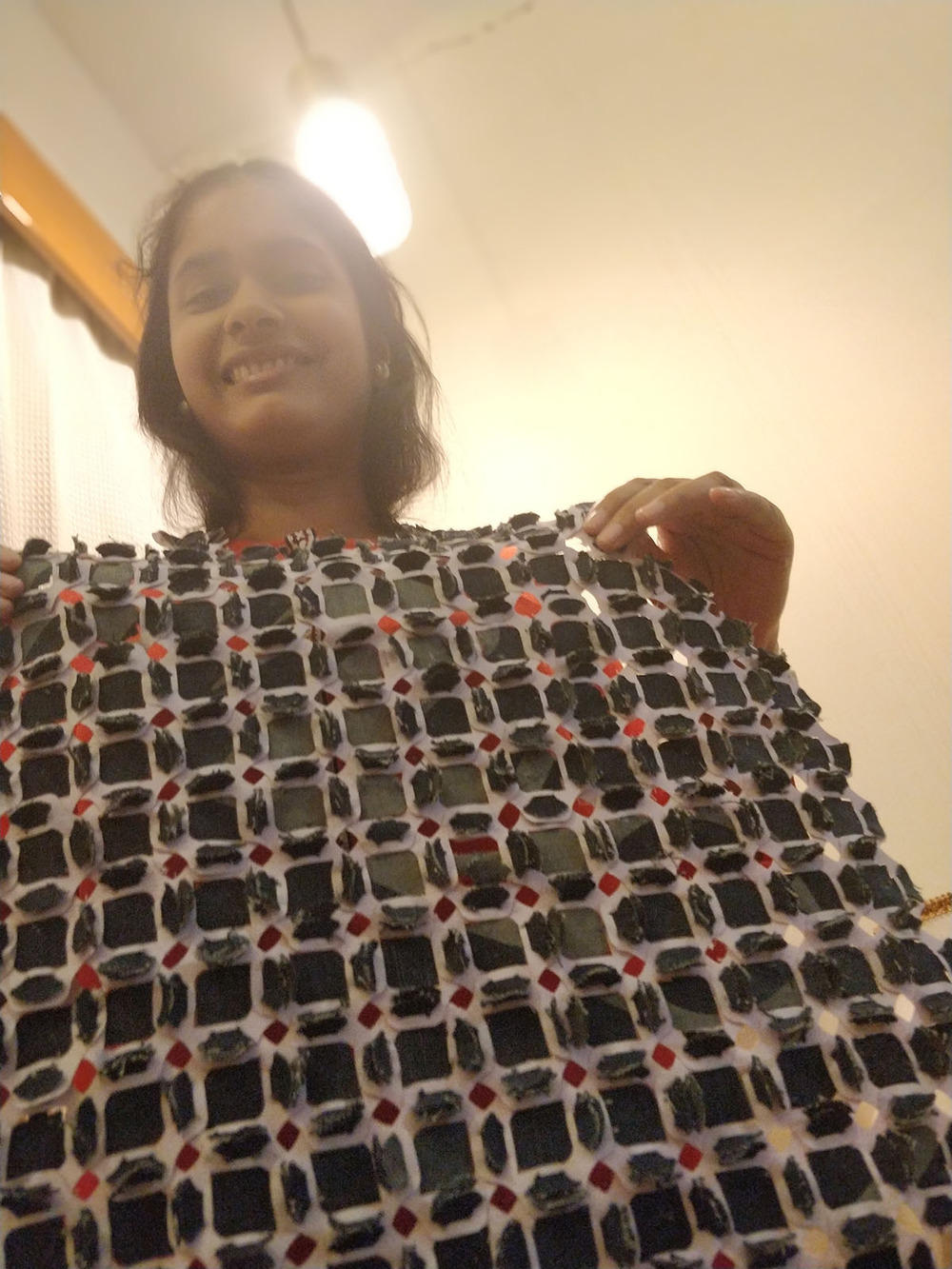
Our current fashion system is built on the traditional linear system of “take, make, and dispose of”. In this system we are using up our planet’s resources with increasing speed, and selling them to our customers as disposable commodities. At a time where over-consumption is already putting a huge strain on our environment, can we still accept a wasteful business model like this? It`s high time we took a closer look at a new concept for our times: the circular economy. This week explored about Circular fashion just like circular economy, a recent term in fashion. This week was about designing a modern reconfigurable seamless garment. It started from understanding designing a garment to observing seamless joints and holds.
"This week helps manipulate materials and achieve designs without stitching."
Nishtha Kaushik
Steps
Step 1: Understanding Circuar Fashion System
Circular fashion covers multiple aspects but which is very common in india is reusing the old clothes for making different products or to use the cut pieces and threads for making all new piece. This has been a very common practice in rural India and is now a type of fashion in urban india. having high number of population everything we buy put into a circle which goes from manufacturing to using to reuse to discard and reuse. Therefore, this week made me familiar about other aspects of circular fashion as follow. If fashion refers to a piece of garment, an accessory, or a pair of shoes, circular fashion can be defined as any fashion item that is:
-Designed so that its sub-components can be disassembled or separated to facilitate repair, remake, reuse and eventually material recycling at its end of use;
-Designed with high quality materials and in timeless style to maximize its durability, longevity and attractiveness to many users (if passed on to new users);
-Designed on demand (custom-made) in order to be more optimally designed for its specific user in terms of fabric/material, style and fit, thus increasing its perceived value and likely lifespan;
-Produced with non-toxic, high quality and preferably biodegradable materials, so that its material(s) may be safely biodegraded and composted at the end of use; or produced with non-toxic synthetic materials that may be effectively recycled (such as recyclable polyester);
-Produced in such a way that all waste generation is minimized during production, and all potential spill material and rest products can be reclaimed and reused as raw material for other processes, thus minimizing the extraction of new virgin material;
-Produced, transported and marketed using renewable energy, such as wind or solar power, wherever possible, and using water and other raw materials effectively and safely throughout production and distribution;
-Can be used by multiple users throughout its life time through swapping, borrowing, rental, redesign, or second hand services, thus extending its user life; and
-Can be safely and effectively reclaimed and recycled, whereby its components are utilized as raw material for manufacturing of new products, or are biodegraded and turned into biological nutrients for microorganisms in the soil. Below is an interesting video which eventually would like to run in my own lab too.
Open Fit Lab: a very interesting concept from Kyle McDonald on Vimeo.
Step 2: Concept development
After an amazing lecture, I went through articles and practices under this and eventually i started designing few joints on paper first. I didnt know what piece to make but while thinking of ideas i realised how so many things are made with simple joints without stitching like above and finally started designing what i felt was something i havent seen around yet..Material selected was OLD jean and BUKRAM (Buckram is a stiff cloth, made of cotton)
Different designs i thought initially,dont judge my sketches, i made this in a moving car and selected two of these:One is this below: In this i actually made interacting and intersecting ducks and it came out like a flower after laser cutting trials, was beautiful, very indian and organic but I preffered making one whole apparel so preferred one which will hold better.
The above image was also a beautiful concept of having ducks hold each other together and it became a flower but then i designed something better in Auto CAD.
I picked one of the design i made and started making on Auto CAD.
My first prototype by cutting paper and trying joints.
Itookthefile to RD works for cutting my first sample, with the following settings where I am using Cotton Fabric and jean fabric and cutting it on our small laser cutter,Speed is 200 and Power is 15.
Assembling my first iteration. Looks perfect to go ahead.. hold on I just thought something crazy I want to etch my company mascot on the whole piece.
Continuing making more of these..
Step 3: Compiling my Pieces
Using Auto Cad,I compiled all my pieces together and i wated to try engraving zios logo so i spread zios logo over it and manually trimmed it from outside each box.. took about 20 mins or so to do so but worth the effort.
Confirmng their locking for all pieces
Step 4: Laser cutting settings
Ready to laser engrave and cut with right Power and Speed below.I went about selecting two actions on the software, first was engraving and second was cutting. After engravng, few pieces tore off while picking up from the laser bed as jean was already old ,besides that engraving was basically burningof toplayer making it weak plus the jean already had laser marking designs, so i recut pieces on those parts of jean which were plain and it came out well. Etching effect on jean stays afterwash but in case of cotton etching washes away and piece becomes softer.
Selecting Cutting and etching profiles for the pieces. Power 80 and Speed 25 for cutting Cotton.
Setting for Etching profile.
On our small lase cutter we have sensor, that it doesnt start cutting until door is open so its automatically safe but we have tomake sure we have our Exhaust fan on of that particular machine. In image below, its etching right now. Here, i had to check if I am not using the weak or already etched part of the jean.
Fially cutting cotton, i cut the large piece equal to bed size and placed it with help of magnets and here it goes.
Step 5: Moment of "JOY"
Pictures explains :)
Collecting pieces..SUBMITTED THE BIG SIZE SWATCH OF MY DESIGN ON THE LAB.Front side of my "APPAREL"
Back side of my "APPAREL"
My side of HAPPINESS :)
Published on Oscircular Fashion Platform