4. BioChromes¶
🗓️ 2023_October 10th to 16th
part of my work
This week's theme intrigued me from the start. I'd already seen a few tutorials on the internet and Pinterest about vegetable dyes, but I didn't think there were so many parameters to consider when dyeing fabrics.
Research¶
A reflection on the repercussions of dyeing in the textile industry, its effects and impacts on the environment and the working conditions of the people who make the dyes (not always biochromes). Here are some articles about the impact of dyed industrial clothing, and Textile Dyes Pollution: The Truth About Fashion’s Toxic Colours.
The idea would be to switch to more ethical or eco-friendly brands, like the brand created by Miranda Bennet.
On the other hand, it seems appropriate to reflect on the way we think about and design large-scale plant dyeing. The impact of growing or harvesting plants at source: what if we deplete these resources (as many others do)?
My fav alumni's pages as reference:
- Laora Guillermin Le Textile Lab Lyon 2022-2023
- Marion Banon Le Textile Lab Lyon 2022-2023
- Olatz Pereda Basque Design Center 2021-22
- Surzhana Radnaeva Le Textile Lab Lyon 2022-2023
References & Inspiration¶
Work of David Santandreu, french artisan dyer, worked for several years with a workshop in Morocco to promote the country's traditional dyes.
Screenshot-David Santandreu
Colore ton Monde is an french association that develops innovative workshops and training courses to discover and apply natural dyes to textiles and paint.
Screenshot-Colore ton Monde
Another french textile designer Sandrine Rozier, who create clothes and garnements whith natural dyes.
Screenshot-Sandrine Ronzier
Tools¶
- metal pots (preferably)
- hot plate
- plastic or wooden spoons
- forks
- wooden branches (for stirring)
- measuring cup
- kitchen scale
- strings
- infusion bag
- protective smock
- gloves (if necessary)
- hair dryer
- brush paint
Process and workflow¶
After this rich presentation by Cecilia Raspanti, I had the chance to follow the training led by Charlotte Julien, who has created her own brand Marga. Specializing in plant dyes since 6 years, these three days were very instructives with her.
Day 1 : The Dyeing Process¶
Step 1 : Prepare the fiber¶
Charlotte introduces us to the mechanisms of vegetable dyeing. Differentiate between different fibers like plant fibers (or cellulosic like cotton, linen, ramie, viscose,...) and animal. Cellulose is a natural component of the cell walls of plants and trees. Fibers from certain plants have a very high cellulose content (cotton and ramie: >90%; jute, flax and hemp: >60%), while fibers from trees (pine, spruce, fir, birch, poplar) generally contain around 40-50% cellulose. They are treated differently for preparation and dyeing. Animal fibers (wool and silk) must be mordanted and dyed in cold water, and only then heated. Otherwise, the fiber felts and becomes damaged.
Fabrics tested¶
Material name | Fabric composition | Breathability | Moisture-wicking abilities | Heat retention abilities | Stretchability | Washing temperatures |
---|---|---|---|---|---|---|
Silk | Animal fibers - silkworm insect | Highly breathable | High | Low | Low | Cool or Warm |
Wool | Animal fibers - wool sheep | Highly breathable | High | High | High | Preferably Cold |
Cotton | Naturel fibers - cellulose fibers | Highly breathable | High | Low | Low | Cool or Warm |
Process :¶
Ingredients and recipes
Preparing the fibers is an important, even essential step, which, if not done correctly, will influence the duration and quality of the color.
Always wash the fibers to be dyed (preferably using a natural detergent without bleaching agents). Rinse well and dry.
Step 2 : Mordanting the fiber¶
The fiber must be prepared to receive the color. To do this, the fabric must be mordanted to allow the dye to set ("mordant") on the fiber.
Process : Apply a fiber-opening mordant to the fiber to help the color bite into the fiber and integrate in a durable, solid way.¶
Alumina mordanting recipe:
- Weigh the fiber
- Rinse fiber
- Measure 10-20% of fiber weight in alum (for strong or weak mordants)
- Measure the volume of water in the fiber in a large 5X basin
- Add measured alum to water
- Stir well to dissolve the alum
- Add fibers
- Stir constantly for uniform application
- Heat until boiling (1 to 2 hours)
- Carefully remove the fibers. The wool should be removed once the water has cooled, to avoid temperature differences
- Allow to dry
- Rinse fiber well before dyeing to remove any excess alum in the dye bath
Tannins bath recipe: to complete the alumina mordanting:
Tannins are used for their brown/beige color, but also for their anti-UV properties, which reinforce the alumina mordant.
30% powder to be diluted in water before applying fibers.
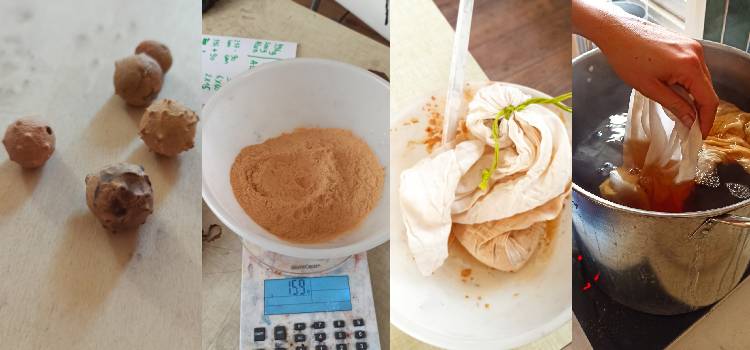
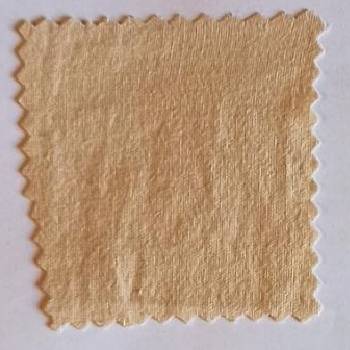
We can add additional mordant to the fiber to further solidify the dye. For animal fibers, we can add cream of tartar to amplify, brighten and solidify the color on the fiber.
We can also dye in another mordant like iron sulfate mordant to darken the shade and create nuances.
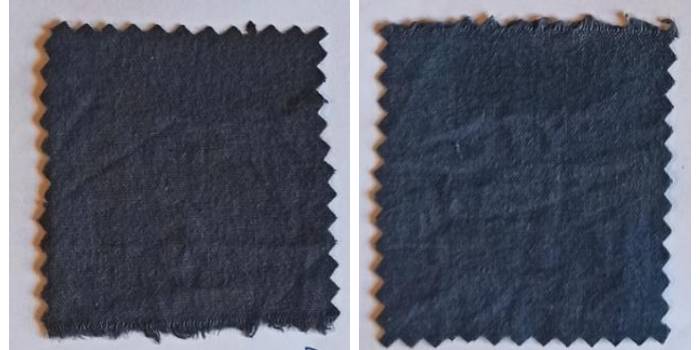
Day 2 : The tinctorial plants and insect¶
We look at the different families of color molecules with tinctorial plants and insect (for the cochineal) :
-
Red tinctorial plants are called Anthraquinones.
The madder root (Rubia Tinctorium) having the most anthraquinone molecules (19). Each molecule must be deposited on the fabric for the red to set. Cold and hot dyeing too -
The Cochineals also has many anthraquinones but more pink (hot dyeing). It is one of the best-known "natural" dyes for pink dyes that is not a plant but an insect. (A deep purple dye is extracted from female cochineal beetles. The female Dactylopius coccus is used to produce various shades of red, orange and scarlet. This coloration comes from the carminic acid.)
-
Yellow tinctorial plants are from the Flavonoïds family (different from Flavonoles, which are less solid). Reseda, Gaude, Goldenrod or Pomegranate are excellent yellow tinctarial plants.
-
Brown tinctorial plants like chestnuts or gallnuts have Tannins, very strong molecules. Like the Brou de noix (wich must macerate for a long time before being used for dyeing, almost 1 year!!).
The amount of plant influences the color tone : + plant = dark color, - plant = light color. fresh plant = 60% of fiber weight
if the plant is dry = 100 to 150% of fiber weight
There were 6 dye tests to prepare. I chose to make 2 : one with dried cochineals and the other one with extract of madder root. The fibers weighed a total of 130 gr.
specific features of wool!!
Remember : the wool should always be put in when the water is cold, and then the water temperature should be raised to prevent felting.
The Cochineal recipe1 pink dye¶
Recipe
- With 40% dried insects
- Place dried insects in a fabric bag
- Crush the cocheneal or stir the bag in hot water to infuse the tincture
- Add wool when the water is cool and others fabrics after
- Mix and heat to 80°C max during 1 hour
Process
The Madder root recipe (hot and cold)1 red dye¶
Madder root can be dyed both hot and cold. I tested the cold recipe.
Recipe
- With 50% plants
- Mix in cold water (with a blender if necessary)
- Filter before putting in the pot (what I forgot to do😅)
- Adjuct water
- Add wool when the water is cool and others fabrics after
- Adjuct water, mix and heat to 80°C max during 1 hour
With 150% and hot preparation | With 50% and cold preparation
Process
The Myrobolan recipe1 green dye¶
Recipe
- With 150% plants or 50% extract
- Place plants in a fabric bag an steep in water
- Heat to 80°C during 30 minutes (don't forget to put the wool when water is cold)
- Once the colored juice is obtained, leave to cool
- Add rinsed fibers
- Mix and heat to 80°C max during 1 hour
The Catechu recipe1 brown dye¶
Recipe
- With 100% plants
- Place plants in a fabric bag an steep in water
- Add wool when the water is cool and others fabrics after
- Mix and heat to 80°C max during 1 hour
The Pomegranate recipe1 yellow dye¶
Recipe
- With 150% pomegranate peel or 50% extract of pomegranate peel
- Place plants or extract in a fabric bag an steep in water
- Heat to 80°C during 30 minutes (don't forget to put the wool when water is cold)
- Once the colored juice is obtained, leave to cool
- Add rinsed fibers
- Mix and heat to 80°C max during 1 hour
Biochromes results¶
In order : Myrobolan | Catechu | Pomegranate | Madder root 50% | Madder root 150% | Cocheneal
!Always dry fabrics before rinsing! Sun or moonlight affect colors!
Eco Printing¶
Some inspiration : Work of Beste Bonnard
Process and results¶
- Place plants, flowers, petals, leaves, roots, etc. on half an etched cloth.
- Cover with the other half of the fabric
- Wrap around a stick, tie tightly with string
- Wet the fabric
- Unwind the fabric
- Steam (1h to 3h)
- Dry before washing
Patterns with mordant pastes¶
Application of vegetable dyes for printing with mordant pastes/ink
Recipe Mordanting Paste (for mordanted fabrics)
Acetate preparation
- 1L white vinegar
- 60gr alumina sulfate or iron sulfate
- 50gr sodium carbonate or lime/chalk
Printing paste
- Alumina acetate or iron sulfate
- 100gr alum or 60 gr iron sulfate
- 50gr sodium carbonate or lime/chalk
Recipe Colored Printing Paste/Ink
- 50gr plant juice
- 50gr alumina acetate or iron
- 1% thickener (ex:guar gum=textile, rice flour=paper, ...)
These printing pastes can be applied with silkscreen screens, stencils or brushes.
Iron sulfate printing paste can cause staining. The table surface must be thoroughly cleaned between each trial.
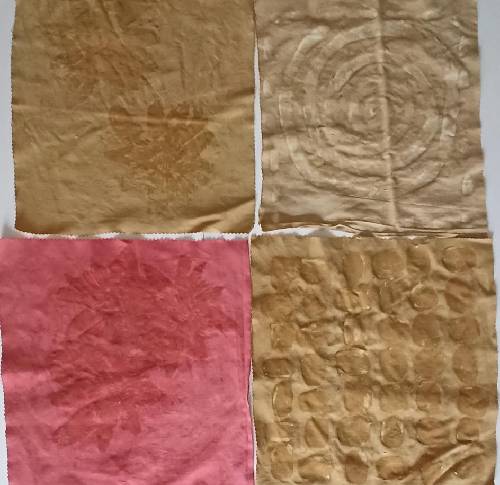
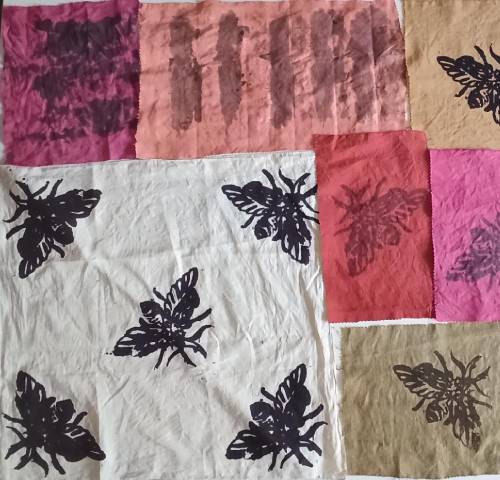
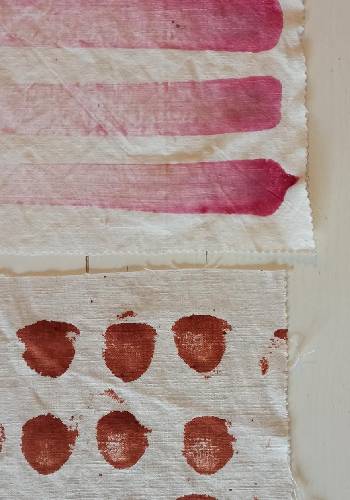
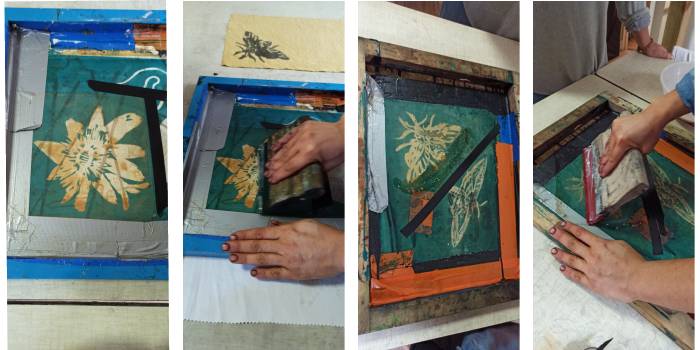
Going Further¶
Do pigment test
Try bacterial dyeing
Retry to dye fabrics myself!
Sew the fabrics dyed for my project 😅