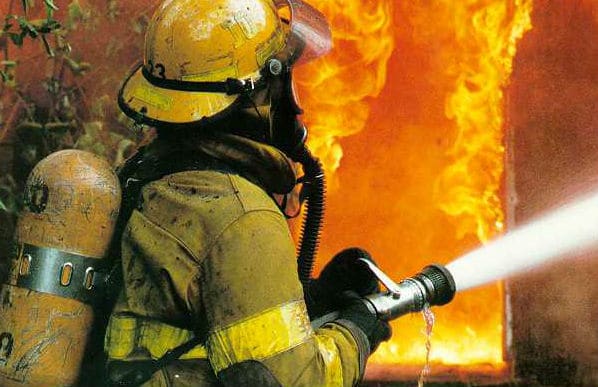
Cars are implementing more vibration alerting features to help drivers be as safe as possible on the roads. Unfortunately, motorbike users do not benefit from vibration motors being added into the bike, as the bike already heavily vibrates and the protective clothing is sometimes thick enough to dampen the vibration from motors. If the motors were located in the protective clothing, then these could be used for a variety of safety alerts such as lane drifting, blind spot aids, or indicators being left on.
Some types of machinery have high amounts of vibration already present making general vibration alerting on the machine difficult to implement effectively. An alternative would be to build the vibration alerts into the clothing so that the vibration is localised and therefore easier to sense.
Athlete Rehabilitation / Performance Measuring
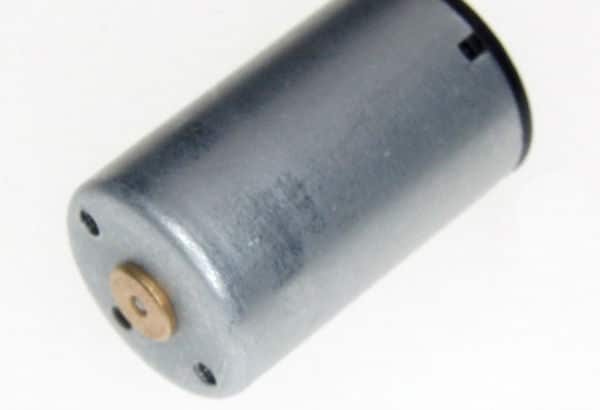
Vibrations are added to massagers to aid the stimulation of blood flow and enhance the healing process, popularly used with health patients and professional athletes. However massaging machines still require an operator, often a nurse or physiotherapist. If these tasks could be performed by wearable sleeves then this could enable the patient to perform self-treatment, increasing patient empowerment and freeing valuable resources.
Haptic feedback is also a growing field for athletes, as they can receive performance details as they practice. For most, this would require minimal intrusion, i.e. lightweight motors mounted to flexible materials to alert of heart-rate levels for example.
Motor Selection
Before considering how to mount the motors, it is worth discussing the types of motor that are most suitable for use with flexible materials. To produce vibrations, the motors must be allowed to rotate freely and the eccentric mass must not be impeded. For more information on the production of vibrations, we have an Application Bulletin on how eccentric rotating mass vibrating motors work. The design of fixing the motor to the material is certainly made simpler when there are no external moving parts and the material cannot prevent the motor from rotating.
With regards to motor size, the required vibration intensity can differ depending on the application. For example, a haptic feedback enabled glove would likely need a lower level of vibration than a vest because the user’s fingers are likely to be more responsive to the sense of touch. Also, a vest may be designed to be worn over other items of clothing, which would further dampen the vibrations and require a larger vibrating motor.
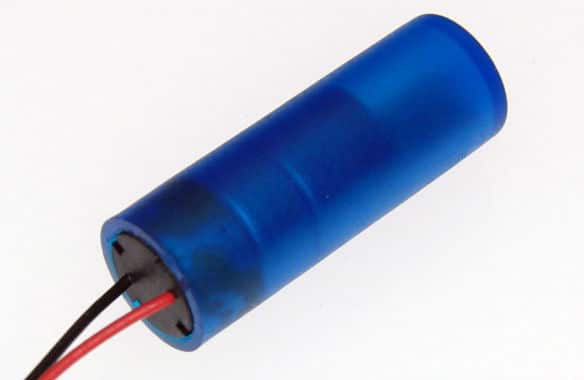
It’s important to remember the effect that flexible material has on dampening too. Motors of lower vibration frequency should be selected, as the as high frequencies are likely to be filtered out by the material. This effect is increased with thicker and softer materials.
We stock types of vibration motors which do not have any external moving parts in a variety of sizes and frequencies, making them ideal for use in flexible materials.
Our Uni Vibe Range™ includes several enclosed vibration motors. These behave in the exact same way as our cylindrical ERM vibration motors, except their metal casing, encloses the rotating mass.
Similarly, our encapsulated vibration motors are also free of external moving parts. In addition, they have sealed casings and connections leads making them easier to waterproof, there’s more on that in the next section.
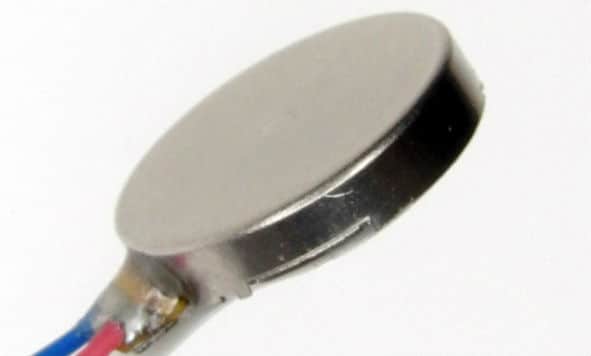
Coin or pancake vibration motors also have a case which contains the rotating mass. All of these motors use leaded connectors and have self-adhesive pads designed specifically for easy mounting. They are a similar form factor to our Linear Resonant Actuators (LRAs), which may also be suitable as they too have no external moving parts. LRA’s do however require a suitable driver, see our Application Bulletin on driving LRAs for more detail.
Water Proofing
With flexible materials, a water-proofed motor is very desirable. Assuming the flexible material is to be worn, or at least in contact with human skin, it will probably need to be washed. It is also possible that the material may be exposed to moisture during its normal operation, such as rain or sweat.
Here at Precision Microdrives we have taken some of our encapsulated vibration motors and coin vibrating motors and used two types of potting compounds to seal them. We’ll be publishing a full application bulletin about our investigation in due course; keep an eye on the list of our Application Bulletins – UPDATE: It’s here! AB-016: Experiments in Waterproofing / Overmolding Vibration Motors.
In the meantime, to summarise, we’ve used the following motors with mixed results:
- Encapsulated vibrating motor types – already marked as ‘water resistant’
- Coin vibration motor types – not water resistant at all
After covering the leads (and holes in the coin motors) of 10 of each motor type in potting compound/resin we found that if the motor worked after being covered, then it worked when placed in water. Some of the coin motors failed to start after the compound was applied due to ingression of the potting compound into the motor mechanism. This was most common in the 312-101 (>50% success rate), then the 310-103 (~70% success rate), and the 308-100.
However, the 307-100 (since replaced with the 307-103) and 306-108 (since replaced with the 306-117) encapsulated motors were all 100% successful in waterproofing when the potting compound was applied.
Actually, the 306-108’s tested worked in water without the compound, but we tested it for completeness. Note, however, that the 306-108 is not IP rated, and is sold as ‘water resistant’. Therefore to be sure, a waterproofing process needs to be completed, if waterproofing is required.
It would also be possible to waterproof some motors, e.g. the encapsulated motors, with over-moulding low-pressure plastic moulds (e.g. silicon).
Mounting Suggestions
Sewing Motors Directly Into Material
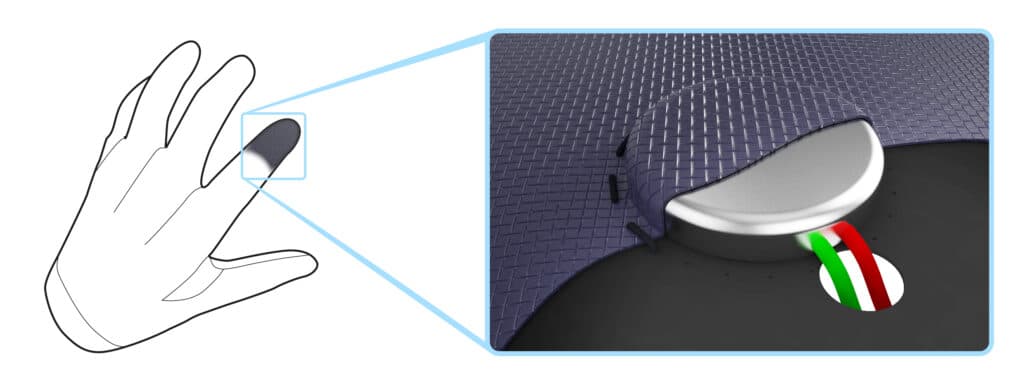
If you know your way around a needle and thread, it is possible to stitch the motors directly into the fabric. This allows for exact placement and is a cheap and simple approach when prototyping. The strength of vibration may be reduced unless the stitching can hold the motor exactly in place, in which case the full vibration effect may not be transferred through the material to the user.
This is a semi-permanent to a permanent method of securing the vibration motor, depending on the quality of stitching. Of course, in a production scenario, it would make more sense to use machines to produce pre-stitched pockets which the motor is then manually secured in.
Injection Moulded Housings
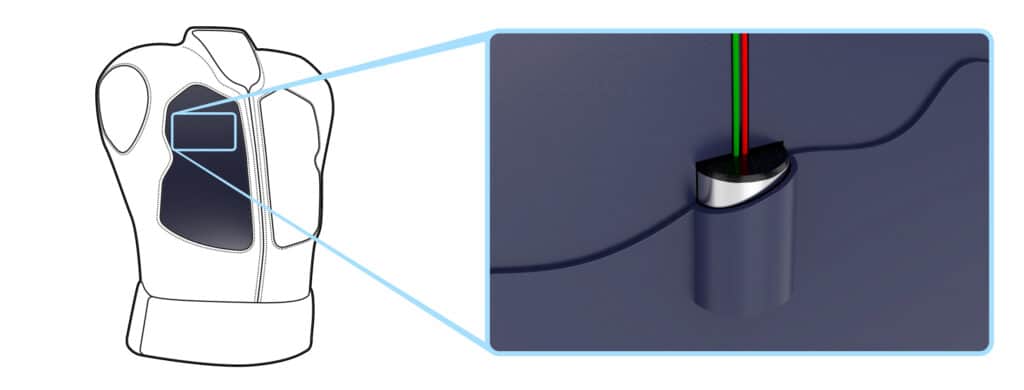
Probably the most complex solution is to use specially moulded housing to secure the motor and then affix the mould to the material. It may be that the material can have the injection moulding designed into it, or it could be used in conjunction with stitching or adhesive methods.
The housing benefits from being a rigid body around the motor, allowing you to use motors with external moving parts if desired. In addition, the transfer of vibrations could be made more efficient because the whole injection moulded part will vibrate, not just the motor. It may also be possible to design motor injection moulded housing where the vibrating motor can be easily removed if required (e.g. for replacement in long-life applications).
This could, however, limit the placement of the haptic alert. For example, if the design was to be worn by a human, the housing might be fine in areas like the chest or back where little flexibility was required. However if bulky it would be uncomfortable around the joints and may impede the user.
Foam Housing
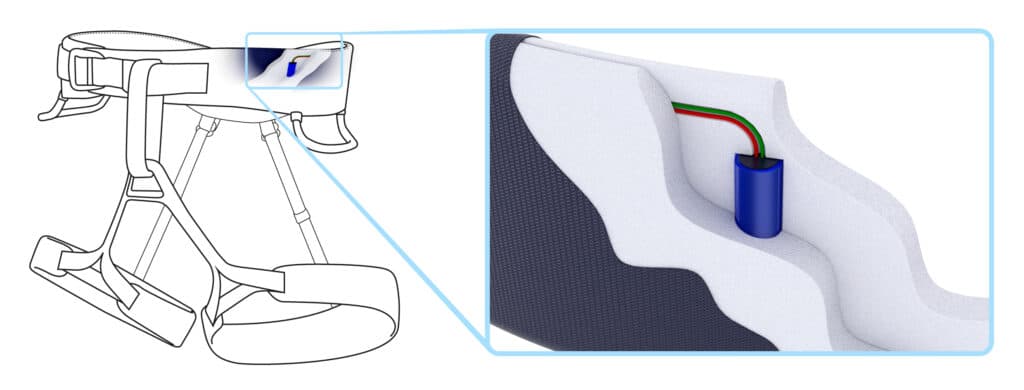
Foam housing for the motor would act as a half-way house between sewing the motor directly into the material and producing an injection moulded house. It would encase the motor in a more rigid body than the material itself, improving the vibration performance, but would also be more flexible than the injection moulded housing. Foams are available in a wide range of rigidities and thicknesses for use in a variety of applications. The thicker and softer the foam, the more vibrations it will absorb, but this may be required for user comfort.
Adhesives
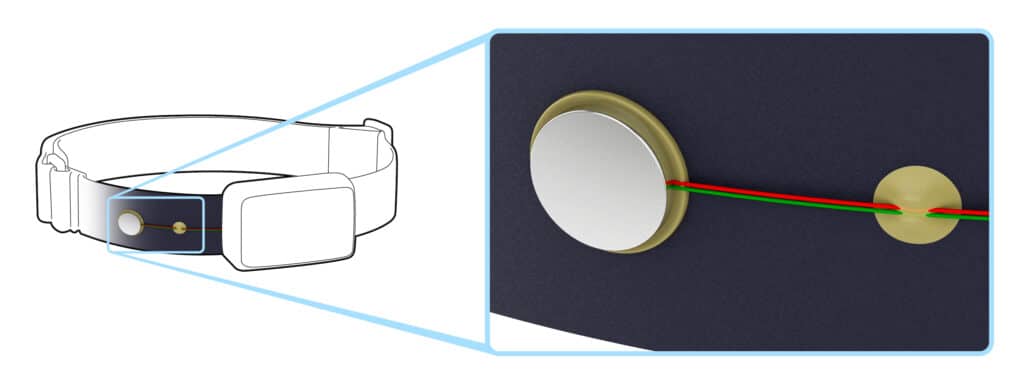
Due to its simplicity, this is a popular method for prototypes and experimenters. Also, suitable adhesives are widely available and generally inexpensive. This method supports leaded motors and motors with terminals, both allow for flexible mounting options.
Attention must be taken to ensure that the adhesive is strong enough to secure the motor. The strength of the adhesive can be easily improved with careful application to clean surfaces. Flexible adhesives like rubber-based glues would likely need to be used.
Our coin vibrating motors and LRAs have adhesive pads making them very easy to mount. However these pads are designed to be attached to solid surfaces like PCB’s, and therefore the pads won’t likely attach so well to fabrics.
An adhesive may be used on its own or in conjunction with other methods above, such as foam housing, for added security. Seams of thicker neoprene-type materials are often glued and stitched together, and it may be possible to include a foam or injection moulded housing between the seams.
Conclusion
The field of wearable haptic feedback or vibration alerting clothing has many applications, including safety, rehabilitation, and performance-enhancing. As it is a relatively unexplored field, adding these features to existing or new products can dramatically increase differentiation from competing designs.
We offered some examples of wearable applications and noted that mounting a vibration motor to a flexible material can be seen as an obstacle to implementation. However, these obstacles can be overcome with careful motor selection and following our design hints.
It may be possible to suitably mount a vibration motor for haptic feedback or vibration alerting using one/some of the following methods:
- Sewn directly into the material
- Injection moulded housing
- Foam housing
- Adhesives
The above methods are suggestions for consideration, however, there may be other appropriate techniques that have not been discussed. If you have any suggestions, please feel free to pen us an email.
If it is desirable for the motor to be waterproof, i.e. in the instance the clothes need to be washed, this may be achieved most effectively using encapsulated vibration motors and a high viscosity potting compound to seal any gaps in the enclosure. Of course, the drive circuitry and power source would also need to be waterproofed.
Newsletter
Sign up to receive new blogs, case studies and resources – directly to your inbox.

Sign up
Discover more
Resources and guides
Discover our product application notes, design guides, news and case studies.
Case studies
Explore our collection of case studies, examples of our products in a range of applications.
Precision Microdrives
Whether you need a motor component, or a fully validated and tested complex mechanism – we’re here to help. Find out more about our company.