UNFLATABLES
Exploration of inflatables as visual and haptic actuators
Unflatables is a research project exploring the potential uses of soft robotics in wearables and e-textiles. It covers three different processes used to produce the actuators and investigates the design methods for predefined three-dimensional deformation, which may be used for both visual and haptic feedback
Soft robotics
Soft robotics is a novel kind of robotics that is based on soft, flexible materials rather than rigid joints used in most mechanical designs. The softness of the robot bodies gives it unique features and allows affordances that differ from the traditional/hard robotic approach. Some of them include more safety, when closely interacting with other soft bodies, especially evident with human and animal tissues, prone to injury and damage, when applied too much pressure on.
Currently, soft robots are being adapted and developed for medical and bioengineering uses as internal and external actuators. Made of bio-compatible materials such as silicones and synthetics, they are safer to use than hard mechanical parts consisting of various kinds of metals. The full potential of pneumatically operated robots is being investigated in various fields. They are in focus of scientists, engineers, but also gaining popularity among fashion designers, artists, hobbyists and makers, due to their shape-changing nature and transition potential.
Key problems in the pneumatic actuators current research:
- Visual and haptic feedback
- Engaging the sense of touch in novel ways
- Paradigms of tangibility and embodiment in tangible user interfaces
- Affordances of body proximity and directness in wearables
Haptic feedback as an under-explored field in HCI, exploring the potential of our skin as a connector between the inner and outer world The first, the most detailed and prominent study that introduced and explored the heat-sealed thermoplastic inflatables is aeroMorph. The research includes software that calculates and simulates the deformation based on the geometry and morphology of the design. Explores only the visual outcome of inflation and shape-changing, leaves the potential sensations out. Details the mentioned fabrication process with necessary parameters, includes also various materials the authors experimented with. Presents guidelines on design for achieving certain movement from the actuators.
Most of the projects developed in the realm of soft robotics are based primarily on just one sensation at a time. The most explored sensory feedback sources are temperature (hot and cold shifts), simple pressure and vibration. They are usually changing in certain, predefined patterns, recognizable to the user, providing feedback in the human-computer- interaction loop. They, however, seem to be unintuitive and require the user to understand and learn how the system works in order to fully enjoy its potential.
There are no comparative studies of various fabrication methods that would include both the sealing of thermoplastics and casting of solidifying liquids . There is usually focus on one method when research is about fabrication or other aspects. Most of the exploration of soft robotics uses only silicone casting technique or other polymer-based casting materials.
Being a part of Fabricademy course, which is based primarily on material and technological explorations, I decided to follow that perspective in my final project. I chose the material driven design method to design for material experiences in relation to embodiment in interaction, as a main principle for my further research.The aforementioned method is based on the following steps:
- “Understanding The Material: Technical and Experiential
- Characterization,
- Creating Materials Experience Vision,
- Manifesting Materials Experience Patterns,
- Designing Material/Product Concepts”
Biomomicry
With their flexibility, soft robotics resemble soft bodies of animals, octopuses, elephant trunks, jellyfish for example. This ways, they may imitate the movement mechanics found in nature. Throughout the evolution process and its biodiversity, nature has developed a wide variety of solutions for body transformation and mobility, that now may serve as a source of inspiration and reference for scientists, engineers and technology innovators, in a process named biomimicry.
Processes
HEAT-TRANSFER VINYL
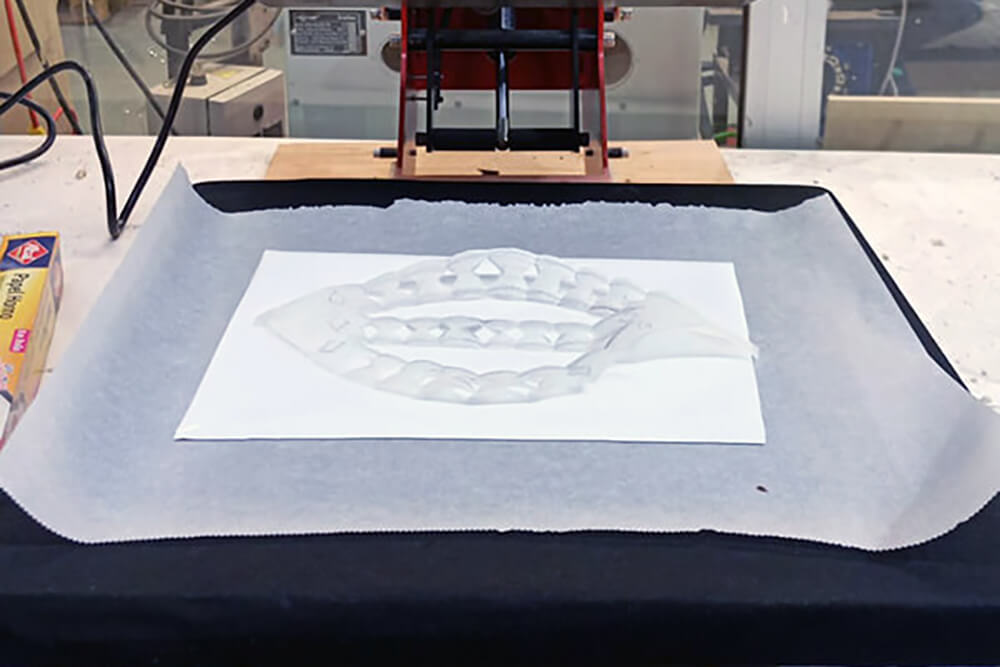
- 2D shapes
- under 1mm thin
- Cheap
- Very fast
- Requires vinyl or laser cutter for fabricating inserts
- Inserts non-reusable
- Seals at least 3-5mm thick
- Air channels at least 3-5mm thick
Heat-transfer vinyl
download here
Heat-transfer vinyl inflatable process
- Design your inflatable. The non-sticky insert will make air channels inside, connect them all. Make sure to add an opening leading to the edge, where you'll insert the pipe later. The air tunnels as well as the gluing lines should be at least 5mm wide
- Cut out the insert for your inflatable from a sheet of baking paper. You may do it by hand or use a vinyl cutter
- Put the insert between two sheets of heat-transfer vinyl. The shiny side is usually the one with glue layer, so it should be facing inside
- Put the sandwiched inflatable in a heat-press (around 140 C degrees, 15 seconds) or use a regular iron to apply heat. Always put additional layers of baking paper between the vinyl and other surfaces where it may stick
- Let the inflatable cool down for a few minutes before moving it, so it sticks better
- Cut out the excess vinyl around the edges
- Insert a pipe in the previously prepared opening
- Inflate your design with a syringe or an air compressor
silicone casting
Silicone casting process
- Read the manufacturer's instructions carefully. The process may vary, pay attention to processing time and proportions.
- Measure the A part (preferably with a digital scale or good volume scale) and the B part
- Pour the B part into the container with the A part. Mix them VERY thorougly, at least 10 minutes
- Do not exceed the processing time, the silicone mix would start hardening after certain time set by manufacturer
- Optionally you may use mold release spray on your mold prior to casting
- Pour the silicone mix in your mold, do it very slowly, as little at time as possible. Avoid making bubbles that could interfere with your design properties or thin the inflatables walls. The narrower the stream - the more bubbles would pop in the process - the better Start from one corner, hold the mold at an angle and let the mix flow
- Put the mold in a place where it wouldn't be moved. Make sure the table surface is perfectly horizontal, and the silicone layers are even throghout the whole mold. Otherwise it may not inflate as intended. Leave for the time set by the mix manufacturer
- Once it's cured, remove the casting gently form the mold
- Mix a small amount of silicone. Cut a piece of non-stretchy fabric in a size that would cover the mold. Pour some silicone on top of it and smear it evenly
- Smear some more silicone on the silicone casting, where it shoudl adhere to the fabric part. Put it on top of the soaked fabric and let it cure once again
heat fusing
Researchers at MiT Media Lab have developed an alternative fabrication technique for soft robotics. It involves computer-controlled heat source using high temperature to seal two flat sheets of meltable materials. One of the papers coveres upcycling thermoplastic waste packaging, that may be transformed into inflatable actuators by using a 3D printer extruder.
The process requires a piece of cardboard placed on the printer's bed,waste plastic bag and a sheet of alluminium foil, all pressed by heated-up nozzle. I tried to recreate the process according to the described setup, however I did not have the same machine park available as at MiT. The printer I had available was an old Reprap, produced in 2014, with some technical issues. The main problem was an uneven bed of the printer, which was impossible to calibrate, what was resulting in failed fusing trials.
In order to compensate the machine limitations, I modified the process according to the options available. I replaced the alluminium foil, which was getting torn easily, with sheets of baking paper. The waxed surface allows the extruder to slide on top of it easily. I also substituted the thin cardboard with a sheet of flexible fabric, in my case it was neoprene. The fabric should be spongy enough to return to its original shape after being pressed by the travelling nozzle tip. The fabric helps to distribute the pressure more evenly, creating a more uniform surface. Equal sealing quality gives more reliable end result within an inflatable.
Baking paper
is used as a protective layer. It separates the hot extruder from the thermosplastic sheets, letting it slide on top of the surface. Glossy, waxed layer keeps the melting plastic from sticking to other materials and prevents unwanted deformations. Baking paper is somewhat thermoresistant, so it reduces some of the temperature emitted by the extruder
Neoprene fabric
is used to compensate the unevennes of the 3D printer bed. Thanks to it, the pressure form the extruder is applied more evenly on the materials above. It may also help to protect the bed from scratching. Neoprene of 1mm thickness was used
Extruder and nozzle
the extruder heats the thermoplastics through the tip of the nozzle. In general, the thicker nozzle - the better, as it helps spread the pressure more evenly on materials below. The tip should be flat and not sharp as it may rip the baking paper
3D printer bed
the bed should be as even as possible and should be calibrated before the process.
Extruder temperature
Should be adjusted accordingly to the melting point of the material. The baking paper layer reduces some of the temperature reaching the thermoplastic sheets. I used range between 140-240°C
Z offset
Should be adjusted according to the thickness of all the layers between the extruder and the printer bed and as well as the calibration of the printer. Type and softness of fabric may influence the pressure necessary to fuse plastic sheets
Printing speed
The speed of travel of the extruder on top of the materials. The slowers it is - the more temperature from the extruder reaches the plastics. I used ranges between 10-20
Z hop height
How far the nozzle goes up to travel between embossing certain parts of the design. Low melting point plastics require higher elevation, as the heat from the nozzle may fuse the plastics in unwanted areas
Lasercutter welding
Urban legend has it, it is possible to seal sheets of thermoplastic with an out-of-focus lasercutter. 3 hours of trial and error proved, that it requires more patience than I have.
See more about this process on Javier Alboguijarro's Fab Academy documentation website
Materials
I selected the materials to experiment with focusing on the reproducibility and accessibility in the maker-space context. Materials suitable for fabrication of actuators via Ilding are mainly various types of thermoplastics with low to medium melting point temperature. I chose three of them varying in stiffness and overall felling: low-density polyethylene, ethylene-vinyl acetate and polypropylene with ethylene-vinyl acetate. Heat-transfer vinyl sheets have a wide spectrum of textures available on the market, thick, shiny, iridescent or textile-like flock for example that all produce varying effect the skin. For the silicone casting, I selected the Eco-flex silicone type, as it is soft, semi-transparent and easily accessible industry standard.
Furthermore, thermoplastics and silicone may be combined with textiles and other materials to produce composite actuators for Inflatables. This way, the range of possible sensations and feelings on the surface of the skin may be widened and enriched even more.
Electronics
In order to perform the shape-changing inflatables require a source of compressed air, did prototyping paste may be done using a regular medical disposable syringe of a required volume,, however, for wearable purposes, an interactive electronic system is necessary. The circuit compromises 4.5 volt air pump powered by li-po battery. With the help of fab lab experts, I developed a custom-made PCB board that operates the pump through the Attiny 85 microcontroller. The microcontroller executes an Arduino code that turns the pump on and off in a given time, triggered by a button input from the User. The li-po battery is small enough to make the electronic system convenient and portable enough for wearable use.. In attempt to minimize the vibration from the pump as well as the size of it, I purchased a device called micro-blower. It is a piezo-electric ceramic diaphragm component that can blow air with surprising pressure given the small size of the device - 2cm x 2cm x 0.2cm.
//int ledPin = 9; // LED connected to digital pin 9
//int analogPin = 3;
// potentiometer connected to analog pin 3
//#define ledPin 0;
//#define pumpPin 1;
int buttonState = 0;
int val = 0; // variable to store the read value
#include
#define SWITCH_OFF 0
#define SWITCH_ON 1
unsigned long previousMillis;
int switch_state = SWITCH_OFF; // initial state
int ledPin = 0; // LED connected to digital pin 12
int pumpPin = 1; // Pump connected to digital pin 9
int buttonPin = 4;
bool stateChanged = false;
int onTime = 5000;
int offTime = 1000;
bool pumpState = false;
ezButton button(buttonPin); // create ezButton object that attach to pin 7;
void setup() {
// Serial.begin(9600);
button.setDebounceTime(50); // set debounce time to 50 milliseconds
pinMode (ledPin, OUTPUT);
pinMode (pumpPin, OUTPUT);
pinMode (buttonPin, INPUT);
}
void loop() {
button.loop(); // MUST call the loop() function first\
if (button.isPressed() && stateChanged == false) {
// change state of switch
if (switch_state == SWITCH_OFF) {
switch_state = SWITCH_ON;
previousMillis = millis();
}
else {
switch_state = SWITCH_OFF;
}
//Serial.print("switch's state -> ");
//Serial.println(switch_state);
stateChanged = true;
}
else if (button.isPressed() == false) {
stateChanged = false;
}
if (switch_state == SWITCH_ON) {
unsigned long currentMillis = millis();
if ((pumpState == true) && (currentMillis - previousMillis >= onTime)) {
analogWrite(pumpPin, 0);
previousMillis = currentMillis;
pumpState = false;
}
else if ((pumpState == false) && (currentMillis - previousMillis >= offTime)) {
analogWrite(pumpPin, 250);
previousMillis = currentMillis;
pumpState = true;
}
digitalWrite(ledPin, HIGH);
}
else {
digitalWrite(ledPin, LOW);
digitalWrite(pumpPin, LOW);
}
}
board 1.0
piezoelectric microblower
Murata MZB Microblowers are suitable as a source for high-pressure air generation for liquid displacement or dispensing applications. They are extremely compact and low profile, utilizing a piezoelectric based drive system that features small dimensions, quick response and less pulsation airflow.
- Piezoelectric ceramic-based drive system
- 1900Pa to 50kPa static pressure range
- 21.5kHz to 27.0kHz resonant frequency range
- SMD termination
So far, no success in making the blower work. Fab Lab experts - Josep & Victor - gave it everything it requires according to the datasheets and it still failed to blow air. Setup: H-bridge, 9V power supply, Arduino with code generating 26.0-27.0kHz frequency. Measured with oscilloscope that showed similar curve to depicted in the diagrams. The component works, produces some sounds, but no air flow.
Movements
Expansion
Bending
Twisting
Geometries
Sensations
According to the Cambridge Dictionary, a sensation is “the ability to feel something physically, especially by touching, or a physical feeling that results from this ability”. People have various means of communication, the verbal way is the first one, that usually comes to mind. However, during the process of socialization, we also develop non-verbal skills for interpersonal communication. They include facial expressions, gesticulation, movement, posture, eye contact, voice tone and modulation to name a few examples. These features are currently being explored as input sources for machines, to better respond to human actions and feelings in a more context-aware computing. approach.
The conscious and unconscious bodily actions are associated with the notion of embodiment in the field of HCI, first introduced by Paul Dourish. This concept explores how our bodies and experiences determine how we perceive the surrounding world, feel/sense and think. It refers to humans as physical entities, whose cognition is affected by the way they are situated in the world. It is based on phenomenology and challenges the belief of mind and body dualism.
Drawing inspiration from human-human interaction techniques based on gestures and tangibility, I selected three haptic patterns generating three different sensations, that may be reproduced with the use of the inflatable technology. The selected ones include poking, grabbing and stroking. They are the most prevalent in everyday situations and interactions between humans and are easily understandable and recognizable. They are also possible to achieve with the use of the shape morphologies that I have already developed, that generate certain movements and predefined deformation of the actuators.
Pressing
Poking is the most basic of the sensations. It is based on applying pressure on points. It has a similar feeling to a person tapping on somebody’s shoulder to ask a question. It is based on the simplest expansion movement and does not require constraints.
Grabbing
Grabbing is the sensation based on poking but instead of separate pressure points, the pressure is applied evenly on a surface, generating a feeling of being wrapped around or something shrinking on top of the skin.
Stroking
Stroking resembles the feeling of petting an animal. It may be summarized as a pressure point in transition from one position on the surface to another. The movement of the pressure points may have many variables: intensity, speed, direction or repeatability. May as well be a an array of poking sensations triggered in a sequence.
Samples and testing
In order to test user feedback from various body locations, I embedded the inflatable samples into stripes of textiles. I tested both flexible material (Lycra) and inflexible (cotton). Cotton proved to be more suitable as it constrained the air into pressing against the skin surface, while the elasticity of Lycra allowed deformation in both directions. The stripes could be wrapped around arms and legs, as well as torso, collecting user feedback from skin of varied sensitivity and amount of nerve endings. The proportions and distance between the pressure points are modified across the samples. The size and curvature of the surface of particular body parts are some of the other examined variables affecting the user experience.
The textiles may be used as constraints for further directing the shape-change of the inflatable actuators and for triggering certain effects on the skin. Depending on the side which is stiffer, either by the thickness of silicone or thermoplastic or by creating a composite with other materials, the air may be compressed towards the more flexible direction, as shown in the illiustration. I incorporated this property, when investigating the affordances of the samples. The same inflatable actuator could be used to produce either visual feedback or haptic feedback, depending on which side was placed towards the skin, and which was facing away from it. The inflation would then happen either outwards, producing a visual effect, or inwards, giving a sensation on the skin, as depicted.
Direction of deformation
Gallery
conclusions
The outcome of this research is a set of samples that give visual or haptic feedback. They were crafted using four different fabrication methods and materials appropriate for each technique: heat-transfer vinyl, EVA and LDPE . Following the design process of shape-changing geometries, the artifacts recreate three biomicry-inspired movements: expansion, bending and twisting.
The same set of samples was further tested on body for their ability to reproduce the three selected sensations based on the everyday interaction between humans: poking, grabbing and stroking. They were placed on various areas of the body to collect feedback. According to the user’s reactions, two of the sensations were recognizable and understandable: the poking and grabbing. However the stroking effect was not successful.
It proves that inflatables behave differently, when placed on the body. They are affected by the rigidity and pressure coming from the contact with another object. The attachment method such as flexible or non-flexible textile stripe also plays a role. Due to these facts, it may be concluded that designing for haptic feedback is more particular than for visual outcomes and requires different solutions. It is challenging to translate visual changes in geometry to haptic sensations on body.
Different fabrication methods utilize diverse materials that vary in texture, properties and overall feeling, producing a range of sensations on the skin. It may be further enriched by further investigation of composites of various materials that combine different properties. Some of the shape-shifting may be also enhanced by the use of constraining techniques that also should be explored in more detail. Materials affect the behavior and experience of inflatables and their affordances may be used as a starting-point of the design process. The exploration of visual movement mechanics and geometries resulted in creation of basic vocabulary of motion in multiple samples. It is possible to achieve a wide range of motion using the plastic sheets methods. The silicone has more limited spectrum of possible deformation and shape-shifting abilities due to its three-dimensional nature and flexibility in all directions.
Due to the lack of established methods of evaluating sensory experiences, the assessment of the outcomes of this research is not entirely objective. There is no proper language or vocabulary to address the bodily experience of touch in an academic way. Sensations are very personal reactions to signals from the skin’s nerve endings and sensitivity to certain actions vary greatly among people.
The further development of this project should incorporate the findings, technological and material affordances exploration of inflatables with the somaesthetic approach to interactive systems design. This combination may educate sensory sensitivity to better understand and experience the surrounding world via technologically augmented body.
References
- Ou, Jifei, Mélina Skouras, Nikolaos Vlavianos, Felix Heibeck, Chin-Yi Cheng, Jannik Peters and Hiroshi Ishii. “aeroMorph - Heat-sealing Inflatable Shape-change Materials for Interaction Design.” Proceedings of the 29th Annual Symposium on User Interface Software and Technology (2016): n. pag.
- Choi, Kyung Yun and Hiroshi Ishii. “Therms-Up!: DIY Inflatables and Interactive Materials by Upcycling Wasted Thermoplastic Bags.” Proceedings of the Fifteenth International Conference on Tangible, Embedded, and Embodied Interaction (2021): n. pag.
- Material Driven Design (MDD): A Method to Design for Material Experiences , Karana, E., Barati, B., Rognoli, V., & Zeeuw van der Laan, A. 2015 Aug 30. Material Driven Design (MDD): A Method to Design for Material Experiences. International Journal of Design [Online] 9:2. Available: http://www.ijdesign.org/index.php/IJDesign/article/view/1965
- Dourish, Paul. 2001. Where the action is: the foundations of embodied interaction. Cambridge, Mass: MIT Press.
- Benyus, Janine M. Biomimicry: Innovation Inspired by Nature. New York: Morrow, 1997.
Files
- Gripper and bubble mold files
download
Back