10. Textile Scaffold¶
RESEARCH & IDEATION¶
KOFTA
This independent couture studio works with leather molding and different other technologies techniques,and they have a whole collection of leather molding pieces with body parts shapes designs, which I find very inspiring for this week's project!
CREDITS
NERI OXMAN
As an architect I couldn't not mention Neri Oxman's SilK Pavillion, this is the second version of it, it's so amazing how nature and humancraft can collaborate in a symbiosis to make such a beautiful creation!
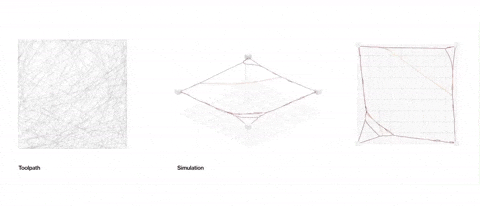
CRYSTALVERSE
In this website which was mentioned in the lecture you can find all the information everyone could possibly need to start making their own crystals, I couldn't explore it that much as I focused more on CNC Milling, but I'll definiteley check their website and make a few experiments with crystals in the future.
REFERENCES & INSPIRATIONS¶
BATOUL-RASHDAN & STEPHANIE JOHNSON
I admire so much the work that Batoul (left) did for her final project, I find it so mesmerizing, her crystals and how she turns them into a whole fashion piece is so beautiful to me. Also, Stephanie's work and documentation on CNC Milling was indredibly useful! And her results are very good!!!
CREDITS BATOUL CREDITS STEPHANIE JOHNSON
SCHIAPARELLI
The first two things that came to my mind when we were told we were going to make a mould for leather, were corset and Bella's Hadid Schiaparelli dress, jajaja I have no idea why, but the last one was definetely my inspiration!
I also wanted to make a necklace, so the whole idea begins with putting those two things together and finding a middle ground (corset and necklace) which following Schiaparelli's dress lead me to make a bustier!
TOOLS¶
PROCESS¶
SO LET'S BEGIN!
My first step was to make the bustier shape based on a human 3D model!
Here in the slides you can see step by step:
Then, I wanted to learn more about Grasshopper, so I challenged myself to make all geometry in Grasshopper so it was all parametrized!
You can right click on the image and open it in a new tab to see it clearly or just download the Grasshopper Scrip!
Here 2 you can find the full Grasshopper Script
In this video I show step by step my whole Grasshopper Script and where you can find each geometry:
'''
Then when the attractor geometry was ready it was time to transfer it to the bustier, but I faced a small problem and didn't have much time so I decided to finish my geometry in Rhino turning the bustier shape into a surface using Drape Command and then Flowing my attractor geometry along the bustier shape:
HEREYOU CAN FIND ALL THE INFORMATION YOU NEED TO USE THE COMMAND DRAPE SURFACE OVER OBJECTS PROPERLY
RESULTS!!!¶
RHINOCAM SETTING & SIMULATION¶
After that I was ready to do the setting for RhinoCAM to use the CNC Milling machine, here you can see all of them in my file:
SIMULATION!!!
CNC MILLING¶
I was very excited from the beginning to learn about this!!! So I really enjoyed it and I'm very thankful for the lab support and guidance using the machine
ROUGHING
This is the first thing that the machine does and the one that takes more time, and it is to create layer by layer tha shape
FINISHING
After, he smooths the layers giving this ncie finish that you can see in the video:
"IMPORTANT: The CNC milling machine is an XYZ (three-axis) machine, so this must be considered when designing. The machine cannot cut hidden faces, as this would require a fourth axis."
RESULTS!!!¶
Here 1 you can find the file with the settings
TIP!!
YOUR RHINOCAM SETTINGS ARE WITHIN YOUR FILE SO YOU JUST NEED TO COPY AND PASTE YOUR GEOMETRY IN MY FILE TO HAVE MY SETTINGS, YOU DON'T NEED TO PUT THE VALUES MANUALLY
Here 3 you can find the file I used for CNC milling
LEATHER MOULDING¶
- First, we have to prepare the leather for moulding, so this is what we'll need:
TOOLS¶
- Pots
- Stove
- Spoon
- Baking Soda
- Water
===> RECIPE
* Soak the leather in cold water for at least 2 hours
* Heat water (No more than 80°C)
because the leather can shrink
* Put 5 spoons of baking soda
* Mix well
* Remove excess of cold water and put the leather in
the warm water with baking soda
* Leave the leather there for 7 minutes
* Take it out and remove excess water
* Massage and stretch
* Put the leather in the mould
FIRST, AND MOST IMPORTANT BE CAREFUL :)
It's so funny to me that everytime I go to the lab accidentally I get a new fashion piece jaja, I always spill something on my clothes so my advice is to be careful, wear gloves and always check if what you're working with releases ink as it happened to me with the leather:
MOULDING
Then after putting the leather in the molding and pressing very hard I used this clamps so it would be very tight
RESULTS!!!¶
INGREDIENTS & RECIPES CRYSTALS¶
Now it's time to make some crystals! Here you can find the three recipes we did with our local instructor when she was teaching us how to make them, but as I mentioned in the research there are a lot of possibilities!
For me is so crazy that a so simple chemical reaction can create such beautiful results!
TOOLS¶
- Pots
- Stove
- Spoons
- Scale
- Borax
- Alum
- Water
===> RECIPE
* Measure your borax/alum powder
(proportions in recipes image above)
* Heat water
* Sterilize with alcohol the pot where the mix goes
* Pour the warm water
* Add borax/alum following the proportions
* If the powder dissolves very easily, add more
* Add the piece you want to crystalize
* Leave in a dark place for 24h or more
I must also thank my classmate Aleks beacuse she helped to make them while I was struggking with leather and crstals at the same time in the lab
COMPARISON BETWEEN MATERIALS¶
MAN-MADE VS ORGANIC¶
Material pic | Material name | Source | Powder | Time |
---|---|---|---|---|
![]() |
PLA | Man-made | Borax powder | < 48h |
![]() |
Flower | Organic | Borax powder | < 48h |
RESULTS!!!¶
CONCLUSIONS¶
The crystals adhered better to the flower bracelet. On the other hand, while they worked well with PLA, they performed best with a rough design that allowed them to stick and adhere more effectively.
FILES¶
-
File: RHINO FILE ↩
-
File: GRASSHOPPER FILE ↩