11. Implications and applications¶
This week I worked on formalizing my final project idea. I also visited 3DS Fablab and met their R&D team to talk about project ideas.
- Document the concept, sketches, references also to artistic and scientific publications
- Create an Ultra-personalised product service systems (UPPSS) for your final project
- Map the potential stakeholders
- Explore personalisation at all the different levels
- EXTRA POINT : Interview your potential users/ target group about your concept, quantify results
When traces become information
My final projet is an art installation and performance which is about digital traces and that questions how
individuals can become a self in the age of ubiquitous mediality of technology. This performance is displaying in live a process of digital fabrication where the inputs are the traces left by the performer's body in a biosensing material,
and the output is a 3D printed sculpture that reproduces the anthromorphic shape of the performer.
Inspiration¶
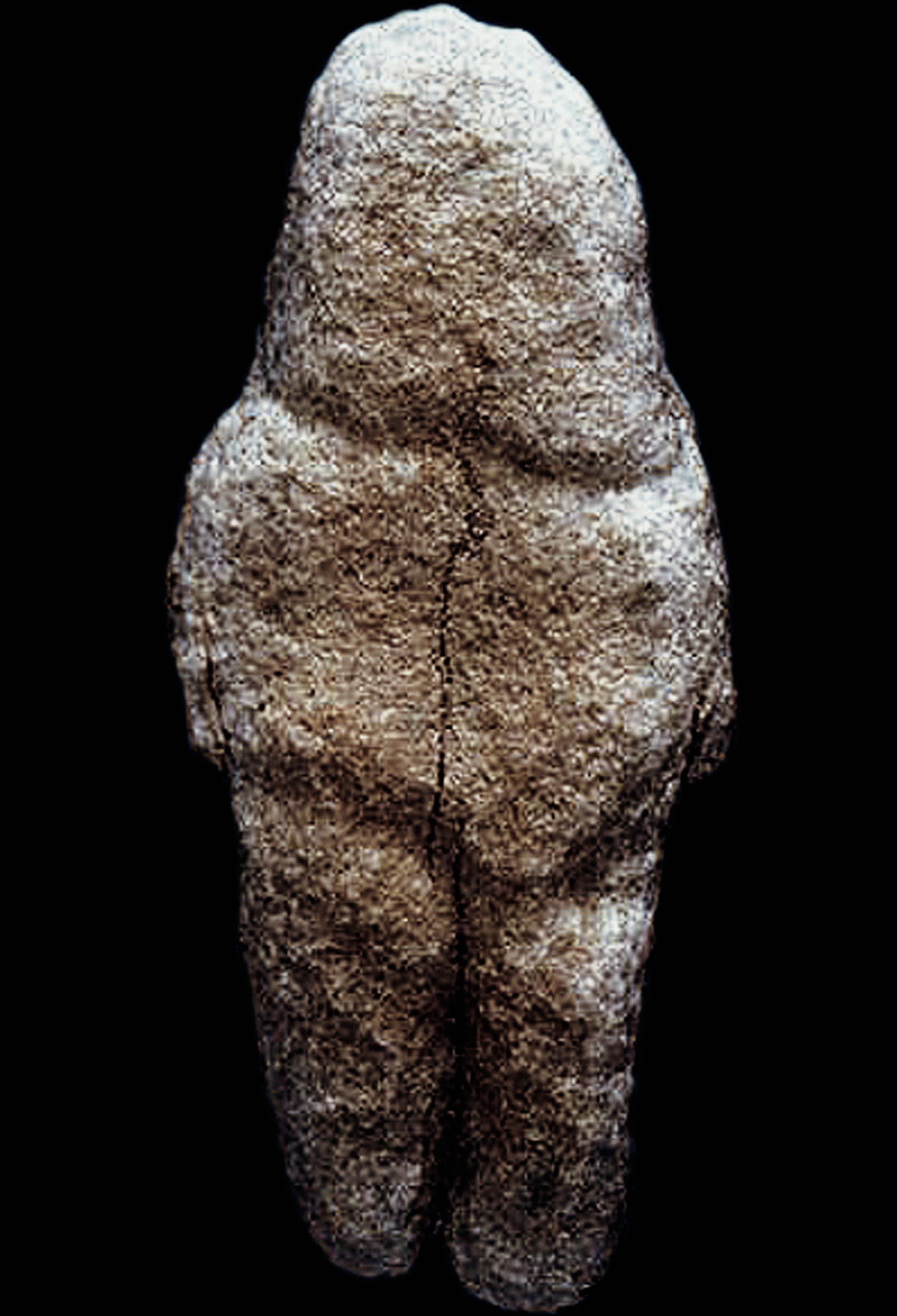
Sculpture representing Venus of Tan-Tan. Earliest representations of the human form (Acheulian 500,000-300,000 years old)
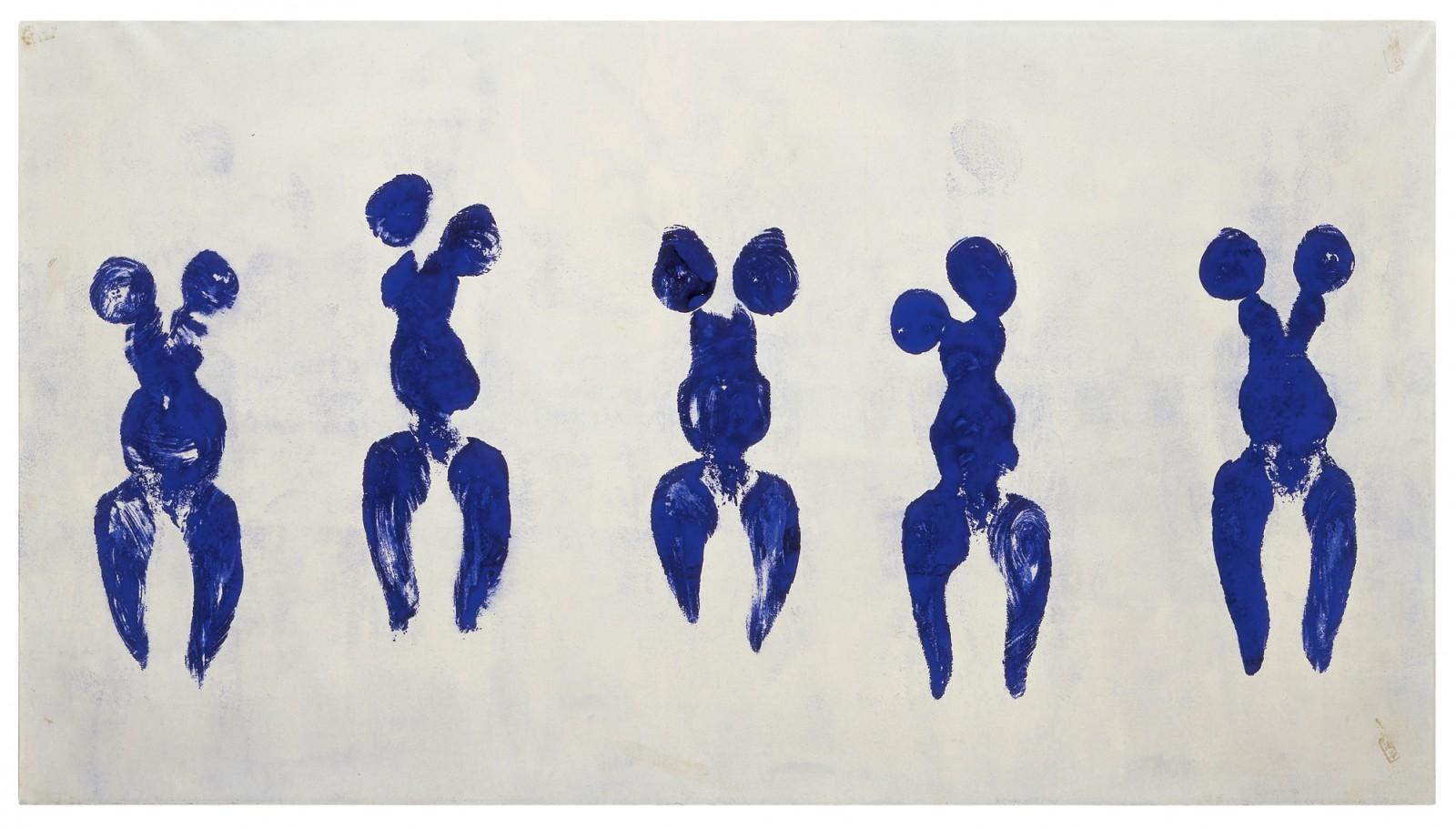
Yves Klein. Anthropométries de l'Epoque Bleue. 1960.
/https%3A%2F%2Fdev.lareviewofbooks.org%2Fwp-content%2Fuploads%2F2017%2F04%2F05_WOMB_TOMB.jpg)
Mariechen Danz. Womb Tomb. 2015.

Dress, No. 13, spring/summer 1999. Alexander McQueen.
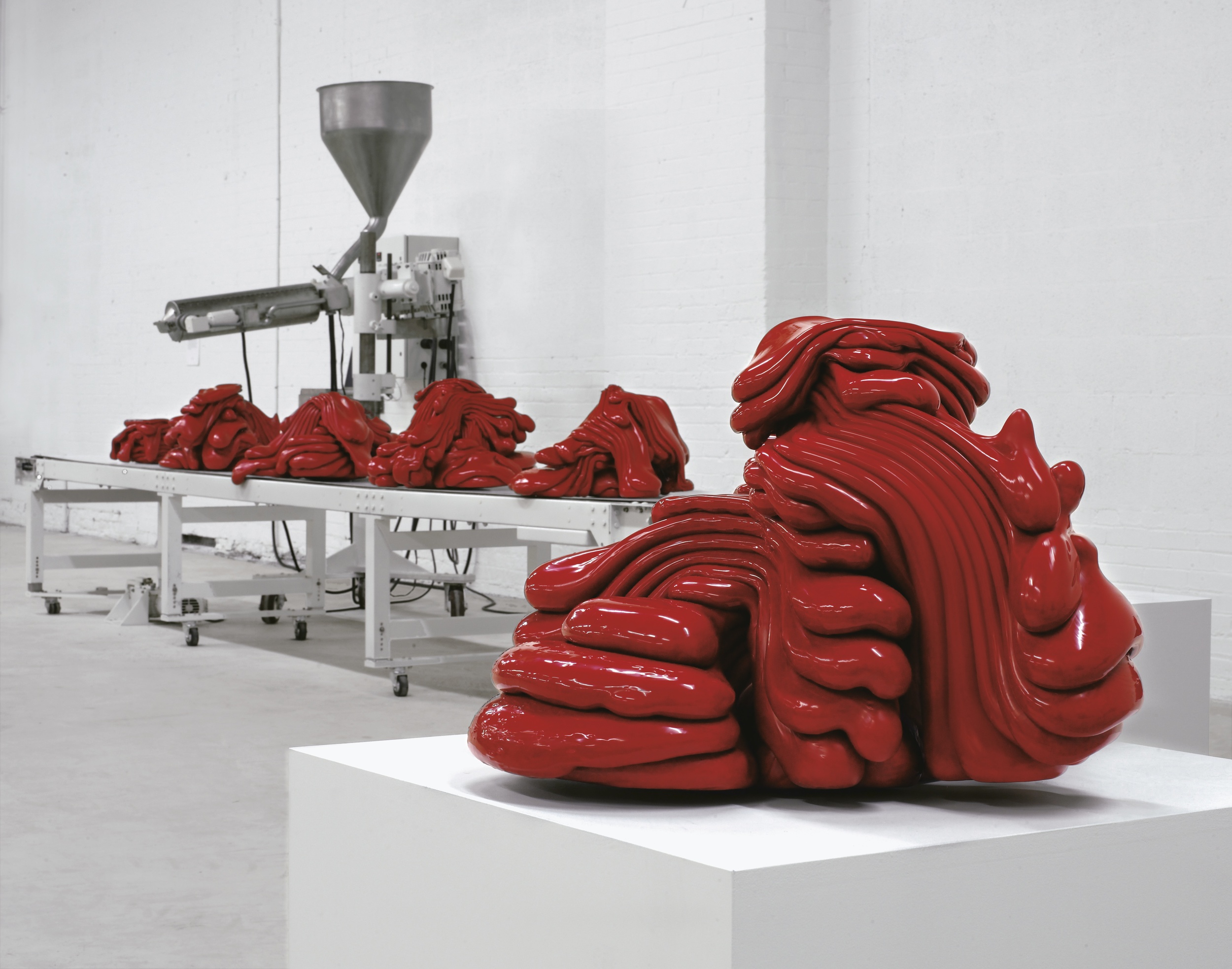
Roxy Paine's SCUMAK
Concept¶
When traces become information is an art installation and performance that reinterprets the structure of the triptych in the digital era. It depicts the echography of the individual who is nascent in and by technology, in the sense of Gilbert Simondon. The installation is divided into three frames, the phases of the performance, separated from the public by a transparent glass-like plate, which serves as the screen of the performance and defines the space for the audience.
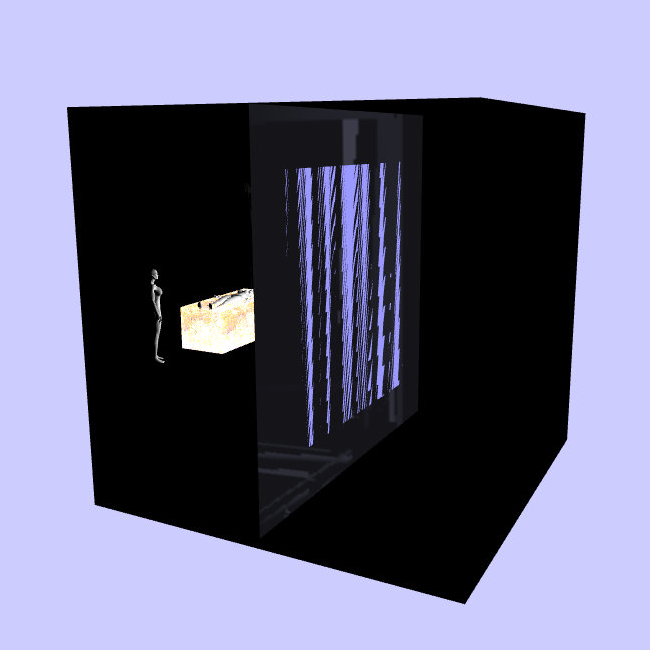
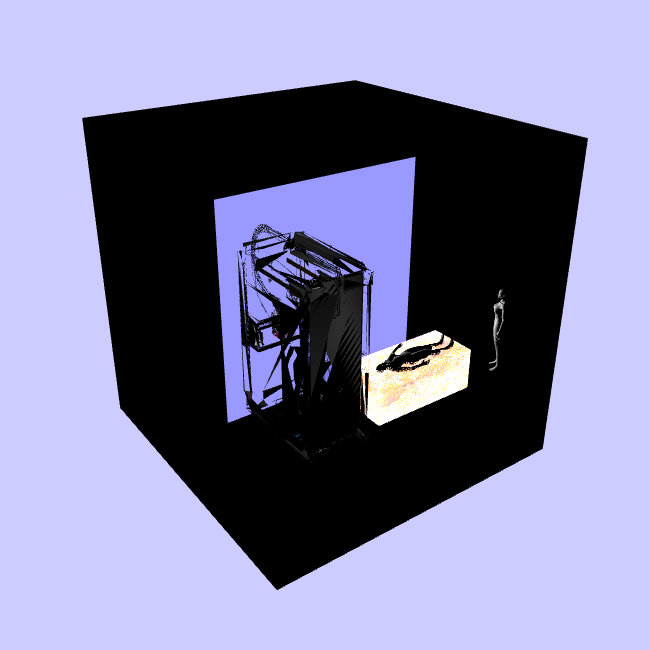
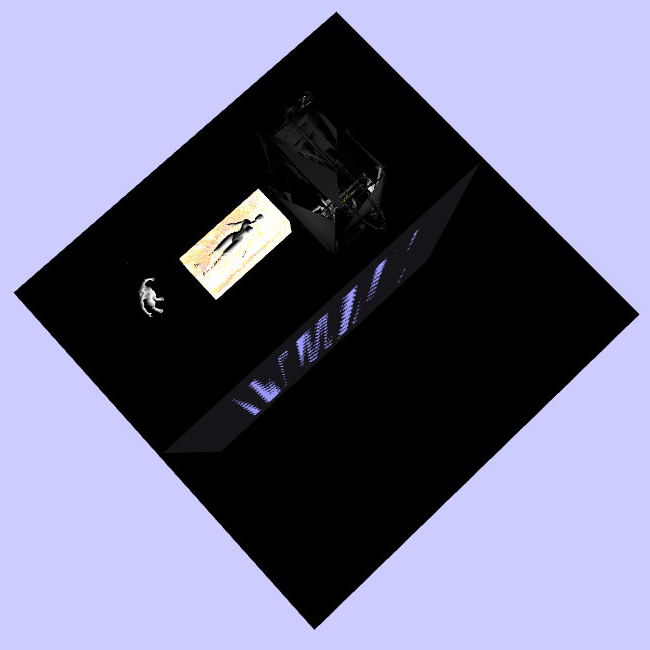
A genuinely organic installation crafted to host a human body, this work is an incarnation of how humankind continues to externalize itself through technê, relying on technique not only as a collection of tools, but also as an epiphylogenetic memory [Stiegler]. It is an attempt at initiating a dialogue between the virtual and the material, the telepresence and the corporeality, questioning how individuals can build up their self in the age of ubiquitous mediality of technology.
Phase I (Wünderblock)¶
The performer enters a human-sized mold made up of malleable material filled with sensors
that help building a complex, skin-moisture landscape of the body. The autopoietic machine takes the physiological (and psychological) data of the performer as inputs and then translates it into a generative shape which defines the self by the synesthetic syntax of the digital traces. This memory apparatus sets up an instrumented way of producing traces that are digitized.
Phase II (Replica)¶
From the gathered digital traces a three-dimensional model of the real size individual is formed to be replicated throughout the performance in industrial quantities. To that end, a robotic arm is taking part in the performance, condemned to make the same movement, over and over again in the spirit of the spirit of a modern Sisyphus.
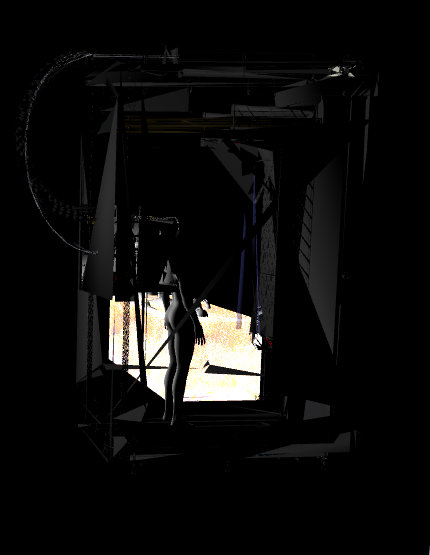
This part aims to represent the accumulation of things, the artifacts, the melancholic repetition of single machines, as well as the obsolescence of Man who became an antiquity.
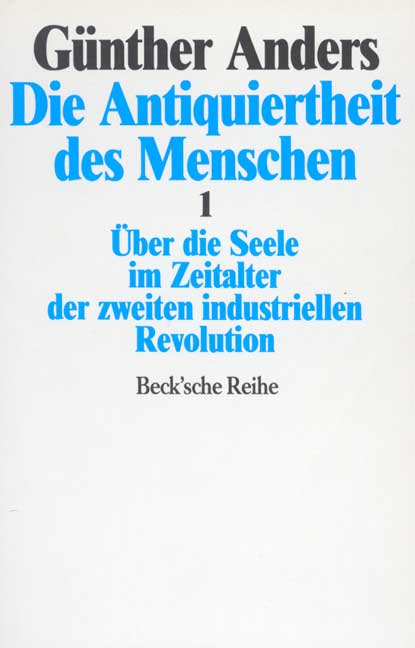
Through the performance, the end object is not the goal of the manufacturing process : it could be destroyed during of after the performance. But rather, what matters is the production for production's sake.
Phase III (Meme)¶
As these digital traces further ooze away to the internet in an uncontrollable way (as NFTs, in the Metaverse, on a dedicated website), they grow a rhizome-like information structure, eventually coming back decades later to us through our descendants.
Material Experience¶
❝Materials are experienced at four experiential levels:
sensorial, interpretive, affective and performative❝
from Giaccardi, Elisa & Karana, Elvin. (2015). Foundations of Materials Experience: An Approach for HCI. Proceedings of the 33Rd SIGCHI Conference on Human Factors in Computing Systems.
I found interesting the typology of Material Experience developed by Giaccardi, Elisa & Karana, Elvin. (2015). As a result, I tried to define precisely the material experience I want to create in the installation "Wünderblock", according to their typology.
On the sensorial level, the biomaterial is slightly resistive, soft, flesh-like, organic, and acts as a memory alloy.
Regarding interpretation, I want it to look like a biotech artifact, a body prothesis. On the one hand, the translucence of the flesh-like material creates a organic, warm and intimate atmosphere.
On the other hand, the electronic components give a sci-fi appearence to the device.
On the affective level, the resemblance of the artifact to a human-size mold, evokes a sense of embodiement, thus facilitating a feeling of connectedness, fusion with the material.
Finally, the malleable clay-like texture of the material reveals its affordances. It entices people into performing different action with it : touch, press, lay down, etc.

Ittah Yoda, No History of Its Own, 2021, Mixed media, Soap, Beeswax, natural pigment.

Kombucha Skin, from Fabtextiles.org
The material for the main installation could be either grown (kombucha) or made with glycerol-based transparent soap. Different test has to be done to see which material better suit the sensing and aesthetical purpose.
Ultra-personalised product service systems¶
Since my performance is displaying a manufacturing process, I decided to formalize this process into the different stages of Ultra-personalised product service systems.
❝Between the ‘Co-’ phases are enabling transitions of encode, materialise, profile, and monitor.
Encode enables Co-Analysis to become
Co-Design by making the data compatible with the parameters needed to generate.
Materialise enables Co-Design to become Co-Manufacturing by making the data ready
for digital manufacturing processes (which may be distributed). Profiling enables Co-Manufacturing to become Co-Use by remembering the data from all previous phases for
later comparison and predicting the lifecycle of the object. Monitor enables Co-Use to
become Co-Analysis by taking the data from the object (and use) and making it available
for analysis❝
from Troy Nachtigall, Svetlana Mironcika, Oscar Tomico & Loe Feijs (2020)
Designing ultra-personalized product service systems, CoDesign, 16:4, 274-292, DOI:
10.1080/15710882.2020.1842454
Co-Analyze¶
The product Wünderblock is an intelligent sensing biomaterial, which is aimed to collect data from the performer. It is litteraly a transcoding matrix. Precisely, the service that it provides is to build in real-time a skin-moisture landscape of the body, from various biometrics (pressure, humidity, temperature). At the system level, it allows to compare through time the dynamic micro changes of the performer's body.
Co-Design¶
The most complex part of this project is the mapping of the data to a sensible 3D shape that is meaningful, anthropomorphic (pebble-like), rather than arbitrary. It is required to generate a shape that is parametrized by the data gathered from the matrix. The Co-Design is a negociating process where the algorithm tunes the parameters of the performer to the design considerations of the object being made. The feedback loop between performer and the object is actualized in real time so that the performer become the maestro and co-create with the algorithm.
Co-Manufacture¶
The challenge of this work is indeed the real time dimension of the manufacturing process. That is why the chosen technology to replicate the 3D model has to be relatively quick, or the slowness of the machine has to be integrated in the performance. A real time data flow between the sensing matrix and the CNC machine has to me automatized. In technical terms, several solutions are possible :
- 3D print the model at very tiny scale
- Instead 3D printing a 3D model multiple time, printing a sculpture layer by layer during the performance
- Using a soft robotics system that change the shape of an humanoïd sculpture, according to the performer's movements
Knotty. 2017. Pawel Lasota and Magda Mojsiejuk
at Industrial Design, School of Form. Poznan, Poland
Co-Use¶
The first prototype of the sensing matrix will be presented as an interactive device during the seminar PHITECO at the University of Technology of Compiègne. In this case it will be usable not in the context of a performance but rather as an experiment with users.
Fabricademy modules¶
This project involves knowledge acquired during several modules of Fabricademy: Digital body, Textile as Scaffold, Biomaterials, E-textile, Skin electronics.
I conceived this concept of artwork as modular, i.e. independent modules. Within the time of Fabricademy, I would like to work on the biomaterial one (Wünderblock) and the 3D printed one (Replica).
In the long term, I would like to create a full scenography for this artwork, with the "screen", musical composition and several interactions with the space of the exhibition, through a smart-house-like technology.
Stakeholders¶
First and foremost, my final project is a performance-installation, which means its "end users" are both the performer and the spectators. On the other hand, it is displaying a manufacturing process in real time, thus it challenges the frontier between Art and Industry, questioning production scale, means of production ownership, product lifetime, mass production and
customisation.
Since I was granted a scholarship from Dassault Systèmes Solidworks, I have the chance to benefit from 3DS Experience Lab's ressources. As a consequence, I will take this opportunity to use their software for the CAD/CAM part of my work. Moreover, I could potentially get their support in setting up a robotic arm 3D printing solution.
Interview with Dassault¶
The second meeting with Dassault was very fruitful. They expressed interest in my idea for the industry of telepresence, as well as the digital fabrication of molds on the fly. It resulted in 3 hypotheses of technical solution for the replication of the 3D shape in quasi real time :
1. Actuator behind fabric![]() inForm by Tangible Media Group |
2. Projection of powder/material that dry quickly on a structure![]() Hendrik Menné, 114L |
3. Water jet that freeze![]() Ana Mendieta, Silueta |
Regarding (1.) a member of the team suggested that Dassault could initiate a partnership with Festo to make actuators.
Roadmap¶
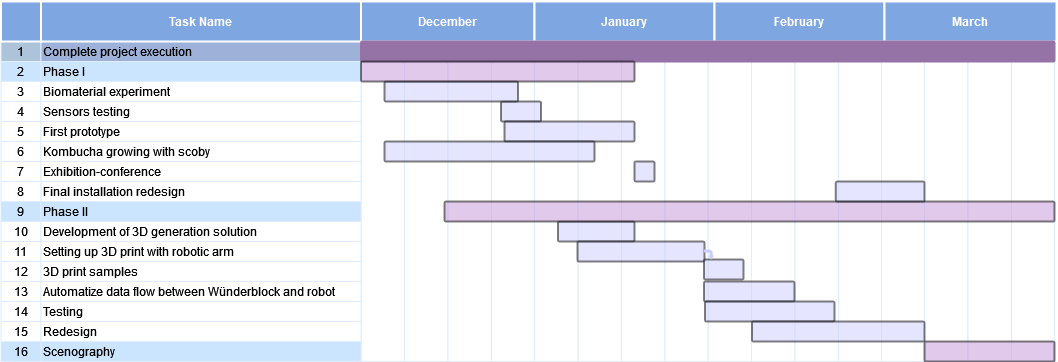
First Tests¶
Glycerol based soap![]() | 16x16 pressure sensor matrix with multiplexer![]() |
References¶
Troy Nachtigall, Svetlana Mironcika, Oscar Tomico & Loe Feijs (2020) Designing ultra-personalized product service systems, CoDesign, 16:4, 274-292, DOI: 10.1080/15710882.2020.1842454
Giaccardi, Elisa & Karana, Elvin. (2015). Foundations of Materials Experience: An Approach for HCI. Proceedings of the 33Rd SIGCHI Conference on Human Factors in Computing Systems.
Karana, E., Hekkert, P., Kandachar, P. 2008. Materials experience: descriptive categories in material appraisal. Proc. International Conference Tools and Methods in Competitive Engineering, 399-412
B. Stiegler, La technique et le temps. 2018. Fayard.
G. Anders, Die Antiquiertheit Des Menschen. 1956. C.H. Beck
G. Simondon, L'individuation à la lumière des notions de forme et d'information. 2005. J.Millon.